Imagine a world where crafting complex, high-performance aircraft parts wasn’t limited by traditional manufacturing methods. Enter metal powder, a revolutionary material that’s taking the aerospace industry by storm. These fine, metallic grains are transforming how we design, build, and propel our next generation of airplanes, rockets, and spacecraft. But how exactly are these tiny particles making such a giant leap forward? Let’s delve into the fascinating world of proszek metalowy dla przemysłu lotniczego applications.
Types of Metal Powder for Aerospace
Not all metal powders are created equal. In the aerospace industry, where every ounce counts, specific properties are paramount. Here are some of the key players:
- Titanium Alloys: These lightweight champions boast exceptional strength-to-weight ratios, making them ideal for airframes, engine components, and landing gear. Think of them as the weightlifters of the metal powder world, packing serious muscle without the bulk.
- Nickel-based Superalloys: For parts that endure scorching temperatures and intense pressure, look no further than nickel-based superalloys. Used in turbine blades and combustors, these alloys can withstand extreme heat while maintaining structural integrity. Imagine them as fireproof suits for your engine, shielding it from the inferno within.
- Stopy aluminium: Offering a fantastic balance of affordability and performance, aluminum alloys are a popular choice for non-critical structures and internal components. Think of them as the workhorses of the metal powder family, offering a reliable and cost-effective option for many applications.
Table 1: Key Properties of Common Metal Powders for Aerospace
Metalowy proszek | Kluczowe właściwości | Zalety | Słabe strony |
---|---|---|---|
Stopy tytanu | High Strength-to-weight ratio, Excellent corrosion resistance | Lekki, wytrzymały | Drogie |
Nickel-based Superalloys | High-temperature strength, Oxidation resistance | Withstands extreme heat | Limited availability, High cost |
Stopy aluminium | Affordable, Lightweight, Good formability | Cost-effective, Versatile | Lower strength compared to other options |
Beyond these heavy hitters, other specialty metal powders like cobalt-chromium alloys and refractory metals are finding their niche in aerospace applications. The choice of powder ultimately depends on the specific needs of the component being manufactured.
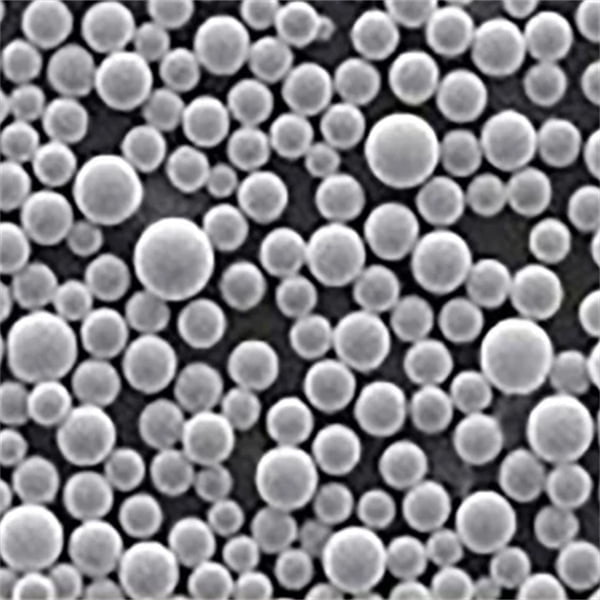
Preparation Methods of Metal Powder for Aerospace
Just like baking a delicious cake requires the right ingredients and techniques, crafting high-quality metal powder involves specific processes. Here are two of the most common methods used in aerospace:
- Atomizacja gazu: This method involves molten metal being broken up into a fine mist by a high-pressure gas stream. The resulting droplets rapidly solidify into spherical-shaped particles, ideal for consistent flow and packing during 3D printing. Imagine a high-tech sprinkler system creating a metallic rain of tiny, perfect spheres.
- Atomizacja wody: Similar to gas atomization, water atomization uses a high-velocity water jet to fragment molten metal. This method is typically used for less critical applications or when cost is a major factor. Think of it as a more industrial version of the gas atomization process, using the power of water instead of gas.
The chosen method significantly impacts the final properties of the metal powder. Gas atomization generally produces powders with higher purity, flowability, and spherical shape, making them ideal for demanding aerospace applications. Water atomization, on the other hand, can be a more cost-effective option for less critical parts.
The Application of Metal Powder for Aerospace
Metal powder isn’t just some futuristic concept; it’s revolutionizing the way we manufacture aerospace components. Here are some of the exciting applications driving this transformation:
- Produkcja addytywna (druk 3D): Metal powder takes center stage in this game-changing technology. 3D printers meticulously build complex parts layer by layer, using a laser or electron beam to melt and fuse the metal powder particles together. This allows for intricate designs that were previously impossible with traditional methods, leading to lighter, stronger, and more efficient aircraft structures. Think of it as a magic sculptor, meticulously building intricate parts from a bed of metallic sand.
- Near-Net-Shape Manufacturing: This process utilizes metal powder to create parts close to their final dimensions. The near-net-shape parts then undergo minimal machining, reducing waste and production time. Imagine it as baking a cake in a mold that’s almost exactly the final shape, minimizing the need for frosting and trimming.
- Formowanie wtryskowe metalu (MIM): Metal powder mixed with a binder is injected into a mold cavity to create complex shapes. The binder is then removed, leaving behind a green part that is sintered (heated) to achieve its final strength and properties. Think of it as a sophisticated version of sand casting, but with metal powder instead of sand and a much higher degree of precision. MIM allows for the creation of intricate parts with fine features, making it ideal for complex aerospace components like fuel injectors and turbine blades.
These are just a few examples of how metal powder is reshaping the aerospace landscape. As the technology matures and powder properties continue to improve, we can expect to see even more innovative applications emerge.
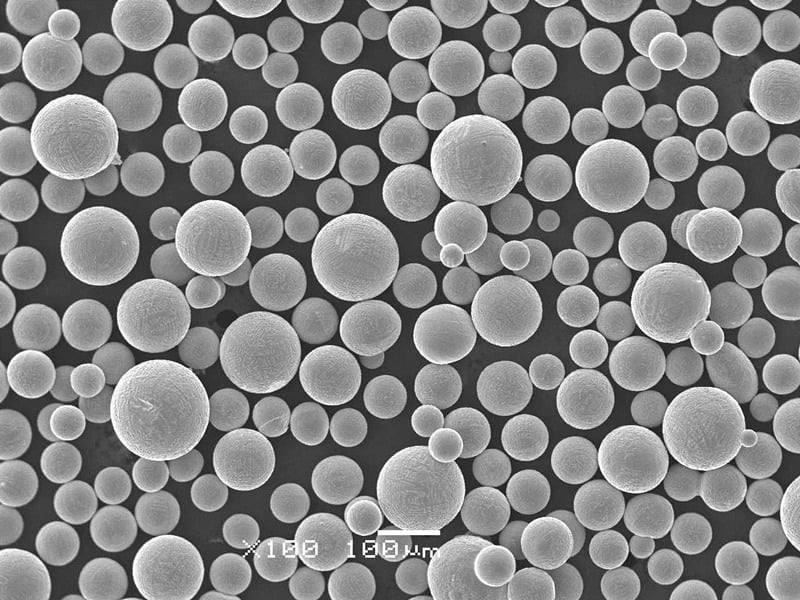
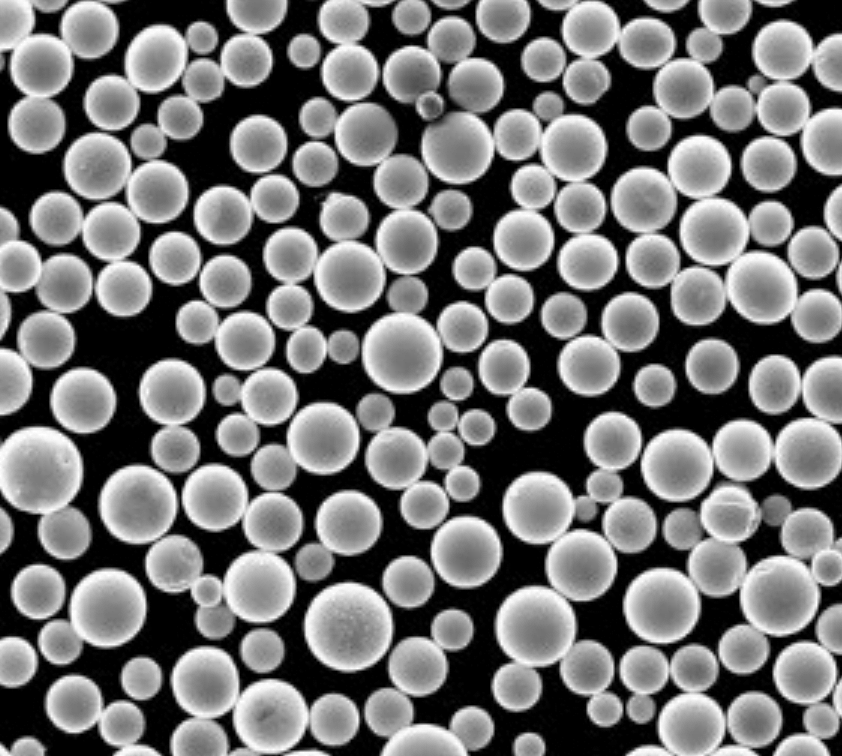
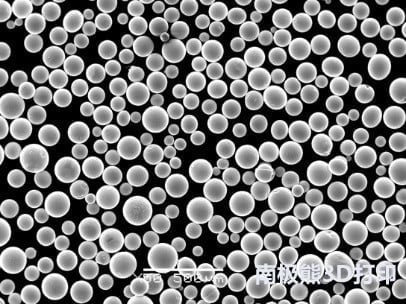
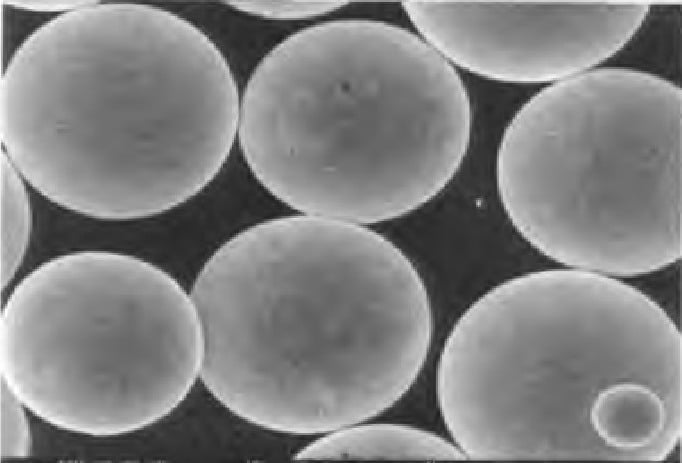
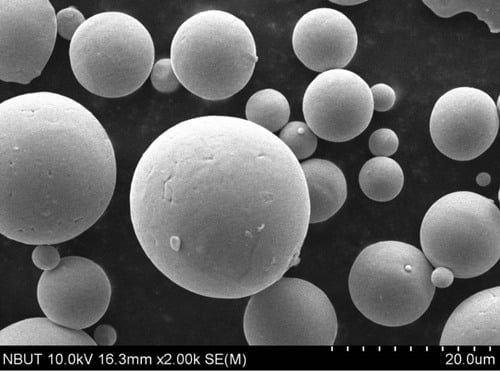
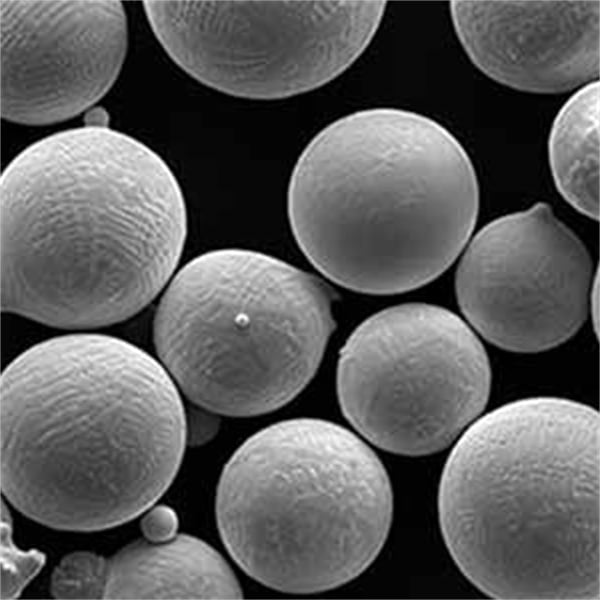
Advantages and Considerations of Using Metal Powder in Aerospace
While metal powder offers a treasure trove of benefits for aerospace manufacturing, it’s important to consider both the upsides and downsides:
Zalety:
- Lightweight Designs: Metal powders enable the creation of components with complex internal structures, leading to significant weight reduction compared to traditional manufacturing methods. This translates to improved fuel efficiency, increased payload capacity, and greater range for aircraft. Imagine an airplane built with lighter bones, allowing it to carry more weight or fly farther on the same amount of fuel.
- Swoboda projektowania: 3D printing with metal powder unlocks a world of design possibilities. Gone are the limitations of traditional machining; complex geometries, internal channels, and lattice structures become achievable. This design freedom allows engineers to optimize components for performance and weight, pushing the boundaries of what’s possible. Think of it as having a magic paintbrush that can create any 3D shape imaginable.
- Zmniejszona ilość odpadów: Unlike traditional methods that generate significant scrap material, metal powder additive manufacturing offers a more sustainable approach. Only the necessary material is used, minimizing waste and environmental impact. Imagine building an airplane with minimal leftover materials, like having a perfectly portioned meal with no food scraps.
- Faster Time-to-Market: Metal powder technologies can significantly reduce production lead times compared to traditional methods. Complex parts can be created directly from digital models, eliminating the need for lengthy tooling development. This allows for faster prototyping, iteration, and ultimately, quicker product development cycles. Imagine designing and building a new aircraft prototype in a fraction of the time it used to take.
Rozważania:
- Koszt: While the benefits are undeniable, metal powder additive manufacturing can still be a relatively expensive process compared to traditional methods. The cost of the metal powder itself, coupled with the specialized equipment required, can be significant hurdles for some applications. Think of it as a high-tech machine compared to a traditional hand tool; it offers more capability but comes with a higher price tag.
- Part Qualification: Aerospace components are subject to rigorous testing and certification standards. Metal powder parts need to meet these stringent requirements, which can involve additional development and qualification processes. Imagine building a bridge; you need to ensure it’s strong and safe before allowing cars to drive on it. Similarly, metal powder parts need to be thoroughly tested before being used in critical aerospace applications.
- Wykończenie powierzchni: Metal powder parts can sometimes have a rougher surface finish compared to traditionally machined parts. While this may not be an issue for all applications, it can be a factor for components requiring smooth, aerodynamic surfaces. Imagine the difference between a hand-knitted sweater and a smooth, store-bought one; metal powder parts can sometimes have a “hand-knitted” texture that may require additional finishing for certain applications.
Despite these considerations, the potential benefits of proszek metalowy dla przemysłu lotniczego are undeniable. As costs decrease, qualification processes become more streamlined, and surface finishing techniques improve, metal powder is poised to become an even more dominant force in the industry.
The Future of Metal Powder in Aerospace: A Universe of Possibilities
The future of metal powder in aerospace is as bright as the stars themselves. Here are some exciting possibilities on the horizon:
- Development of Novel Metal Powders: Researchers are constantly innovating, creating new metal powder alloys with even better properties. These advancements will push the boundaries of performance, enabling the creation of lighter, stronger, and more heat-resistant components. Imagine a new generation of metal powders that are like superheroes with enhanced strength, heat resistance, and other extraordinary properties.
- Druk wielomateriałowy: The ability to combine different metal powders within a single print could revolutionize component design. Imagine printing a turbine blade with a core structure made from a lightweight titanium alloy and an outer layer of a high-temperature nickel-based superalloy. This would create a component with exceptional strength-to-weight ratio and superior heat resistance.
- In-Space Manufacturing: The dream of building and repairing spacecraft in space might soon become a reality. Metal powder 3D printing could be used to create replacement parts or even entire structures on-demand, eliminating the need for expensive and time-consuming launches from Earth. Imagine astronauts using a 3D printer to create a critical antenna component for a malfunctioning satellite, all within the confines of the spacecraft. Metal powder could become the ultimate tool for self-sufficiency in space exploration.
These are just a glimpse of the exciting possibilities that metal powder holds for the future of aerospace. As research and development continue, we can expect to see even more groundbreaking applications emerge, taking us further and faster than ever before.
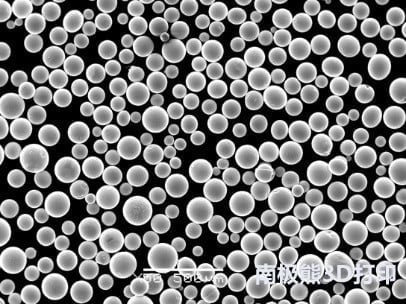
FAQ
Q: What are the benefits of using proszek metalowy dla przemysłu lotniczego applications?
A: Metal powder offers a multitude of benefits, including:
- Lightweight designs: Leading to improved fuel efficiency, increased payload capacity, and greater range for aircraft.
- Swoboda projektowania: Enabling the creation of complex geometries and internal structures that were previously impossible with traditional methods.
- Zmniejszona ilość odpadów: Minimizing waste and environmental impact compared to traditional manufacturing techniques.
- Faster time-to-market: Significantly reducing production lead times by eliminating the need for lengthy tooling development.
Q: What are some of the considerations for using metal powder in aerospace?
A: While promising, there are some factors to consider:
- Koszt: Metal powder additive manufacturing can be expensive compared to traditional methods due to the cost of the powder and specialized equipment.
- Part qualification: Metal powder parts need to meet rigorous testing and certification standards, which can involve additional development and qualification processes.
- Wykończenie powierzchni: Metal powder parts can sometimes have a rougher surface finish compared to traditionally machined parts, which may require additional finishing for certain applications.
Q: What are the different types of metal powder used in aerospace?
A: Some of the most common metal powders used in aerospace include:
- Stopy tytanu: Offering exceptional strength-to-weight ratio, ideal for airframes, engine components, and landing gear.
- Nadstopy na bazie niklu: Withstanding extreme heat and pressure, used in turbine blades and combustors.
- Aluminum alloys: Providing a balance of affordability and performance for non-critical structures and internal components.
Q: How is metal powder prepared for aerospace applications?
A: Two common methods are used:
- Atomizacja gazu: Molten metal is broken up into a fine mist by a high-pressure gas stream, resulting in spherical-shaped particles ideal for 3D printing.
- Water atomization: A high-velocity water jet fragments molten metal, typically used for less critical applications or when cost is a major factor.
Q: What are some of the future applications of metal powder in aerospace?
A: The future is bright, with possibilities like:
- Development of novel metal powders: With even better properties for lighter, stronger, and more heat-resistant components.
- Drukowanie na wielu materiałach: Combining different metal powders within a single print for components with exceptional properties.
- In-space manufacturing: Using metal powder 3D printing to create replacement parts or entire structures on-demand during space missions.
Metal powder is revolutionizing the aerospace industry, and its potential for the future seems limitless. As we continue to explore the possibilities of this transformative material, the sky truly is no longer the limit.
Informacje o 3DP mETAL
Kategoria produktu
SKONTAKTUJ SIĘ Z NAMI
Masz jakiekolwiek pytania? Wyślij nam wiadomość już teraz! Po otrzymaniu wiadomości przetworzymy Twoje zapytanie z całym zespołem.