Imagine a world where complex, lightweight metal parts can be conjured from a digital file, layer by layer, with minimal waste. This isn’t science fiction; it’s the reality of aluminum additive manufacturing (AM), also known as 3D printing for metals.
This revolutionary technology is transforming industries like aerospace, automotive, and consumer goods, offering a treasure trove of benefits for designers, engineers, and manufacturers alike. But how exactly does it work? What are the different approaches, and what are the exciting applications taking flight with aluminum AM? Buckle up, because we’re about to delve into the fascinating world of crafting metal from thin air.
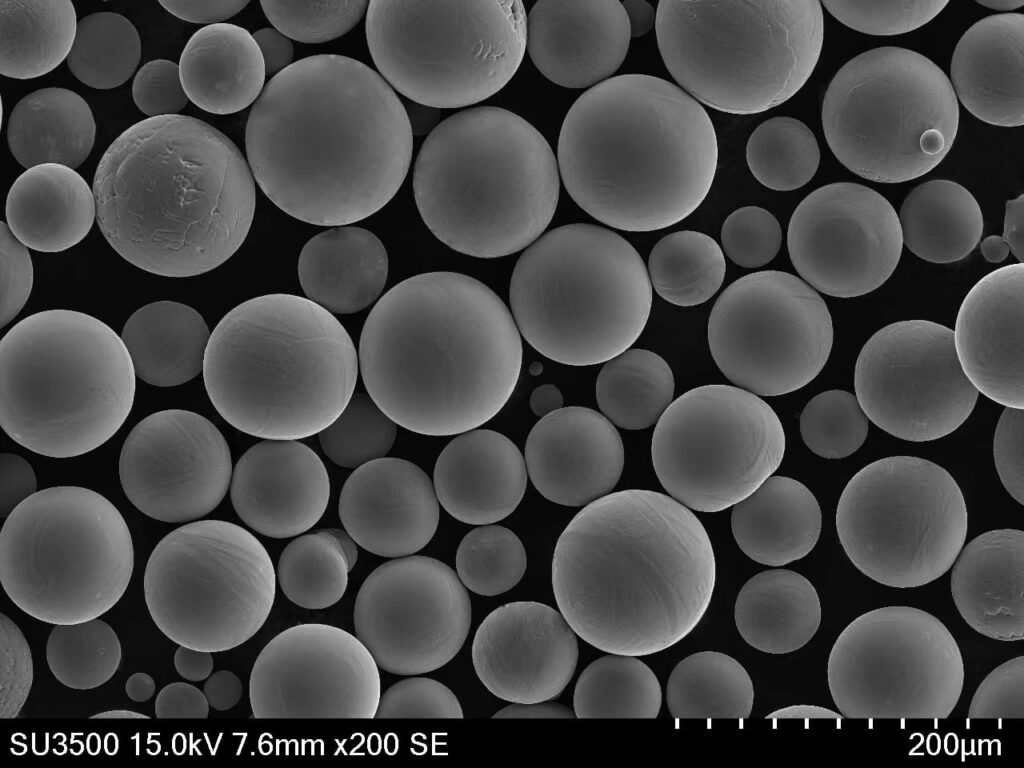
Common Aluminum Additive Manufacturing Methods
Aluminum AM isn’t a one-size-fits-all solution. There are several techniques vying for dominance, each with its own strengths and limitations. Let’s explore the three most prominent players in this metallic printing game:
- Selective Laser Melting (SLM): Picture a high-powered laser acting like a virtual sculptor. In SLM, a laser beam selectively melts aluminum powder layer by layer, meticulously following a digital blueprint. This method boasts incredible precision and detail, making it ideal for intricate, high-performance parts. Think lightweight aerospace components with complex internal structures – feats impossible with traditional manufacturing.
However, SLM comes with a hefty price tag. The high-powered lasers and meticulous process control translate to slower printing speeds and higher costs compared to other methods. Additionally, residual stresses from the rapid solidification of the metal can sometimes pose challenges.
- Electron Beam Melting (EBM): If lasers are the delicate artists in the AM world, electron beams are the industrial workhorses. EBM utilizes a concentrated beam of electrons in a vacuum chamber to melt aluminum powder. This method offers several advantages: faster build rates compared to SLM and the ability to handle a wider range of aluminum alloys, including those with higher melting points.
However, EBM also has its drawbacks. The vacuum environment adds complexity to the setup, and the process can be susceptible to warping due to the high temperatures involved. Additionally, surface finish can be rougher compared to SLM, requiring additional post-processing steps.
- Binder Jet Additive Manufacturing (BJAM): Here’s where things get a bit more unconventional. BJAM uses a liquid binding agent to selectively glue together aluminum powder particles, layer by layer. After printing, the part undergoes a debinding and sintering process to remove the binder and fuse the metal particles together.
BJAM offers several advantages. It’s significantly faster and cheaper compared to SLM and EBM, making it a good option for prototyping or non-critical applications. Additionally, it can handle larger build volumes, allowing for the creation of bigger parts.
The downside? BJAM parts typically have lower mechanical properties compared to those produced by SLM or EBM. Additionally, the post-processing steps can be time-consuming and add to the overall production time.
Choosing the Right Method: Picking the ideal AM technique depends on your specific needs. If precision and strength are paramount, SLM might be the way to go. If speed and cost are your primary concerns, BJAM could be a good option. EBM occupies a middle ground, offering a balance between speed and strength. Consulting with an AM expert can help you navigate this decision and select the method that best suits your application.
The Winning Formula: Aluminum Alloys for AM
Not all aluminum alloys are created equal for AM. Traditional casting or forging alloys might not translate well to the rapid heating and cooling cycles involved in the printing process. Here are some key considerations when selecting aluminum alloys for AM:
- Powder characteristics: The aluminum powder used for AM needs to be highly spherical and flow freely to ensure smooth layer formation. Irregularly shaped particles can lead to inconsistencies and defects in the final part.
- Melt pool behavior: Certain alloys are more prone to cracking during the printing process due to the rapid solidification. Alloys with elements like silicon or magnesium can help improve crack resistance.
- Post-processing requirements: Some alloys might require extensive heat treatment or hot isostatic pressing (HIP) to achieve the desired mechanical properties. These additional steps can add to the overall cost and production time.
Popular choices for aluminum AM include:
- AlSi10Mg: This versatile alloy offers a good balance between strength, ductility, and printability. It’s commonly used for applications like automotive components, brackets, and housings.
- F357: This high-strength aluminum alloy finds application in demanding environments like aerospace and defense. It boasts excellent mechanical properties but requires careful process control to avoid cracking.
- AA2024: This widely used alloy offers a good strength-to-weight ratio. However, it’s more susceptible to cracking compared to other options and might require post-processing for critical
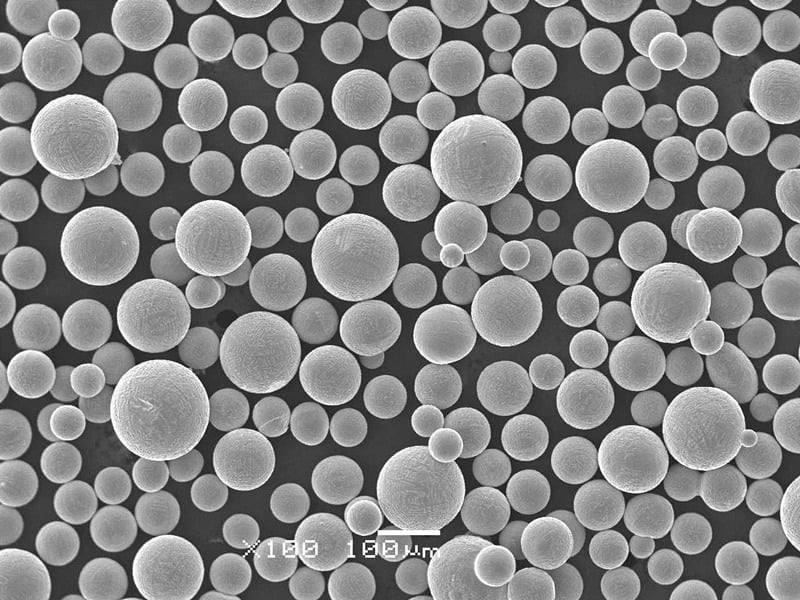
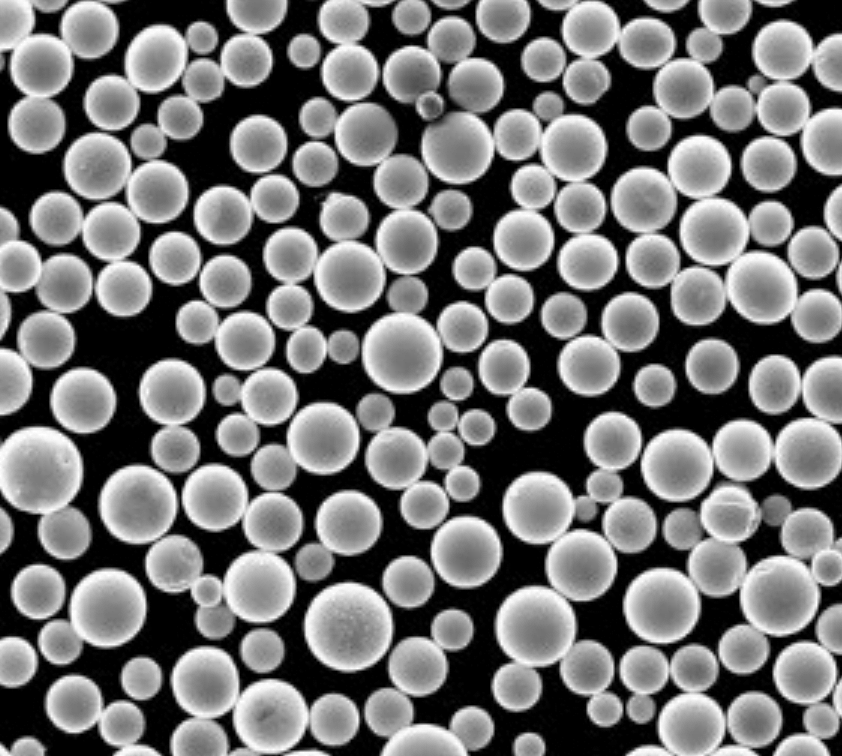
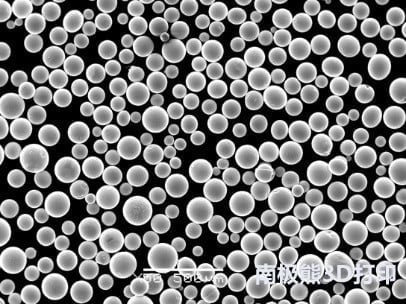
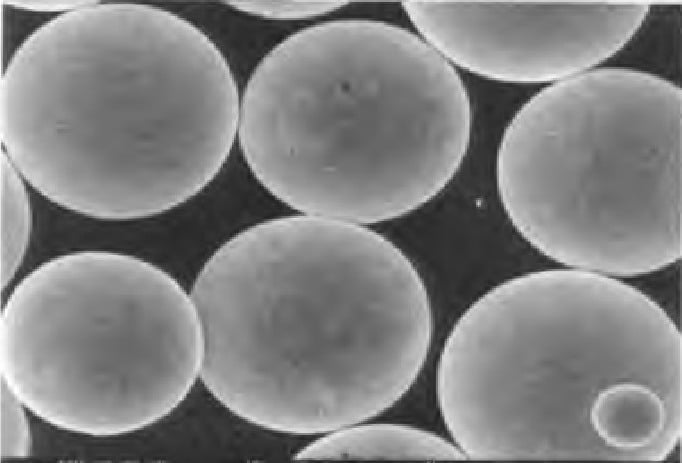
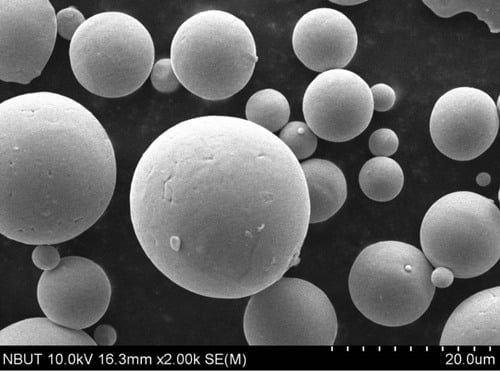
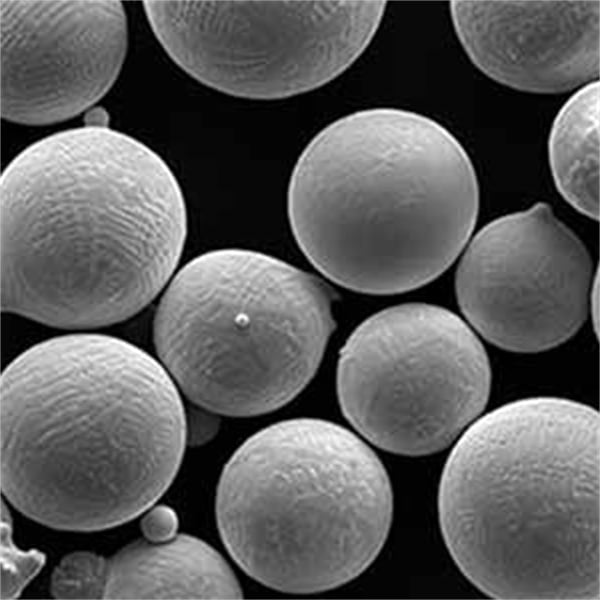
Applications of Aluminum Additive Manufacturing
Aluminum AM isn’t just a technological marvel; it’s a game-changer for various industries. Here’s a glimpse into how this technology is taking flight across different sectors:
การบินและอวกาศ: Shedding weight is an eternal quest in the aerospace industry. Every gram saved translates to increased fuel efficiency and payload capacity. Aluminum AM is a perfect fit for this mission.
- Complex, lightweight components: Imagine intricate lattice structures that provide immense strength while minimizing weight. AM can create such components for aircraft wings, engine mounts, and other critical parts. This translates to lighter, more fuel-efficient airplanes with longer ranges.
- Rapid prototyping and customization: Developing and testing new aircraft designs traditionally involves long lead times and expensive tooling. AM allows for rapid prototyping of components, enabling engineers to iterate and optimize designs quickly. Additionally, AM can be used to create customized parts for specific applications, a boon for maintenance and repair.
อุตสาหกรรมยานยนต์: The race for lighter, more fuel-efficient vehicles is heating up, and aluminum AM is at the forefront.
- Performance parts: High-strength, lightweight components like pistons, connecting rods, and suspension parts can be crafted using AM. This translates to better performance, handling, and fuel economy.
- Consolidation and design freedom: AM allows for the consolidation of multiple parts into a single, lighter component. This not only reduces weight but also simplifies assembly processes. Additionally, the design freedom offered by AM allows for the creation of parts with complex geometries that would be impossible with traditional manufacturing techniques.
Consumer Goods: Aluminum AM isn’t just about spaceships and race cars; it’s finding its way into everyday products.
- Custom prosthetics and implants: Imagine personalized prosthetics and implants that perfectly match a patient’s anatomy. AM allows for the creation of such intricate, customized medical devices, improving patient outcomes and quality of life.
- Luxury and high-performance products: From lightweight, high-strength bicycle frames to customized sporting goods, AM is making its mark on the high-end consumer market. The ability to create unique, complex designs is a major draw for these applications.
Beyond these examples, the applications of aluminum AM are constantly expanding. From medical devices to architectural components, this technology is pushing the boundaries of what’s possible.
Advantages and Considerations
While aluminum AM offers a plethora of benefits, there are also some factors to consider before diving headfirst. Here’s a balanced view of the pros and cons:
Advantages:
- Design freedom: Unlike traditional manufacturing methods, AM offers nearly limitless design possibilities. Complex geometries, internal channels, and lightweight structures are all achievable with AM.
- Lightweighting: The ability to create parts with high strength-to-weight ratios is a major advantage for industries like aerospace and automotive. Lighter parts translate to better fuel efficiency, performance, and payload capacity.
- Rapid prototyping: AM allows for the rapid creation of prototypes, accelerating the design and development process. This can significantly reduce time-to-market for new products.
- Reduced waste: Traditional manufacturing often involves significant material waste. AM, on the other hand, uses a layered approach, minimizing waste and making it a more sustainable option.
- Customization and mass personalization: AM allows for the creation of customized parts and products, catering to individual needs and preferences. This opens doors for new business models and customer experiences.
Considerations:
- Cost: While costs are coming down, AM can still be a relatively expensive technology compared to traditional manufacturing for mass production.
- Build speed and size: Building complex parts with AM can be a time-consuming process. Additionally, build volumes are often limited compared to traditional techniques.
- Surface finish: Depending on the chosen method, surface finish from AM processes might require additional finishing steps.
- Post-processing: Some AM processes require post-processing steps like heat treatment or hot isostatic pressing to achieve the desired mechanical properties. These steps can add to the overall production time and cost.
- Limited material selection: While the range of aluminum alloys available for AM is growing, it’s still not as extensive as those used in traditional manufacturing.
Despite these considerations, the advantages of aluminum AM are undeniable. As technology continues to advance and costs decrease, we can expect this technology to become even more widespread, revolutionizing the way we design, develop, and manufacture products across various industries.
The Future of Aluminum Additive Manufacturing
The future of aluminum AM is bright, with exciting possibilities on the horizon. Here are some trends to watch:
- Reduced costs and faster build times: As technology matures and production volumes increase, we can expect AM to become more cost-effective and faster. This will open up new applications for AM, making it a viable option for a wider range of products and industries.
- Multi-material printing: The ability to combine different materials within a single AM process is a future possibility. This could allow for the creation of parts with unique combinations of properties, such as high strength and conductivity.
- Hybrid manufacturing: AM can be integrated with traditional manufacturing techniques to create best-of-both-worlds solutions. For instance, complex internal structures could be printed using AM, while simpler external geometries could be manufactured traditionally.
- Standardization and qualification: As AM adoption grows, there’s a growing need for standardized processes and qualification procedures. This will ensure the consistent quality and reliability of AM parts for critical applications.
- Sustainability: The inherent efficiency and reduced waste associated with AM make it an attractive option from a sustainability standpoint. Additionally, AM can be used to create lighter components, which can contribute to lower energy consumption during product use.
The future of aluminum AM is a collaborative effort. Material scientists, engineers, machine manufacturers, and software developers all play a crucial role in pushing the boundaries of this technology. As these collaborations intensify, we can expect even more groundbreaking advancements in the years to come.
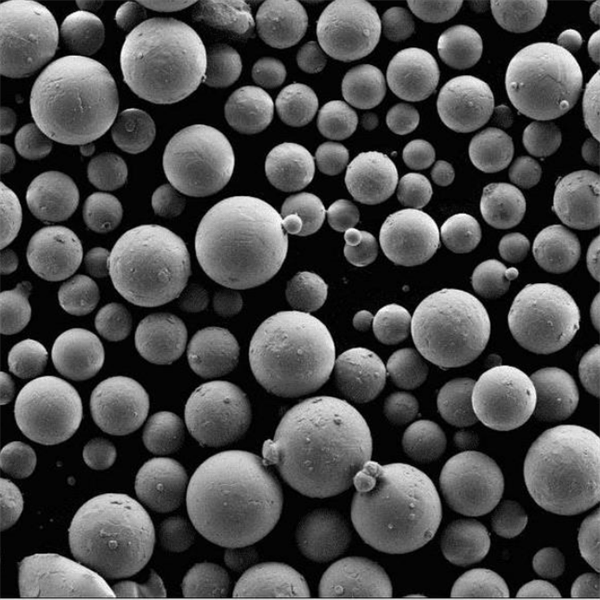
คำถามพบบ่อย
Here are some frequently asked questions (FAQs) about aluminum additive manufacturing to shed some light on this exciting technology:
Q: What are the advantages of aluminum AM compared to traditional manufacturing?
A: Aluminum AM offers several advantages, including design freedom, lightweighting, rapid prototyping, reduced waste, and customization. Traditional manufacturing techniques might be limited in these aspects.
Q: What are the limitations of aluminum AM?
A: Current limitations of aluminum AM include higher costs compared to mass production, slower build speeds and limited build volumes, potential surface finish issues, and post-processing requirements. Additionally, the selection of aluminum alloys for AM is still evolving.
Q: What industries are using aluminum AM?
A: Aluminum AM is finding applications in various industries, including aerospace, automotive, consumer goods, medical devices, and architecture.
Q: Is aluminum AM suitable for mass production?
A: While not currently the most cost-effective option for mass production, aluminum AM is becoming increasingly viable for smaller production runs or applications where the benefits of design freedom and lightweighting outweigh the cost considerations. As technology advances and costs decrease, AM could become a more mainstream option for mass production in the future.
Q: What is the future of aluminum AM?
A: The future of aluminum AM is full of promise. We can expect advancements in areas like reduced costs, faster build times, multi-material printing, hybrid manufacturing, and standardization. Additionally, sustainability considerations will likely play a significant role in the future development of this technology.
In conclusion, aluminum additive manufacturing is revolutionizing the way we design and manufacture metal parts. With its unique capabilities and ever-evolving potential, aluminum AM is poised to take flight in various industries, shaping the future of metal fabrication.
About 3DP mETAL
Product Category
ติดต่อเรา
มีคำถามอะไรไหม? ส่งข้อความมาเดี๋ยวนี้! หลังจากที่ได้รับข้อความแล้ว เราจะประมวลผลคำขอของคุณพร้อมทีมงานทั้งหมด