Overview of Plasma-Rotating Electrode Process
De Plasma-Roterende Elektrode Proces (PREP) is an advanced method for producing high-quality metal powders with exceptional purity and uniformity. These powders are crucial for various applications, including additive manufacturing, aerospace components, and medical implants. PREP involves melting the end of a rotating metal rod using a plasma arc, causing droplets to be ejected and solidified into fine powders. This process is renowned for producing spherical particles with excellent flowability and packing density.
Key Details of Plasma-Rotating Electrode Process:
- Proces: Utilizes a plasma arc to melt a rotating metal rod.
- Output: High-purity, spherical metal powders.
- Toepassingen: Additive manufacturing, aerospace, medical implants, etc.
- Voordelen: High purity, excellent flowability, uniform particle size.
- Beperkingen: High cost, complex equipment, limited to specific metals.
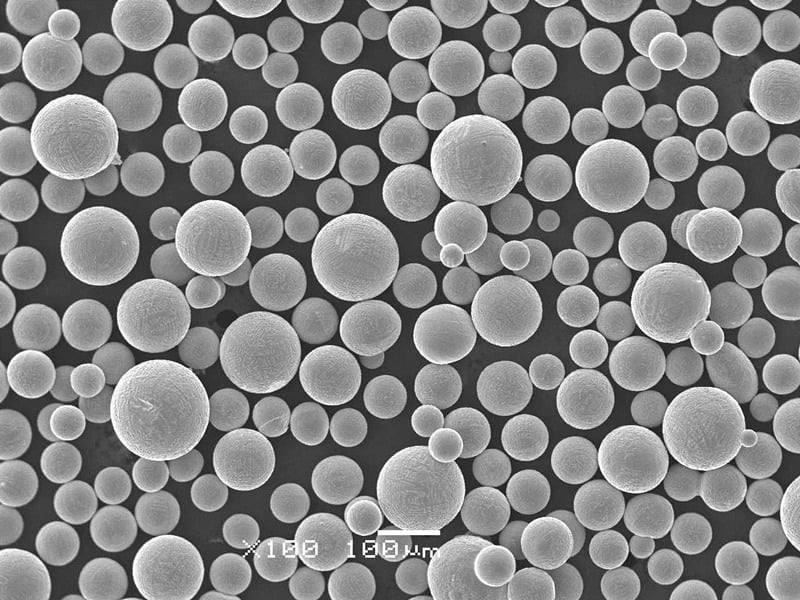
Types of Metal Powders Produced by PREP
Common Metal Powders:
Metaalpoeder | Compositie | Eigenschappen | Kenmerken |
---|---|---|---|
Titanium (Ti) | Pure Ti or Ti-6Al-4V | Hoge sterkte, corrosiebestendigheid | Biocompatible, lightweight |
Nikkel (Ni) | Pure Ni or Ni-based superalloys | Bestand tegen hoge temperaturen | Uitstekende kruipweerstand |
Kobalt (Co) | Pure Co or Co-Cr alloys | Wear resistance, strength | Gebruikt in tandheelkundige en orthopedische implantaten |
Aluminium (Al) | Pure Al or Al-Si alloys | Lichtgewicht, goede geleiding | Uitstekende bewerkbaarheid |
RVS | Various SS grades (304, 316, etc.) | Corrosiebestendigheid, sterkte | Veelzijdig, veel gebruikt |
Koper (Cu) | Zuiver Cu | Uitstekende elektrische geleidbaarheid | Gebruikt in elektrische onderdelen |
Wolfraam (W) | Pure W or W alloys | High density, heat resistance | Used in aerospace and defense |
IJzer (Fe) | Pure Fe or Fe-based alloys | Magnetische eigenschappen, sterkte | Widely used in engineering applications |
Zirkonium (Zr) | Pure Zr or Zr alloys | Corrosion resistance, biocompatible | Used in nuclear reactors and medical |
Molybdeen (Mo) | Pure Mo or Mo alloys | Sterkte bij hoge temperatuur | Used in aerospace and electronics |
Toepassingen van Plasma-Roterende Elektrode Proces
Typical Applications:
Applicatie | Beschrijving |
---|---|
additive manufacturing | Producing complex, high-strength components layer by layer with metal powders |
Lucht- en ruimtevaartcomponenten | Manufacturing lightweight, high-performance parts for aircraft and spacecraft |
Medische implantaten | Creating biocompatible implants with precise geometries, such as dental and orthopedic devices |
Auto-industrie | Producing lightweight, durable parts for vehicles |
Energiesector | Manufacturing components for nuclear reactors and power plants |
Elektronica | Producing conductive parts and heat sinks for electronic devices |
Gereedschappen en mallen | Creating durable, high-precision tooling and molds for various industries |
Specificaties, maten, kwaliteiten en normen
Detailed Specifications:
Metaalpoeder | Afmetingen (µm) | Rangen | Standaarden |
---|---|---|---|
Titanium (Ti) | 15-45, 45-90, 90-150 | Rang 1, Rang 2 | ASTM B348, ASTM F67 |
Nikkel (Ni) | 10-50, 50-100 | Inconel 625, 718 | ASTM B883 |
Kobalt (Co) | 10-45, 45-100 | CoCrMo, CoCrW | ASTM F75, ASTM F1537 |
Aluminium (Al) | 10-50, 50-150 | 6061, 7075 | ASTM B928, ASTM B209 |
RVS | 15-45, 45-90 | 304, 316L | ASTM A276, ASTM A240 |
Koper (Cu) | 15-45, 45-90 | C10100, C11000 | ASTM B152, ASTM B187 |
Wolfraam (W) | 10-45, 45-150 | Zuiver W | ASTM B777 |
IJzer (Fe) | 10-50, 50-100 | Pure Fe, FeSi | ASTM A848 |
Zirkonium (Zr) | 15-45, 45-90 | Zr702, Zr705 | ASTM B550 |
Molybdeen (Mo) | 10-45, 45-100 | Pure Mo | ASTM B387 |
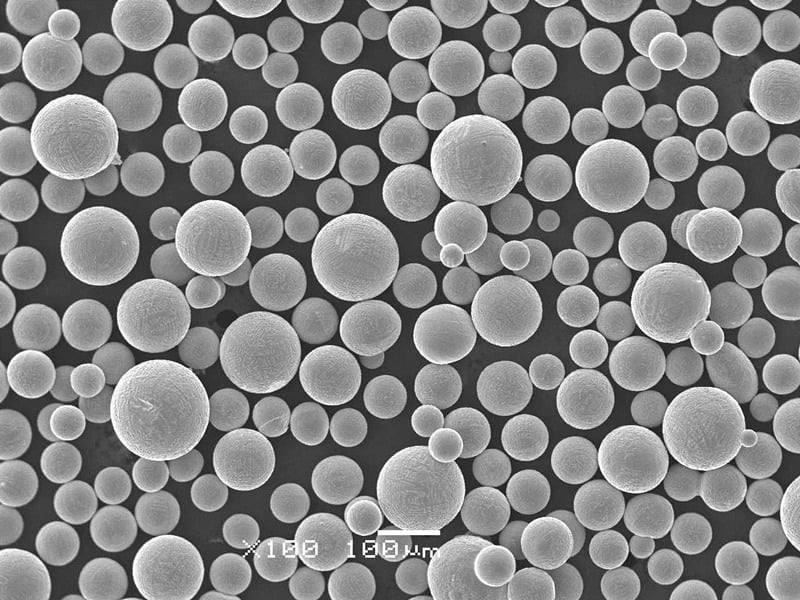
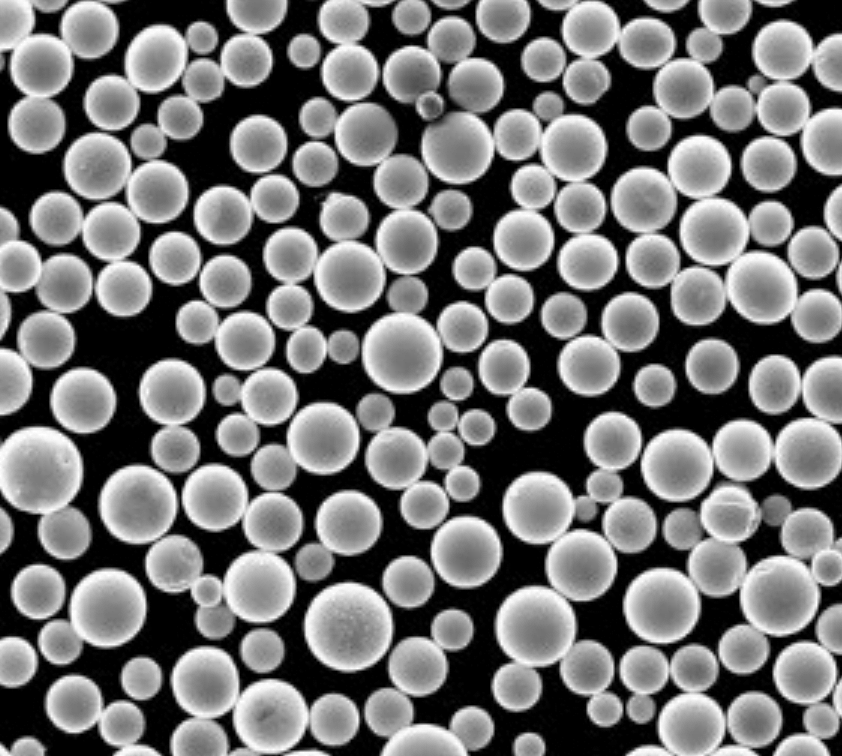
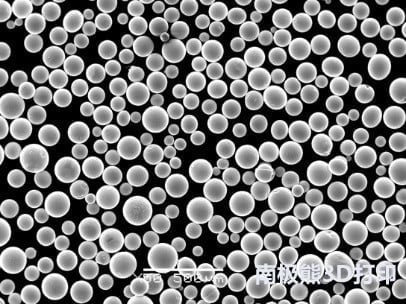
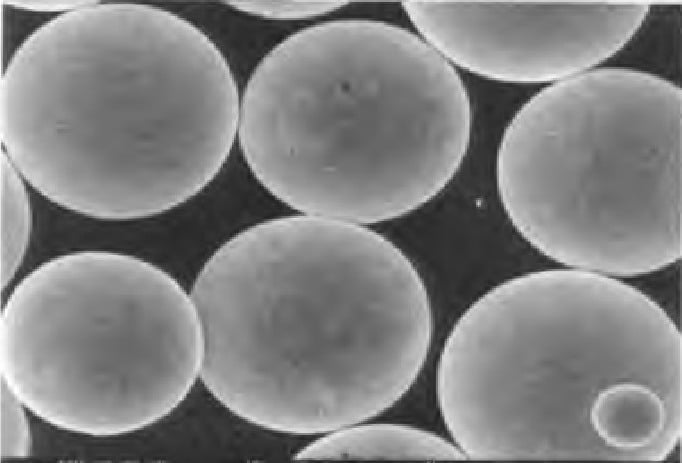
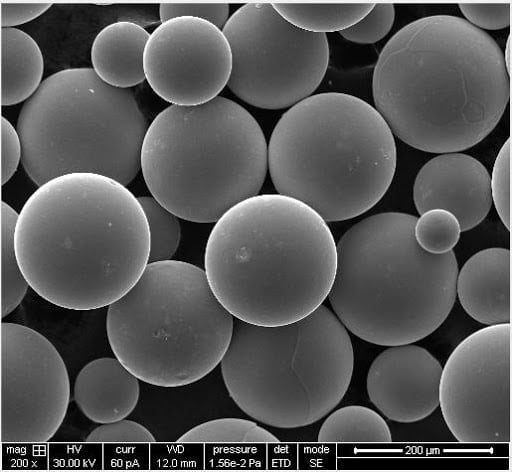
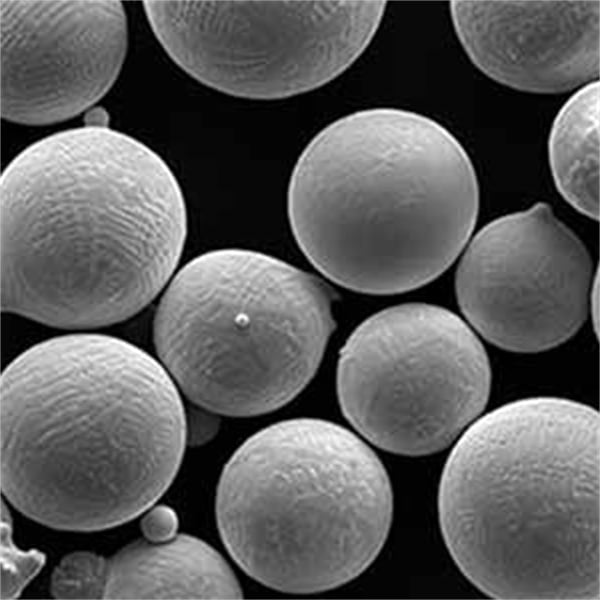
Leveranciers en prijsinformatie
Metal Powder Suppliers:
Provider | Aangeboden metaalpoeders | Prijs (per kg) | Aanvullende diensten |
---|---|---|---|
AP&C | Ti, Ni, Co, Al, SS, Cu, W, Fe, Zr | $150 – $500 | Custom particle size distribution |
GKN additief | Ti, Ni, Co, Al, SS, Cu, W, Fe, Zr | $100 – $450 | R&D support, custom alloy development |
Timmerman Technologie | Ti, Ni, Co, Al, SS, Cu, W, Fe, Zr | $120 – $480 | Material testing, certification |
LPW-technologie | Ti, Ni, Co, Al, SS, Cu, W, Fe, Zr | $130 – $490 | Powder recycling, characterization |
Höganäs | Ti, Ni, Co, Al, SS, Cu, W, Fe, Zr | $110 – $470 | Application engineering, support |
Voordelen en beperkingen van Plasma-Roterende Elektrode Proces
Pros and Cons:
Aspect | Voordelen | Beperkingen |
---|---|---|
Vorm van deeltjes | Produces spherical particles with high flowability and packing density | Limited control over particle size distribution |
Zuiverheid | High-purity powders due to the inert atmosphere and minimal contamination | High cost of production and equipment |
Uniformiteit | Uniform particle size and composition | Complexity in handling and maintenance of the equipment |
Veelzijdigheid | Suitable for a wide range of metals and alloys | Not suitable for all metals; some may not form spherical particles |
Kwaliteit | Consistent quality with minimal impurities | Initial setup and operational costs can be prohibitive for small-scale production |
TOEPASSINGEN | Widely used in high-tech applications requiring precision and reliability | Limited to industries that can justify the higher costs |
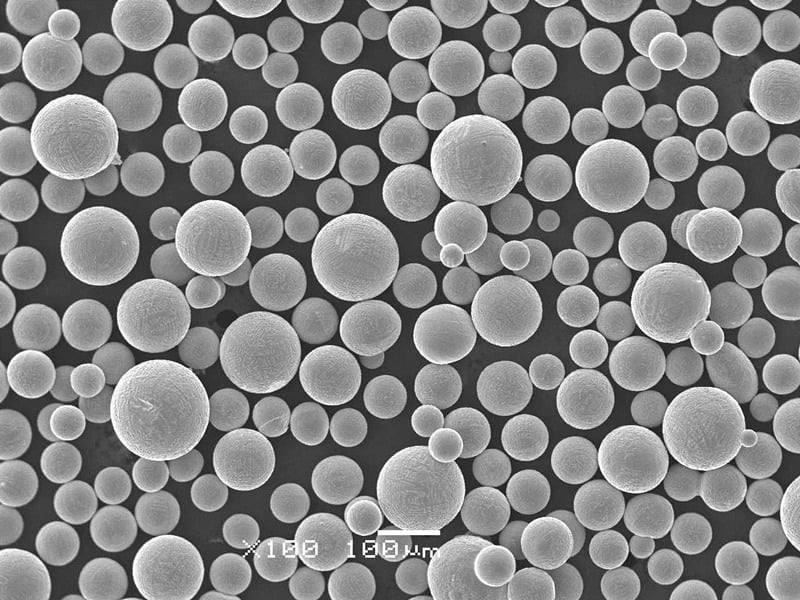
Detailed Analysis of Metal Powder Models
Titanium (Ti) and Titanium Alloys:
Titanium powders produced by PREP, such as pure titanium (Grade 1) and titanium alloys (Ti-6Al-4V), are highly valued for their high strength-to-weight ratio, corrosion resistance, and biocompatibility. These properties make them ideal for aerospace components, medical implants, and high-performance automotive parts. Titanium powders are characterized by their excellent flowability, which is crucial for additive manufacturing processes.
Nickel (Ni) and Nickel-Based Superalloys:
Nickel powders, including those of Inconel 625 and 718, are essential for high-temperature applications due to their exceptional resistance to oxidation and creep. These powders are widely used in the aerospace industry for turbine blades and other components that must withstand extreme conditions. The high purity and uniformity of PREP-produced nickel powders ensure optimal performance in these demanding environments.
Cobalt (Co) and Cobalt-Chromium Alloys:
Cobalt powders, particularly CoCr and CoCrMo alloys, are renowned for their wear resistance and strength. These properties make them suitable for medical implants, such as dental and orthopedic devices, where durability and biocompatibility are critical. The spherical shape and high density of PREP-produced cobalt powders contribute to their excellent performance in these applications.
Aluminum (Al) and Aluminum Alloys:
Aluminum powders, such as 6061 and 7075 alloys, are prized for their lightweight and good conductivity. These powders are extensively used in the automotive and aerospace industries to produce lightweight components that enhance fuel efficiency and performance. The fine, spherical particles produced by PREP ensure superior flowability and packing density, making them ideal for additive manufacturing.
Roestvrij staal:
Stainless steel powders, including grades 304 and 316L,
offer a balance of strength, corrosion resistance, and versatility. These powders are used across various industries, from construction to medical devices, due to their durability and ease of fabrication. The PREP process ensures that the stainless steel powders have consistent quality and uniform particle size, which are essential for reliable performance.
Copper (Cu) and Copper Alloys:
Copper powders, such as C10100 and C11000, are essential for their excellent electrical conductivity and thermal properties. These powders are widely used in electronics, electrical components, and heat exchangers. The high purity and spherical shape of PREP-produced copper powders enhance their performance in these applications, ensuring efficient conductivity and heat transfer.
Tungsten (W) and Tungsten Alloys:
Tungsten powders are known for their high density and heat resistance, making them suitable for applications in the aerospace and defense industries. The spherical particles produced by PREP ensure uniform packing and flowability, which are crucial for manufacturing high-performance components such as rocket nozzles and radiation shielding.
Iron (Fe) and Iron-Based Alloys:
Iron powders, including pure iron and iron-silicon alloys, are widely used in engineering applications due to their magnetic properties and strength. These powders are essential for producing components such as magnetic cores and structural parts. The PREP process ensures high purity and uniform particle size, which are critical for consistent performance.
Zirconium (Zr) and Zirconium Alloys:
Zirconium powders, such as Zr702 and Zr705, are valued for their corrosion resistance and biocompatibility. These properties make them ideal for medical applications, including implants and surgical instruments, as well as for use in nuclear reactors. The spherical shape and high purity of PREP-produced zirconium powders ensure reliable performance in these critical applications.
Molybdenum (Mo) and Molybdenum Alloys:
Molybdenum powders are prized for their high-temperature strength and conductivity. These powders are used in the aerospace and electronics industries for components that must withstand extreme conditions. The PREP process produces molybdenum powders with uniform particle size and high purity, ensuring their effectiveness in demanding applications.
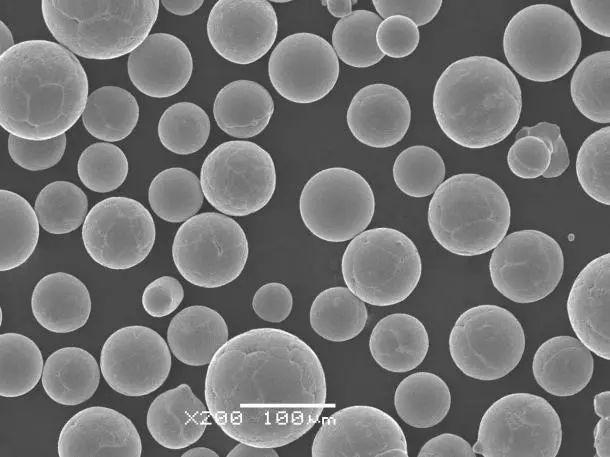
FAQ's
Vraag | Antwoord |
---|---|
What is the Plasma-Rotating Electrode Process (PREP)? | PREP is a method for producing high-purity, spherical metal powders by melting the end of a rotating metal rod using a plasma arc. |
What metals can be processed using PREP? | PREP can process a wide range of metals, including titanium, nickel, cobalt, aluminum, stainless steel, copper, tungsten, iron, zirconium, and molybdenum. |
What are the advantages of using PREP for metal powder production? | PREP offers high purity, uniform particle size, excellent flowability, and the ability to produce spherical particles, making it ideal for high-tech applications. |
What are the limitations of PREP? | The process is expensive, requires complex equipment, and is not suitable for all metals. Additionally, controlling particle size distribution can be challenging. |
How are PREP-produced powders used in additive manufacturing? | These powders are used in additive manufacturing to create complex, high-strength components layer by layer, offering precision and reliability in critical applications. |
Why are spherical particles important in metal powders? | Spherical particles ensure better flowability and packing density, which are crucial for consistent performance in applications such as additive manufacturing and powder metallurgy. |
Can PREP be used for producing metal powders for medical implants? | Yes, PREP-produced powders such as titanium and cobalt-chromium alloys are commonly used for creating biocompatible medical implants with precise geometries. |
What are the key applications of PREP-produced nickel-based superalloys? | Nickel-based superalloys produced by PREP are used in high-temperature applications, such as turbine blades in the aerospace industry, due to their excellent oxidation and creep resistance. |
How does the cost of PREP-produced powders compare to other methods? | PREP-produced powders are generally more expensive due to the high cost of the process and equipment, but they offer superior quality and performance for critical applications. |
Are there any environmental concerns with the PREP process? | PREP is performed in an inert atmosphere, which minimizes contamination and environmental impact, but the energy-intensive nature of the process can be a concern. |
Conclusie
The Plasma-Rotating Electrode Process (PREP) stands out as a premier method for producing high-quality metal powders essential for various advanced applications. From aerospace components to medical implants, the purity, uniformity, and spherical shape of PREP-produced powders ensure superior performance and reliability. While the process comes with high costs and complex equipment requirements, its advantages make it a valuable technology in industries where precision and quality are paramount. As technology advances, further innovations in PREP are likely to enhance its efficiency and broaden its applicability, solidifying its role in the future of material science and engineering.
Over 3DP mETAL
Productcategorie
NEEM CONTACT OP
Vragen? Stuur ons nu een bericht! Na ontvangst van uw bericht gaan we met een heel team uw aanvraag verwerken.