Imagine a metal so finely ground, it transforms from a familiar, solid chunk into a dust-like substance with unique properties. This is the world of high purity iron powder, a versatile material that plays a vital role in various industries. But what exactly is it, and why is it so special? Buckle up, because we’re diving deep into the fascinating realm of microscopic iron particles!
Chemical Composition and Properties
High purity iron powder, as the name suggests, boasts an iron (Fe) content exceeding 98%. However, the magic lies not just in its main component, but also in the minimal presence of impurities. These impurities, typically elements like oxygen, carbon, and sulfur, can significantly affect the powder’s properties. By minimizing their presence, manufacturers create a highly reactive and functional material.
Key Properties of High Purity Iron Powder:
- High Surface Area: Due to its fine particle size, high purity iron powder possesses a significantly larger surface area compared to bulk iron. This translates to increased reactivity and enhanced performance in various applications.
- Good Conductivity: The high purity of the iron allows for excellent electrical and thermal conductivity, making it valuable in applications like electromagnetic interference (EMI) shielding.
- Magnetic Properties: The iron particles exhibit strong magnetic properties, making the powder ideal for use in magnets and magnetic recording media.
- Sinterability: High purity iron powder readily bonds together when heated under pressure, a process called sintering. This property makes it perfect for creating shaped metal components.
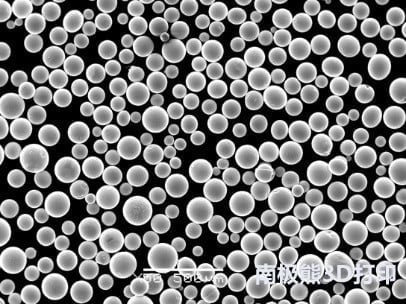
Composition Variations: A Spectrum of Options
While the core element remains iron, high purity iron powder can be further categorized based on its production method and resulting properties. Here are some prominent types to consider:
- Hydrogen Reduced Iron Powder: This type is produced by reducing iron oxide with hydrogen gas. It offers high purity (often exceeding 99.5%) and excellent flowability, making it ideal for applications like powder metallurgy and brazing.
- Electrolytic Iron Powder: This variety is electroplated from iron salts, resulting in a very pure and fine powder (particle size less than 10 microns). Its high surface area makes it perfect for catalysts and pyrotechnics.
- Atomized Iron Powder: Produced by rapidly cooling molten iron in a gas stream, atomized iron powder offers a wider range of particle sizes and good flowability. It’s commonly used in friction components and metal injection molding (MIM).
- Carbonyl Iron Powder: This unique type is produced by decomposing iron pentacarbonyl gas. It boasts high purity, spherical particle shape, and excellent magnetic properties, making it ideal for soft magnetic applications like transformers and inductors.
Applications of High Purity Iron Powder
High purity iron powder isn’t just a novelty; it’s a workhorse material with a diverse range of applications across various industries. Let’s explore some of its most prominent uses:
- ธาตุผงโลหะ: Iron powder forms the backbone of powder metallurgy, a process where metal parts are shaped from compressed powder and then sintered. This technique allows for the creation of complex shapes with high precision and minimal material waste. High purity iron powder, with its excellent sintering characteristics, is a key player in this field.
- Friction Components: Iron powder mixed with lubricants finds extensive use in automotive parts like brake pads, clutches, and engine components. The high surface area of the powder enhances friction properties, leading to smoother operation and improved wear resistance.
- Magnetic Applications: From soft magnetic components like transformers and inductors to permanent magnets used in motors and speakers, high purity iron powder plays a crucial role. Its tailorable magnetic properties make it a versatile material for various magnetic needs.
- Chemical Reactions: Due to its high surface area and reactivity, high purity iron powder is used as a catalyst in various chemical reactions. It can also be employed for deoxidation and pyrotechnic applications.
- Electronic Applications: The conductivity and magnetic properties of high purity iron powder make it valuable in EMI shielding materials and electromagnetic core materials used in transformers and inductors.
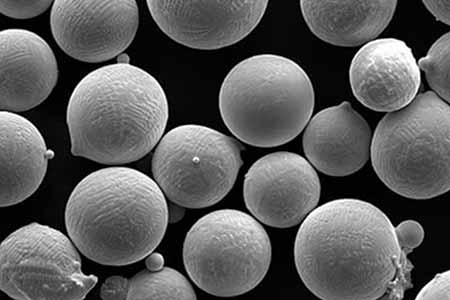
คำถามที่พบบ่อย
Q: What are some specific models of high purity iron powder available?
A: Due to the vast range of customization possibilities, high purity iron powder manufacturers often categorize their products based on key characteristics like production method, particle size distribution, and apparent density. Here are some examples from prominent suppliers to give you an idea:
- Höganäs AB:
- Höganäs Atomized Iron Powder (A Series): This series offers a range of atomized iron powders with varying particle sizes (10-100 microns) and apparent densities, suitable for powder metallurgy, friction components, and EMI shielding applications.
- Höganäs Water Atomized Iron Powder (D Series): This series features coarser water-atomized iron powders (typically over 100 microns) with good flowability, ideal for applications like brazing and metal injection molding (MIM).
- AMETEK Inc.:
- ** carbonyl iron powder (CQ grade):** This carbonyl iron powder boasts high purity (over 99.5%) and a spherical particle shape, making it perfect for soft magnetic applications like transformers and inductors.
- Electrolytic Iron Powder (EC grade): This electrolytic iron powder offers exceptional purity (over 99.9%) and a very fine particle size (less than 10 microns), ideal for use as a catalyst and in pyrotechnic applications.
- BASF SE:
- Cataclyst 34: This high purity iron powder is specifically designed for use as a catalyst in various chemical reactions.
- Pyrotek 100: This iron powder is tailored for pyrotechnic applications, offering the desired reactivity and burning characteristics.
Q: How is high purity iron powder stored and handled?
A: Due to its susceptibility to oxidation, proper storage and handling are crucial for high purity iron powder. Here are some key points to consider:
- Storage: The powder should be stored in a cool, dry, and inert atmosphere to minimize oxidation. Sealed containers with moisture-absorbing desiccants are ideal.
- Handling: Minimize exposure to air and moisture during handling. Utilize proper ventilation and dust collection systems to prevent inhalation risks.
Q: Are there any safety considerations when working with high purity iron powder?
A: Yes, there are some safety precautions to take when handling high purity iron powder:
- Inhalation Risks: Fine iron powder can be irritating to the lungs. Wear appropriate respiratory protection, such as a dust mask, to prevent inhalation.
- Fire Hazards: Iron powder can be combustible in a fine, dispersed state. Avoid ignition sources and implement proper grounding procedures to minimize explosion risks.
- Skin and Eye Irritation: Iron powder may cause skin and eye irritation. Wear gloves, safety glasses, and protective clothing when handling the powder.
Q: What is the future outlook for high purity iron powder?
A: The future of high purity iron powder appears bright. Here are some trends to watch:
- Growing Demand in Additive Manufacturing: With the increasing adoption of additive manufacturing techniques like metal 3D printing, the demand for high purity iron powders specifically tailored for these processes is expected to rise.
- Development of New Applications: Research and development efforts are continually exploring new applications for high purity iron powder, potentially leading to breakthroughs in areas like energy storage and environmental remediation.
- Focus on Sustainability: Manufacturers are likely to focus on developing sustainable production methods for high purity iron powder, minimizing environmental impact and resource consumption.
By understanding the properties, applications, and limitations of high purity iron powder, you can leverage this versatile material to create innovative solutions across various industries. As technology evolves and new applications emerge, high purity iron powder is poised to play an even more significant role in shaping the future.
About 3DP mETAL
Product Category
ติดต่อเรา
มีคำถามอะไรไหม? ส่งข้อความมาเดี๋ยวนี้! หลังจากที่ได้รับข้อความแล้ว เราจะประมวลผลคำขอของคุณพร้อมทีมงานทั้งหมด