Imagine a world where lighter airplanes soar through the sky, medical implants seamlessly integrate with the human body, and energy-efficient buildings rise from the ground. This future is closer than you think, and it’s being built with a revolutionary material: advanced material powders.
What are Advanced Material Powders?
Advanced material powders are finely-ground particles of engineered materials boasting exceptional properties. Unlike their bulk counterparts, these microscopic marvels offer a unique set of advantages, making them ideal for cutting-edge applications in various industries.
Chemical Composition of Advanced Material Powders
The composition of advanced material powders varies greatly depending on their intended use. Here’s a glimpse into the diverse world of these tiny powerhouses:
Material Type | Common Chemical Composition | ตัวอย่าง |
---|---|---|
Metals | Elements like iron, titanium, aluminum, and alloys like nickel-chromium | Stainless steel powders, Inconel powders, Titanium aluminide (TiAl) powders |
Ceramics | Ceramic oxides like alumina (Al2O3), zirconia (ZrO2), and silicon nitride (Si3N4) | Alumina powders, Zirconia powders, Silicon nitride powders |
Polymers | Polymers like polyamide (PA), polyamide 12 (PA12), and thermoplastic polyurethane (TPU) | Nylon powders, PA12 powders, TPU powders |
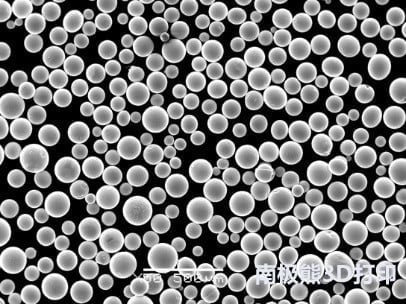
The Advantages of Advanced Material Powders
So, what makes these advanced material powders so special? Let’s delve into some of their key benefits:
- Unmatched Design Freedom: Unlike traditional manufacturing techniques, advanced material powders enable the creation of complex geometries with intricate details. Think lightweight components with internal lattices for enhanced strength-to-weight ratios or medical implants that mimic natural bone structures.
- Superior Material Properties: The unique processing methods used to create advanced material powders often result in enhanced properties compared to bulk materials. For instance, metal powders can achieve higher strength and improved flow characteristics, while ceramic powders can boast superior wear resistance and thermal stability.
- Reduced Waste: Traditional manufacturing processes often generate significant scrap material. Advanced material powder-based techniques, like additive manufacturing, minimize waste by using only the necessary material for a specific part. This translates to a more environmentally friendly and cost-effective production process.
- Mass Customization: Advanced material powders pave the way for mass customization. Imagine being able to tailor material properties to meet the specific needs of an application. This level of control allows engineers to push the boundaries of design and performance.
Exploring Specific Metal Powder Models
Let’s delve deeper into the world of metal powders and explore ten specific models, each with its unique properties and applications:
- Stainless Steel 316L Powders: This workhorse material offers excellent corrosion resistance, making it ideal for applications in the medical, marine, and chemical processing industries.
- Inconel 625 Powders: Known for its high-temperature strength and resistance to harsh environments, Inconel 625 powders are perfect for aerospace, gas turbine engines, and heat exchangers.
- Titanium Aluminide (TiAl) Powders: This lightweight and high-temperature material is a game-changer in the aerospace industry. TiAl powders offer exceptional strength-to-weight ratios, making them ideal for jet engine components.
- Aluminum 6061 Powders: A versatile and cost-effective option, aluminum 6061 powders are widely used in automotive parts, electronics enclosures, and consumer goods due to their good machinability and strength.
- Nickel Chromium Powders: Offering excellent wear resistance and high-temperature performance, nickel-chromium powders are used in applications like molds, dies, and wear pads.
- Copper Powders: Known for their high electrical conductivity and thermal conductivity, copper powders are used in electrical components, heat sinks, and electromagnetic devices.
- Tungsten Powders: Incredibly dense and boasting a high melting point, tungsten powders are used in armor-piercing projectiles, welding electrodes, and ballast weights.
- Cobalt Chrome Powders: A biocompatible material that integrates well with the human body, cobalt chrome powders are used in medical implants like hip replacements and knee replacements.
- Hastelloy C-276 Powders: This superalloy offers exceptional resistance to a wide range of corrosive environments, making it ideal for chemical processing equipment and pollution control systems. 1 Maraging Steel Powders: Combining high strength with good ductility, maraging steel powders are used in applications demanding both toughness and lightweight construction, such as aerospace components and sporting goods.
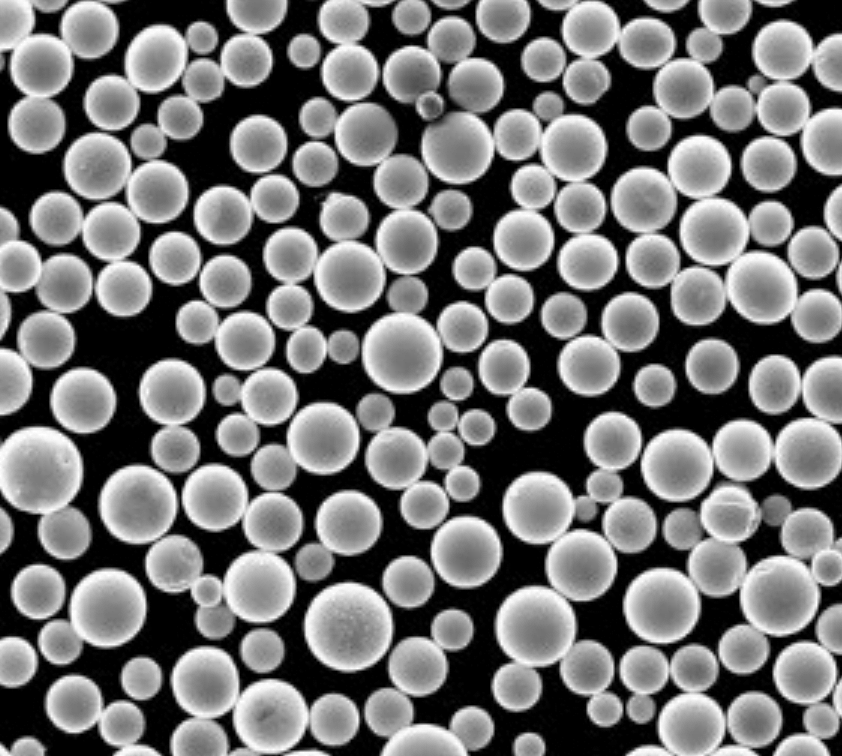
Applications of Advanced Material Powders
อุตสาหกรรม | แอปพลิเคชัน | Specific Powder Types |
---|---|---|
อวกาศ | Jet engine components, airframes, spacecraft parts | Titanium Aluminide (TiAl) powders, Inconel powders, Aluminum powders |
ยานยนต์ | Lightweight car parts, engine components, heat sinks | Aluminum powders, Nickel Chromium powders, Copper powders |
แพทย์ | Implants (hips, knees, dental), prosthetic limbs, surgical instruments | Cobalt Chrome powders, Stainless steel 316L powders, Titanium powders |
เครื่องใช้ไฟฟ้า | Electrical components, heat sinks, connectors | Copper powders, Silver powders, Tungsten powders |
พลังงาน | Fuel cells, turbines, heat exchangers | Inconel powders, Nickel Chromium powders, Stainless steel powders |
สินค้าอุปโภคบริโภค | Sporting goods, eyewear frames, prosthetics | Aluminum powders, Nylon powders, TPU powders |
การก่อสร้าง | Customizable building components, lightweight structures, energy-efficient facades | Stainless steel powders, Aluminum powders, Titanium powders |
Properties and Characteristics of Advanced Material Powders
Beyond their chemical composition, several key properties and characteristics define advanced material powders:
- Particle Size and Distribution: The size and distribution of powder particles significantly impact their flowability, packing density, and final product properties. Powders with a narrow size distribution typically offer better packing and improved mechanical properties in the final product.
- Surface Morphology: The shape and texture of the powder particles influence their behavior during processing and the final product’s microstructure. Spherical powders generally flow better and can lead to denser final parts compared to irregularly shaped particles.
- ความบริสุทธิ์: The presence of impurities in advanced material powders can negatively impact their performance. Manufacturers strive for high purity levels to ensure consistent and reliable material properties.
- การไหล: The ease with which a powder flows is crucial for several processes, including additive manufacturing. Powders with good flowability enable smooth and consistent material deposition, leading to high-quality final products.
Specifications, Sizes, Grades, and Standards
Advanced material powders are available in a wide range of specifications, sizes, grades, and adhere to various industry standards. Here’s a breakdown to help you navigate this diverse landscape:
ทรัพย์สิน | คำอธิบาย | Example |
---|---|---|
ขนาดอนุภาค | Measured in microns (µm) | Stainless steel 316L powders: 15-45 µm |
เกรด | Defines the purity level and other key characteristics | Inconel 625 powders: Grade AM (for Additive Manufacturing) |
มาตรฐาน | Ensures consistent quality and adherence to specific requirements | Aluminum 6061 powders: ASTM B289 standard |
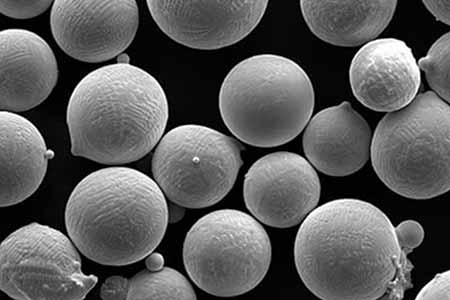
ซัพพลายเออร์และราคา
Several companies worldwide specialize in the production and distribution of advanced material powders. Here’s a table with some prominent suppliers, but keep in mind this is not an exhaustive list:
ซัพพลายเออร์ | Website | Material Focus |
---|---|---|
AP Powder Company | https://www.allpowderpaints.com/ | Metal powders for various applications |
Höganäs | https://www.hoganas.com/en/ | Metal powders for additive manufacturing and other processes |
Inframat Advanced Materials | http://www.advancedmaterials.us/ | Metal, ceramic, and polymer powders |
Carpenter Additive Manufacturing | https://www.carpenteradditive.com/ | Metal powders for aerospace, medical, and other industries |
BASF 3D Printing Solutions | https://forward-am.com/ | Polyamide powders for various additive manufacturing applications |
Pricing for advanced material powders can vary significantly depending on the material type, particle size, grade, and order quantity. Generally, metal powders tend to be more expensive than polymer powders.
Pros and Cons of Advanced Material Powders
Like any technology, advanced material powders come with their own set of advantages and limitations:
ข้อดี
- Unmatched design freedom
- Superior material properties
- Reduced waste
- Mass customization
ข้อเสีย
- Higher upfront costs compared to traditional manufacturing techniques for some materials.
- Powder handling can be complex and may require specialized equipment and expertise.
- Limited availability of certain advanced material powders, especially those with unique properties.
Addressing these limitations is an ongoing area of research and development. As the technology matures and production volumes increase, the cost of advanced material powders is expected to come down. Additionally, advancements in powder handling techniques and equipment are simplifying the use of these materials for a wider range of manufacturers.
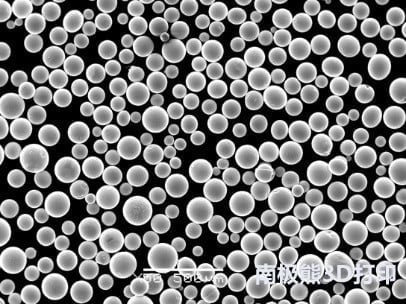
คำถามพบบ่อย
Here are some frequently asked questions regarding advanced material powders, answered in a table format for easy reference:
Question | Answer |
---|---|
What are the different types of advanced material powders? | Advanced material powders encompass a wide range of materials, including metals, ceramics, polymers, and composites. Each type offers unique properties and benefits for specific applications. |
How are advanced material powders produced? | There are various techniques for producing advanced material powders, including atomization, grinding, and chemical synthesis. The chosen method depends on the desired material properties and particle size distribution. |
What are the advantages of using advanced material powders in additive manufacturing? | Advanced material powders offer exceptional design freedom, enabling the creation of complex geometries and intricate lattice structures. Additionally, they can achieve superior material properties compared to traditional manufacturing techniques. |
Are advanced material powders safe to handle? | Some advanced material powders, particularly those containing metals or certain chemicals, may require specific handling precautions. It’s crucial to consult the safety data sheet (SDS) for the specific powder material and follow recommended handling procedures. |
What is the future of advanced material powders? | The future of advanced material powders is incredibly bright. As technology continues to evolve, we can expect to see the development of new powder materials with even more remarkable properties. Additionally, advancements in powder handling and processing techniques will make these materials more accessible and cost-effective for a wider range of industries. |
About 3DP mETAL
Product Category
ติดต่อเรา
มีคำถามอะไรไหม? ส่งข้อความมาเดี๋ยวนี้! หลังจากที่ได้รับข้อความแล้ว เราจะประมวลผลคำขอของคุณพร้อมทีมงานทั้งหมด