Unleashing the Potential of Complex Components with High-Performance Metal Powders
Imagine building intricate, high-strength components that can withstand extreme environments. This is the reality with Inconel 625 powder for Hot Isostatic Pressing (HIP). This powerhouse combination offers a unique solution for demanding applications in aerospace, energy, and beyond. But what exactly makes Inconel 625 powder so special for HIP, and what are the specific metal powder options available? Buckle up, because we’re diving deep into this fascinating world of advanced materials!
Overview: Inconel 625 and the Power of HIP
Inconel 625 is a nickel-chromium-based superalloy renowned for its exceptional strength, corrosion resistance, and high-temperature performance. However, traditional fabrication methods like forging can be limiting for complex geometries. Enter Hot Isostatic Pressing (HIP). This process utilizes high pressure and temperature to eliminate internal voids and create near-net-shape components from metal powders. Combining Inconel 625 powder with HIP unlocks a new level of design freedom and material performance.
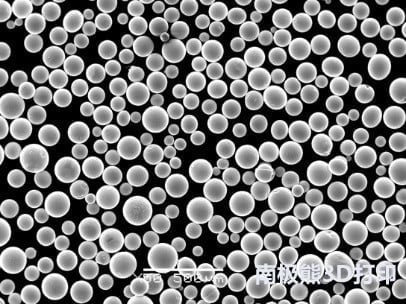
Metal Powder Options for Inconel 625 HIP
The choice of Inconel 625 powder significantly impacts the final component’s properties. Here’s a breakdown of some prominent options:
Type | องค์ประกอบ | คุณสมบัติ | คำอธิบาย |
---|---|---|---|
Atomized | Ni-Cr-Mo-Nb (Base composition) | Excellent strength, high-temperature capability, good corrosion resistance | This versatile powder offers a balanced mix of properties and is widely used for HIP applications. |
AM (Additive Manufacturing) Optimized | Tailored Ni-Cr-Mo-Nb composition | Improved flowability, tighter size distribution | Powders specifically designed for additive manufacturing techniques like laser melting can be used with HIP for near-net-shape components. |
CW (Consolidated Wire) | Recrystallized Inconel 625 wire | High density, good mechanical properties | This option offers a more uniform microstructure and predictable performance compared to atomized powders. |
Fفره (Carbonyl) | High purity Ni-Cr-Mo-Nb | Excellent corrosion resistance, good for high-temperature applications | This ultra-clean powder is ideal for components requiring exceptional purity, like those used in chemical processing. |
Plasma Atomized | Rapidly solidified Inconel 625 | Fine microstructure, improved creep resistance | This process creates fine, spherical powders with enhanced strength at elevated temperatures. |
Water Atomized | Cost-effective Ni-Cr-Mo-Nb | Good balance of properties, lower cost | A budget-friendly option for less demanding applications where cost is a major concern. |
Lanthanum Modified | Ni-Cr-Mo-Nb with Lanthanum addition | Improved grain boundary strength, high-temperature oxidation resistance | The addition of Lanthanum enhances grain boundary strength and oxidation resistance, ideal for turbine components. |
Yttrium Modified | Ni-Cr-Mo-Nb with Yttrium addition | Improved creep resistance, high-temperature stability | Yttrium improves creep resistance, making this powder suitable for long-term service at elevated temperatures. |
Boron Modified | Ni-Cr-Mo-Nb with Boron addition | Enhanced wear resistance, improved brazing characteristics | Boron addition provides superior wear resistance, beneficial for components exposed to friction and wear. |
Nickel-Rich | Increased Nickel content | Enhanced corrosion resistance, improved high-temperature strength | Powders with a higher nickel content excel in highly corrosive environments and applications requiring exceptional strength at elevated temperatures. |
Applications of Inconel 625 Powder for HIP
The unique combination of Inconel 625’s properties and the design freedom offered by HIP unlocks a vast array of applications. Here are some prominent examples:
- การบินและอวกาศ: Turbine blades, combustor liners, landing gear components, high-pressure vessels – all benefit from Inconel 625’s strength, temperature resistance, and light weight.
- การดำเนินการทางเคมี: Reaction vessels, heat exchangers, valves – Inconel 625 excels in highly corrosive environments.
- Oil and Gas: Downhole wellhead components, drilling tools – the material’s strength and corrosion resistance are crucial for harsh downhole conditions.
- Biomedical: Prosthetic implants – Inconel 625 offers excellent biocompatibility and durability for demanding medical applications.
Advantages of Inconel 625 Powder for HIP
- Design Freedom: HIP allows for the creation of complex geometries previously limited by traditional fabrication methods.
- Improved Material Properties: HIP eliminates internal voids, leading to denser, stronger components with superior mechanical properties.
- Reduced Waste: Near-net-shape manufacturing minimizes material waste compared to traditional methods.
- Lightweighting: The high strength-to-weight ratio of Inconel 625 enables the creation of lighter components, crucial for aerospace and other weight-sensitive applications.
- Enhanced Performance: Tailored powder compositions can optimize properties like creep resistance, oxidation resistance, and wear resistance for specific applications.
Disadvantages of Inconel 625 Powder for HIP
- Cost: Inconel 625 powder and the HIP process can be expensive compared to traditional methods.
- Process Complexity: HIP requires specialized equipment and expertise, adding complexity to the manufacturing process.
- Limited Size: Current HIP technology may limit the size of components that can be effectively processed.
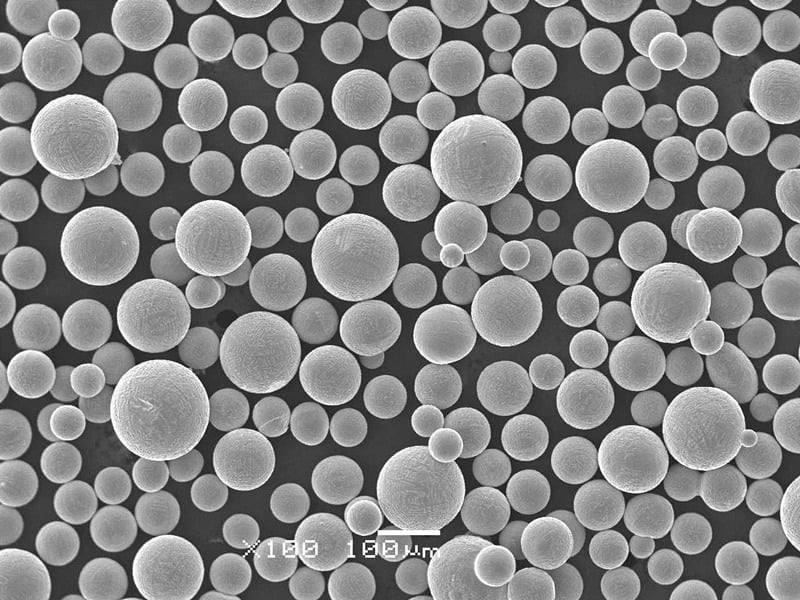
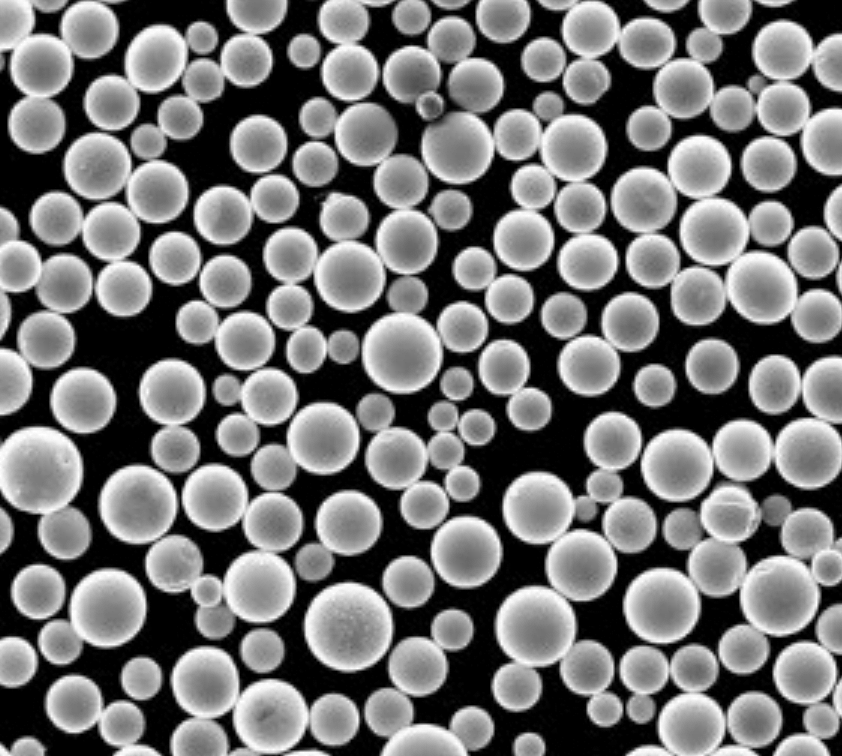
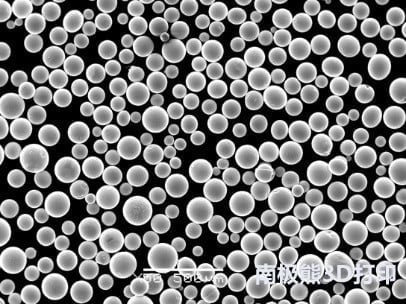
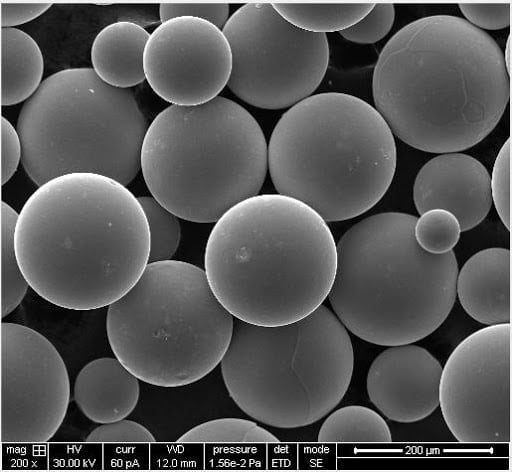
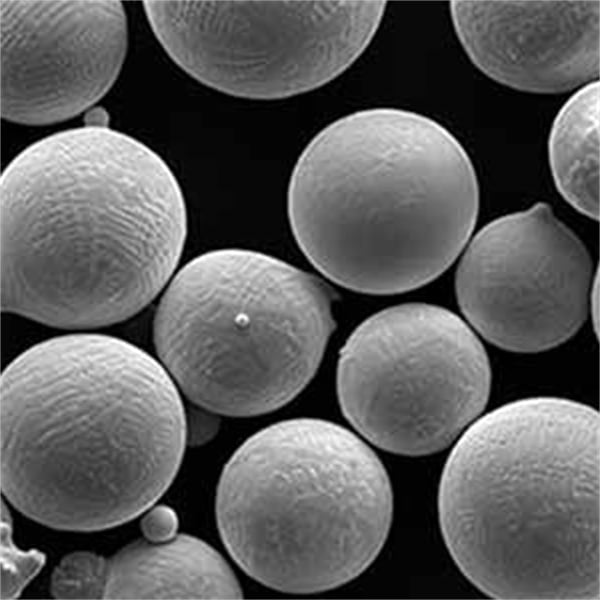
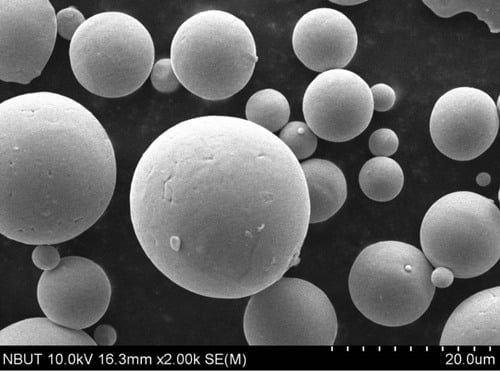
Material Property Comparison of Inconel 625 Powder Options
When choosing an Inconel 625 powder for HIP, it’s crucial to consider the desired final component properties. Here’s a table summarizing key property variations:
ทรัพย์สิน | Atomized | AM Optimized | CW | Carbonyl | Plasma Atomized | Water Atomized | Lanthanum Modified | Yttrium Modified | Boron Modified | Nickel-Rich |
---|---|---|---|---|---|---|---|---|---|---|
Density (g/cm³) | 8.3 – 8.4 | 8.3 – 8.4 | High close to) 8.4 | High close to) 8.4 | 8.3 – 8.4 | 8.2 – 8.3 | 8.3 – 8.4 | 8.3 – 8.4 | 8.3 – 8.4 | 8.4 – 8.5 |
Tensile Strength (MPa) | 900 – 1000 | 850 – 950 | 950 – 1050 | 920 – 1020 | 980 – 1080 | 880 – 980 | 920 – 1020 | 900 – 1000 | 930 – 1030 | 950 – 1050 |
Yield Strength (MPa) | 450 – 550 | 420 – 520 | 500 – 600 | 480 – 580 | 530 – 630 | 430 – 530 | 480 – 580 | 450 – 550 | 480 – 580 | 500 – 600 |
Elongation (%) | 30 – 50 | 25 – 45 | 40 – 60 | 35 – 55 | 20 – 40 | 35 – 55 | 30 – 50 | 25 – 45 | 20 – 40 | 25 – 45 |
Creep Resistance | ดี | ปานกลาง | ดี | ยอดเยี่ยม | ยอดเยี่ยม | ดี | Improved | ยอดเยี่ยม | Improved | ดี |
**ตามข้างล่าง** This table provides a general comparison, and specific properties can vary depending on the manufacturer and processing parameters.
Suppliers of Inconel 625 Powder for HIP
Several reputable suppliers offer Inconel 625 powder for HIP applications. Here are some prominent examples:
- Carpenter Additive Powder Products (https://www.carpenteradditive.com/)
- AP Powder Company (https://www.allpowderpaints.com/)
- Höganäs (https://www.hoganas.com/en/)
- Aubert & Duval (https://www.aubertduval.com/about-aubert-duval/)
- Special Metals Corporation (https://www.specialmetals.com/)
Pricing of Inconel 625 Powder for HIP
The pricing of Inconel 625 powder for HIP varies depending on several factors, including:
- Powder type: Premium powders like carbonyl or plasma atomized will typically be more expensive than standard atomized powders.
- Quantity: Bulk purchases often receive discounted pricing compared to smaller orders.
- Supplier: Pricing can vary between suppliers based on their production costs and market positioning.
It’s important to contact potential suppliers directly for current pricing information.
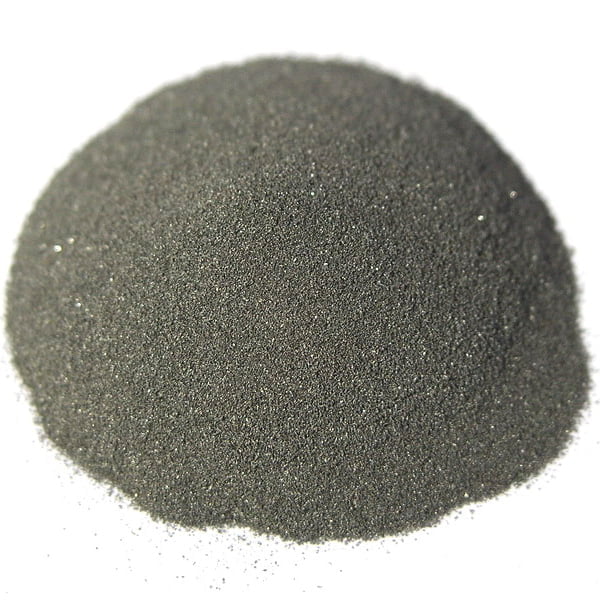
คำถามพบบ่อย
Q: What are the advantages of using HIP with Inconel 625 powder?
A: The advantages of using HIP with Inconel 625 powder include:
- Design Freedom: HIP allows for the creation of complex geometries that are impossible or highly challenging with traditional fabrication methods like casting or machining. Imagine intricate internal channels or lattice structures – HIP with Inconel 625 powder can bring these designs to life.
- Improved Material Properties: The HIP process eliminates internal voids and porosity within the powder particles, resulting in a denser and more uniform microstructure. This translates to superior mechanical properties like tensile strength, yield strength, and creep resistance compared to conventionally manufactured Inconel 625 components.
- Reduced Waste: HIP with Inconel 625 powder enables near-net-shape manufacturing. This minimizes material waste compared to traditional methods that often involve significant machining to achieve the desired final shape. In a world increasingly focused on sustainability, this advantage is becoming increasingly important.
- Lightweighting: Inconel 625 is already known for its exceptional strength-to-weight ratio. HIP further enhances this advantage by creating components with a denser microstructure. This makes Inconel 625 powder with HIP ideal for applications where weight reduction is critical, such as aerospace and high-performance automotive components.
Q: What are the disadvantages of using HIP with Inconel 625 powder?
A: While powerful, there are some limitations to consider:
- Cost: Both Inconel 625 powder and the HIP process itself can be expensive compared to traditional fabrication methods. The cost of the powder itself is driven by factors like the specific composition and production technique. Additionally, HIP equipment and expertise add to the overall manufacturing cost.
- Process Complexity: HIP is a complex process with specific parameters for pressure, temperature, and hold time. Operating a HIP unit requires specialized training and expertise, which can add complexity to the manufacturing process compared to simpler techniques like welding or machining.
- Limited Size: Current HIP technology may limit the size of components that can be effectively processed. While the technology is constantly evolving, there’s a practical limit on the size of vessels used for HIP, which can restrict the size of components that can be manufactured using this method.
Q: How does the choice of Inconel 625 powder impact the final component properties?
A: The choice of Inconel 625 powder significantly affects the final component’s properties. Here’s a breakdown of some key considerations:
- Powder type: Standard atomized powder offers a balanced mix of properties, while premium options like carbonyl or plasma atomized powders can provide enhanced characteristics like creep resistance or corrosion resistance.
- Compositional variations: Some powders incorporate minor element additions like Lanthanum or Yttrium to improve specific properties like grain boundary strength or high-temperature performance.
It’s crucial to carefully consider the desired application and its specific demands when selecting an Inconel 625 powder for HIP. Consulting with a material supplier or a qualified engineer can help you choose the most suitable powder for your project.
Q: Where can I find more information about Inconel 625 powder and HIP?
A: Several resources can provide additional information about Inconel 625 powder and HIP:
- Material supplier websites: Many reputable suppliers of Inconel 625 powder provide technical datasheets and application guides on their websites. These resources offer detailed information about the specific properties and recommended uses of their powders.
- Industry associations: Organizations like the American Society for Materials Testing (ASTM) and the Special Metals Corporation (SMC) publish technical standards and resources related to metal powders and HIP.
- Online technical publications: Several online publications and websites cater to the additive manufacturing and metalworking industries. These resources often feature articles and discussions on advanced materials like Inconel 625 powder and HIP applications.
By exploring these resources, you can gain a deeper understanding of this powerful combination and its potential for your specific needs.
บทสรุป
Inconel 625 powder for Hot Isostatic Pressing (HIP) represents a revolutionary approach to manufacturing complex, high-performance components. This technology unlocks a new world of design possibilities while offering exceptional material properties. While cost and process complexity are considerations, the advantages of HIP with Inconel 625 powder are undeniable for various demanding applications. As the technology continues to mature and become more cost-effective, we can expect to see even wider adoption of this innovative manufacturing method.
About 3DP mETAL
Product Category
ติดต่อเรา
มีคำถามอะไรไหม? ส่งข้อความมาเดี๋ยวนี้! หลังจากที่ได้รับข้อความแล้ว เราจะประมวลผลคำขอของคุณพร้อมทีมงานทั้งหมด