ภาพรวม
Have you ever heard the phrase, “less is more”? Well, when it comes to the powder metallurgy world, especially in additive manufacturing and high-precision applications, this adage holds true. Enter Fewer Satellite Particles Powder—a technological innovation that’s transforming industries by improving the quality and performance of metal powders. But what exactly does this term mean? And why should you care about it?
Fewer satellite particles refer to metal powders that are specifically engineered to have minimal satellite particles—those tiny, pesky, and often irregular attachments that cling to the surface of the primary powder particles. These can be problematic, causing issues in manufacturing processes and leading to defects in the final product.
In this article, we’re diving deep into the world of fewer satellite particles powder. We’ll explore the specific types of powders that fall under this category, their composition, characteristics, applications, and the advantages they offer over traditional powders. We’ll also compare various products available on the market, providing you with a comprehensive guide to making informed decisions.
What is Fewer Satellite Particles Powder?
If you’re picturing a space-themed product, you might be a little off course, but you’re not far from a revolution. Fewer satellite particles powder is a type of metal powder designed with precision in mind. Imagine a sphere—a perfect metal sphere. Now, picture tiny, irregular particles sticking to its surface. These are what we call satellite particles.
In many manufacturing processes, particularly in additive manufacturing like 3D printing, the presence of these satellite particles can cause significant issues. They lead to uneven layering, poor sintering, and overall lower-quality parts. This is where fewer satellite particles powder comes into play. By reducing or eliminating these satellites, manufacturers can achieve smoother surfaces, higher densities, and better mechanical properties in the final product.
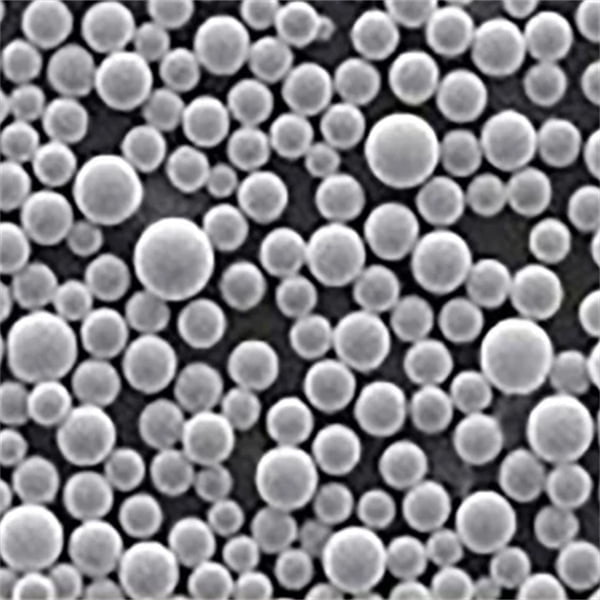
Composition of Fewer Satellite Particles Powder
Understanding the composition of fewer satellite particles powder is like getting to know the secret recipe of a master chef. The composition can vary depending on the base metal or alloy used and the specific process employed to produce the powder. Here, we break down the typical components and their roles.
Metal/Alloy | องค์ประกอบ | คุณสมบัติ | ใช้ |
---|---|---|---|
Titanium Alloys | Ti-6Al-4V, Ti-5Al-2.5Fe | High strength, low density, corrosion resistance | Aerospace, medical implants, automotive |
สเตนเลสสตีล | 316L, 304L, 17-4 PH | Corrosion resistance, high tensile strength | Medical devices, food processing equipment |
Aluminum Alloys | AlSi10Mg, 6061, 7075 | Lightweight, high strength, good conductivity | Automotive, aerospace, consumer electronics |
Nickel-Based Alloys | Inconel 718, Inconel 625 | High temperature resistance, corrosion resistance | Turbine blades, exhaust systems, chemical processing |
Cobalt-Chrome Alloys | CoCrMo, CoCrNi | Wear resistance, biocompatibility | Dental implants, orthopedic implants, turbine blades |
Copper Alloys | CuSn10, CuCrZr | High electrical conductivity, good corrosion resistance | Electrical components, heat exchangers |
Characteristics of Fewer Satellite Particles Powder
When comparing powders, fewer satellite particles powder often stands out due to its superior characteristics. Here’s what sets it apart:
- การกระจายขนาดของอนุภาค: Typically, fewer satellite particles powder has a narrow particle size distribution. This means that the particles are more uniform in size, leading to better packing density and smoother surface finishes in final products.
- Sphericity: The powder particles are often more spherical compared to traditional powders. High sphericity is crucial for consistent flowability, which is essential for processes like selective laser sintering (SLS) and direct metal laser sintering (DMLS).
- Surface Texture: The surface of fewer satellite particles powder is usually smoother, which reduces the risk of agglomeration (clumping together of particles), a common issue in traditional powders.
- ความไหลได้: Fewer satellite particles result in improved flowability, which is vital for powder-based manufacturing processes. Poor flowability can lead to inconsistent layering and defects in additive manufacturing.
- Packing Density: With fewer satellite particles, the packing density of the powder increases. This leads to denser, stronger parts when the powder is used in manufacturing.
Advantages of Fewer Satellite Particles Powder
Why should you consider using fewer satellite particles powder? Here are some compelling reasons:
1. Improved Mechanical Properties
Because the powder is more uniform and has better packing density, the resulting parts often exhibit superior mechanical properties. This means higher strength, better fatigue resistance, and improved durability.
2. Enhanced Surface Finish
One of the main issues with traditional powders is that they can produce parts with rough or uneven surfaces. Fewer satellite particles powder, with its smoother and more spherical particles, helps in achieving a finer surface finish, reducing the need for post-processing.
3. Better Flowability
In powder-based manufacturing processes, flowability is key. Poor flowability can cause inconsistent layering, leading to defects in the final product. Fewer satellite particles powder offers better flowability, ensuring more reliable and repeatable production.
4. Reduced Defects
With fewer satellite particles, there are fewer opportunities for defects to occur during manufacturing. This translates to higher-quality parts, fewer rejects, and lower production costs.
5. Versatility in Applications
Thanks to its improved properties, fewer satellite particles powder can be used in a wide range of applications, from aerospace and automotive to medical devices and consumer electronics.
Applications of Fewer Satellite Particles Powder
Given its superior characteristics, fewer satellite particles powder is used in a variety of high-precision applications. Here’s a look at some of the most common:
แอปพลิเคชัน | รายละเอียด |
---|---|
อวกาศ | Used for manufacturing lightweight, high-strength components with excellent fatigue resistance. |
Medical Implants | Ideal for producing biocompatible implants with smooth surfaces, reducing the risk of infection. |
ยานยนต์ | Utilized in the production of high-performance engine components, offering improved durability and reduced weight. |
Consumer Electronics | Provides the necessary precision for producing intricate parts in devices like smartphones and laptops. |
Turbine Blades | Used in the production of turbine blades that require high temperature and corrosion resistance. |
Dental Implants | Offers the precision and biocompatibility required for dental implants, ensuring a long-lasting, comfortable fit. |
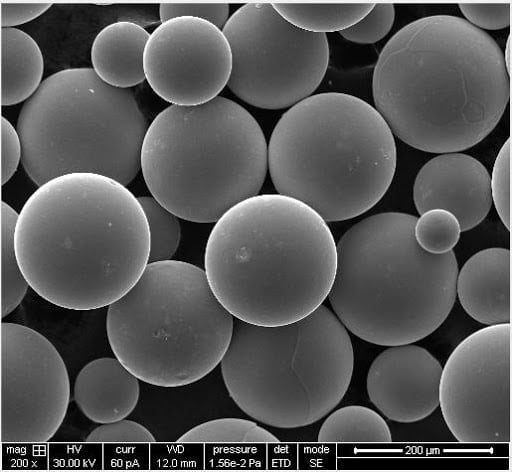
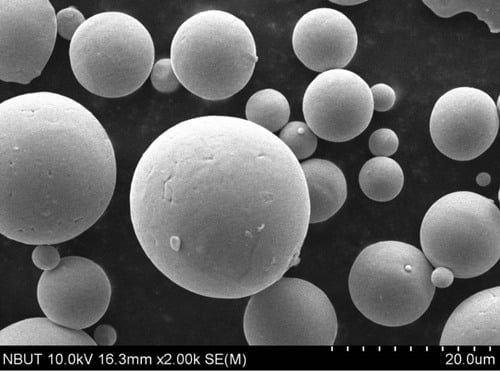
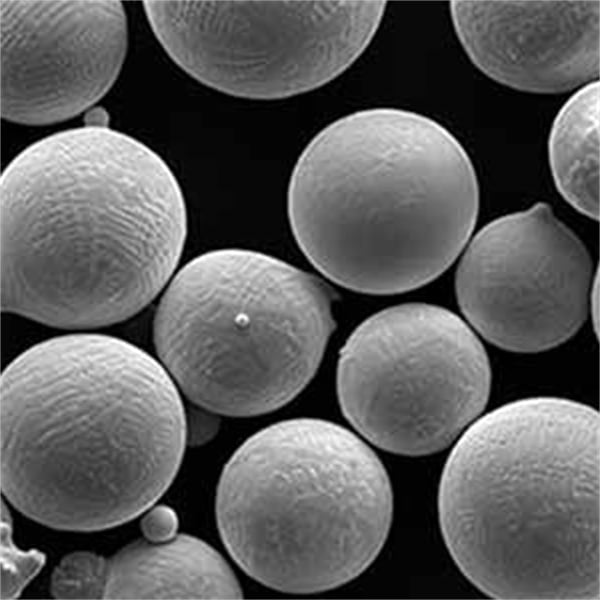
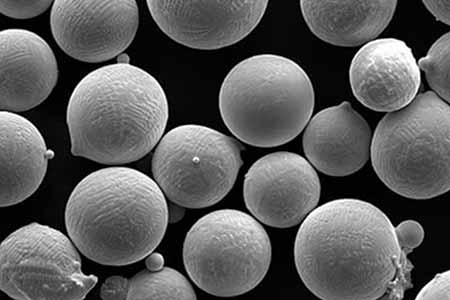
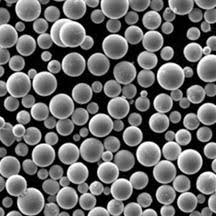
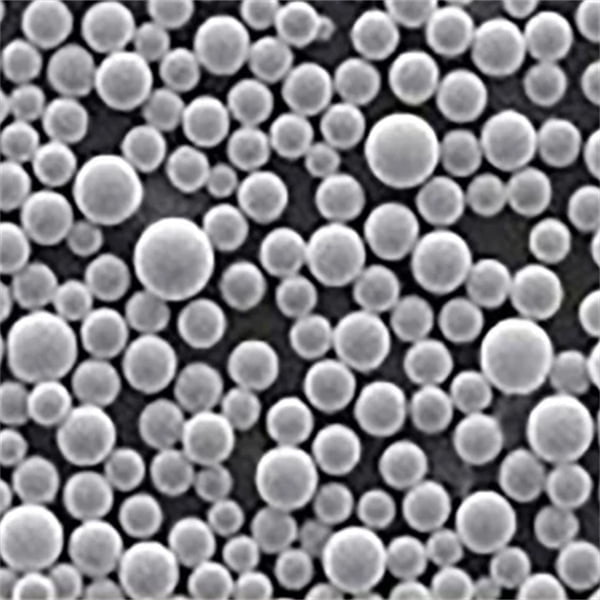
Specific Metal Powder Models
When selecting a fewer satellite particles powder, the specific model you choose can make all the difference. Below are some of the top metal powder models available, each tailored to specific applications and requirements.
1. EOS Titanium Ti64 Grade 23
คำอธิบาย: EOS Titanium Ti64 Grade 23 is a popular powder in the additive manufacturing industry, known for its high strength-to-weight ratio and excellent biocompatibility. This powder is often used in medical and aerospace applications where strength, lightweight, and corrosion resistance are critical.
2. Carpenter Additive 316L Stainless Steel
คำอธิบาย: Carpenter Additive’s 316L stainless steel powder is designed for parts requiring superior corrosion resistance and excellent mechanical properties. It’s commonly used in medical devices, food processing equipment, and various industrial applications.
3. Praxair TruForm AlSi10Mg
คำอธิบาย: Praxair’s TruForm AlSi10Mg is an aluminum alloy powder known for its high strength and good thermal conductivity. It’s widely used in automotive and aerospace applications where lightweight and durability are essential.
4. Sandvik Osprey Inconel 718
คำอธิบาย: Sandvik Osprey’s Inconel 718 powder is a nickel-based superalloy powder known for its high temperature and corrosion resistance. This powder is ideal for applications in the aerospace and energy sectors, where extreme conditions are the norm.
5. GKN Hoeganaes AncorTi
คำอธิบาย: GKN Hoeganaes’s AncorTi powder is a titanium-based powder designed for additive manufacturing. It’s prized for its excellent strength-to-weight ratio and is commonly used in aerospace and medical applications.
6. AP&C Cobalt-Chrome F75
คำอธิบาย: AP&C’s Cobalt-Chrome F75 powder is known for its excellent wear resistance and biocompatibility. It’s commonly used in dental and orthopedic implants, as well as in turbine blades.
7. Höganäs Amperit Copper 3D
คำอธิบาย: Höganäs’s Amperit Copper 3D is a high-purity copper powder designed for additive manufacturing. It’s known for its excellent electrical conductivity and is commonly used in electronics and heat exchangers.
8. LPW Technology Maraging Steel
คำอธิบาย: LPW Technology’s Maraging Steel powder is known for its high strength and toughness. It’s commonly used in
tooling and aerospace applications where durability is critical.
9. Arcam EBM Ti6Al4V Grade 5
คำอธิบาย: Arcam’s Ti6Al4V Grade 5 powder is a titanium alloy powder specifically designed for electron beam melting (EBM) processes. It’s used in aerospace and medical applications where high strength and low weight are required.
10. Carpenter Additive 17-4 PH Stainless Steel
คำอธิบาย: Carpenter Additive’s 17-4 PH stainless steel powder is a martensitic precipitation-hardening stainless steel powder known for its high strength and corrosion resistance. It’s commonly used in aerospace, automotive, and industrial applications.
Specifications, Sizes, Grades, and Standards
When selecting a fewer satellite particles powder, it’s crucial to consider the specifications, sizes, grades, and standards to ensure compatibility with your application.
Powder Model | Particle Size (μm) | เกรด | มาตรฐาน |
---|---|---|---|
EOS Titanium Ti64 Grade 23 | 15-45 | ชั้นปีที่ 23 | ASTM F136 |
Carpenter Additive 316L | 15-45 | 316L | ASTM A276 |
Praxair TruForm AlSi10Mg | 20-63 | AlSi10Mg | ASTM F3318 |
Sandvik Osprey Inconel 718 | 15-45 | Inconel 718 | AMS 5662 |
GKN Hoeganaes AncorTi | 15-45 | Ti6Al4V | ASTM F1472 |
AP&C Cobalt-Chrome F75 | 15-45 | F75 | ASTM F75 |
Höganäs Amperit Copper 3D | 15-45 | CuSn10 | UNS C90700 |
LPW Technology Maraging Steel | 20-63 | Maraging 300 | AMS 6514 |
Arcam EBM Ti6Al4V Grade 5 | 15-45 | ชั้น ป.5 | ASTM F1472 |
Carpenter Additive 17-4 PH | 15-45 | 17-4 PH | ASTM A564 |
Suppliers and Pricing Details
Choosing the right supplier is crucial for getting high-quality fewer satellite particles powder. Here’s a comparison of top suppliers, along with pricing details.
ซัพพลายเออร์ | Powder Model | Price/kg ($USD) | Lead Time | ที่ตั้ง |
---|---|---|---|---|
EOS GmbH | EOS Titanium Ti64 Grade 23 | 450 | 2-4 weeks | เยอรมนี |
Carpenter Additive | Carpenter Additive 316L | 200 | 4-6 weeks | สหรัฐอเมริกา |
Praxair Surface Technologies | Praxair TruForm AlSi10Mg | 150 | 3-5 weeks | สหรัฐอเมริกา |
Sandvik Osprey | Sandvik Osprey Inconel 718 | 350 | 4-8 weeks | สวีเดน |
GKN Hoeganaes | GKN Hoeganaes AncorTi | 400 | 4-6 weeks | สหรัฐอเมริกา |
AP&C (GE Additive) | AP&C Cobalt-Chrome F75 | 500 | 4-6 weeks | แคนาดา |
Höganäs AB | Höganäs Amperit Copper 3D | 100 | 2-4 weeks | สวีเดน |
เทคโนโลยี LPW | LPW Technology Maraging Steel | 250 | 4-6 weeks | สหราชอาณาจักร |
Arcam AB (GE Additive) | Arcam EBM Ti6Al4V Grade 5 | 450 | 4-8 weeks | สวีเดน |
Carpenter Additive | Carpenter Additive 17-4 PH | 300 | 4-6 weeks | สหรัฐอเมริกา |
Comparing Pros and Cons
Let’s break down the advantages and limitations of fewer satellite particles powder compared to traditional powders.
แฟคเตอร์ | Fewer Satellite Particles Powder | Traditional Powder |
---|---|---|
Surface Finish | Smoother surface, less post-processing required | Rougher surface, often requires extensive post-processing |
คุณสมบัติเชิงกล | Enhanced strength and durability | Variable, depending on particle distribution |
ความไหลได้ | Better flowability, ideal for complex geometries | Inconsistent flow, can lead to defects |
Defect Rate | Lower defect rate, higher quality parts | Higher defect rate, potential for more rejects |
ค่าใช้จ่าย | Higher initial cost but lower total cost due to fewer defects | Lower initial cost but potentially higher total cost due to defects |
Versatility | Suitable for a wide range of high-precision applications | May be limited in high-precision applications |
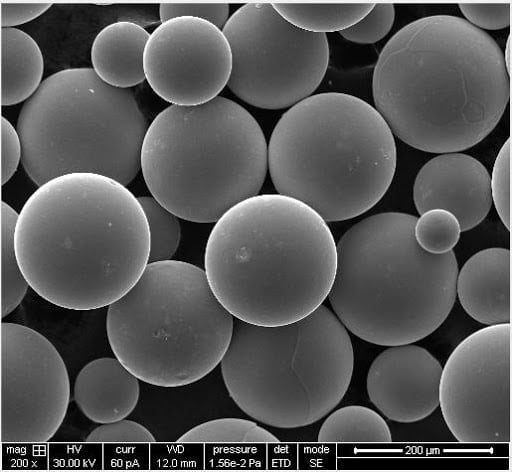
คำถามพบบ่อย
Q: What are satellite particles in metal powder?
A: Satellite particles are small, often irregularly shaped particles that adhere to the surface of the main powder particles. They can cause issues in manufacturing processes, leading to defects in the final product.
Q: Why is fewer satellite particles powder better?
A: Fewer satellite particles powder offers better flowability, improved surface finish, higher mechanical properties, and a lower defect rate, making it ideal for high-precision manufacturing processes.
Q: What industries benefit most from fewer satellite particles powder?
A: Industries like aerospace, medical devices, automotive, and consumer electronics benefit the most, where high precision, strength, and quality are critical.
Q: How does fewer satellite particles powder compare in cost to traditional powder?
A: While fewer satellite particles powder may have a higher initial cost, it can result in lower total production costs due to its superior performance and reduced defect rates.
Q: Can fewer satellite particles powder be used in all additive manufacturing processes?
A: Yes, fewer satellite particles powder is versatile and can be used in various additive manufacturing processes, including selective laser sintering (SLS), direct metal laser sintering (DMLS), and electron beam melting (EBM).
บทสรุป
The world of metal powders is vast and complex, but fewer satellite particles powder stands out as a game-changer for industries that demand high precision, strength, and quality. By understanding its composition, characteristics, advantages, and applications, you can make informed decisions that lead to better products and more efficient manufacturing processes.
Whether you’re in aerospace, automotive, or medical device manufacturing, investing in fewer satellite particles powder can offer significant returns in terms of product quality and production efficiency. As the technology continues to evolve, we can expect even greater innovations in this field, pushing the boundaries of what’s possible in manufacturing.
About 3DP mETAL
Product Category
ติดต่อเรา
มีคำถามอะไรไหม? ส่งข้อความมาเดี๋ยวนี้! หลังจากที่ได้รับข้อความแล้ว เราจะประมวลผลคำขอของคุณพร้อมทีมงานทั้งหมด