ภาพรวม
Metal atomization systems are pivotal in the production of metal powders, which are fundamental in various industries, including additive manufacturing, aerospace, automotive, and more. These systems convert molten metal into fine powder particles through different atomization techniques. This comprehensive guide will delve into the intricacies of metal atomization systems, exploring their types, applications, advantages, disadvantages, and specific models available in the market.
Introduction to Metal Atomization Systems
Metal atomization is a process where molten metal is disintegrated into fine droplets that solidify into powder particles. This technique is essential in manufacturing metal powders for various applications, from 3D printing to metallurgy. The quality and characteristics of the metal powders depend significantly on the atomization method used.
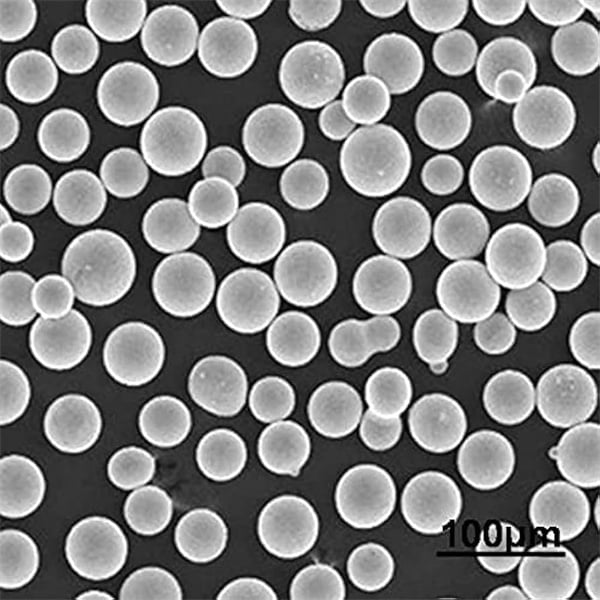
Types of Metal Atomization Systems
การแปรสภาพเป็นอะตอมของแก๊ส
Gas atomization involves the use of high-pressure gas jets to break up a stream of molten metal into fine droplets. The type of gas used (often nitrogen or argon) and the gas-to-metal ratio significantly influence the properties of the resulting powders.
การทำให้ละอองน้ำกลายเป็นไอ
Water atomization uses high-pressure water jets instead of gas. This method is typically used for ferrous metals and results in powders with irregular shapes due to the rapid cooling and solidification process.
Centrifugal Atomization
Centrifugal atomization involves spinning molten metal at high speeds, using centrifugal force to propel the droplets outward. This method is often used for producing spherical powders and is suitable for both ferrous and non-ferrous metals.
Vacuum Atomization
Vacuum atomization occurs in a controlled environment to prevent contamination and oxidation. This technique is used for high-purity metal powders, often in specialized applications where maintaining the integrity of the powder is crucial.
Applications of Metal Atomization Systems
Metal powders produced through atomization have diverse applications across multiple industries:
อุตสาหกรรม | แอปพลิเคชัน |
---|---|
การผลิตแบบเติมเนื้อ | 3D printing of complex metal parts |
อวกาศ | High-performance components |
ยานยนต์ | Engine parts, transmission components |
แพทย์ | Implants, prosthetics |
เครื่องใช้ไฟฟ้า | Conductive inks, solder pastes |
Metallurgy | Powder metallurgy, alloy production |
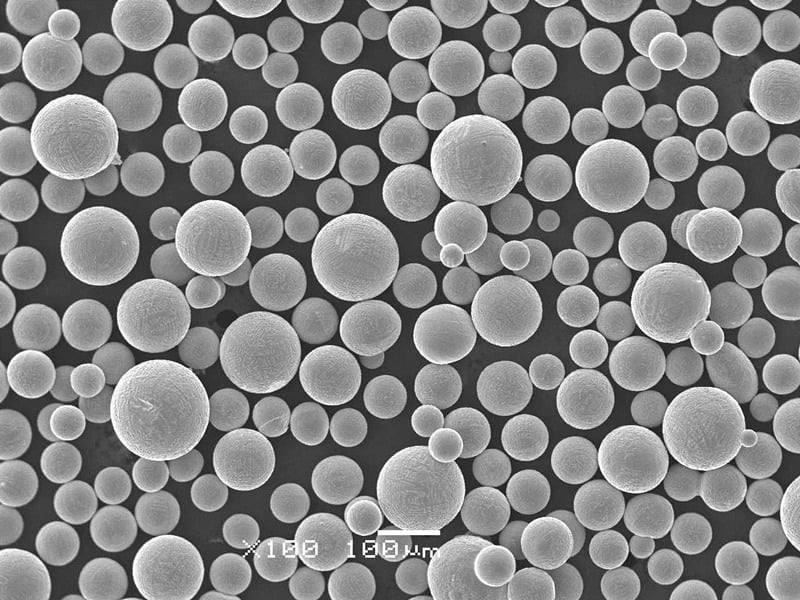
Specific Metal Powder Models
1. 316L Stainless Steel Powder
Description: Known for its corrosion resistance and excellent mechanical properties, 316L is widely used in marine and medical applications.
Characteristics: Spherical particles, low carbon content.
Applications: 3D printing, biomedical implants, marine components.
2. Inconel 718 Powder
Description: A nickel-chromium alloy powder known for its high strength and resistance to heat and corrosion.
Characteristics: Spherical particles, high tensile strength.
Applications: Aerospace components, high-temperature applications.
3. Titanium Ti-6Al-4V Powder
Description: A high-strength titanium alloy powder with excellent biocompatibility.
Characteristics: Spherical particles, lightweight, high strength.
Applications: Medical implants, aerospace components, automotive parts.
4. AlSi10Mg Powder
Description: An aluminum alloy powder with good thermal properties and low density.
Characteristics: Spherical particles, excellent casting properties.
Applications: Automotive parts, lightweight structures, 3D printing.
5. Copper Cu Powder
Description: Pure copper powder known for its excellent electrical and thermal conductivity.
Characteristics: Spherical particles, high purity.
Applications: Electrical components, conductive inks, heat sinks.
6. Tool Steel H13 Powder
Description: A versatile tool steel powder with high hardness and wear resistance.
Characteristics: Irregular particles, high toughness.
Applications: Molds, dies, high-stress tools.
7. Cobalt-Chrome CoCr Powder
Description: A biocompatible alloy powder with high wear resistance.
Characteristics: Spherical particles, corrosion-resistant.
Applications: Medical implants, dental prosthetics, aerospace components.
8. Stainless Steel 17-4 PH Powder
Description: A precipitation-hardening stainless steel powder with high strength and corrosion resistance.
Characteristics: Spherical particles, excellent mechanical properties.
Applications: Aerospace components, industrial parts, 3D printing.
9. Nickel Ni Powder
Description: Pure nickel powder with high corrosion resistance and electrical conductivity.
Characteristics: Spherical particles, high purity.
Applications: Batteries, catalysts, electronics.
10. Bronze CuSn10 Powder
Description: An alloy powder of copper and tin known for its excellent casting properties and corrosion resistance.
Characteristics: Spherical particles, good mechanical properties.
Applications: Bearings, bushings, sculptures.
Specifications, Sizes, Grades, Standards
Metal Powder Model | Particle Size Range (µm) | เกรด | มาตรฐาน |
---|---|---|---|
316L Stainless Steel | 15-45, 45-90 | Fine, Medium | ASTM B243, ISO 4499-4 |
Inconel 718 | 15-45, 45-106 | Fine, Medium | ASTM B838, AMS 5662 |
Ti-6Al-4V | 20-53, 45-90 | Fine, Medium | ASTM F2924, ISO 5832-3 |
AlSi10Mg | 20-63, 45-90 | กลางๆ | ASTM B928, ISO 3522 |
Copper Cu | 10-45, 45-75 | Fine, Medium | ASTM B212, ISO 4289 |
Tool Steel H13 | 20-63, 45-150 | Medium, Coarse | ASTM A681, ISO 4957 |
Cobalt-Chrome CoCr | 10-45, 45-90 | Fine, Medium | ASTM F75, ISO 5832-4 |
Stainless Steel 17-4 PH | 15-45, 45-106 | Fine, Medium | ASTM A693, ISO 4957 |
Nickel Ni | 10-45, 45-90 | Fine, Medium | ASTM B330, ISO 4501 |
Bronze CuSn10 | 20-63, 45-150 | Medium, Coarse | ASTM B505, ISO 3544 |
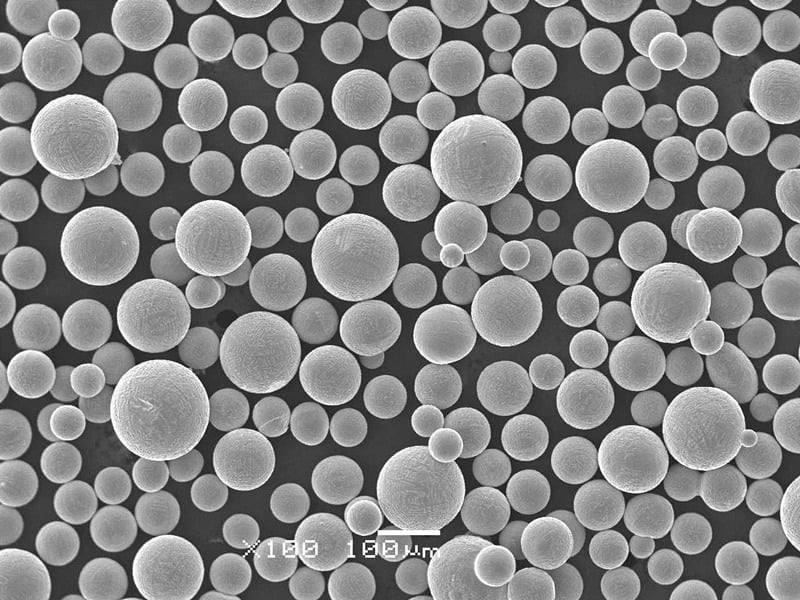
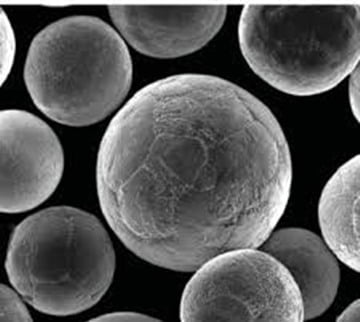
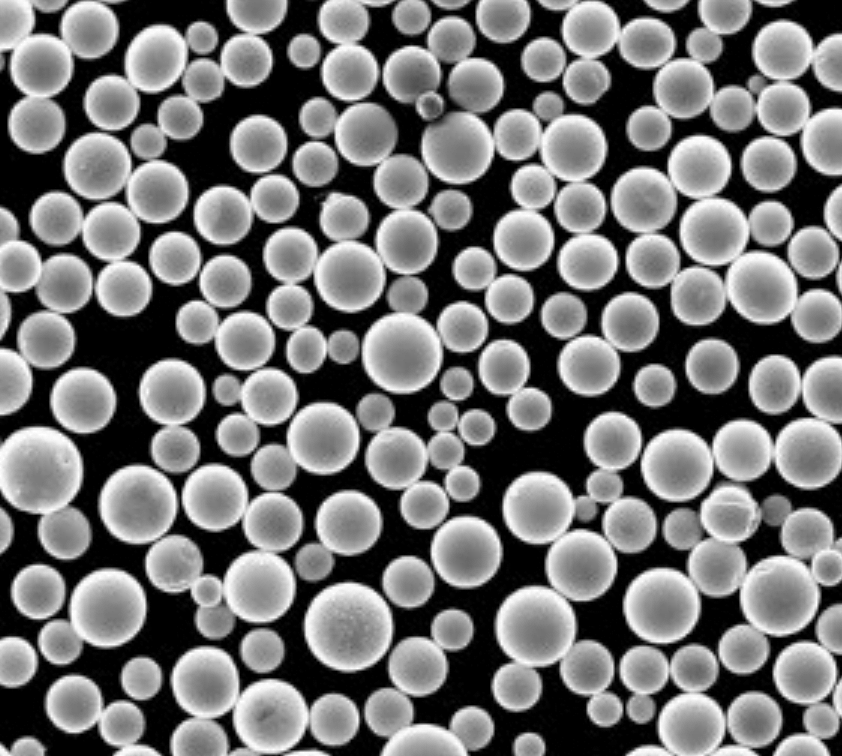
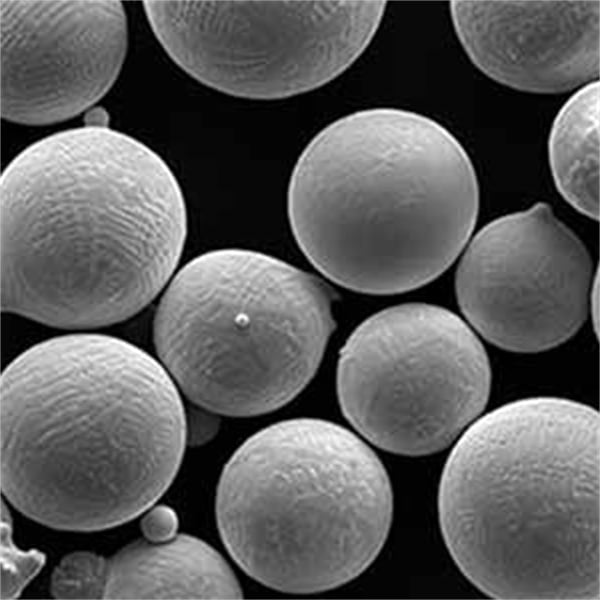
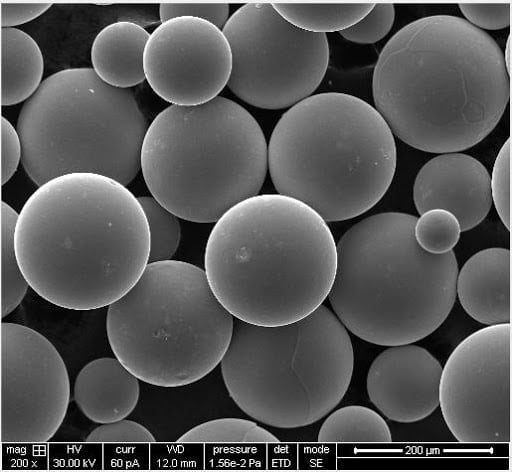
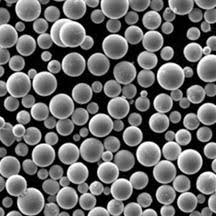
Suppliers and Pricing Details
ซัพพลายเออร์ | Metal Powder Models | Pricing (per kg) | Region |
---|---|---|---|
Carpenter Technology | 316L Stainless Steel, Ti-6Al-4V, Inconel 718 | $150 – $300 | North America |
Höganäs AB | AlSi10Mg, Copper Cu, Tool Steel H13 | $50 – $200 | Europe, Asia |
Sandvik Osprey | Stainless Steel 17-4 PH, Cobalt-Chrome CoCr | $100 – $250 | Global |
GKN Additive | Bronze CuSn10, Nickel Ni | $80 – $220 | North America, Europe |
AP&C (GE Additive) | Inconel 718, Ti-6Al-4V | $180 – $350 | Global |
Praxair Surface Technologies | Copper Cu, 316L Stainless Steel | $60 – $180 | North America |
เทคโนโลยี LPW | Tool Steel H13, AlSi10Mg | $70 – $190 | Europe, Asia |
Aubert & Duval | Cobalt-Chrome CoCr, Nickel Ni | $120 – $300 | ยุโรป |
Comparing Pros and Cons
316L Stainless Steel Powder
ข้อได้เปรียบ | ข้อเสีย |
---|---|
High corrosion resistance | Relatively high cost |
Excellent mechanical properties | Requires precise handling and storage |
Biocompatible | Lower strength compared to other alloys |
Inconel 718 Powder
ข้อได้เปรียบ | ข้อเสีย |
---|---|
High strength at elevated temperatures | Expensive compared to other powders |
Excellent corrosion and oxidation resistance | Difficult to machine |
Suitable for high-stress applications | Longer production times |
ผง Ti-6Al-4V
ข้อได้เปรียบ | ข้อเสีย |
---|---|
Lightweight and high strength | Expensive material |
Excellent biocompatibility | Difficult to weld and machine |
High fatigue resistance | Limited use at temperatures above 400°C |
ผง AlSi10Mg
ข้อได้เปรียบ | ข้อเสีย |
---|---|
Low density and good thermal conductivity | Lower strength compared to steel alloys |
Excellent casting properties | Can be prone to cracking |
Cost-effective | Limited high-temperature performance |
Copper Cu Powder
ข้อได้เปรียบ | ข้อเสีย |
---|---|
นำไฟฟ้าและความร้อนได้ดี | High cost for high-purity copper |
Easy to machine | Susceptible to oxidation |
ทนการกัดกร่อนได้ดี | Lower mechanical strength |
Tool Steel H13 Powder
ข้อได้เปรียบ | ข้อเสีย |
---|---|
High hardness and wear resistance | Requires heat treatment for full properties |
Good toughness | Expensive compared to carbon steels |
Versatile applications | Difficult to machine in hardened state |
Cobalt-Chrome CoCr Powder
ข้อได้เปรียบ | ข้อเสีย |
---|---|
High wear and corrosion resistance | Expensive material |
Excellent biocompatibility | Difficult to process |
ความแข็งแรงสูง | Limited ductility |
Stainless Steel 17-4 PH Powder
ข้อได้เปรียบ | ข้อเสีย |
---|---|
มีความแข็งแรงทนทาน | Expensive compared to regular stainless steels |
ทนการกัดกร่อนได้ดี | Requires precise heat treatment |
Easy to fabricate | Limited availability |
Nickel Ni Powder
ข้อได้เปรียบ | ข้อเสีย |
---|---|
High corrosion resistance | High cost for high-purity nickel |
Excellent electrical conductivity | Limited strength |
Versatile applications | Susceptible to sulphur contamination |
Bronze CuSn10 Powder
ข้อได้เปรียบ | ข้อเสีย |
---|---|
Good casting properties | Prone to brittleness |
ทนทานต่อการกัดกร่อนได้ดีเยี่ยม | Lower strength compared to steel |
Cost-effective | Limited high-temperature applications |
Advantages and Disadvantages of Metal Atomization Systems
Advantages of Metal Atomization Systems
- High Purity and Quality: Metal atomization produces powders with high purity and uniform particle size distribution, crucial for high-performance applications.
- Versatility: Suitable for a wide range of metals and alloys, allowing customization of powder properties for specific applications.
- Scalability: Can be scaled to produce small batches for research or large volumes for industrial applications.
- Customization: Ability to control particle size, shape, and distribution through different atomization techniques.
Disadvantages of Metal Atomization Systems
- High Cost: Initial setup and operational costs can be high, making it less accessible for smaller enterprises.
- Complexity: Requires precise control of parameters and conditions, necessitating skilled operators and sophisticated equipment.
- Energy-Intensive: Processes like gas and centrifugal atomization consume significant amounts of energy.
- Limited Material Types: Some metals and alloys are challenging to atomize due to their physical properties.
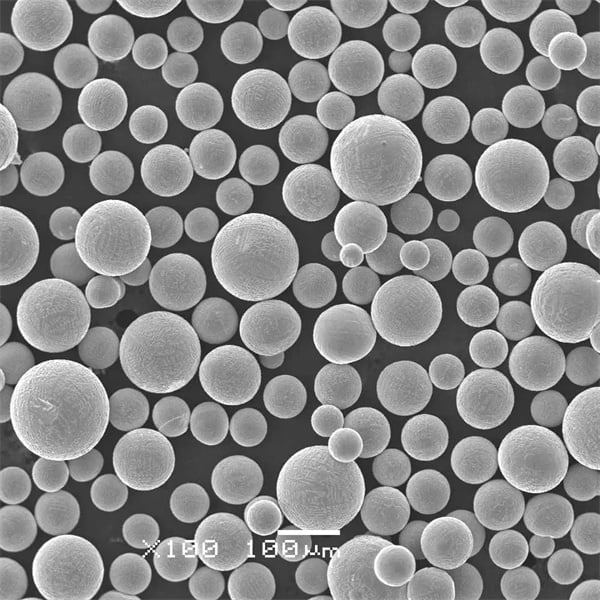
คำถามที่พบบ่อย
Question | Answer |
---|---|
What is metal atomization? | Metal atomization is the process of converting molten metal into fine powder particles using various techniques like gas, water, centrifugal, or vacuum atomization. |
Why are metal powders important in additive manufacturing? | Metal powders are essential in additive manufacturing because they allow for the precise creation of complex parts layer by layer, ensuring high-quality and consistent properties. |
Which metals can be atomized? | Almost any metal can be atomized, including steel, aluminum, titanium, copper, and nickel alloys, depending on the specific atomization method used. |
What are the key factors influencing the quality of metal powders? | Key factors include the atomization method, gas or water pressure, cooling rate, and the purity of the molten metal. |
Can metal atomization systems be used for recycling? | Yes, metal atomization can be used to recycle metal scrap into high-quality powders for reuse in various applications. |
How does the choice of atomization method affect the powder characteristics? | Different methods produce powders with varying particle shapes, sizes, and purity levels. For example, gas atomization tends to produce spherical particles, while water atomization results in irregular shapes. |
บทสรุป
Metal atomization systems are a cornerstone in the production of high-quality metal powders, crucial for numerous advanced manufacturing processes. By understanding the different types of atomization methods, their applications, and the specific models available, industries can make informed decisions to optimize their production and product quality. Despite the challenges, the advantages of metal atomization systems make them indispensable in modern manufacturing.
About 3DP mETAL
Product Category
ติดต่อเรา
มีคำถามอะไรไหม? ส่งข้อความมาเดี๋ยวนี้! หลังจากที่ได้รับข้อความแล้ว เราจะประมวลผลคำขอของคุณพร้อมทีมงานทั้งหมด