Welcome, dear reader! Let’s dive into the fascinating world of advanced material powders. Imagine a world where metals and ceramics are not just solid structures but can be transformed into fine powders with exceptional properties. These powders pave the way for groundbreaking innovations across various industries. Whether you’re a tech enthusiast, an engineer, or just curious, this guide will help you understand the intricacies and applications of advanced material powders.
Overview of Advanced Material Powders
Advanced material powders are finely milled metals, ceramics, and composites that exhibit unique physical and chemical properties. These powders are integral to manufacturing processes such as additive manufacturing (3D printing), coating, and sintering. They provide superior performance in terms of strength, durability, and resistance to extreme conditions.
Key Features of Advanced Material Powders:
- High purity and uniform particle size
- Enhanced mechanical properties
- การนำความร้อนและไฟฟ้าที่ดีเยี่ยม
- High surface area to volume ratio
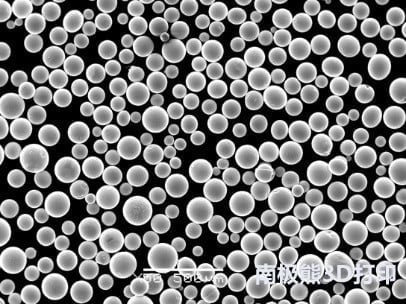
Types and Characteristics of Advanced Material Powders
Here’s a detailed look at specific metal powder models, their compositions, properties, and characteristics.
Metal Powder Model | องค์ประกอบ | คุณสมบัติ | ลักษณะเฉพาะ |
---|---|---|---|
Titanium Alloy (Ti-6Al-4V) | Titanium, Aluminum, Vanadium | High strength, corrosion resistance, biocompatibility | Widely used in aerospace, medical implants |
Stainless Steel 316L | Iron, Chromium, Nickel, Molybdenum | Excellent corrosion resistance, good mechanical properties | Ideal for marine and medical applications |
Aluminum Alloy (AlSi10Mg) | Aluminum, Silicon, Magnesium | Lightweight, high thermal conductivity | Commonly used in automotive and aerospace industries |
Inconel 718 | Nickel, Chromium, Iron, Molybdenum, Niobium | High temperature resistance, good mechanical strength | Suitable for turbine engines, power plants |
Cobalt-Chromium (CoCr) | Cobalt, Chromium | High wear resistance, biocompatibility | Used in dental and orthopedic implants |
ทองแดง (Cu) | ทองแดง | นำไฟฟ้าและความร้อนได้ดี | Used in electrical components, heat exchangers |
Tungsten Carbide (WC) | Tungsten, Carbon | Extremely hard, wear resistance | Used in cutting tools, mining machinery |
Nickel Alloy (NiCr) | Nickel, Chromium | Oxidation resistance, high-temperature stability | Ideal for chemical processing equipment |
Magnesium Alloy (AZ91D) | Magnesium, Aluminum, Zinc | Lightweight, good castability | Used in automotive and electronics industries |
Boron Carbide (B4C) | Boron, Carbon | High hardness, low density | Used in ballistic armor, abrasives |
Applications of Advanced Material Powders
These powders find applications in diverse fields, making them invaluable in modern technology and industry.
แอปพลิเคชัน | Materials Used | คำอธิบาย |
---|---|---|
ส่วนประกอบอากาศยาน | Titanium Alloys, Inconel | Lightweight and strong materials for aircraft parts |
Medical Implants | Titanium Alloy, CoCr | Biocompatible powders for prosthetics and implants |
อะไหล่รถยนต์ | Aluminum Alloys, Magnesium Alloys | Lightweight materials for fuel efficiency |
การพิมพ์สามมิติ | Stainless Steel, Aluminum, Titanium | Precise manufacturing of complex structures |
Coatings | Tungsten Carbide, Nickel Alloys | Durable coatings for wear and corrosion resistance |
เครื่องใช้ไฟฟ้า | Copper, Aluminum | Conductive powders for electronic components |
Cutting Tools | Tungsten Carbide, Boron Carbide | Hard materials for efficient cutting and drilling |
พลังงาน | Nickel Alloys, Stainless Steel | Materials for turbines, fuel cells, and batteries |
การป้องกัน | Boron Carbide, Titanium | Lightweight and strong materials for armor and weaponry |
กระบวนการทางเคมี | Nickel Alloys, Stainless Steel | Corrosion-resistant materials for chemical handling |
Specifications, Sizes, Grades, and Standards
When selecting advanced material powders, it’s crucial to consider their specifications to ensure they meet the required standards for your application.
Material | Particle Size Range | Grades | มาตรฐาน |
---|---|---|---|
Titanium Alloy (Ti-6Al-4V) | 15-45 µm, 45-100 µm | ชั้นปีที่ 23 | ASTM F1472 |
Stainless Steel 316L | 15-45 µm, 45-100 µm | AISI 316L | ASTM A276 |
Aluminum Alloy (AlSi10Mg) | 20-63 µm | A360, A380 | ASTM B85 |
Inconel 718 | 15-53 µm | UNS N07718 | ASTM B637 |
Cobalt-Chromium (CoCr) | 20-50 µm | F75 | ASTM F1537 |
ทองแดง (Cu) | 10-50 µm | C11000 | ASTM B170 |
Tungsten Carbide (WC) | 1-5 µm, 5-15 µm | – | ISO 9001 |
Nickel Alloy (NiCr) | 15-45 µm | – | ASTM B333 |
Magnesium Alloy (AZ91D) | 30-50 µm | AZ91D | ASTM B93/B93M |
Boron Carbide (B4C) | 1-10 µm | – | MIL-PRF-9954B |
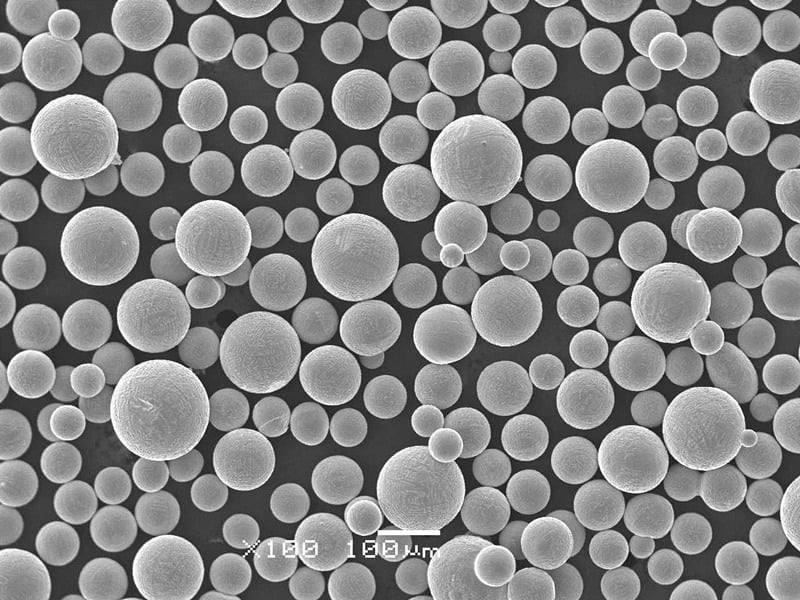
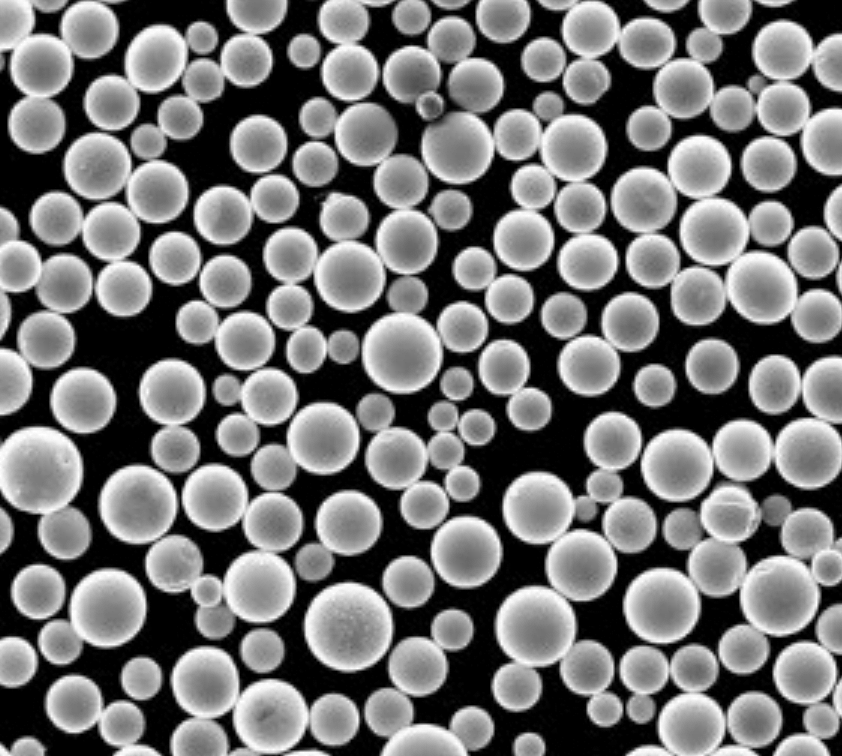
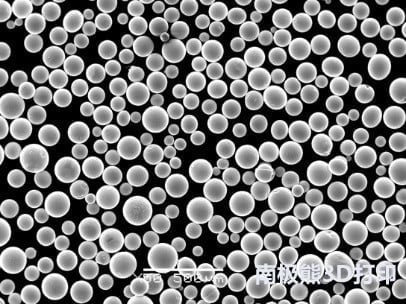
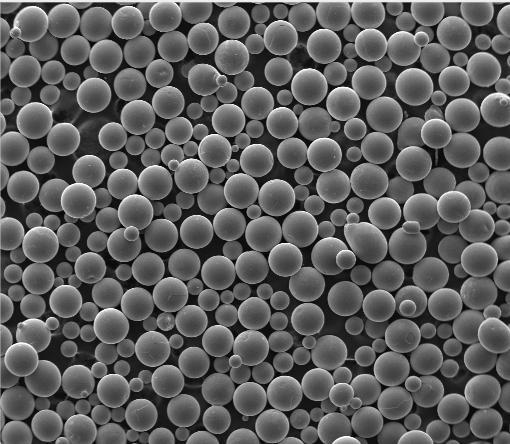
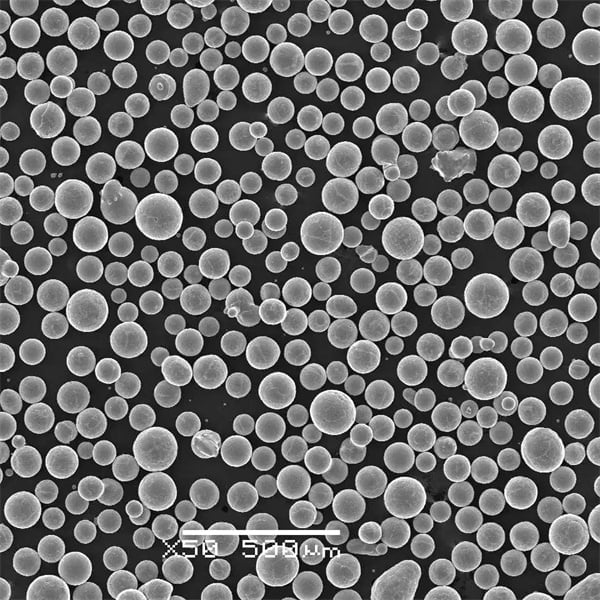
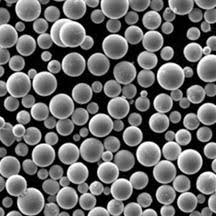
Suppliers and Pricing Details
The market for advanced material powders is diverse, with several suppliers offering a range of products. Pricing can vary based on the material, quantity, and specifications.
ซัพพลายเออร์ | Material | Price Range (per kg) | Notes |
---|---|---|---|
Höganäs AB | Stainless Steel, Copper | $50 – $200 | Global supplier with a broad portfolio |
Carpenter Technology | Titanium, Nickel Alloys | $100 – $500 | High-performance alloys for various industries |
แชนด์วิค | Tungsten Carbide, Inconel | $200 – $800 | Specializes in hard and superalloy powders |
ATI Metals | Titanium Alloys, Stainless Steel | $150 – $600 | Known for high-quality aerospace materials |
GKN Hoeganaes | Aluminum, Iron Alloys | $40 – $180 | Leader in metal powders for additive manufacturing |
Eramet | Nickel, Cobalt Alloys | $120 – $400 | Focuses on energy and industrial applications |
Kennametal | Tungsten Carbide, Boron Carbide | $250 – $900 | Offers wear-resistant materials for cutting tools |
Valimet | Aluminum Alloys | $80 – $250 | Provides spherical aluminum powders |
HC Starck | Titanium, Tantalum | $130 – $550 | Specializes in refractory metals |
Aubert & Duval | Nickel Alloys, Stainless Steel | $150 – $500 | Supplies high-performance materials for critical applications |
Pros and Cons: Comparing Advanced Material Powders
Understanding the advantages and limitations of each material is crucial for making an informed decision.
Material | ข้อได้เปรียบ | ข้อเสีย |
---|---|---|
Titanium Alloy (Ti-6Al-4V) | High strength-to-weight ratio, corrosion resistance, biocompatibility | Expensive, challenging to machine |
Stainless Steel 316L | Corrosion resistance, good mechanical properties, biocompatibility | Heavier than aluminum and titanium |
Aluminum Alloy (AlSi10Mg) | Lightweight, good thermal conductivity, cost-effective | Lower strength compared to titanium |
Inconel 718 | High temperature resistance, good mechanical strength | High cost, difficult to machine |
Cobalt-Chromium (CoCr) | High wear resistance, biocompatibility | Expensive, limited machinability |
ทองแดง (Cu) | Excellent electrical and thermal conductivity, cost-effective | Lower mechanical strength, prone to oxidation |
Tungsten Carbide (WC) | Extreme hardness, wear resistance | Brittle, high cost |
Nickel Alloy (NiCr) | Oxidation resistance, high-temperature stability | Expensive, difficult to process |
Magnesium Alloy (AZ91D) | Lightweight, good castability | Corrosion-prone, lower mechanical strength |
Boron Carbide (B4C) | High hardness, low density | Brittle, expensive |
Advanced Material Powders in Additive Manufacturing
Additive manufacturing, or 3D printing, has revolutionized how we produce complex components. Advanced material powders play a pivotal role in this technology, enabling the creation of intricate designs with superior material properties.
Key Benefits of Using Advanced Material Powders in 3D Printing:
- Precision: Achieve high accuracy in complex geometries.
- Customization: Tailor material properties to specific needs.
- Efficiency: Reduce waste compared to traditional manufacturing.
- Speed: Accelerate prototyping and production timelines.
Composition of Advanced Material Powders
Understanding the composition of advanced material powders is essential for selecting the right material for your application. Each powder’s unique blend of elements contributes to its specific properties.
Titanium Alloy (Ti-6Al-4V)
- การเรียบเรียง: 90% Titanium (Ti), 6% Aluminum (Al), 4% Vanadium (V)
- Key Properties: High strength-to-weight ratio, corrosion resistance, excellent fatigue resistance
- Applications: Aerospace components, medical implants, high-performance parts
Stainless Steel 316L
- การเรียบเรียง: 16% Chromium (Cr), 10% Nickel (Ni), 2% Molybdenum (Mo), balance Iron (Fe)
- Key Properties: Excellent corrosion resistance, good mechanical strength, high-temperature resistance
- Applications: Marine environments, medical devices, food processing equipment
Aluminum Alloy (AlSi10Mg)
- การเรียบเรียง: 90% Aluminum (Al), 10% Silicon (Si), 0.3% Magnesium (Mg)
- Key Properties: Lightweight, good thermal and electrical conductivity, high strength
- Applications: Automotive parts, aerospace components, industrial machinery
Inconel 718
- การเรียบเรียง: 50% Nickel (Ni), 19% Chromium (Cr), 5% Molybdenum (Mo), 3% Niobium (Nb), balance Iron (Fe)
- Key Properties: High temperature and oxidation resistance, good mechanical strength
- Applications: Turbine engines, aerospace applications, high-stress environments
Cobalt-Chromium (CoCr)
- การเรียบเรียง: 60% Cobalt (Co), 30% Chromium (Cr), 10% Molybdenum (Mo)
- Key Properties: High wear resistance, biocompatibility, high hardness
- Applications: Dental implants, orthopedic prosthetics, high-wear components
ทองแดง (Cu)
- การเรียบเรียง: 99% Copper (Cu), trace impurities
- Key Properties: Excellent electrical and thermal conductivity, malleability
- Applications: Electrical wiring, heat exchangers, electronics
Tungsten Carbide (WC)
- การเรียบเรียง: 94% Tungsten (W), 6% Carbon (C)
- Key Properties: Extreme hardness, high wear resistance, high melting point
- Applications: Cutting tools, mining machinery, industrial abrasives
Nickel Alloy (NiCr)
- การเรียบเรียง: 75% Nickel (Ni), 15% Chromium (Cr), trace amounts of other elements
- Key Properties: High-temperature stability, oxidation resistance, good mechanical properties
- Applications: Chemical processing equipment, furnace components, gas turbines
Magnesium Alloy (AZ91D)
- การเรียบเรียง: 90% Magnesium (Mg), 9% Aluminum (Al), 1% Zinc (Zn)
- Key Properties: Lightweight, good castability, high strength-to-weight ratio
- Applications: Automotive parts, aerospace components, electronic housings
Boron Carbide (B4C)
- การเรียบเรียง: 80% Boron (B), 20% Carbon (C)
- Key Properties: High hardness, low density, excellent wear resistance
- Applications: Ballistic armor, abrasives, nuclear reactors
Characteristics of Advanced Material Powders
The characteristics of advanced material powders play a vital role in determining their suitability for specific applications. Here’s a closer look at their defining attributes:
คุณสมบัติเชิงกล
- จุดแข็ง: How well a material can withstand forces without breaking. For instance, Tungsten Carbide’s extreme hardness makes it ideal for cutting tools, while Titanium Alloy offers high strength with a lower density.
- Toughness: The ability of a material to absorb energy and deform without fracturing. Materials like Inconel 718 excel here, especially under high temperatures.
คุณสมบัติทางความร้อน
- Conductivity: The ability to conduct heat or electricity. Copper leads in thermal and electrical conductivity, while Tungsten Carbide and Boron Carbide have high melting points and are used in high-temperature applications.
- Expansion: How much a material expands with temperature changes. Materials used in aerospace and electronics need low thermal expansion to maintain dimensional stability.
Chemical Properties
- Corrosion Resistance: The ability to withstand deterioration caused by chemicals or environmental conditions. Stainless Steel 316L and Cobalt-Chromium are highly resistant to corrosion, making them suitable for harsh environments.
- Reactivity: How a material reacts with other substances. For example, Magnesium Alloys can be prone to corrosion if not treated properly.
คุณสมบัติทางฟิสิกส์
- ความหนาแน่น: The mass per unit volume of a material. Magnesium alloys are known for their low density, making them useful in applications where weight reduction is critical.
- Hardness: The resistance to surface deformation. Boron Carbide’s high hardness is beneficial for wear-resistant applications.
Advantages and Limitations of Advanced Material Powders
Choosing the right material powder involves weighing its advantages against potential limitations. Here’s a comparison of various materials based on their benefits and drawbacks:
Titanium Alloy (Ti-6Al-4V)
- Advantages: High strength-to-weight ratio, excellent corrosion resistance, biocompatibility.
- Limitations: Expensive, challenging to machine.
Stainless Steel 316L
- Advantages: Excellent corrosion resistance, good mechanical properties, biocompatibility.
- Limitations: Heavier compared to aluminum and titanium, more expensive than some alternatives.
Aluminum Alloy (AlSi10Mg)
- Advantages: Lightweight, good thermal conductivity, cost-effective.
- Limitations: Lower strength compared to titanium, less suitable for high-stress applications.
Inconel 718
- Advantages: High temperature and oxidation resistance, good mechanical strength.
- Limitations: High cost, difficult to machine.
Cobalt-Chromium (CoCr)
- Advantages: High wear resistance, biocompatibility.
- Limitations: Expensive, challenging to process.
ทองแดง (Cu)
- Advantages: Excellent electrical and thermal conductivity, relatively low cost.
- Limitations: Lower mechanical strength, prone to oxidation.
Tungsten Carbide (WC)
- Advantages: Extreme hardness, excellent wear resistance.
- Limitations: Brittle, high cost.
Nickel Alloy (NiCr)
- Advantages: High-temperature stability, oxidation resistance.
- Limitations: Expensive, difficult to process.
Magnesium Alloy (AZ91D)
- Advantages: Lightweight, good castability.
- Limitations: Corrosion-prone, lower mechanical strength.
Boron Carbide (B4C)
- Advantages: High hardness, low density.
- Limitations: Brittle, expensive.
Advanced Material Powders in Additive Manufacturing
Additive manufacturing, or 3D printing, has revolutionized how we produce complex components. Advanced material powders play a pivotal role in this technology, enabling the creation of intricate designs with superior material properties.
Key Benefits of Using Advanced Material Powders in 3D Printing
- Precision: Achieve high accuracy in complex geometries. Advanced material powders allow for the fabrication of intricate parts that would be challenging with traditional manufacturing methods.
- Customization: Tailor material properties to specific needs. Different powders can be combined or treated to achieve desired characteristics, such as increased strength or improved thermal resistance.
- Efficiency: Reduce waste compared to traditional manufacturing. Additive manufacturing builds objects layer by layer, minimizing material wastage and allowing for efficient use of expensive powders.
- Speed: Accelerate prototyping and production timelines. Advanced powders enable rapid production of prototypes and final parts, speeding up the development process and reducing time-to-market.
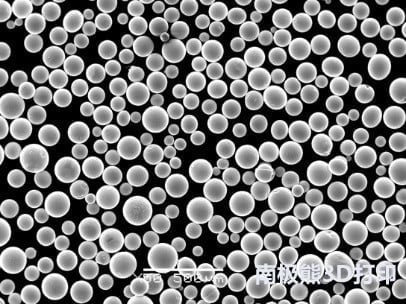
คำถามพบบ่อย
Here’s a handy FAQ section to address common questions about advanced material powders:
Question | Answer |
---|---|
What are advanced material powders used for? | Advanced material powders are used in various applications including aerospace, medical implants, automotive parts, and 3D printing. They provide enhanced performance characteristics like high strength, low weight, and excellent thermal resistance. |
How are metal powders produced? | Metal powders are produced through processes such as atomization, mechanical milling, and chemical reduction. Each method affects the powder’s particle size, shape, and distribution, impacting its performance in applications. |
What is the difference between spherical and irregular powders? | Spherical powders have a round shape, which enhances flowability and packing density, making them ideal for additive manufacturing. Irregular powders, on the other hand, may be used in traditional powder metallurgy processes but can lead to uneven packing and flow issues. |
How do I choose the right powder for my application? | Choosing the right powder depends on factors like the material’s properties (e.g., strength, conductivity), the manufacturing process, and the intended application. Consider the specific requirements of your project and consult with suppliers to select the best powder. |
Are there any safety concerns with handling advanced material powders? | Yes, safety is crucial when handling advanced material powders. Many powders can be hazardous if inhaled or ingested, and some may be reactive with moisture or other chemicals. Always follow safety guidelines, use appropriate protective equipment, and ensure proper ventilation. |
Can advanced material powders be recycled? | Yes, many advanced material powders can be recycled. For instance, excess powder from additive manufacturing can often be reused. However, recycling processes vary |
About 3DP mETAL
Product Category
ติดต่อเรา
มีคำถามอะไรไหม? ส่งข้อความมาเดี๋ยวนี้! หลังจากที่ได้รับข้อความแล้ว เราจะประมวลผลคำขอของคุณพร้อมทีมงานทั้งหมด