Imagine a material that combines the strength of metal with the heat resistance of ceramics. That’s the magic of nickel aluminide powder, a remarkable substance with a unique set of properties that make it a game-changer in various industries. Buckle up as we delve into the fascinating world of nickel aluminide powder, exploring its characteristics, applications, advantages, and considerations.
De kenmerken van Nikkel-aluminide poeder
Nickel aluminide powder, also known as NiAl powder, is an intermetallic compound formed by combining nickel and aluminum atoms in specific ratios. This marriage of elements results in a material with a distinct crystalline structure, offering a captivating blend of properties:
- Prestaties bij hoge temperaturen: One of the most compelling characteristics of nickel aluminide powder is its exceptional resistance to extreme temperatures. It boasts a melting point exceeding 1600°C (2912°F), making it a prime candidate for applications where conventional materials would simply melt away. Think jet engines roaring at scorching temperatures or gas turbines enduring intense heat – nickel aluminide powder thrives in these fiery environments.
Imagine a jet engine, the heart of an airplane, constantly battling scorching temperatures. Traditional materials might struggle under such duress, but nickel aluminide powder steps up to the challenge, maintaining its structural integrity and contributing to the engine’s efficient operation.
- Lage dichtheid: Despite its impressive heat resistance, nickel aluminide powder is surprisingly lightweight. Its density is roughly 60% that of steel, offering a significant weight advantage in applications where every gram counts. This lightweight nature makes it particularly attractive in the aerospace industry, where minimizing weight translates to improved fuel efficiency and overall aircraft performance.
Think of an airplane – every ounce matters. By incorporating nickel aluminide powder in critical components, engineers can shave off precious weight, allowing the aircraft to fly farther on less fuel. It’s a win-win for both efficiency and environmental impact.
- Uitstekende weerstand tegen oxidatie: High temperatures aren’t the only foe that nickel aluminide powder tackles. It also demonstrates outstanding resistance to oxidation, a process where a material reacts with oxygen and deteriorates. This resistance is crucial in hot environments where oxidation can rapidly weaken components. In essence, nickel aluminide powder fights the good fight against rust and degradation, ensuring components last longer under demanding conditions.
- Superior Strength and Creep Resistance: Strength is another hallmark of nickel aluminide powder. It possesses impressive tensile strength, meaning it can withstand significant pulling forces without breaking. Additionally, it exhibits exceptional creep resistance, the tendency of a material to deform slowly under constant stress at high temperatures. This combination of strength and creep resistance makes nickel aluminide powder ideal for components that need to maintain their shape and function even under prolonged exposure to heat and pressure.
Imagine a turbine blade in a gas turbine – it’s constantly under immense stress from hot gases flowing through it. Nickel aluminide powder steps in, providing the necessary strength and creep resistance to ensure the blade retains its shape and continues to operate efficiently.
- Tailorable Properties: The beauty of nickel aluminide powder lies in its versatility. By adjusting the composition and processing methods, engineers can tailor its properties to specific applications. Different ratios of nickel and aluminum, along with variations in particle size and distribution, can influence factors like strength, oxidation resistance, and even electrical conductivity. This level of customization allows for the creation of nickel aluminide powder formulations that perfectly match the demands of a particular application.
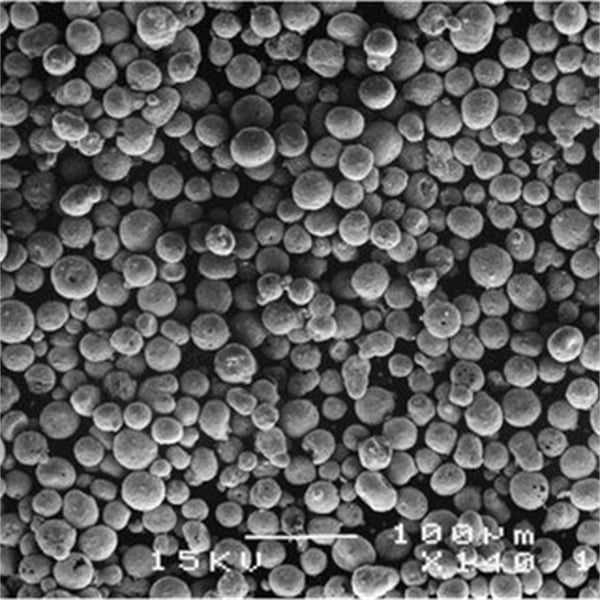
Belangrijkste eigenschappen van Nikkel-aluminide poeder
Onroerend goed | Waarde |
---|---|
Smeltpunt | > 1600°C (2912°F) |
Dichtheid | ~60% of steel |
Oxidatiebestendigheid | Uitmuntend |
Treksterkte | Hoog |
Kruipweerstand | Uitmuntend |
Tailorable Properties | Yes (through composition & processing) |
These fascinating characteristics collectively make nickel aluminide powder a highly sought-after material for various demanding applications.
The Applications of Nickel Aluminide Powder
Now that we’ve explored the remarkable characteristics of nickel aluminide powder, let’s delve into the exciting world of its applications. This versatile material finds itself at the forefront of various industries where high-temperature performance is paramount. Here are some key areas where nickel aluminide powder shines:
- Lucht- en ruimtevaart: As mentioned earlier, the aerospace industry leverages nickel aluminide powder’s unique combination of lightweight nature and high-temperature resistance to great effect. It’s used in critical engine components like turbine blades and combustors, where it helps to:
- Reduce weight: Every gram shaved off an aircraft translates to improved fuel efficiency and increased payload capacity. Nickel aluminide powder’s lightweight nature contributes significantly to weight reduction efforts in aerospace design.
- Enhance durability: Jet engines operate at scorching temperatures, and nickel aluminide powder’s exceptional heat resistance ensures these components can withstand the intense heat without succumbing to deformation or failure. This translates to longer engine life and improved aircraft reliability.
- Boost efficiency: By maintaining their structural integrity at high temperatures, nickel aluminide powder components contribute to improved engine efficiency. This translates to better fuel burn and ultimately, a reduction in environmental impact.
- Gasturbines: Power generation through gas turbines relies heavily on materials that can handle extreme temperatures and pressures. Nickel aluminide powder steps up to the challenge in various turbine components, including:
- Turbine blades: As in jet engines, nickel aluminide powder’s strength and heat resistance make it an ideal material for turbine blades, ensuring they retain their shape and function efficiently even under the intense heat and pressure of gas combustion.
- Vanes: These stationary components within the turbine also benefit from nickel aluminide powder’s properties. Their ability to withstand high temperatures without warping or losing strength is crucial for optimal turbine operation.
- Combustors: The combustor is where fuel is burned in a gas turbine. Nickel aluminide powder’s resistance to oxidation and high temperatures makes it a valuable material for combustor components, ensuring they maintain their integrity in this harsh environment.
- Auto-industrie: The automotive industry is constantly pushing the boundaries of performance and efficiency. Nickel aluminide powder is finding its way into some high-performance vehicles, particularly in:
- Exhaust manifolds: These components channel hot exhaust gases away from the engine. Nickel aluminide powder’s ability to withstand high temperatures makes it a potential candidate for exhaust manifolds, especially in high-performance engines that generate significant heat.
- Turbocharger components: Turbochargers rely on hot exhaust gases to spin a turbine, which in turn compresses incoming air for improved engine performance. Nickel aluminide powder’s heat resistance could be beneficial in certain turbocharger components, although cost considerations and the need for precise tolerances may limit its widespread adoption.
- Other Industrial Applications: Beyond these core areas, nickel aluminide powder is also explored in various other industrial applications, including:
- Heat exchangers: These devices transfer heat from one fluid to another. Nickel aluminide powder’s combination of heat resistance and corrosion resistance makes it a potential candidate for use in heat exchangers operating at high temperatures.
- Chemical processing equipment: In chemical processing plants where high temperatures and corrosive environments are present, nickel aluminide powder could be used for specific components due to its resistance to both factors.
It’s important to note that nickel aluminide powder is still under development for some of these applications. While its properties are promising, factors like cost, manufacturability, and the need for further research and testing can influence its widespread adoption.
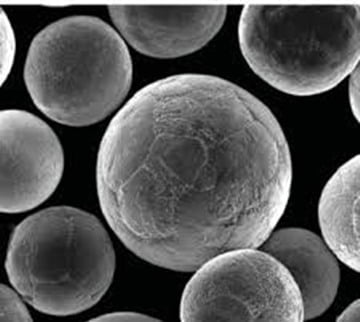
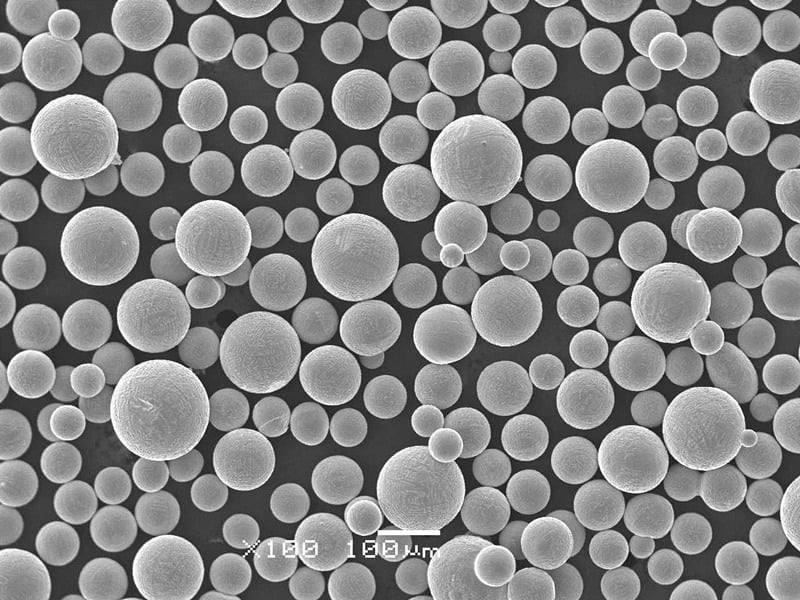
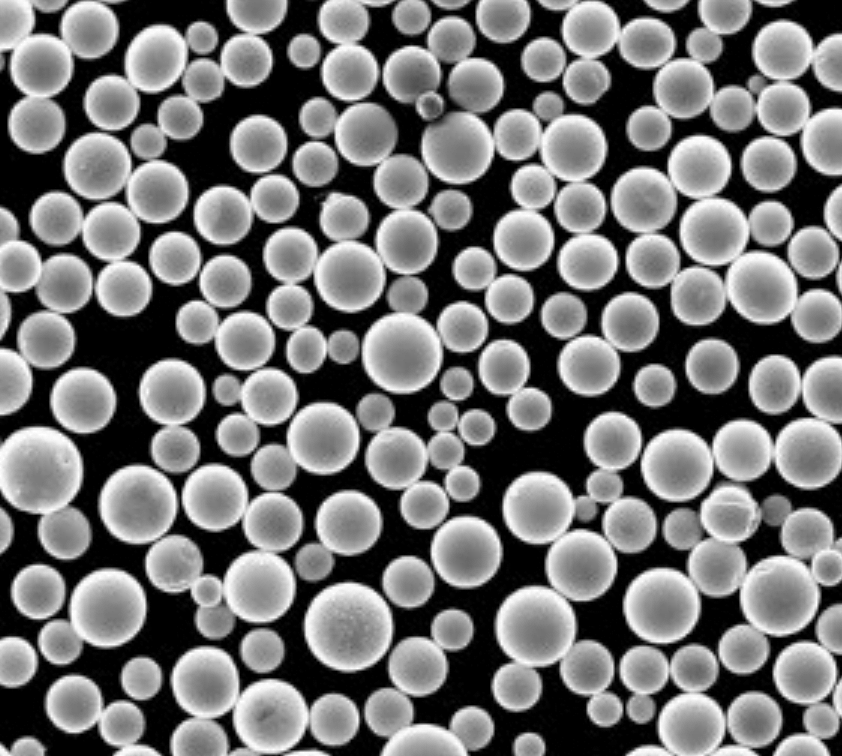
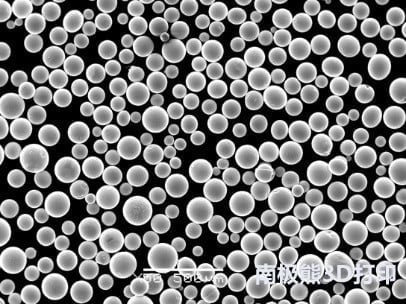
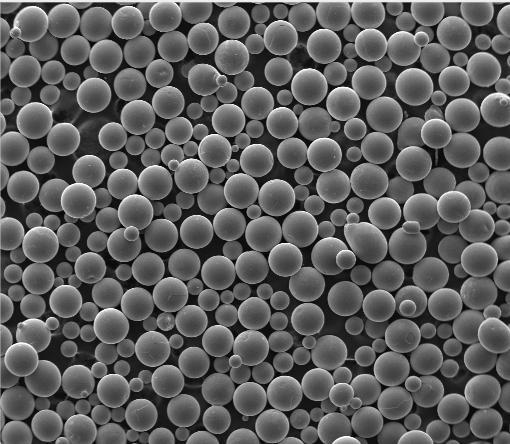
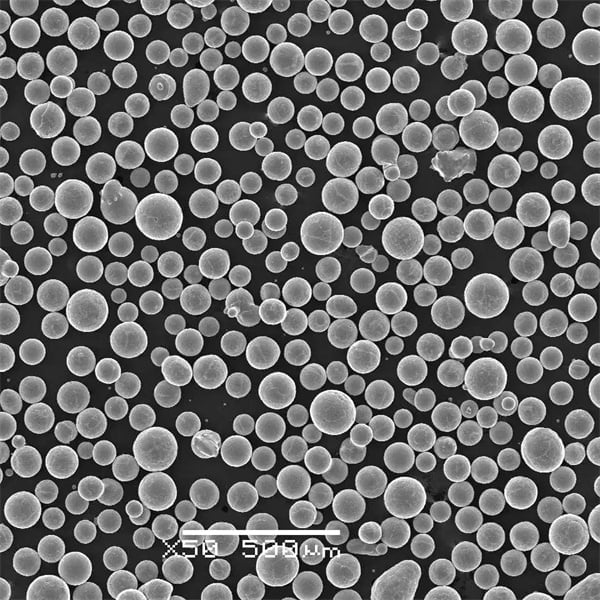
Voordelen en nadelen van Nikkel-aluminide poeder
No material is perfect, and nickel aluminide powder is no exception. Let’s take a balanced look at its advantages and disadvantages to understand where it shines and where there might be room for improvement:
Voordelen:
- Exceptional high-temperature performance: The ability to withstand extreme temperatures without losing strength or structure is nickel aluminide powder’s most compelling advantage. This makes it ideal for applications where conventional materials would simply fail.
- Lightweight nature: The low density of nickel aluminide powder compared to traditional materials like steel offers a significant weight advantage, particularly crucial in weight-sensitive applications like aerospace.
- Excellent oxidation resistance: Nickel aluminide powder’s resistance to oxidation allows components to operate for longer durations in high-temperature environments without succumbing to degradation.
- Superior strength and creep resistance: The combination of high strength and exceptional creep resistance makes nickel aluminide powder a reliable choice for components that need to maintain their shape and function under prolonged stress and high temperatures.
- Tailorable properties: The ability to adjust the composition and processing methods of nickel aluminide powder allows engineers to tailor its properties to specific applications. This versatility opens doors for creating customized materials that perfectly match the demands of a particular use case.
Nadelen:
- Kosten: One of the primary limitations of nickel aluminide powder is its cost. The production process can be more complex compared to traditional materials, leading to a higher price tag. This can be a significant hurdle for widespread adoption in some applications.
- Manufacturability: While advancements are being made, manufacturing nickel aluminide powder components can be more challenging compared to conventional materials. Factors like powder characteristics, processing techniques, and the need for specialized equipment can influence the ease and cost of manufacturing.
- Brittleness at low temperatures: While exceptional at high temperatures, nickel aluminide powder can exhibit some brittleness at lower temperatures. This characteristic needs to be considered during design and application selection.
- Limited availability of certain grades: Not all variations and grades of nickel aluminide powder are readily available commercially. This can limit design options and potentially add to the cost if specific properties are required.
Een geïnformeerd besluit nemen:
Understanding both the advantages and disadvantages of nickel aluminide powder is crucial for making informed decisions about its suitability for a particular application. While its high-temperature performance, lightweight nature, and other advantages are undeniable, the cost, manufacturability considerations, and potential brittleness at lower temperatures need to be carefully weighed.
The Future of Nickel Aluminide Powder:
Despite these limitations, ongoing research and development efforts are focused on improving the cost-effectiveness, manufacturability, and overall performance of nickel aluminide powder. Advancements in powder production techniques, sintering processes, and the development of new compositions could pave the way for wider adoption in various industries. As these advancements unfold, nickel aluminide powder has the potential to revolutionize how we design and build components for high-temperature applications.
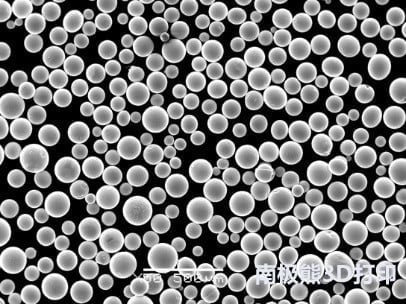
Overwegingen voor het gebruik Nikkel-aluminide poeder
Here are some key considerations to keep in mind if you’re exploring the use of nickel aluminide powder in your application:
- Toepassingsvereisten: Clearly define the specific demands of your application, including the expected temperature range, pressure, and desired mechanical properties. This will help determine if nickel aluminide powder is a suitable candidate.
- Cost vs. benefits: Weigh the cost of nickel aluminide powder against the potential benefits it offers. Consider whether the improved performance justifies the higher cost compared to traditional materials.
- Manufacturability: Evaluate the feasibility of manufacturing components using nickel aluminide powder. Consider factors like the complexity of the shapes required, available manufacturing techniques, and any potential challenges associated with processing this material.
- Availability of desired grades: Ensure the specific grade of nickel aluminide powder with the required properties is readily available commercially. This can influence the design and potentially impact costs.
- Design considerations: The potential for brittleness at lower temperatures needs to be factored into the design process. Consider how components will be used across the entire temperature range they might encounter.
By carefully considering these factors, you can make an informed decision about whether nickel aluminide powder is the right choice for your application.
FAQ
Q: What is nickel aluminide powder?
A: Nickel aluminide powder is an intermetallic compound formed by combining nickel and aluminum atoms. It offers a unique combination of high-temperature resistance, low density, excellent oxidation resistance, and superior strength and creep resistance.
Q: What are the applications of nickel aluminide powder?
A: Nickel aluminide powder finds applications in various industries, including aerospace (turbine blades, combustors), gas turbines (blades, vanes, combustors), automotive (potentially in exhaust manifolds and turbocharger components), and other industrial applications like heat exchangers and chemical processing equipment.
Q: What are the advantages of nickel aluminide powder?
A: The key advantages include exceptional high-temperature performance, lightweight nature, excellent oxidation resistance, superior strength and creep resistance, and the ability to tailor properties for specific applications.
Q: What are the disadvantages of nickel aluminide powder?
A: The primary limitations include higher cost compared to traditional materials, challenges in manufacturability, potential brittleness at lower temperatures, and limited availability of certain grades.
Over 3DP mETAL
Productcategorie
NEEM CONTACT OP
Vragen? Stuur ons nu een bericht! Na ontvangst van uw bericht gaan we met een heel team uw aanvraag verwerken.