Maszyny do formowania metalu od wieków stanowią podstawę produkcji metalowej, tworząc wszystko, od skomplikowanych urządzeń medycznych po potężne silniki napędzające nasze samochody. Jednak krajobraz formowania metalu szybko ewoluuje, a nowe technologie i materiały przesuwają granice tego, co jest możliwe. W tym kompleksowym przewodniku zagłębimy się w fascynujący świat maszyn do formowania metalu, badając ich typy, zastosowania, zalety i rozważania.
Przegląd maszyn do formowania metalu
Wyobraź sobie rzeźbiarza skrupulatnie kształtującego glinę w arcydzieło. Maszyny do formowania metalu działają na podobnej zasadzie, ale zamiast gliny manipulują stopionym metalem lub proszkami metalowymi w złożone i precyzyjne kształty. Maszyny te występują w różnych formach, z których każda ma swoje mocne strony i idealne zastosowania. Niektóre popularne typy obejmują:
- Maszyny do odlewania ciśnieniowego: Te woły robocze przemysłu wtryskują stopiony metal pod wysokim ciśnieniem do formy wielokrotnego użytku (matrycy). Doskonale sprawdzają się w produkcji dużych ilości skomplikowanych części o doskonałej dokładności wymiarowej.
- Maszyny do odlewania metodą traconego wosku: Ten skomplikowany proces polega na stworzeniu woskowego wzoru pożądanej części, umieszczeniu go w ceramicznej formie, a następnie wypaleniu wosku. Stopiony metal jest następnie wlewany do ceramicznej skorupy, tworząc odlew o kształcie zbliżonym do siatki z wyjątkowymi szczegółami.
- Maszyny do odlewania piasku: Najbardziej tradycyjna metoda, odlewanie w piasku, wykorzystuje formę wyrzeźbioną z piasku. Stopiony metal jest wlewany do wnęki, a po zestaleniu piasek jest usuwany, aby odsłonić gotowy produkt. Odlewanie w piasku jest znane ze swojej wszechstronności i przystępnej ceny, ale dokładność wymiarowa może być mniej precyzyjna w porównaniu z innymi metodami.
- Maszyny do formowania wtryskowego metali (MIM): Ta innowacyjna technologia łączy w sobie aspekty formowania wtryskowego tworzyw sztucznych z metalurgią proszków. Metalowy proszek zmieszany ze spoiwem jest wtryskiwany do formy, a następnie spoiwo jest usuwane w procesie usuwania spoiwa. Na koniec część jest spiekana w celu uzyskania ostatecznej wytrzymałości i właściwości. MIM jest idealnym rozwiązaniem dla złożonych części o kształcie zbliżonym do siatki, o dobrej dokładności wymiarowej i właściwościach materiału zbliżonych do metali kutych.
To tylko rzut oka na zróżnicowany świat maszyn do formowania metalu. Każdy typ oferuje unikalne zalety i zaspokaja określone potrzeby.
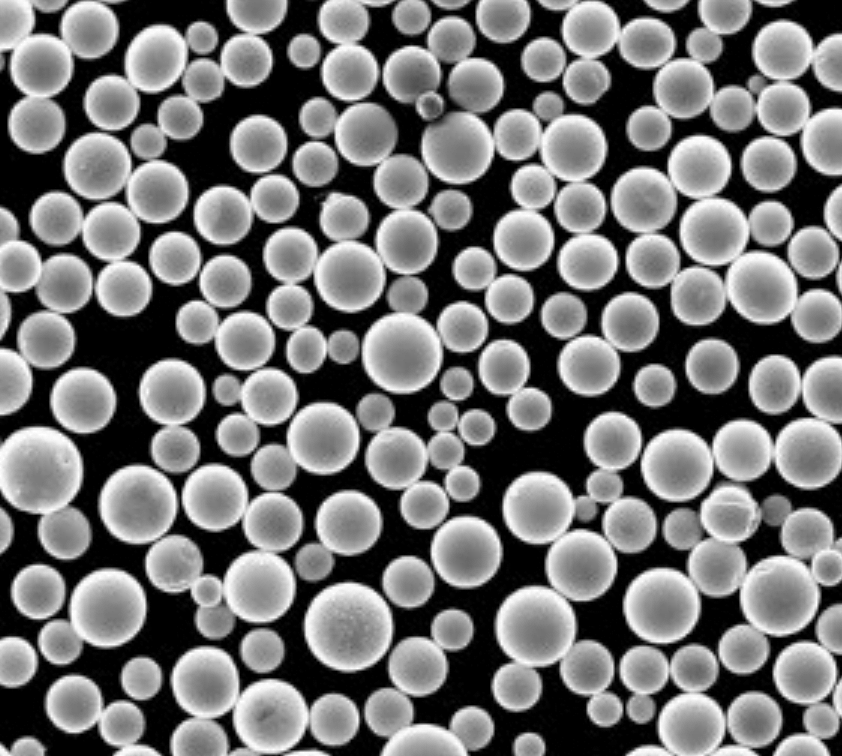
Proszki metali do formowania: Menażeria materiałów
Formowanie metali to nie tylko maszyny; wybór proszku metalowego znacząco wpływa na właściwości i zastosowania produktu końcowego. Oto kilka powszechnie stosowanych proszków metali do formowania:
1. Proszki ze stali nierdzewnej: Oferując doskonałą odporność na korozję i dobre właściwości mechaniczne, proszki ze stali nierdzewnej są szeroko stosowane w aplikacjach takich jak urządzenia medyczne, elementy pomp i części samochodowe.
2. Proszki stali narzędziowej: Znane z wysokiej odporności na zużycie i twardości proszki stali narzędziowej są idealne do tworzenia narzędzi skrawających, matryc i form.
3. Proszki aluminiowe: Lekkie i oferujące dobrą przewodność proszki aluminiowe są popularne w zastosowaniach w przemyśle lotniczym, elektronicznym i motoryzacyjnym ze względu na ich właściwości zmniejszające wagę.
4. Proszki na bazie niklu: Wykazując wyjątkową wytrzymałość w wysokich temperaturach i odporność na korozję, proszki na bazie niklu cieszą się dużym popytem na komponenty w silnikach odrzutowych, turbinach oraz w poszukiwaniach ropy i gazu.
5. Proszki tytanowe: Znane z wyjątkowego stosunku wytrzymałości do wagi i biokompatybilności, proszki tytanowe są stosowane w komponentach lotniczych, implantach medycznych i wysokiej jakości sprzęcie sportowym.
6. Proszki miedzi: Wysoce przewodzące i plastyczne proszki miedzi są stosowane w komponentach elektrycznych, radiatorach i aplikacjach wymagających doskonałego zarządzania temperaturą.
7. Proszki żelaza: Proszki żelaza, będące podstawowym materiałem wśród proszków metalowych, oferują dobre właściwości mechaniczne i przystępną cenę. Są one szeroko stosowane w komponentach samochodowych, przekładniach i częściach konstrukcyjnych.
8. Proszki kobaltowo-chromowe: Oferując połączenie wysokiej wytrzymałości, odporności na korozję i biokompatybilności, proszki kobaltowo-chromowe są stosowane w implantach medycznych, protetyce dentystycznej i elementach odpornych na zużycie.
9. Proszki Kovar: Dzięki współczynnikowi rozszerzalności cieplnej, który ściśle odpowiada szkłu, proszki Kovar są idealne do zastosowań wymagających hermetycznego uszczelnienia między metalem a szkłem, np. w opakowaniach elektronicznych.
10. Proszki Inconel: Proszki Inconel, należące do rodziny nadstopów niklowo-chromowych znanych z wyjątkowej wytrzymałości w wysokich temperaturach i odporności na utlenianie, są wykorzystywane w takich zastosowaniach jak komponenty silników odrzutowych, wymienniki ciepła i sprzęt do przetwarzania chemicznego.
To tylko wybór z szerokiej gamy proszków metalowych dostępnych do formowania. Każdy materiał oferuje unikalne korzyści i względy, dzięki czemu proces wyboru jest kluczowym krokiem w formowaniu metali.
właściwości i zastosowania niektórych popularnych proszków metali
Metalowy proszek | Właściwości | APLIKACJE |
---|---|---|
Stal nierdzewna | Odporność na korozję, dobre właściwości mechaniczne | Urządzenia medyczne, komponenty pomp, części samochodowe |
Stal narzędziowa | Wysoka odporność na zużycie, twardość | Narzędzia tnące, matryce, formy. |
Na bazie niklu | Wyjątkowa wytrzymałość na wysokie temperatury, odporność na korozję | Komponenty silników odrzutowych, turbiny, wydobycie ropy i gazu |
Tytan | Wyjątkowy stosunek wytrzymałości do wagi, biokompatybilność | Komponenty lotnicze, implanty medyczne, wysokowydajne artykuły sportowe |
Miedź | Wysoce przewodzący, ciągliwy | Komponenty elektryczne, radiatory, aplikacje wymagające doskonałego zarządzania temperaturą |
Żelazo | Dobre właściwości mechaniczne, przystępna cena | Komponenty motoryzacyjne, przekładnie, części konstrukcyjne |
Kobalt-chrom | Wysoka wytrzymałość, odporność na korozję, biokompatybilność | Implanty medyczne, protetyka dentystyczna, komponenty odporne na zużycie |
Kovar | Współczynnik rozszerzalności cieplnej pasuje do szkła | Aplikacje wymagające hermetycznego uszczelnienia między metalem a szkłem (opakowania elektroniczne) |
Inconel | Wyjątkowa wytrzymałość na wysokie temperatury, odporność na utlenianie | Komponenty silników odrzutowych, wymienniki ciepła, sprzęt do przetwarzania chemicznego |
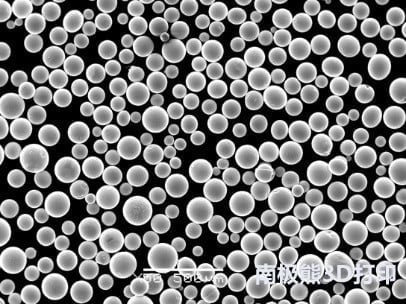
Więcej niż podstawy: Głębsze spojrzenie na proszki metali
Chociaż powyższa tabela stanowi punkt wyjścia, świat proszków metali jest pełen złożoności. Oto kilka dodatkowych czynników, które należy wziąć pod uwagę przy wyborze proszku metalowego do formowania:
- Rozmiar i rozkład cząstek: Rozmiar i rozmieszczenie cząstek proszku metalu znacząco wpływają na właściwości produktu końcowego. Drobniejsze proszki generalnie wytwarzają części o gładszych powierzchniach i lepszej dokładności wymiarowej, ale mogą być również trudniejsze w przepływie i mogą wymagać specjalnych technik formowania. Z kolei grubsze proszki oferują lepszą charakterystykę przepływu, ale mogą skutkować bardziej szorstkim wykończeniem powierzchni i potencjalnie wpływać na tolerancje wymiarowe.
- Czystość proszku: Obecność zanieczyszczeń w proszku metalu może mieć negatywny wpływ na właściwości mechaniczne produktu końcowego, odporność na korozję i ogólną wydajność. Wybór proszków o wysokiej czystości zapewnia spójne i niezawodne wyniki.
- Zachowanie podczas spiekania: Proces spiekania polega na podgrzaniu proszku metalu do określonej temperatury poniżej jego temperatury topnienia, co pozwala cząsteczkom połączyć się ze sobą i utworzyć stałą część. Różne proszki metali wykazują różne właściwości spiekania, co wymaga dostosowania czasu, temperatury i atmosfery podczas procesu spiekania w celu osiągnięcia optymalnych wyników.
- Obróbka powierzchni: Niektóre proszki metali mogą być poddane wstępnej obróbce za pomocą środków smarnych lub innych modyfikatorów powierzchni, aby poprawić płynność, zmniejszyć tarcie podczas formowania i poprawić właściwości produktu końcowego.
Znaczenie wyboru proszku: Równowaga
Wybór odpowiedniego proszku metalowego do projektu formowania wymaga starannego rozważenia pożądanych właściwości, wymagań aplikacji i czynników kosztowych. Często jest to balansowanie, ważenie zalet i ograniczeń różnych materiałów. Ścisła współpraca z renomowanym dostawcą proszków metalowych i wykwalifikowanym ekspertem w dziedzinie formowania metali może zapewnić wybór optymalnego materiału do konkretnych potrzeb.
Zastosowania Maszyny do formowania metalu
Maszyny do formowania metalu są wszechstronnymi końmi roboczymi przemysłu wytwórczego, kształtującymi metal w szeroką gamę produktów w różnych sektorach. Oto wgląd w aplikacje, które wykorzystują moc formowania metalu:
- Motoryzacja: Od skomplikowanych elementów silnika, takich jak tłoki i głowice cylindrów, po lekkie części nadwozia i elementy konstrukcyjne, formowanie metali odgrywa kluczową rolę w nowoczesnych pojazdach. Zdolność do wytwarzania złożonych kształtów z wysoką precyzją i powtarzalnością sprawia, że formowanie metalu jest idealne dla wymagających wymagań przemysłu motoryzacyjnego.
- Astronautyka: Poszukiwanie lekkich, a jednocześnie wytrzymałych materiałów w zastosowaniach lotniczych znajduje idealnego partnera w formowaniu metali. Od komponentów silników odrzutowych, takich jak łopatki turbin i komory spalania, po struktury płatowca, technologie formowania metali, takie jak fuzja proszkowa tytanu i aluminium (PBF), przesuwają granice tego, co jest możliwe w projektowaniu samolotów.
- Urządzenia medyczne: Zapotrzebowanie na biokompatybilne i wysoce precyzyjne komponenty w urządzeniach medycznych jest doskonale zaspokajane przez formowanie metali. Od implantów ortopedycznych, takich jak protezy stawu biodrowego i kolanowego, po narzędzia chirurgiczne i protezy dentystyczne, technologie formowania metali, takie jak odlewanie precyzyjne i MIM, są wykorzystywane do tworzenia urządzeń ratujących i poprawiających jakość życia.
- Elektronika użytkowa: Wszechobecność elektroniki w naszym codziennym życiu opiera się w dużej mierze na formowaniu metali w celu uzyskania skomplikowanych i niezawodnych komponentów. Od maleńkich złączy w smartfonach po radiatory, które rozpraszają ciepło w laptopach, formowanie metali zapewnia płynne działanie naszych urządzeń elektronicznych.
- Maszyny przemysłowe: Trwałość i wysoka wydajność to cechy charakterystyczne maszyn przemysłowych, a formowanie metali spełnia te wymagania. Koła zębate, łożyska i inne krytyczne elementy sprzętu przemysłowego są często produkowane przy użyciu technik formowania metali, takich jak odlewanie piaskowe i odlewanie ciśnieniowe, zapewniając solidne i niezawodne działanie.
To tylko kilka przykładów, a potencjalne zastosowania maszyn do formowania metalu wykraczają daleko poza nie. Od skomplikowanego działania mechanicznego zegarka po potężne turbiny generujące energię elektryczną, formowanie metalu kształtuje otaczający nas świat na niezliczone sposoby.
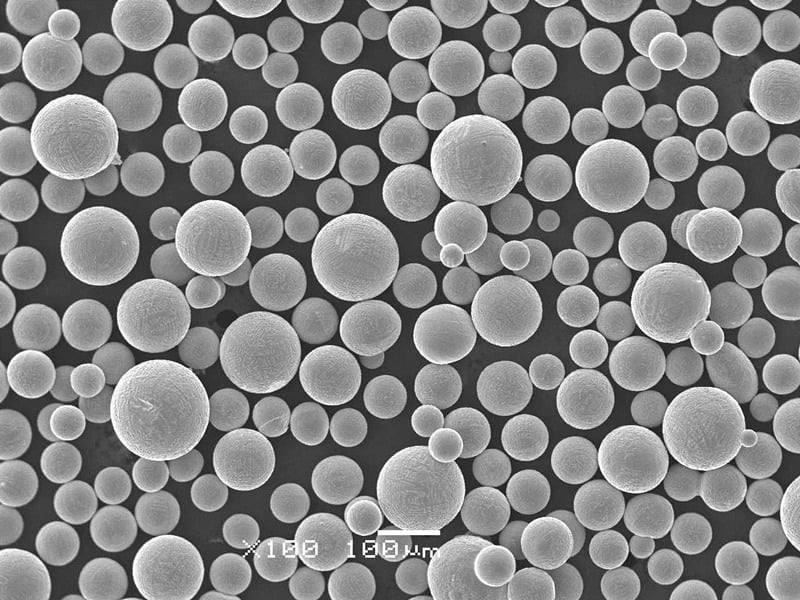
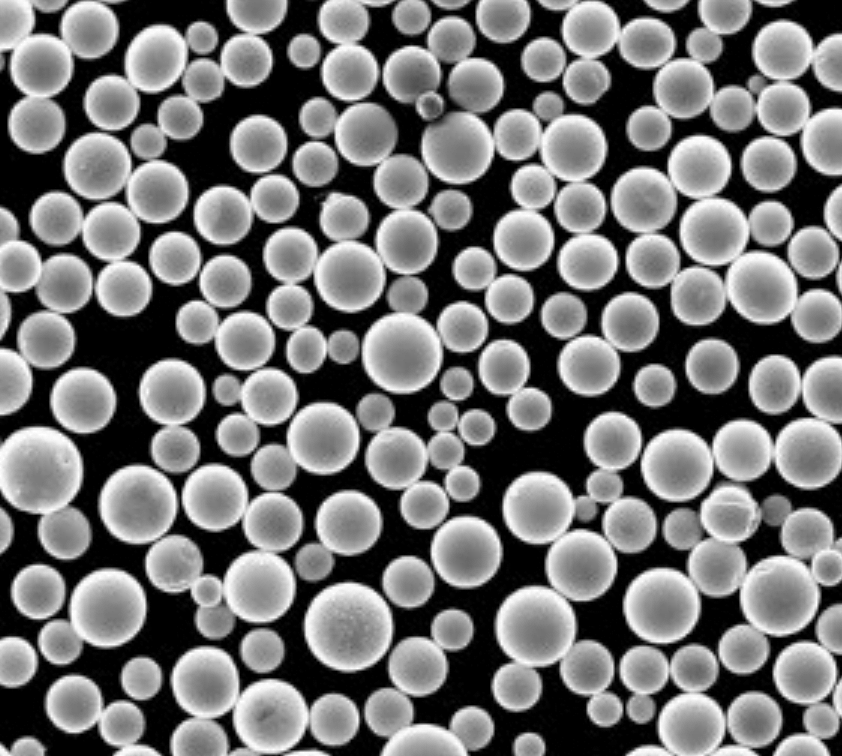
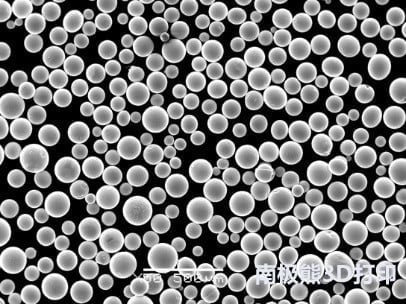
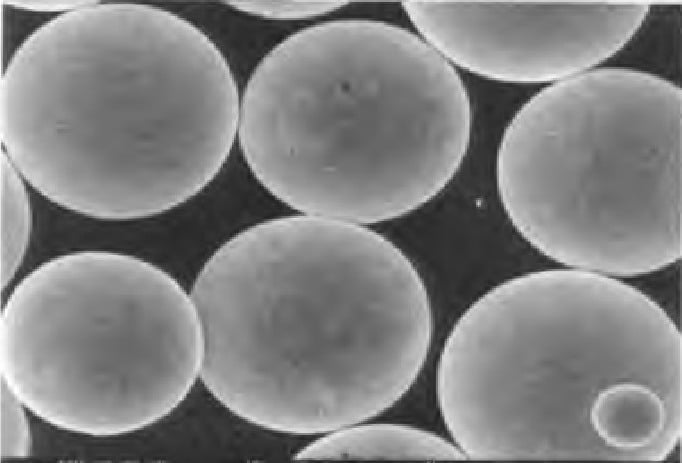
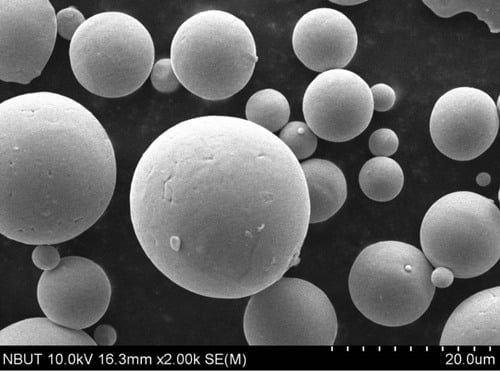
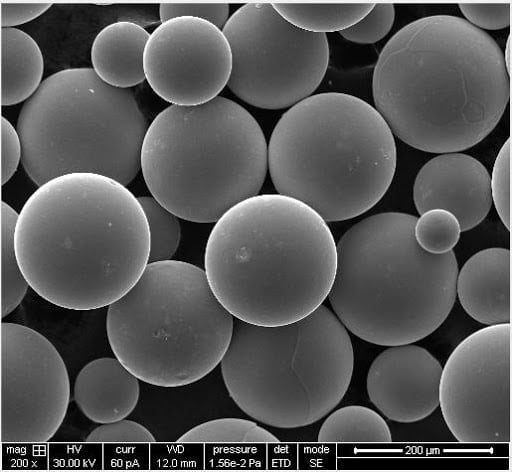
Zalety maszyn do formowania metalu: Zwycięska kombinacja
Maszyny do formowania metalu oferują atrakcyjne połączenie zalet, które uczyniły je kamieniem węgielnym przemysłu metalowego. Oto niektóre z kluczowych korzyści, które sprawiają, że są one tak korzystnym wyborem:
- Elastyczność konstrukcji: W przeciwieństwie do tradycyjnych technik produkcji subtraktywnej, takich jak obróbka skrawaniem, formowanie metalu pozwala na tworzenie złożonych geometrii i skomplikowanych kształtów. Ta swoboda projektowania umożliwia inżynierom przekraczanie granic funkcjonalności i tworzenie innowacyjnych produktów.
- Wysoka precyzja i powtarzalność: Maszyny do formowania metalu mogą produkować części o wyjątkowej dokładności wymiarowej i wysokim stopniu spójności. Jest to szczególnie korzystne w przypadku zastosowań wymagających precyzyjnych tolerancji i wymiennych części.
- Zdolność do produkcji masowej: Niektóre techniki formowania metali, takie jak odlewanie ciśnieniowe, doskonale sprawdzają się w produkcji wielkoseryjnej. To czyni je idealnymi do produkcji dużych ilości części w sposób wydajny i opłacalny.
- Wszechstronność materiału: Maszyny do formowania metalu mogą obsługiwać szeroką gamę proszków metalowych, od popularnych materiałów, takich jak aluminium i stal, po bardziej egzotyczne opcje, takie jak tytan i stopy niklu. Ta wszechstronność pozwala producentom dostosować wybór materiału do konkretnych potrzeb aplikacji.
- Near-Net-Shape Manufacturing: Niektóre techniki formowania metalu, takie jak MIM, mogą wytwarzać części bardzo zbliżone do ich ostatecznego kształtu. Minimalizuje to potrzebę wykonywania obszernych etapów obróbki końcowej, skracając czas i koszty produkcji.
- Zmniejszona ilość odpadów materiałowych: W porównaniu z technikami produkcji subtraktywnej, które generują znaczną ilość odpadów, formowanie metalu oferuje bardziej wydajne wykorzystanie materiałów. Przekłada się to na oszczędność kosztów i mniejszy wpływ na środowisko.
Poza oczywistością: dodatkowe korzyści do rozważenia
Podczas gdy podstawowe zalety wymienione powyżej są dobrze ugruntowane, istnieją dodatkowe korzyści, które należy wziąć pod uwagę przy ocenie maszyn do formowania metalu:
- Ulepszone wykończenie powierzchni: Niektóre techniki formowania metalu mogą wytwarzać części o doskonałym wykończeniu powierzchni, zmniejszając lub eliminując potrzebę dodatkowych procesów wykańczania.
- Ulepszone właściwości mechaniczne: Procesy formowania metali, takie jak stapianie w złożu proszkowym (PBF), mogą tworzyć części o unikalnych mikrostrukturach, prowadząc do poprawy właściwości mechanicznych, takich jak wytrzymałość i odporność na zmęczenie.
- Potencjał lekkości: Zdolność do wytwarzania złożonych kształtów za pomocą formowania metalu pozwala na projektowanie lekkich komponentów, co ma kluczowe znaczenie w sektorach takich jak lotnictwo i motoryzacja, gdzie redukcja masy jest głównym celem.
- Potencjał automatyzacji: Wiele maszyn do formowania metalu jest wysoce zautomatyzowanych, co zmniejsza zależność od pracy ręcznej oraz poprawia wydajność i spójność produkcji.
Ważne jest, aby pamiętać, że żadna pojedyncza technologia produkcji nie jest idealnie dopasowana do każdego zastosowania. Maszyny do formowania metalu mają również ograniczenia, które należy wziąć pod uwagę, a które omówimy w następnej sekcji.
Wady Maszyny do formowania metalu
Podczas gdy maszyny do formowania metalu oferują mnóstwo zalet, mają one również pewne ograniczenia, które należy wziąć pod uwagę:
- Wysoka inwestycja początkowa: Maszyny do formowania metalu, w szczególności zaawansowane technologie, takie jak PBF, mogą wiązać się ze znacznymi kosztami początkowymi. Może to stanowić barierę dla mniejszych firm lub tych z ograniczonym budżetem.
- Koszty narzędzi: W zależności od konkretnej techniki formowania metalu, koszty oprzyrządowania mogą być znaczne. Obejmuje to koszt matryc, form i innego specjalistycznego sprzętu potrzebnego do tego procesu.
- Minimalne ilości zamówienia: Niektóre techniki formowania metali, takie jak odlewanie ciśnieniowe, są najbardziej wydajne w przypadku produkcji wielkoseryjnej. Może to być wadą w przypadku projektów wymagających mniejszych ilości części.
- Złożoność procesu: Obsługa maszyn do formowania metalu, zwłaszcza nowszych technologii, takich jak PBF, może wymagać wysokiego poziomu wiedzy technicznej i kontroli procesu. Może to wymagać specjalistycznych szkoleń dla personelu.
- Istotne ograniczenia: Podczas gdy formowanie metalu oferuje wszechstronność materiału, mogą istnieć ograniczenia dotyczące rodzajów proszków, które można skutecznie przetwarzać za pomocą niektórych technik.
- Wymagania dotyczące przetwarzania końcowego: Podczas gdy niektóre techniki formowania metalu oferują części o kształcie zbliżonym do siatki, pewien poziom obróbki końcowej, taki jak obróbka cieplna lub obróbka skrawaniem, może być nadal konieczny w zależności od wymagań aplikacji.
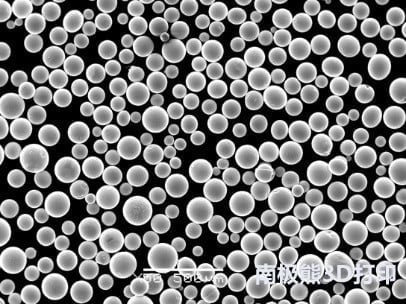
Często zadawane pytania (FAQ)
W tej sekcji zajmiemy się kilkoma często zadawanymi pytaniami (FAQ) dotyczącymi maszyn do formowania metalu:
P: Jaka jest różnica między odlewaniem metali a formowaniem metali?
O: Terminy "odlewanie metali" i "formowanie metali" są często używane zamiennie. Można jednak dokonać subtelnego rozróżnienia. Odlewanie metali zazwyczaj odnosi się do procesów wykorzystujących stopiony metal wlewany do wnęki formy. Formowanie metalu może obejmować szerszy zakres technik, w tym te, które wykorzystują proszki metali zamiast stopionego metalu.
P: Jakie są różne rodzaje maszyn do formowania metalu?
O: Istnieją różne rodzaje maszyn do formowania metalu, z których każda ma swoje mocne strony i zastosowania. Niektóre typowe przykłady obejmują:
- Maszyny do odlewania ciśnieniowego: Te woły robocze wtryskują stopiony metal pod wysokim ciśnieniem do formy wielokrotnego użytku (matrycy) w celu uzyskania skomplikowanych części o dużej objętości.
- Maszyny do odlewania metodą traconego wosku: W procesie tym tworzy się woskowy wzór, umieszcza go w ceramicznej formie, wypala wosk i wlewa stopiony metal w celu uzyskania odlewów o kształcie zbliżonym do siatki i wyjątkowej szczegółowości.
- Maszyny do odlewania piasku: Najbardziej tradycyjna metoda, odlew piaskowy, wykorzystuje rzeźbioną formę piaskową, zapewniając wszechstronność i przystępność cenową, ale z mniejszą dokładnością wymiarową.
- Maszyny do formowania wtryskowego metali (MIM): MIM łączy formowanie wtryskowe tworzyw sztucznych z metalurgią proszków w celu uzyskania złożonych części o kształcie zbliżonym do siatki, o dobrej dokładności wymiarowej i właściwościach materiału zbliżonych do kutych metali.
P: Jak wybrać odpowiednią maszynę do formowania metalu dla mojego projektu?
O: Wybór odpowiedniej maszyny do formowania metalu wymaga uwzględnienia kilku czynników:
- Częściowa złożoność: W przypadku skomplikowanych kształtów odpowiednie może być odlewanie ciśnieniowe lub MIM. Odlewanie piaskowe oferuje większą elastyczność w przypadku prostszych geometrii.
- Wielkość produkcji: Odlewanie ciśnieniowe wyróżnia się dużą objętością, podczas gdy odlewanie precyzyjne jest przeznaczone do mniejszych partii.
- Wymagania materiałowe: Należy wziąć pod uwagę pożądane właściwości i kompatybilność z różnymi proszkami metali.
- Ograniczenia kosztowe: Zrównoważenie kosztów początkowych (maszyna, oprzyrządowanie) z kosztami produkcji (na część) i potrzebami przetwarzania końcowego.
Konsultacja z ekspertem w dziedzinie formowania metali może dostarczyć cennych wskazówek przy wyborze optymalnej maszyny do konkretnych wymagań projektu.
P: Jakie są przyszłe trendy w maszynach do formowania metalu?
O: Przyszłość maszyn do formowania metalu rysuje się w jasnych barwach dzięki postępowi w kilku obszarach:
- Produkcja addytywna (AM): Techniki AM, takie jak Powder Bed Fusion (PBF), rewolucjonizują formowanie metali, umożliwiając tworzenie złożonych geometrii, wcześniej niemożliwych do uzyskania tradycyjnymi metodami.
- Zaawansowane materiały: Opracowanie nowych proszków metali o doskonałych właściwościach, takich jak wysoki stosunek wytrzymałości do masy i zwiększona odporność na korozję, rozszerzy możliwości formowania metali.
- Automatyzacja i integracja: Zwiększona automatyzacja i integracja robotów i innych technologii zwiększy wydajność, spójność i bezpieczeństwo procesów formowania metali.
Te postępy obiecują przesunąć granice tego, co jest możliwe dzięki formowaniu metalu, tworząc ekscytujące możliwości dla przyszłych innowacji.
Informacje o 3DP mETAL
Kategoria produktu
SKONTAKTUJ SIĘ Z NAMI
Masz jakiekolwiek pytania? Wyślij nam wiadomość już teraz! Po otrzymaniu wiadomości przetworzymy Twoje zapytanie z całym zespołem.