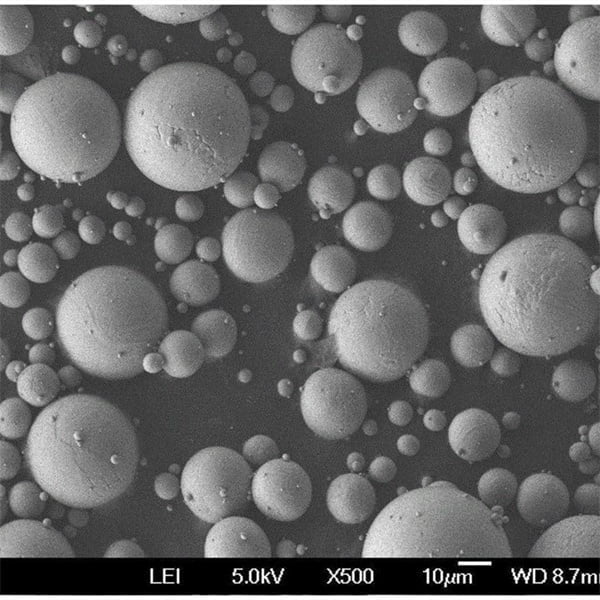
CoCrFeNi Powder
Overview of CoCrFeNi Powder CoCrFeNi powder, also known as CoCrFeNiMn powder or high entropy alloy (HEA) powder, refers to a material composed of cobalt, chromium, iron, and nickel elements in near-equiatomic ratios. This novel alloy powder displays exceptional properties compared to conventional alloys and has garnered significant interest for various applications. Some key features of…
Small MOQ
Flexible sourcing for hundreds of products
Customization support
Customized powder according to industry
Rapid shipment
By DHL Express, safe and fast direct to your hands
Overview of CoCrFeNi Powder
CoCrFeNi powder, also known as CoCrFeNiMn powder or high entropy alloy (HEA) powder, refers to a material composed of cobalt, chromium, iron, and nickel elements in near-equiatomic ratios. This novel alloy powder displays exceptional properties compared to conventional alloys and has garnered significant interest for various applications.
Some key features of CoCrFeNi powder include:
- High configurational entropy leading to outstanding strength, hardness, thermal stability, and corrosion resistance
- Single solid-solution FCC phase microstructure
- Excellent strength-ductility combination
- High fracture toughness
- Good machinability and formability
- Resistance to softening at elevated temperatures
- Customizable with minor additions of elements like manganese
The unique disorder in the atomic arrangement of CoCrFeNi imparts superior mechanical performance. The near-equal concentrations of the main elements hinder dislocation movement, improving hardness. The multiphase structure provides solid solution strengthening through lattice strain effects.
Composition of CoCrFeNi Powder
The composition of CoCrFeNi HEA powder can be tailored but generally consists of:
Element | Typical Composition Range |
---|---|
Cobalt (Co) | 20-35 at.% |
Chromium (Cr) | 20-35 at.% |
Iron (Fe) | 20-35 at.% |
Nickel (Ni) | 20-35 at.% |
The equiatomic ratio provides maximum configurational entropy but minor deviations do not significantly affect properties. Additions of 1-2 at.% of manganese are common to further improve properties through grain refinement and precipitation strengthening.
Properties of CoCrFeNi Powder
CoCrFeNi alloy powder exhibits a unique combination of outstanding properties:
Property | Values |
---|---|
Density | 7.5-8.3 g/cm3 |
Melting Point | >1200¡«C |
Microhardness | 2.5-4 GPa |
Ultimate Tensile Strength | 500-1300 MPa |
Yield Strength | 200-1100 MPa |
Elongation | 10-60% |
Young’s Modulus | 150-250 GPa |
Shear Modulus | 65-85 GPa |
Poisson’s Ratio | 0.21-0.33 |
Fracture Toughness | >100 MPa©|m |
Thermal Conductivity | 10-30 W/mK |
Electrical Resistivity | 70-100 n´Îm |
Corrosion Resistance | Excellent in various environments |
The high hardness arises from solid solution strengthening while the FCC structure imparts good ductility. The properties can be tailored through composition adjustments and processing.
Characteristics of CoCrFeNi Powder
Some salient characteristics of CoCrFeNi alloy powder include:
- Single phase FCC structure lacking intermetallic phases
- Annealing twins and stacking faults present
- Equiaxed powder morphology with good flowability
- Powder size distribution ranging from 15-150 Ã×m
- High purity with low oxygen content
- Spherical powder shape and smooth surface
- Customizable powder size, shape, and composition
The powder exhibits high chemical homogeneity with a uniform distribution of alloying elements. The spherical morphology provides good packing and flow characteristics.
Applications of CoCrFeNi Powder
The exceptional combination of strength, toughness, and processability of CoCrFeNi powder makes it suitable for:
Additive Manufacturing: Excellent printability due to good flow and melting characteristics. Used for aerospace, tooling, and biomedical implants.
Thermal Spray Coatings: Resistance to wear, corrosion, and thermal softening. Coatings for mechanical, marine, and chemical applications.
Alloy Development: Base material for new high entropy alloys with additions of Al, Ti, etc.
Metal Injection Molding: High stiffness parts with good dimensional stability for aviation and automotive.
Powder Metallurgy: High performance P/M parts with balanced strength and ductility.
Cryogenic Applications: Retention of ductility and toughness at subzero temperatures.
Specifications of CoCrFeNi Powder
CoCrFeNi alloy powder is available in various size ranges, compositions, and forms:
Parameter | Variants |
---|---|
Size range | 15-25 Ã×m, 25-45 Ã×m, 45-75 Ã×m, 75-105 Ã×m, 105-150 Ã×m |
Composition | Equiatomic, custom elemental ratios |
Powder shape | Spherical, irregular |
Production method | Gas/water atomization, mechanical alloying |
Supply form | Loose powder, sintered preforms |
Larger powder sizes of 45-150 Ã×m are preferred for thermal spray and metal injection molding. Finer 15-45 Ã×m sizes are used for additive manufacturing. Powders can be customized in shape, size, oxygen content, and flowability.
Suppliers of CoCrFeNi Powder
Some leading global suppliers of CoCrFeNi high entropy alloy powder include:
Company | Production Capacity | Location |
---|---|---|
Sandvik | 200 tons per year | Sweden |
Praxair | 150 tons per year | USA |
Hoganas | 100 tons per year | Sweden |
CNPC Powder | 50 tons per year | China |
Carpenter Technologies | 40 tons per year | USA |
The powders are generally produced via gas or water atomization methods. Custom powder compositions and sizes can be sourced from these suppliers.
Pricing
Powder Size | Price Range |
---|---|
15-45 micron | $150-200 per kg |
45-105 micron | $100-150 per kg |
105-150+ micron | $80-120 per kg |
Larger powder sizes are cheaper due to higher production rates in atomization. Custom alloys and compositions are priced higher. The powder prices have been declining due to increasing market competition and capacities.
Pros and Cons of CoCrFeNi Powder
Advantages | Limitations |
---|---|
Outstanding strength and hardness | High material costs due to Co and Ni |
Excellent ductility and toughness | Limited data on long-term performance |
Good fabricability by AM, MIM, PM | Processing challenges with microstructural control |
Thermal and microstructural stability | Composition must be precisely controlled |
High corrosion and wear resistance | Lower processability than conventional alloys |
Retains strength at elevated temperatures | Often requires HIP post-processing |
CoCrFeNi HEA powder enables components with unmatched property combinations. However, the material and processing costs are high. Microstructure and properties depend heavily on precise composition control.
Comparison with Alternatives
Vs. Stainless Steel Powders
- Higher strength and hardness
- Superior wear and corrosion resistance
- More expensive base material cost
- Lower processability and weldability
Vs. Tool Steel Powders
- Better ductility and fracture toughness
- Lower high-temperature strength
- Less established processing methods
- Limited size and alloy variant availability
Vs. Inconel Superalloy Powders
- Comparable high-temperature strength
- Lower cost material
- Shorter track record of performance
- Restricted microstructural stability at very high temperatures
FAQs
Q: What is high entropy alloy (HEA) powder?
A: HEA powder contains multiple principal elements in near-equiatomic ratios to produce exceptional properties of strength, ductility, and stability. CoCrFeNi powder is a leading HEA.
Q: What are the typical sizes of CoCrFeNi powder available?
A: Common size ranges are 15-45 Ã×m for AM, 45-105 Ã×m for thermal spraying, and 105-150 Ã×m for MIM and other applications. Finer and coarser sizes can be customized.
Q: What affects the price of CoCrFeNi alloy powder?
A: Powder size, composition, purity, production method, and order quantity determine pricing. Larger sizes over 100 Ã×m cost less. Minor additions or tighter composition ranges increase cost.
Q: How is CoCrFeNi HEA powder produced?
A: Gas atomization and water atomization are the main production methods. The powder can also be made by mechanical alloying or cryomilling of prealloyed ingots.
Q: What are some example applications of CoCrFeNi powder?
A: Leading uses are additive manufacturing of tooling and aerospace components, thermal spray coatings for wear/corrosion resistance, alloy development, metal injection molding of automotive parts, and powder metallurgy of high-performance components.
Q: What are the key properties of CoCrFeNi HEA powder?
A: It exhibits an exceptional combination of high strength, hardness, ductility, fracture toughness, thermal stability, and corrosion resistance compared to conventional alloys.
Q: What are the limitations of CoCrFeNi powder?
A: High base material cost, processing challenges in controlling microstructure, limited long-term performance data, reduced weldability compared to steels are some disadvantages.
Q: How does CoCrFeNi powder compare with tool steels and stainless steels?
A: It has vastly higher strength and hardness but lower processability than stainless steels. Compared to tool steels, it provides superior fracture toughness and ductility.
Q: Is CoCrFeNi suitable for cryogenic applications?
A: Yes, it retains good ductility and toughness at sub-zero temperatures while conventional alloys become brittle. This makes it useful for cryogenic equipment.
Q: Can the composition of CoCrFeNi powder be customized?
A: Yes, suppliers can provide custom elemental ratios beyond the equiatomic composition. Common adjustments are 1-2 at.% Mn or Co additions to tailor the properties.
Contact us now
Please contact us for recent product quotes and stock availability.