Overview of Gas Turbine Atomizing Air Systems
In the complex world of gas turbines, efficiency and performance are paramount. Among the myriad components that contribute to a turbine’s operation, the atomizing air system holds significant importance. This system plays a crucial role in ensuring that fuel is properly atomized, or broken into fine droplets, before combustion. The result? A more efficient and cleaner burn, leading to better performance and reduced emissions. In this guide, we’ll dive deep into the gas turbine atomizing air system, explore its components, materials used, characteristics, and much more.
Composition of Gas Turbine Atomizing Air Systems
Understanding the composition of a gas turbine atomizing air system is key to appreciating its function and importance. These systems typically consist of several key components, each made from materials selected for their durability and resistance to high temperatures and pressures.
ส่วนประกอบ | Material | Function | ลักษณะเฉพาะ |
---|---|---|---|
Atomizing Air Nozzles | Nickel-based superalloys | Breaks fuel into fine droplets | High-temperature resistance, corrosion-resistant |
Air Compressor | Titanium alloys | Compresses air for atomization | Lightweight, strong, high fatigue resistance |
Fuel Injector | Stainless steel | Injects fuel into combustion chamber | Durable, corrosion-resistant, high strength |
Heat Exchanger | Inconel | Preheats air to improve atomization | Withstands extreme heat, oxidation-resistant |
Control Valves | Hastelloy | Regulates air and fuel flow | Corrosion-resistant, high-strength |
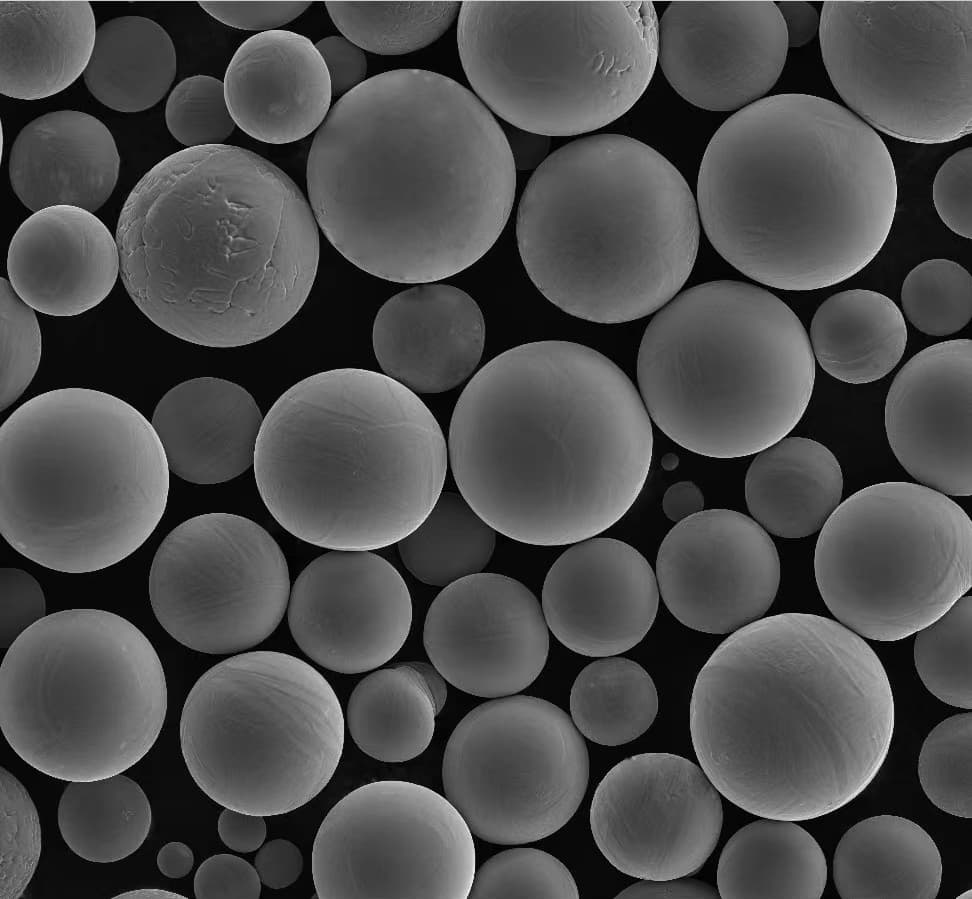
Characteristics of Gas Turbine Atomizing Air Systems
When it comes to characteristics, gas turbine atomizing air systems are designed to optimize the fuel combustion process. Below are some critical characteristics that define these systems:
1. High Efficiency
The atomizing air system significantly enhances the efficiency of fuel combustion by ensuring that the fuel is finely atomized. This leads to a more complete burn and reduces unburned hydrocarbons, improving the overall efficiency of the turbine.
2. Temperature and Pressure Resistance
Given the extreme conditions within a gas turbine, the atomizing air system must withstand high temperatures and pressures. The materials used, such as nickel-based superalloys and Inconel, are chosen specifically for their ability to endure such conditions without degrading.
3. Corrosion Resistance
Corrosion can be a major issue in gas turbines due to the presence of harsh chemicals and high temperatures. The atomizing air system components are typically made from corrosion-resistant materials like stainless steel and Hastelloy, ensuring longevity and reliability.
4. Precision in Fuel Delivery
Precision in atomizing air systems is critical. These systems are designed to deliver fuel in an extremely controlled manner, ensuring that the right amount of air mixes with the fuel for optimal combustion.
Advantages of Gas Turbine Atomizing Air Systems
Now that we’ve covered the basics, let’s explore why these systems are so advantageous in gas turbine operation:
1. Improved Combustion Efficiency
One of the primary benefits of a well-functioning atomizing air system is the improvement in combustion efficiency. By breaking the fuel into fine droplets, the system ensures that the fuel mixes more thoroughly with air, resulting in a more complete burn. This means less fuel is wasted, and more energy is extracted from each unit of fuel.
2. Reduced Emissions
A more complete burn also means fewer unburned hydrocarbons are released into the atmosphere. This leads to lower emissions, which is a critical factor in meeting environmental regulations and reducing the carbon footprint of gas turbine operations.
3. Extended Component Lifespan
Because the atomizing air system helps achieve more complete combustion, it reduces the amount of soot and other combustion by-products that can accumulate on turbine components. This leads to less wear and tear on the system, extending the lifespan of critical components and reducing maintenance costs.
4. Enhanced Turbine Performance
The efficiency gains from an optimized atomizing air system translate directly into better overall turbine performance. With more efficient fuel use, the turbine can produce more power while using less fuel, which is a win-win for operators.
Detailed Breakdown of Specific Metal Powder Models for Atomizing Air Systems
In the manufacturing of gas turbine atomizing air systems, various metal powders are utilized to create components with specific properties. Below, we outline some of the most commonly used metal powder models, detailing their composition, applications, and benefits.
Metal Powder Model | องค์ประกอบ | แอปพลิเคชัน | ประโยชน์ |
---|---|---|---|
Inconel 718 | Nickel-Chromium-Iron alloy | Atomizing air nozzles, heat exchangers | High strength, excellent corrosion and oxidation resistance |
Hastelloy X | Nickel-Chromium-Molybdenum-Iron alloy | Control valves, combustion chamber components | High-temperature strength, oxidation resistance |
Stellite 6 | Cobalt-based alloy | Fuel injectors, valve seats | Wear resistance, corrosion resistance, high-temperature hardness |
Haynes 230 | Nickel-Chromium-Tungsten-Molybdenum alloy | Air compressors, turbine blades | Excellent thermal stability, oxidation resistance |
Rene 41 | Nickel-Chromium-Cobalt-Molybdenum alloy | High-pressure turbine components | Superior high-temperature strength, creep resistance |
Incoloy 800H | Nickel-Iron-Chromium alloy | Heat exchangers, piping | Excellent strength and resistance to oxidation and carburization at high temperatures |
Alumina Toughened Zirconia (ATZ) | Zirconium dioxide stabilized with alumina | Atomizing air nozzles | High fracture toughness, wear resistance, thermal stability |
CMSX-4 | Single-crystal nickel-based superalloy | Turbine blades, vanes | High-temperature creep resistance, fatigue resistance |
Nimonic 263 | Nickel-Chromium-Cobalt-Molybdenum alloy | Combustion chamber liners, heat shields | Good weldability, oxidation resistance, high strength |
Cobalt-Chromium Alloy (CoCr) | Cobalt-Chromium alloy | High-wear components, nozzles | High corrosion resistance, excellent wear resistance |
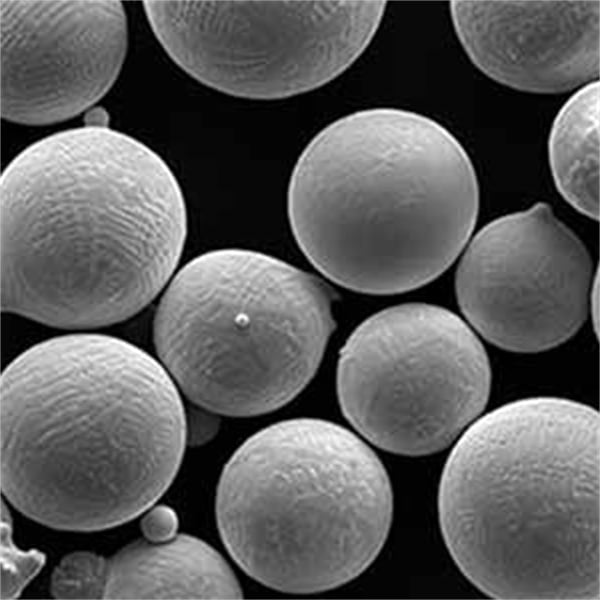
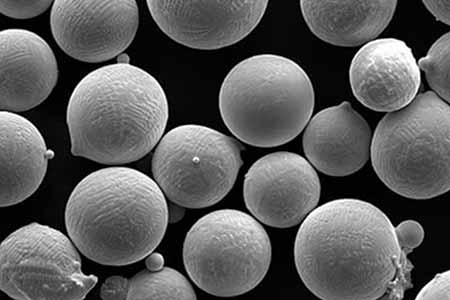
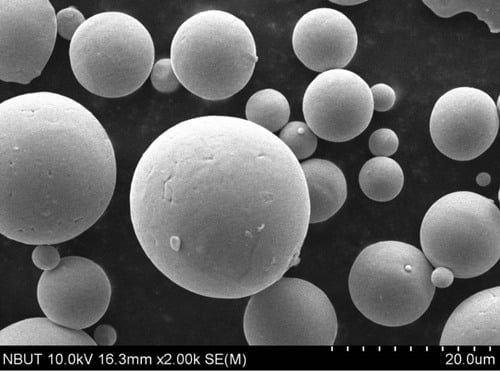
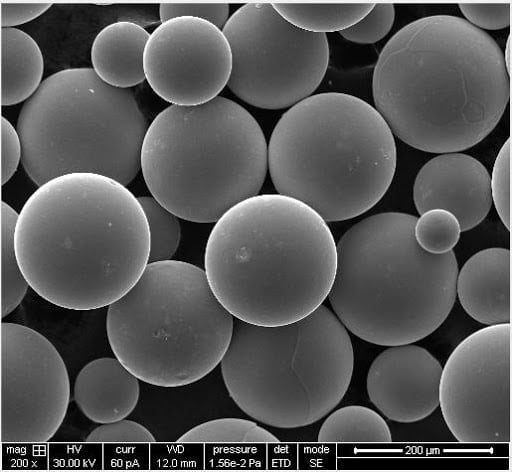
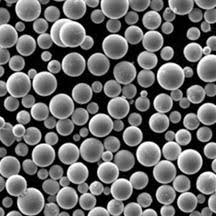
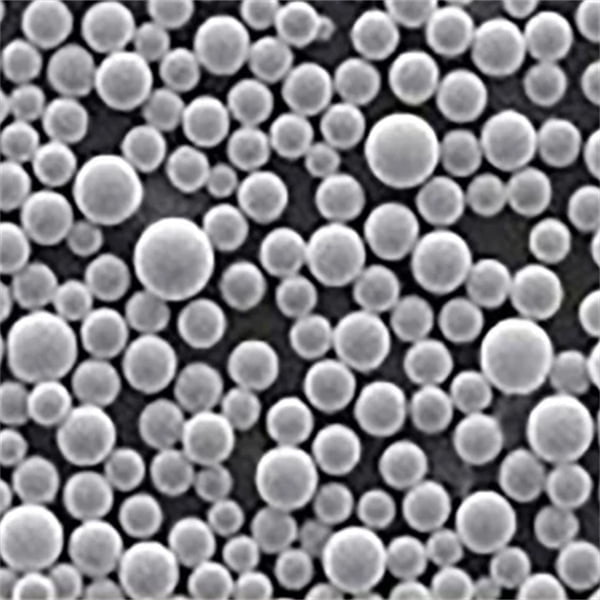
Applications of Gas Turbine Atomizing Air Systems
Gas turbine atomizing air systems are integral to a wide range of applications, particularly in industries where gas turbines are used for power generation, aviation, and marine propulsion. Below is a table summarizing key applications and the associated benefits.
แอปพลิเคชัน | อุตสาหกรรม | ประโยชน์ |
---|---|---|
การผลิตไฟฟ้า | พลังงาน | Enhanced efficiency, reduced emissions, extended turbine life |
Aviation | อวกาศ | Improved fuel efficiency, reduced weight, higher thrust-to-weight ratio |
Marine Propulsion | Maritime | Increased reliability, better fuel economy, lower maintenance costs |
น้ำมันและก๊าซ | พลังงาน | Enhanced durability in harsh environments, reduced operational costs |
Industrial Machinery | การผลิต | Improved process efficiency, reduced downtime, enhanced safety |
Specifications, Sizes, Grades, and Standards
When designing or selecting components for gas turbine atomizing air systems, adhering to industry standards and specifications is crucial. Below is a detailed table highlighting the common specifications, sizes, grades, and standards applicable to these systems.
ส่วนประกอบ | มาตรฐาน | เกรด | ช่วงขนาด |
---|---|---|---|
Atomizing Air Nozzles | ASTM B637 | Inconel 718 | 0.5mm to 5mm orifice sizes |
Fuel Injectors | ASTM A213 | Stainless Steel 316L | 1mm to 10mm injector diameters |
Control Valves | ASTM B575 | Hastelloy C276 | 10mm to 100mm valve sizes |
Heat Exchangers | ASME BPVC Section VIII | Inconel 625 | Custom sizes based on application |
Air Compressors | ASTM B348 | Titanium Grade 5 | Various sizes depending on turbine model |
Suppliers and Pricing Details
Choosing the right supplier for components in gas turbine atomizing air systems is vital for ensuring quality and performance. Here’s a table listing some top suppliers, their locations, and indicative pricing.
ซัพพลายเออร์ | ที่ตั้ง | ส่วนประกอบ | Indicative Price Range |
---|---|---|---|
PCC Structurals | สหรัฐอเมริกา | Inconel 718 Atomizing Air Nozzles | $150 – $500 per unit |
ATI Specialty Materials | สหรัฐอเมริกา | Hastelloy X Control Valves | $200 – $700 per unit |
Carpenter Technology | สหรัฐอเมริกา | Stellite 6 Fuel Injectors | $100 – $400 per unit |
Sandvik Materials Technology | สวีเดน | Incoloy 800H Heat Exchangers | $1,000 – $5,000 per unit |
VSMPO-AVISMA | Russia | Titanium Alloy Air Compressors | $2,000 – $10,000 per unit |
Comparing Pros and Cons: Atomizing Air System Components
When evaluating the components of gas turbine atomizing air systems, it’s essential to weigh the pros and cons of different materials and designs. Here’s a comparison table to help with decision-making.
ส่วนประกอบ | Material | ข้อได้เปรียบ | ข้อเสีย |
---|---|---|---|
Atomizing Air Nozzles | Inconel 718 | High strength, corrosion-resistant | Expensive, complex manufacturing |
Fuel Injectors | Stainless Steel 316L | Durable, cost-effective | Limited high-temperature performance |
Control Valves | Hastelloy C276 | Excellent corrosion resistance, high strength | High cost, availability issues |
Heat Exchangers | Inconel 625 | Withstands extreme temperatures, oxidation-resistant | Heavy, costly |
Air Compressors | Titanium Grade 5 | Lightweight, strong, corrosion-resistant | Difficult to machine, high cost |
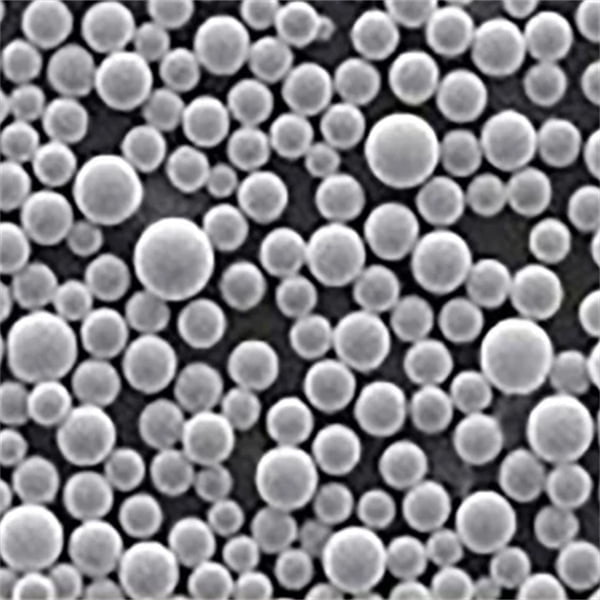
คำถามพบบ่อย
Q1: What is the primary function of an atomizing air system in a gas turbine?
A: The primary function of the atomizing air system is to break down the fuel into fine droplets before it enters the combustion chamber. This process, known as atomization, ensures a more efficient and complete combustion of the fuel, leading to improved turbine performance and reduced emissions.
Q2: Why are nickel-based superalloys commonly used in atomizing air systems?
A: Nickel-based superalloys, such as Inconel 718 and Hastelloy X, are widely used in atomizing air systems because of their excellent resistance to high temperatures, corrosion, and oxidation. These properties make them ideal for components that must endure the extreme conditions inside a gas turbine.
Q3: How does the atomizing air system affect turbine emissions?
A: By ensuring that fuel is finely atomized and mixes thoroughly with air, the atomizing air system helps achieve a more complete combustion. This reduces the amount of unburned hydrocarbons and other pollutants released into the atmosphere, thereby lowering emissions.
Q4: Can the atomizing air system improve fuel efficiency in gas turbines?
A: Yes, a properly functioning atomizing air system can significantly improve fuel efficiency. By ensuring that fuel burns more completely, the system maximizes the energy extracted from each unit of fuel, thereby reducing overall fuel consumption.
Q5: What are the common maintenance challenges with atomizing air systems?
A: Maintenance challenges often involve dealing with wear and tear due to high temperatures and pressures, as well as ensuring that components remain free of soot and other combustion by-products. Regular inspection and cleaning are crucial to maintaining system performance.
บทสรุป
The gas turbine atomizing air system is a critical component in ensuring the efficiency and performance of gas turbines. By understanding its composition, characteristics, advantages, and the specific metal powders used in its construction, operators and engineers can make informed decisions to optimize turbine performance. Whether it’s improving fuel efficiency, reducing emissions, or extending the lifespan of turbine components, the atomizing air system plays a pivotal role in modern gas turbine operations. By leveraging advanced materials and precision engineering, these systems continue to push the boundaries of what gas turbines can achieve.
About 3DP mETAL
Product Category
ติดต่อเรา
มีคำถามอะไรไหม? ส่งข้อความมาเดี๋ยวนี้! หลังจากที่ได้รับข้อความแล้ว เราจะประมวลผลคำขอของคุณพร้อมทีมงานทั้งหมด