Stel je een productieproces voor dat de complexe ontwerpvrijheid van kunststof spuitgieten combineert met de ongeëvenaarde sterkte en duurzaamheid van metaal. Dat is de magie van MIM-technologieeen game-changer in de wereld van metaalbewerking.
Dit artikel duikt in de fascinerende wereld van MIM-technologie en verkent de fijne kneepjes, toepassingen, voordelen en overwegingen. Dus, maak je vast en maak je klaar om een technologie te ontdekken die de grenzen verlegt van wat mogelijk is in metaalproductie.
Het MIM-proces
MIM werkt volgens een bedrieglijk eenvoudig principe. Hier volgt een overzicht van de betrokken stappen:
- Poedercentrale: De reis begint met fijn gepoederd metaal, vergelijkbaar met metaalstof. Dit poeder kan bestaan uit verschillende metalen, waaronder staal, roestvrij staal, titanium en zelfs exotische legeringen.
- Binding: Stel je voor dat je het metaalpoeder mengt met een speciaal bindmiddel, zoals een lijm die alles bij elkaar houdt. Dit brouwsel, bekend als grondstof, wordt het kneedbare materiaal voor de volgende stap.
- Injectie-intuïtie: De grondstof wordt dan onder hoge druk in een precies ontworpen vormholte gespoten. Zie het als het persen van Play-Doh in een koekjesvorm, maar dan met veel geavanceerdere machines.
- Vormgeven: Eenmaal geïnjecteerd neemt de grondstof de vorm aan van de matrijsholte, waardoor een bijna-netvormig onderdeel ontstaat. Deze bijna-netvorm verwijst naar een onderdeel dat een minimale nabewerking nodig heeft om zijn uiteindelijke afmetingen te bereiken.
- Binder Buh-Bye: In de volgende fase wordt het bindmiddel verwijderd door middel van een thermisch ontbindingsproces. Dit kan technieken zijn zoals extractie met oplosmiddelen of thermische afbraak, waarbij het bindmiddel verdampt en het metaalskelet achterblijft.
- Krachtstoot: De laatste stap is een sinterproces op hoge temperatuur. Hier worden de metaaldeeltjes heet en gezellig, smelten ze samen en verdichten ze het onderdeel. Dit verbetert de sterkte en structurele integriteit van het onderdeel aanzienlijk.
Zie MIM als een geraffineerde metalen origami, waarbij metaalpoeder minutieus wordt gevouwen tot ingewikkelde vormen met een indrukwekkende sterkte.
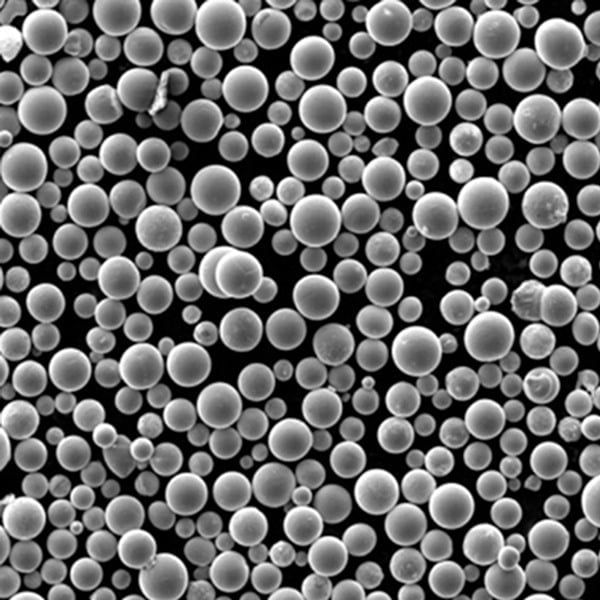
De voordelen van MIM-technologie
MIM-technologie heeft een aantal overtuigende voordelen waardoor het de voorkeur geniet voor verschillende productietoepassingen. Laten we eens kijken naar enkele belangrijke voordelen:
- Ontwerpveelzijdigheid: In tegenstelling tot traditionele metaalbewerkingsmethoden zoals gieten of machinaal bewerken, biedt MIM een uitzonderlijke ontwerpvrijheid. Complexe geometrieën, ingewikkelde details en dunne wanden - MIM kan het allemaal met gemak aan. Stel je voor dat je tandwielen maakt met minuscule tandjes of ingewikkelde medische instrumenten met delicate onderdelen - MIM maakt het mogelijk.
- Hoge volumes, hoge precisie: MIM blinkt uit in productieruns met hoge volumes. De mogelijkheid om bijna-netvormen te maken minimaliseert de noodzaak voor uitgebreide nabewerking, wat leidt tot snellere productiecycli en kostenbesparingen. Bovendien zorgt MIM voor een uitzonderlijke maatnauwkeurigheid, wat cruciaal is voor componenten die precieze toleranties vereisen.
- Materiaal Marvel: MIM biedt de flexibiliteit om te werken met een breed scala aan metaalpoeders. Dit opent deuren om onderdelen te maken van staal met hoge sterkte, corrosiebestendige legeringen of zelfs lichtgewicht materialen zoals titanium.
- Kostenoverwegingen: Hoewel de initiële setupkosten voor MIM hoger kunnen liggen, zorgen de productiemogelijkheden voor grote volumes en de minimale nabewerking voor aanzienlijke kostenbesparingen op de lange termijn. Dit maakt MIM een aantrekkelijke optie voor massaproductie van complexe metalen onderdelen.
- Niet verspillen, niet willen: MIM is een relatief milieuvriendelijk proces vergeleken met traditionele methoden. De bijna-netvorm benadering minimaliseert materiaalverspilling en het gecontroleerde ontbindingsproces maakt het in sommige gevallen mogelijk om bindmiddelen terug te winnen en te hergebruiken.
MIM-technologie is een veelzijdige kampioen die ontwerpflexibiliteit, zeer nauwkeurige productie, materiaalveelzijdigheid en kosteneffectiviteit biedt, terwijl de impact op het milieu tot een minimum wordt beperkt.
De toepassingen van MIM-technologie
MIM-technologie wordt toegepast in een groot aantal industrieën, van de ingewikkelde wereld van medische apparatuur tot de kolossale wereld van auto-onderdelen. Hier zijn enkele prominente voorbeelden:
- Medische wonderen: MIM speelt een cruciale rol bij de vervaardiging van ingewikkelde medische implantaten zoals gewrichtsprothesen, tandprotheses en chirurgische instrumenten. De mogelijkheid om complexe vormen te maken met biocompatibele materialen maakt MIM ideaal voor deze veeleisende toepassingen.
- Voordeel voor auto's: De auto-industrie maakt gebruik van MIM voor de productie van verschillende onderdelen zoals tandwielen, kettingwielen en onderdelen van het brandstofsysteem. De mogelijkheden van MIM om grote volumes te produceren en het vermogen om bijna-nettovormen met kleine toleranties te maken, maken het perfect geschikt voor de snelle autowereld.
- Symfonie van de consumentenelektronica: Van minuscule onderdelen in mobiele telefoons tot ingewikkelde onderdelen in wearables, MIM draagt bij aan de miniaturisatie en functionaliteit van consumentenelektronica. Het vermogen om complexe vormen met hoge precisie te produceren sluit perfect aan bij de steeds kleiner wordende wereld van gadgets.
- Aerospace Ascendancy: De lucht- en ruimtevaartindustrie vraagt om lichtgewicht en toch robuuste componenten. MIM gaat de uitdaging aan door complexe onderdelen te maken van legeringen met een hoge sterkte en een laag gewicht, zoals titanium. Dit vertaalt zich in brandstofefficiëntie en betere prestaties voor vliegtuigen en ruimtevaartuigen.
- Vuurwapenfinesse: MIM speelt een rol in de vuurwapenindustrie voor het maken van ingewikkelde onderdelen zoals trekkers, hamers en beveiligingen. Het vermogen om bijna-netvormen te produceren met hoge precisie en uitzonderlijke sterkte maakt het geschikt voor deze veeleisende toepassingen.
Naast deze prominente voorbeelden heeft MIM-technologie het potentieel om een revolutie teweeg te brengen in verschillende andere industrieën. Naarmate de technologie zich verder ontwikkelt en de kosten concurrerender worden, kunnen we verwachten dat MIM-toepassingen zich uitbreiden naar gebieden als:
- Energie-infrastructuur: Fabricage van ingewikkelde onderdelen voor pompen, kleppen en andere kritieke onderdelen in energieopwekkings- en distributiesystemen.
- Telecommunicatie: Het maken van geminiaturiseerde en zeer nauwkeurige componenten voor complexe telecommunicatieapparatuur.
- Sportartikelen: Het maken van lichtgewicht en duurzame onderdelen voor fietsen, golfclubs en andere sportuitrustingen.
De mogelijkheden van MIM-technologie zijn werkelijk enorm en de invloed ervan op verschillende industrieën zal de komende jaren naar verwachting alleen maar toenemen.
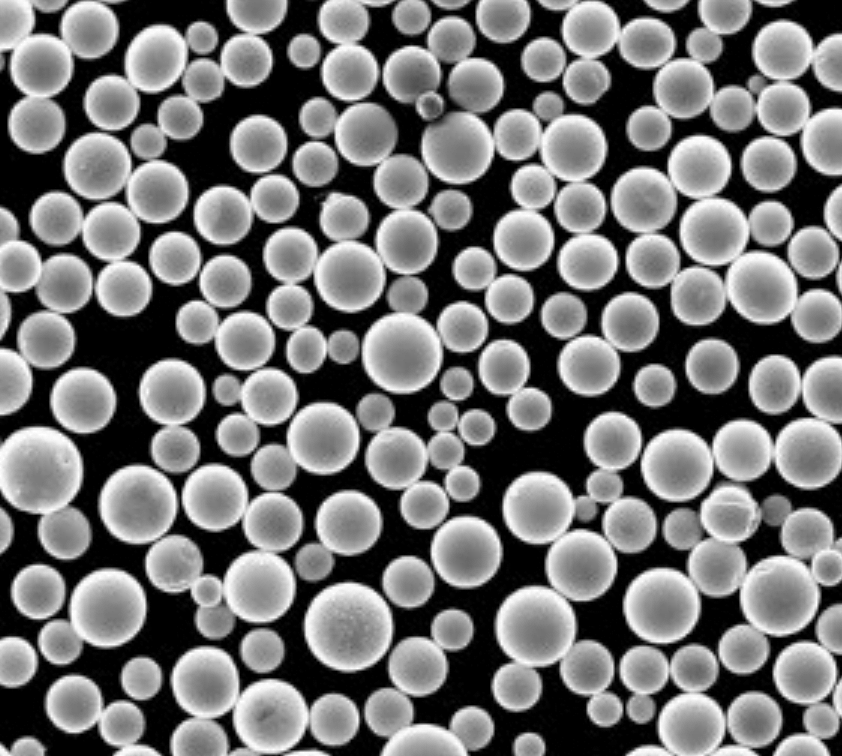
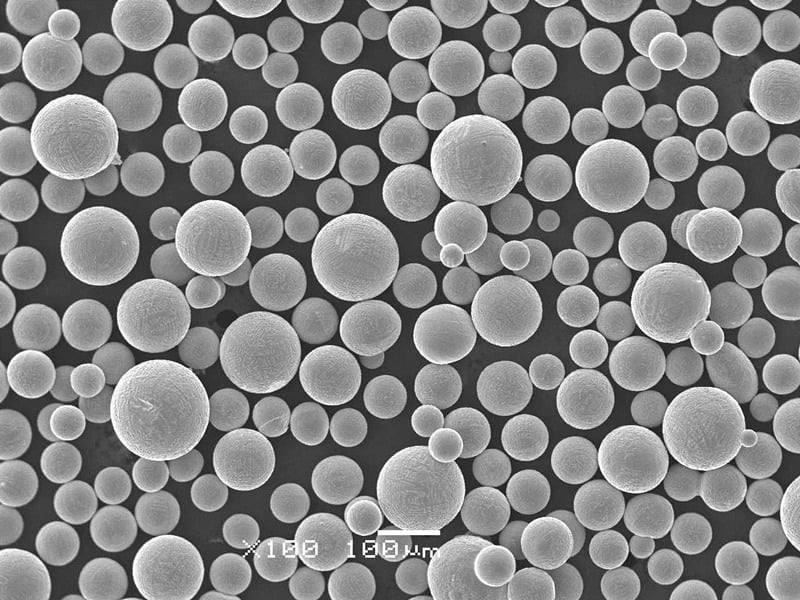
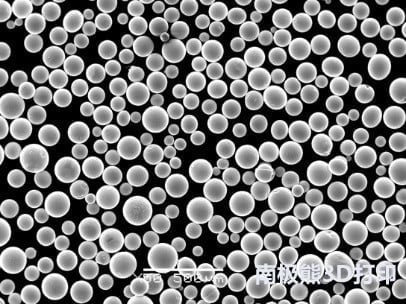
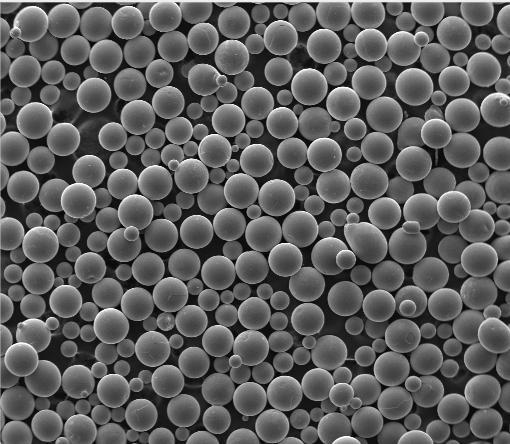
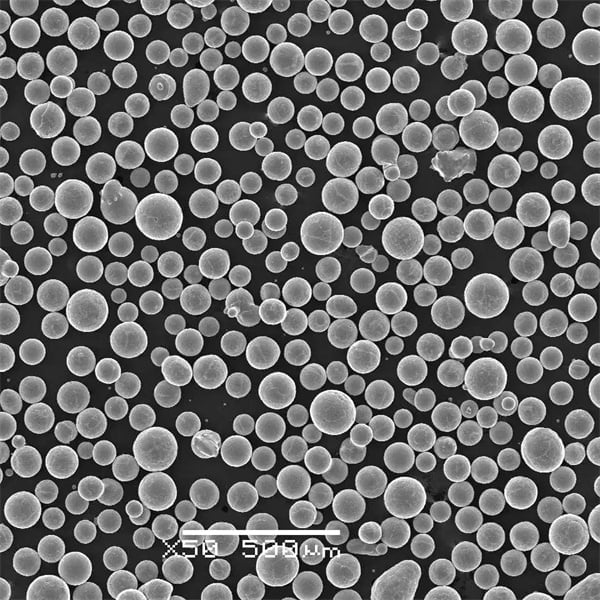
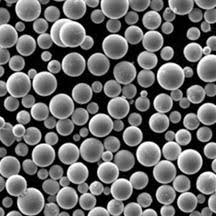
De kenmerken van verstuivingstechnologie
Nu we de magie van MIM hebben verkend, gaan we dieper in op een cruciaal aspect: de verstuivingstechnologie. Dit proces is verantwoordelijk voor het maken van de fijne metaalpoeders die de basis vormen van MIM. Hier volgt een overzicht van de twee primaire atomisatietechnieken:
- Verstuiving van gas: Stel je voor dat gesmolten metaal door een hogedrukpijpje wordt geperst, waardoor het in minuscule druppeltjes uiteenvalt die in de lucht stollen als fijn metaalpoeder. Dit is de essentie van gasatomisatie. Het is een veelzijdige techniek die geschikt is voor een breed scala aan metalen en legeringen.
- Verstuiving van water: Deze methode maakt gebruik van een waterstraal met hoge snelheid om gesmolten metaal in fijne deeltjes te verdelen. Waterverstuiving is bijzonder geschikt voor het produceren van sferische metaalpoeders en wordt vaak gebruikt voor specifieke materialen zoals roestvrij staal.
De keuze van de verstuivingstechniek hangt af van verschillende factoren, waaronder de gewenste poedereigenschappen, het type metaal dat verwerkt wordt en de kostenoverwegingen.
Hier is een tabel met de belangrijkste kenmerken van elke verstuivingstechniek:
Functie | Gasverstuiving | Verstuiven van water |
---|---|---|
Proces | Gesmolten metaal dat door een hogedrukpijpje wordt geperst | Gesmolten metaal versplinterd door een waterstraal met hoge snelheid |
Poeder morfologie | Over het algemeen onregelmatige vormen | Typisch meer bolvormig |
Geschiktheid van metaal | Breed scala aan metalen en legeringen | Voornamelijk geschikt voor specifieke materialen zoals roestvrij staal |
Kosten | Over het algemeen hogere kosten | Lagere kosten in vergelijking met gasverneveling |
Het is belangrijk op te merken dat deze tabel een algemene vergelijking geeft en dat er enige overlap kan zijn in de mogelijkheden, afhankelijk van de specifieke technologie en procesparameters.
Overwegingen en beperkingen van MIM-technologie
Hoewel MIM een aantal overtuigende voordelen biedt, is het essentieel om de beperkingen en overwegingen te begrijpen voordat je er vol induikt. Hier zijn enkele belangrijke punten om in gedachten te houden:
- Beperkingen voor de onderdeelgrootte: MIM is het meest geschikt voor de productie van relatief kleine tot middelgrote onderdelen. De beperkingen komen voort uit factoren zoals de mogelijkheden om de matrijs te vullen en de kans op inwendige scheurvorming tijdens het ontbinden en sinteren.
- Afwerking oppervlak: Hoewel MIM een goede oppervlakteafwerking kan produceren, is het misschien niet ideaal voor toepassingen die een uitzonderlijke gladheid vereisen. In zulke gevallen kunnen extra nabewerkingsstappen zoals polijsten of machinaal bewerken nodig zijn.
- Materiaalkeuze: Niet alle metalen zijn compatibel met MIM. Factoren zoals smeltpunt en sintergedrag spelen een cruciale rol. Vuurvaste metalen met een extreem hoog smeltpunt zijn mogelijk niet geschikt voor MIM vanwege beperkingen in de verwerkingstemperaturen.
- Ontwerp voor MIM: Om de voordelen van MIM ten volle te benutten, is het cruciaal om componenten specifiek voor het proces te ontwerpen. Hierbij moet rekening worden gehouden met factoren zoals wanddikte, ontwerphoeken en mogelijke interne spanningen tijdens het verwerken.
Door deze overwegingen en beperkingen te begrijpen, kunnen fabrikanten weloverwogen beslissen of MIM de juiste keuze is voor hun specifieke toepassing.
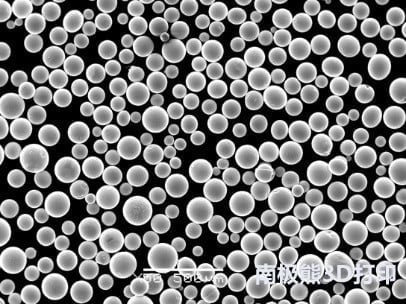
FAQ
Hier is een sectie die een aantal veelgestelde vragen behandelt over MIM-technologiegepresenteerd in een duidelijk en beknopt tabelformaat:
Vraag | Antwoord |
---|---|
Wat zijn de voordelen van MIM-technologie? | Ontwerpflexibiliteit, productie van grote volumes, veelzijdigheid van materialen, kosteneffectiviteit en minimaal afval. |
Wat zijn enkele toepassingen van MIM-technologie? | Medische apparaten, auto-onderdelen, consumentenelektronica, onderdelen voor de ruimtevaart, onderdelen voor vuurwapens en nog veel meer. |
Wat zijn de verschillende soorten verstuivingstechnieken die bij MIM worden gebruikt? | Gasverstuiving en waterverstuiving. |
Wat zijn de beperkingen van MIM-technologie? | Beperkingen in grootte, beperkingen in oppervlakteafwerking, materiaalkeuze en de noodzaak van ontwerpen voor MIM-principes. |
Is MIM een milieuvriendelijk proces? | MIM is relatief milieuvriendelijk vergeleken met traditionele metaalbewerkingsmethoden door minimaal materiaalafval en de mogelijkheid tot hergebruik van bindmiddelen. |
Wat zijn de toekomstperspectieven van MIM-technologie? | MIM-technologie zal naar verwachting blijven groeien en steeds meer worden toegepast in verschillende industrieën vanwege de voordelen en de voortdurende vooruitgang. |
Hoe verhoudt MIM zich tot andere metaalbewerkingsprocessen zoals verspanen of gieten? | MIM biedt meer ontwerpvrijheid en bijna-netvormen in vergelijking met machinale bewerking. Hoewel gieten complexe vormen kan produceren, heeft MIM vaak een hogere precisie en betere materiaaleigenschappen. |
Wat zijn enkele van de uitdagingen van MIM-technologie? | Het ontwikkelen van kosteneffectieve methoden voor het verwerken van een breder scala aan metalen en legeringen, en verdere vooruitgang in ontbindingstechnieken om de kans op defecten te minimaliseren. |
Over 3DP mETAL
Productcategorie
NEEM CONTACT OP
Vragen? Stuur ons nu een bericht! Na ontvangst van uw bericht gaan we met een heel team uw aanvraag verwerken.