Imagine a world where complex metal parts are crafted not through traditional machining, but layer by layer, with each layer meticulously built using tiny metallic particles. This futuristic vision is already a reality thanks to Additive Manufacturing (AM), also known as 3D printing. But what fuels this revolution? Enter the unsung hero – gas atomized powder.
Charakterystyka Proszek rozpylany gazem
Gas atomized powder is a type of metal powder produced through a specialized technique. Unlike other methods that might result in irregularly shaped particles, gas atomization delivers a product with a distinct set of characteristics:
- Spherical Shape: Gas atomized powders boast a near-perfect spherical shape. Think of tiny metal ball bearings. This spherical morphology offers several advantages. It allows for smooth and consistent flow during the AM process, minimizing disruptions and ensuring a flawless final product.
- Tight Particle Size Distribution: The size of these powder particles isn’t random. The atomization process allows for precise control over the particle size distribution. This control is crucial for achieving optimal packing density when building parts layer by layer. Imagine pouring sand versus ball bearings – the ball bearings, with their uniform size, pack together much more efficiently.
- Low Impurity Levels: Gas atomization often takes place in an inert gas environment, like argon or nitrogen. This minimizes contamination from oxygen or nitrogen, which can negatively affect the final properties of the metal parts.
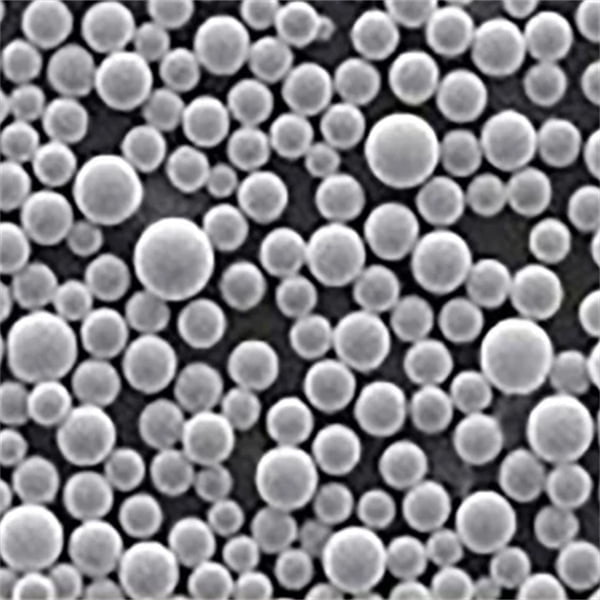
The Process Flow of Gas Atomized Powder
Creating these tiny metallic marvels involves a multi-step process:
- Topienie metalu: The journey begins with the chosen metal or alloy being melted in a crucible under controlled conditions. Imagine a high-tech furnace transforming solid metal into a molten liquid.
- Atomizacja: The molten metal is then forced through a nozzle at high pressure. Simultaneously, a high-velocity gas jet, typically inert gas like argon, breaks the metal stream into tiny droplets. This is akin to using a high-powered water spray to break up a garden hose stream into a fine mist.
- Szybkie krzepnięcie: As the metal droplets travel through the gas stream, they rapidly cool and solidify into individual powder particles. This rapid cooling process allows for the formation of fine-grained microstructures within the particles, leading to superior mechanical properties in the final product.
- Classification and Collection: The cooled powder particles are then classified by size using various techniques like sieving or air classification. Finally, the desired size fraction is collected for further processing or use in AM.
The Influencing Factors of Gas Atomized Powder
The quality and properties of gas atomized powder are influenced by several factors:
- Metal Properties: The type of metal or alloy being processed plays a significant role. Metals with higher melting points may require adjustments in the atomization process for optimal results.
- Atomization Parameters: The pressure of the gas jet, the flow rate of the molten metal, and the distance between the nozzle and the collection chamber all impact the final characteristics of the powder. Just like adjusting the settings on a paint sprayer can affect the outcome, these parameters need to be fine-tuned for each specific material.
- Cooling Rate: The rate at which the molten metal droplets solidify significantly impacts the final microstructure of the powder particles. A faster cooling rate generally results in finer grains, which can enhance certain mechanical properties.
Zastosowania Proszek rozpylany gazem
Gas atomized powders are the workhorses of various industries:
- Produkcja przyrostowa: As mentioned earlier, gas atomized powders are the primary feedstock for many AM processes. From aerospace components to medical implants, these powders are building the future layer by layer.
- Formowanie wtryskowe metalu (MIM): MIM utilizes gas atomized powders to create complex near-net-shape metal parts. This process offers advantages like high dimensional accuracy and mass production capabilities.
- Natryskiwanie termiczne: Gas atomized powders are used to coat surfaces with specific properties like wear resistance or corrosion protection. Imagine spraying a layer of tiny metal particles onto a surface, creating a new “skin” with enhanced functionalities.
- Lutowanie: Brazing involves joining two or more metal parts using a filler metal that melts at a lower temperature. Gas atomized powders can be used as brazing filler metals, offering benefits like controlled flow and precise placement.
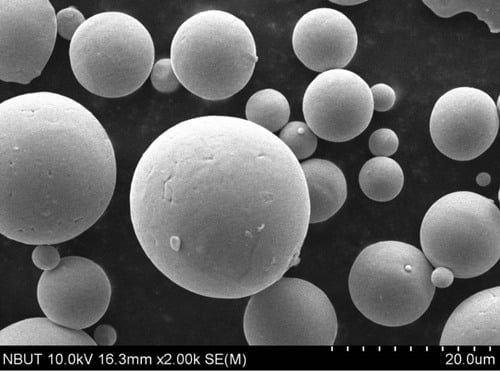
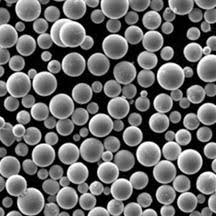
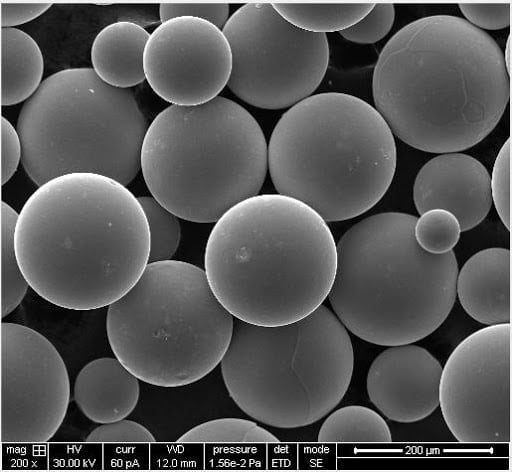
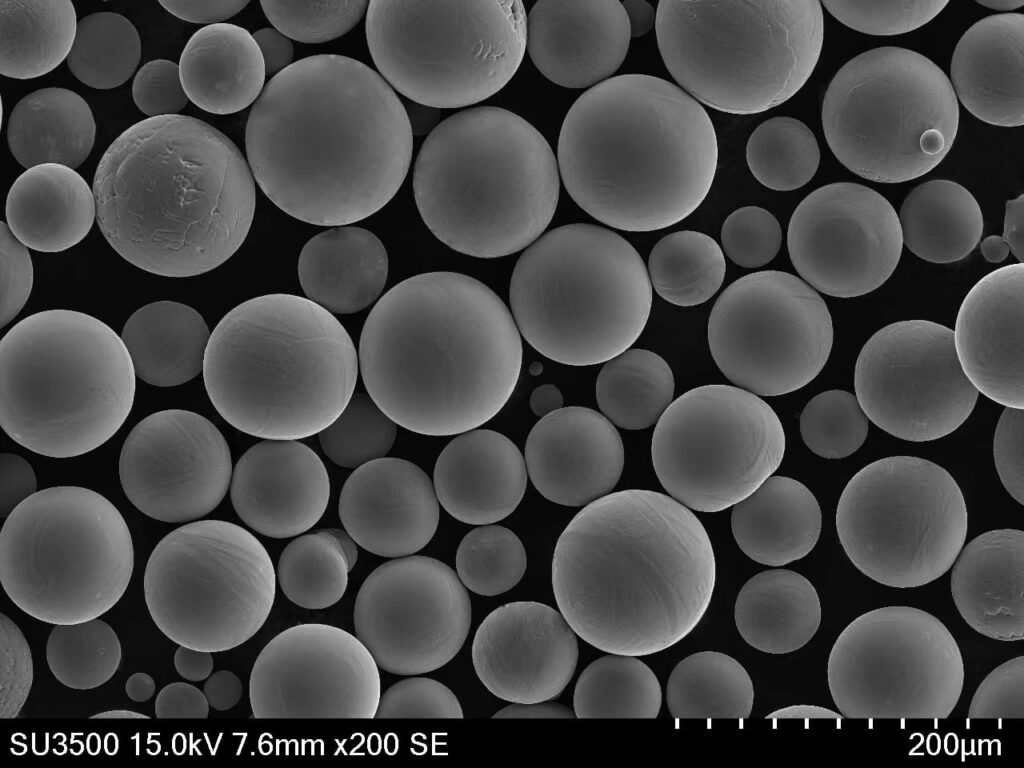
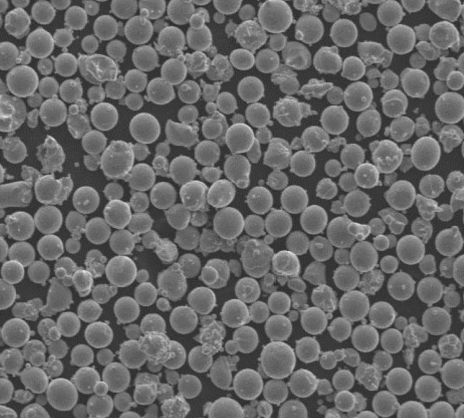
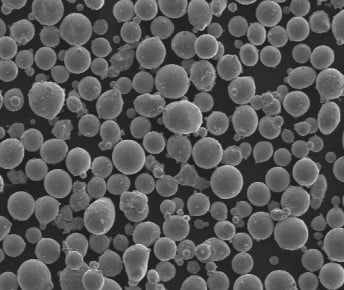
The Development Trend of Gas Atomized Powder
The world of gas atomized powders is constantly evolving, with advancements happening on multiple fronts:
- Nowe materiały: Researchers are continuously developing new alloys and material compositions specifically optimized for AM and other applications. This allows for the creation of parts with unique combinations of properties.
- Drobniejsze proszki: The ability to produce even finer gas atomized powders is an ongoing area of research. Finer powders can enable the creation of highly detailed and intricate parts through AM.
- Zrównoważony rozwój: Minimizing the environmental impact of gas atomization is a growing concern. Research is underway to develop processes that use recycled materials and reduce energy consumption during production.
Advantages and Considerations of Gas Atomized Powders
While gas atomized powders offer numerous benefits, there are also some considerations to keep in mind:
Zalety:
- Superior Powder Characteristics: The spherical shape, tight size distribution, and low impurity levels of gas atomized powders make them ideal for various applications, particularly AM.
- Szeroka kompatybilność materiałowa: Gas atomization can handle a wide range of metals and alloys, offering flexibility in material selection.
- Consistent Quality: The controlled nature of the gas atomization process ensures consistent powder quality, leading to predictable results in downstream applications.
Rozważania:
- Koszt: Gas atomization is a complex and energy-intensive process, which can be reflected in the cost of the powder compared to other methods.
- Health and Safety: Handling fine metal powders requires proper safety precautions to minimize inhalation risks and potential explosions.
Gas Atomized Powder vs. Other Metal Powders
Gas atomized powders aren’t the only players in the metal powder game. Here’s a quick comparison with other common methods:
- Atomizacja wody: This method utilizes a water jet to break up molten metal. While cost-effective, water atomized powders tend to have irregular shapes and higher oxygen content, making them less suitable for demanding applications like AM.
- Atomizacja plazmowa: This technique employs a high-temperature plasma torch to melt and atomize the metal. Plasma atomized powders can achieve finer sizes compared to gas atomization and are suitable for high-melting-point materials. However, the process is typically more expensive.
Przyszłość Gas Atomized Powders
As AM and other advanced manufacturing techniques continue to evolve, the demand for high-quality gas atomized powders is expected to surge. Here’s a glimpse into what the future might hold:
- Increased Production Capacity: With the growing adoption of AM, manufacturers are likely to invest in expanding gas atomization capabilities to meet the rising demand for powders.
- Advanced Process Control: Expect advancements in automation and process control to further optimize the gas atomization process for efficiency, consistency, and minimal waste generation.
- Nowe aplikacje: Gas atomized powders might find applications in new and innovative areas beyond traditional industries, potentially revolutionizing fields like electronics and energy storage.
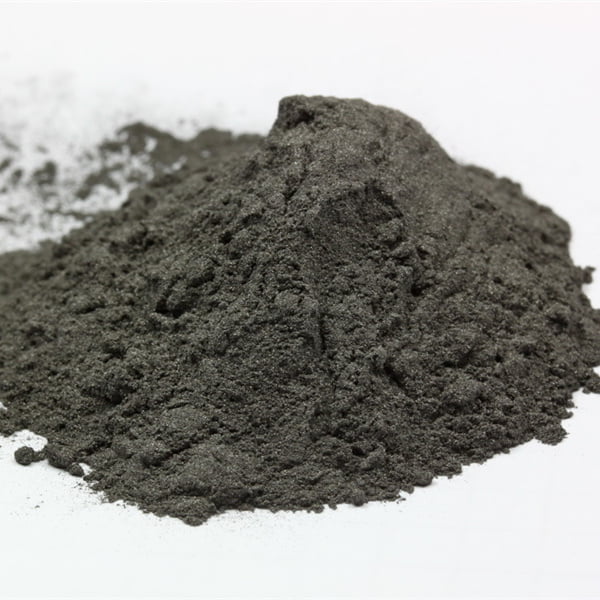
FAQ
Table 1: Frequently Asked Questions on Gas Atomized Powders
Pytanie | Odpowiedź |
---|---|
Jakie są korzyści ze stosowania proszków rozpylanych gazowo? | Gas atomized powders offer several advantages, including spherical shape, tight size distribution, low impurity levels, broad material compatibility, and consistent quality. |
What are some applications of gas atomized powders? | Gas atomized powders are used in various industries, including Additive Manufacturing (AM), Metal Injection Molding (MIM), thermal spraying, and brazing. |
How does gas atomization compare to other metal powder production methods? | Gas atomization offers superior powder characteristics compared to water atomization, while being potentially more cost-effective than plasma atomization. The ideal method depends on the specific application and material requirements. |
What are the limitations of gas atomized powders? | The primary considerations include the potentially higher cost compared to other methods and the need for proper handling procedures due to the fine particle size. |
What does the future hold for gas atomized powders? | The future is bright for gas atomized powders, with anticipated growth in production capacity, advancements in process control, and exploration of new applications across various industries. |
Wniosek
Gas atomized powder plays a pivotal role in shaping the future of manufacturing. These tiny metallic marvels are the building blocks for complex components, intricate structures, and innovative solutions. As technology continues to advance, gas atomized powders will undoubtedly be at the forefront, enabling us to create a world limited only by our imagination.
Informacje o 3DP mETAL
Kategoria produktu
SKONTAKTUJ SIĘ Z NAMI
Masz jakiekolwiek pytania? Wyślij nam wiadomość już teraz! Po otrzymaniu wiadomości przetworzymy Twoje zapytanie z całym zespołem.