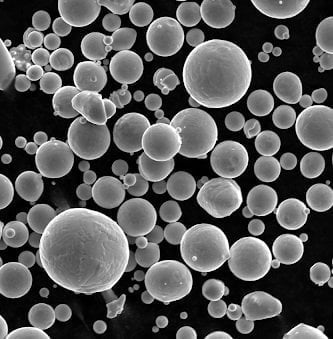
GH3536 Alloy Powder
GH3536 alloy powder was designed specifically for additive manufacturing, using composition optimization and powder atomization techniques to achieve superior properties compared to conventional nickel superalloys. The key features of GH3536 alloy powder include: High strength at temperatures up to 760¡«C (1400¡«F) Oxidation and corrosion resistance in harsh environments Excellent thermal fatigue life and crack growth…
Small MOQ
Flexible sourcing for hundreds of products
Customization support
Customized powder according to industry
Rapid shipment
By DHL Express, safe and fast direct to your hands
GH3536 alloy powder was designed specifically for additive manufacturing, using composition optimization and powder atomization techniques to achieve superior properties compared to conventional nickel superalloys. The key features of GH3536 alloy powder include:
- High strength at temperatures up to 760¡«C (1400¡«F)
- Oxidation and corrosion resistance in harsh environments
- Excellent thermal fatigue life and crack growth resistance
- Good printability and low porosity in printed parts
- Can be age hardened to optimize strength and ductility
The combination of properties make GH3536 suitable for aerospace, power generation, oil & gas, and chemical processing components exposed to extreme temperatures and stresses. Both new part fabrication and repair of worn components can benefit from using this advanced powder.
GH3536 Alloy Powder Composition
GH3536 has a complex composition designed to provide an optimal balance of properties. The nominal composition is shown below:
Element | Weight % |
---|---|
Nickel (Ni) | Balance |
Chromium (Cr) | 13.5 – 16.0 |
Cobalt (Co) | 12.0 – 15.0 |
Tungsten (W) | 5.0 – 7.0 |
Tantalum (Ta) | 3.0 – 5.0 |
Aluminum (Al) | 2.8 – 3.8 |
Titanium (Ti) | 0.5 – 1.5 |
Niobium (Nb) | 0.5 – 1.5 |
Hafnium (Hf) | 0.2 – 0.8 |
Carbon (C) | 0.05 – 0.15 |
Boron (B) | 0.01 – 0.03 |
Zirconium (Zr) | 0.01 – 0.05 |
Nickel forms the matrix, while elements like chromium, cobalt, and aluminum improve oxidation resistance. Refractory elements tantalum, tungsten, niobium, and hafnium contribute to strength at elevated temperatures. Titanium and niobium strengthen the alloy through carbide formation. Trace amounts of carbon, boron, and zirconium enhance precipitation hardening.
The powder composition is designed to limit segregation and maintain composition uniformity during printing, ensuring consistent properties in the final part. The spherical powder morphology also improves flowability and packing density for good printability.
GH3536 Alloy Powder Properties
GH3536 exhibits an excellent combination of strength, ductility, and environmental resistance owing to its tailored composition and optimized production process. The key properties are summarized below:
Mechanical Properties
Property | As-printed | Aged |
---|---|---|
Tensile Strength | 1050 – 1250 MPa (152 – 181 ksi) | 1275 – 1400 MPa (185 – 203 ksi) |
Yield Strength (0.2% offset) | 900 – 1100 MPa (131 – 160 ksi) | 1150 – 1300 MPa (167 – 189 ksi) |
Elongation | 25 – 35% | 16 – 22% |
Hardness | 32 – 38 HRC | 36 – 43 HRC |
Physical Properties
Property | Typical Value |
---|---|
Density | 8.3 g/cm3 |
Melting Point | 1310¡«C (2390¡«F) |
Thermal Properties
Property | Temperature |
---|---|
Coefficient of Thermal Expansion | 12.8 x 10-6/¡«C at 20-100¡«C |
Thermal Conductivity | 11.4 W/m-K at 20¡«C |
Specific Heat | 0.43 J/g-¡«C at 20¡«C |
Oxidation Resistance
- Resists oxidation in air up to ~980¡«C. Protective Cr2O3 oxide scale forms.
- Better oxidation resistance than Inconel 718 and many other Ni alloys.
Corrosion Resistance
- Excellent resistance to hot corrosion and sulfidation.
- Resists many organic acids, chlorides, caustics.
Other Properties
- Retains strength and ductility after prolonged exposures up to 760¡«C.
- Excellent thermal fatigue life. Resists crack growth.
- Low coefficient of friction and galling resistance.
The strength of GH3536 in the aged condition exceeds that of conventional nickel superalloys like Inconel 718 while maintaining robust ductility. The alloy is stronger than many stainless steels at high temperatures. Oxidation resistance approaches that of nickel-chromium alloys like Inconel 601. Overall, GH3536 provides an exceptional balance of properties for critical applications.
Applications of GH3536 Alloy Powder
The combination of strength, environmental resistance, printability, and ease of post-processing makes GH3536 suitable for:
Aerospace Components
- Turbine blades, vanes, combustors
- Structural parts, landing gear
- Rocket engine nozzles, thrusters
- Hypersonic vehicle hot structures
Power Generation
- Gas turbine hot section parts
- Heat exchangers, recuperators
- Heat shields, thermowells
Oil & Gas
- Downhole tools, wellhead parts
- Valves, pumps for corrosive services
Automotive
- Turbocharger wheels and housings
- Exhaust components
Chemical Processing
- Valves, pumps, reaction vessels
- Heat exchanger tubing
Tooling
- Injection molds with conformal cooling
- Die casting dies, hot stamping tools
Others
- Heating elements
- Radioactive waste containers
- Specialty fasteners and springs
GH3536 can replace existing parts made of lower performance materials to improve durability and efficiency. The powder is also ideal for fabricating new designs not possible with conventional manufacturing. Both new part production and repair/refurbishment of worn components are enabled.
Printing GH3536 Alloy Powder
GH3536 powder can be successfully printed using laser powder bed fusion (L-PBF) and electron beam powder bed fusion (E-PBF) processes. The spherical powder morphology provides good flow and packing. Key considerations include:
Printing Process
- Laser and electron beam powder bed technologies applicable.
- Process parameters require development for new machines.
- Inert gas chamber atmosphere (argon or nitrogen).
Powder specification
- Particle size range 10-45 Ã×m, D50 ~25 Ã×m typical.
- Apparent density 2.5-3.5 g/cm3.
- Flow rate 25-35 s (Hall flowmeter).
Printing Recommendations
- Preheating baseplate to ~150¡«C reduces thermal stresses.
- Scan speeds from 400-1000 mm/s are typical.
- Hatch spacing 0.08-0.12 mm for good densification.
- 100% fresh powder for reuse.
Post Processing
- Stress relieving: 1080¡«C/2hr, air cool.
- Aging: 760¡«C/8-16 hr, air cool.
- Hot isostatic pressing can further reduce porosity.
With parameter optimization, densities over 99.8% are possible. The microstructure consists of fine, uniform grains suitable for critical applications.
Specifications of GH3536 Powder
GH3536 alloy powder is commercially available in the standard size distribution and classes summarized below. Custom variations can also be produced.
Powder Size Distribution | |
---|---|
D10 | 10 Ã×m |
D50 | 25 Ã×m |
D90 | 45 Ã×m |
Powder Classes | Nominal Flow Rate | Apparent Density |
---|---|---|
Class I | 25 s | 2.5 g/cm3 |
Class II | 28 s | 2.8 g/cm3 |
Class III | 32 s | 3.2 g/cm3 |
Other specifications:
- Spherical morphology with satellite fraction under 1%.
- Oxygen content under 100 ppm.
- No binders or lubricants added.
Each powder lot is provided with a Certificate of Analysis detailing composition, particle characteristics, flow rate, and other parameters.
Handling and Storage of GH3536
To maintain powder quality during handling and storage:
- Store sealed powder containers in a cool, dry environment. Desiccant is recommended.
- Avoid exposing powder to moisture which can cause clumping and flow issues.
- Limit temperature excursions during transport and storage.
- Open containers only in an inert atmosphere glove box or argon chamber.
- Immediately process open containers to limit oxidation. Do not reuse exposed powder.
- Use appropriate PPE and avoid inhalation or contact with skin and eyes.
With proper handling, GH3536 powder has a shelf life exceeding one year from manufacture date. FIFO inventory management is recommended.
Safety Data for GH3536
As an alloy powder containing nickel and other elements, standard safety precautions should be taken during handling:
- Use PPE: Powder suitable respirator, gloves, eye protection, protective clothing.
- Avoid skin contact or inhalation of dusts during handling.
- Properly ground all powder handling equipment. Inert gas glove boxes recommended.
- Use dust collection during cleanup. Avoid generating airborne dust.
- Dispose of excess powder and cleanup debris appropriately.
- Refer to SDS document for additional safety information.
Nickel powder is classified as a suspected carcinogen. Follow all laws and regulations for safe metal powder handling.
Inspection of GH3536 Powder
To ensureGH3536 powder meets application requirements, the following inspection procedures can be used:
Particle Size Distribution
- Laser diffraction analysis (ISO 13320)
- Sieve analysis (ASTM B214)
Morphology & Microstructure
- Scanning electron microscopy
- Optical microscopy of mounted and polished specimens
Powder Composition
- Inductively coupled plasma mass spectrometry (ASTM E1097)
- Inert gas fusion for O and N (ASTM E1019)
Powder Density
- Apparent density (Hall flowmeter)
- Tap density (ASTM B527)
Powder Flowability
- Hall flowmeter (ASTM B213)
- Revolution powder analyzer
Lot Acceptance
- Sampling per ASTM B215
- Verify powder meets size, composition, morphology specifications
Testing should be conducted for each powder lot to verify conformance to applicable ASTM standards. This ensures consistent, high quality powder feedstock for printing.
FAQs
Q: What makes GH3536 better than other Ni superalloys for AM?
A: GH3536 has higher strength than workhorse alloys like Inconel 718 while maintaining ductility. The powder composition and atomization process minimize segregation and porosity.
Q: Does GH3536 require hot isostatic pressing (HIP) after printing?
A: HIP can further reduce internal porosity but is not required to achieve high densities (>99.5%) with optimized AM parameters. HIP may allow higher service temperatures.
Q: What post processing is required after printing GH3536?
A: A simple stress relief heat treatment can be used after printing. For optimal strength, an aging heat treatment is recommended.
Q: What are the lead times for purchasing GH3536 powder?
A: Small lots can ship in 2-4 weeks. Allow 3-5 months for large production volumes depending on availability.
Q: Does GH3536 contain aluminum or titanium to cause issues during printing?
A: The Al and Ti concentrations are balanced to avoid powder oxidation or excessive reaction with the melt pool during printing.
Q: What particle size distribution is recommended for printing GH3536?
A: A distribution with D10 of 10 Ã×m, D50 of 25 Ã×m, and D90 of 45 Ã×m provides a good balance of flowability and printing.
Q: Can GH3536 be used for printing parts with overhangs and complex geometries?
A: Yes, GH3536 has demonstrated excellent printability for parts with overhangs exceeding 45¡« overhang angle.
Conclusion
GH3536 nickel superalloy powder offers an exceptional combination of high strength, temperature capability, oxidation resistance, printability, and post-processing response for demanding additive manufacturing applications in aerospace, power generation, oil & gas, automotive, and chemical processing industries. The tailored composition, optimized powder characteristics, and potential for heat treatment allow tunable properties for new designs not possible with conventional manufacturing. With proper handling and printing procedures, GH3536 enables complex, high performance metal parts combining low weight and durability like never before.
Contact us now
Please contact us for recent product quotes and stock availability.