Imagine taking a solid bar of metal and, with a flick of a switch, turning it into a cloud of fine, versatile powder. That’s the magic behind metal powder production directly from bar stock. This innovative approach is revolutionizing the way we manufacture complex components, offering a treasure trove of benefits for engineers and designers alike.
But before we delve deeper, let’s address the elephant in the room: how exactly does this process work? Buckle up, because we’re about to embark on a fascinating journey into the world of metal atomization!
Transforming Solid into Powder
There are two primary methods for generating metal powder directly from bar stock:
- Atomization: This technique employs high-pressure forces to break down the bar stock into tiny particles. Imagine a high-powered water jet pummeling the metal, shattering it into a mist of microscopic fragments. Different atomization techniques exist, each with its own advantages:
- Gas Atomization: Inert gas, like nitrogen or argon, is used as the high-pressure medium. This method produces spherical powders with excellent flowability and packing density, making them ideal for additive manufacturing (3D printing) applications.
- Water Atomization: Here, water takes center stage as the atomizing force. This method is more cost-effective but results in less spherical, more irregular powder shapes. It’s often used for applications where precise particle morphology isn’ stainless steel, titanium, and certain nickel alloys.
- Rapid Solidification: This approach involves melting the bar stock using a high-energy source like a laser beam or electron beam. The molten metal is then rapidly quenched (cooled) using a variety of techniques, including gas or water atomization. This rapid cooling process results in unique microstructures with superior mechanical properties, making them ideal for high-performance applications in aerospace, defense, and medical sectors.
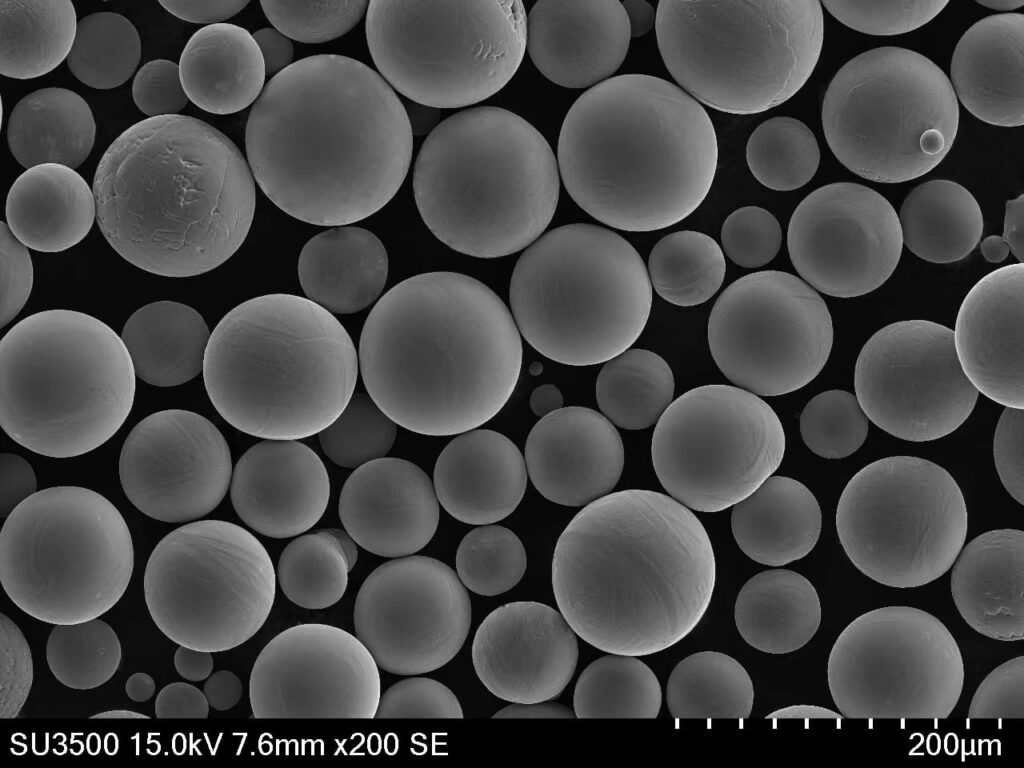
A Gallery of Metal Powders: Unveiling the Arsenal
Now, let’s explore the diverse range of metal powders you can generate directly from bar stock. Here are ten prominent examples, each boasting unique properties and applications:
- Stainless Steel Powders: These versatile powders offer excellent corrosion resistance and come in various grades, like 316L and 17-4PH. They are widely used in additive manufacturing, injection molding, and thermal spraying for applications ranging from medical implants to aerospace components.
- Titanium Powders: Renowned for their high strength-to-weight ratio and biocompatibility, titanium powders are a perfect fit for aerospace, medical, and dental applications. They are typically produced using gas atomization to achieve the spherical morphology desired for additive manufacturing.
- Nickel-based Alloy Powders: These high-performance powders offer exceptional resistance to high temperatures, corrosion, and wear. They cater to demanding applications in jet engines, power generation turbines, and other high-temperature environments. Inconel and Invar are popular examples of nickel-based alloy powders.
- Aluminum Powders: Lightweight and readily recyclable, aluminum powders are a cost-effective option for various applications. They are commonly used in additive manufacturing, metal injection molding (MIM), and pyrotechnics.
- Copper Powders: With their excellent electrical conductivity and thermal properties, copper powders find application in electrical components, heat sinks, and thermal management solutions. They can be produced using various atomization techniques, with water atomization being a popular choice for cost-sensitive applications.
- Cobalt Chrome Powders: A biocompatible blend of cobalt and chromium, these powders are widely used in the production of hip replacements, knee joints, and other orthopedic implants. Their high strength and wear resistance make them ideal for long-lasting prosthetics.
- Tool Steel Powders: Offering exceptional hardness and wear resistance, tool steel powders are used for creating cutting tools, dies, and molds. They are often produced using water atomization techniques due to their less stringent shape requirements compared to materials like titanium.
- Tungsten Powders: These incredibly dense powders boast the highest melting point of any metal element. They are used in a variety of applications, including filaments for incandescent lamps, electrodes for welding, and armor-piercing projectiles.
- Molybdenum Powders: Highly resistant to high temperatures and corrosion, molybdenum powders are used in filaments, crucibles for high-temperature applications, and electrical contacts.
- Precious Metal Powders: Gold, silver, and platinum powders find application in jewelry, electronics, and dentistry. They are typically produced using specialized atomization techniques to achieve the desired particle size and distribution.
the Potential of metal powder direct from bar stock
We’ve explored the fascinating world of metal powder production directly from bar stock, uncovering the techniques and a captivating array of materials. But the journey doesn’t end there. Now, let’s delve deeper into the properties, applications, and considerations that come with using these versatile powders.
Unveiling the Strengths: A Look at Properties
Metal powders generated from bar stock possess unique properties compared to their bulk counterparts. Here’s a breakdown of some key characteristics:
- Particle Size and Distribution: The size and distribution of the powder particles significantly impact the final product’s properties. Finer powders generally offer better surface finish and detail in additive manufacturing but might be more challenging to handle due to increased flowability. Conversely, larger particles can improve flow characteristics but might limit detail resolution in 3D printing applications.
- ความหนาแน่น: The density of the powder directly translates to the final product’s density. Techniques like gas atomization can achieve higher densities due to the creation of more spherical particles with minimal internal voids.
- การไหล: The ease with which the powder flows is crucial for various processes like additive manufacturing and metal injection molding. Powders with a more spherical morphology generally exhibit better flowability.
- Sinterability: This property refers to the powder’s ability to bond together during a high-temperature treatment process called sintering. Good sinterability is essential for achieving a strong and dense final product.
Material Tailoring: One of the significant advantages of using metal powders directly from bar stock is the ability to tailor the material properties. By selecting the specific bar stock composition and the atomization technique, manufacturers can fine-tune the powder characteristics for specific applications. For instance, rapid solidification techniques can create powders with finer grain structures, leading to improved mechanical properties like strength and ductility.
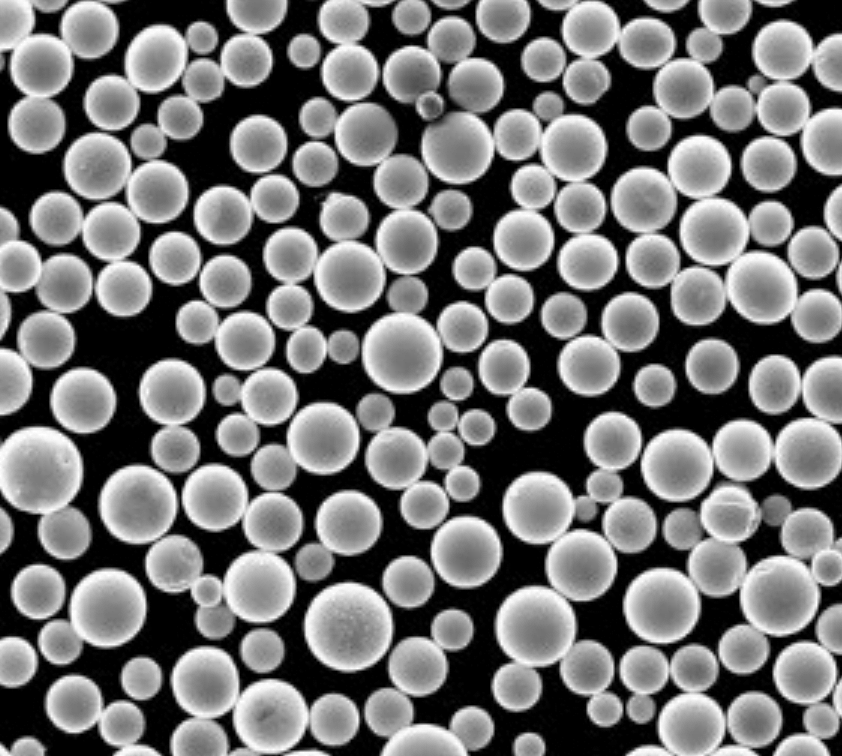
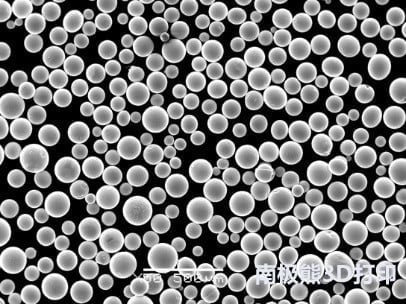
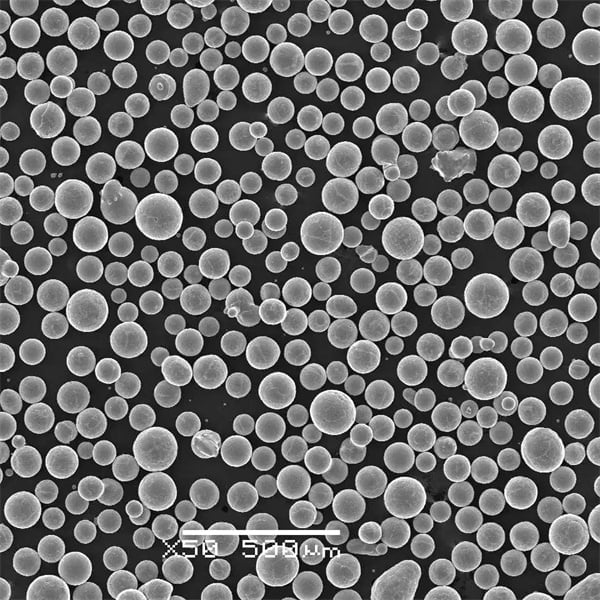
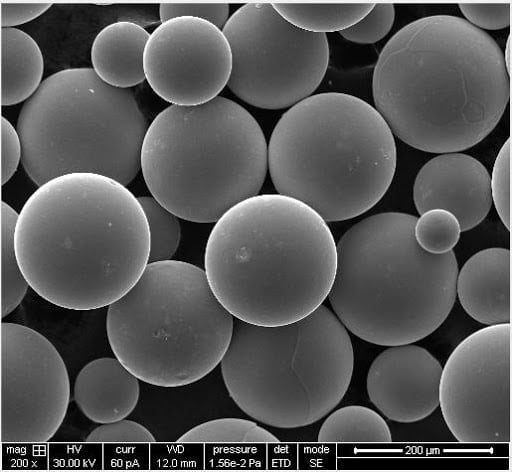
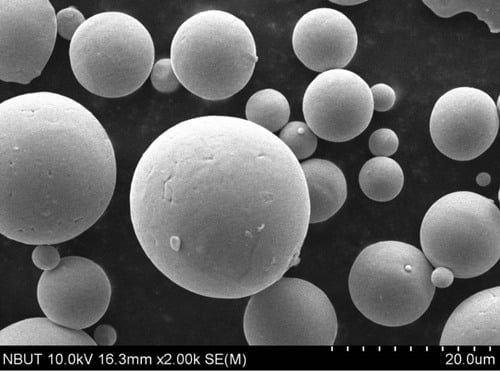
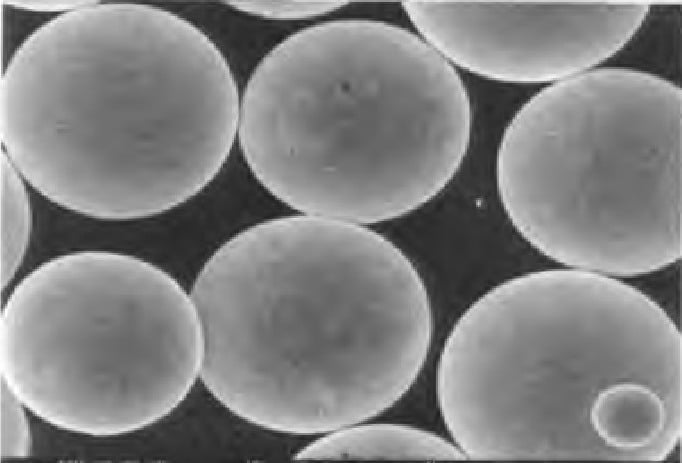
A World of Applications: Where Metal Powders Shine
Metal powders from bar stock are revolutionizing various industries with their unique properties and processing advantages. Here’s a glimpse into some of their prominent applications:
- Additive Manufacturing (3D Printing): Metal powders are the primary feedstock for metal 3D printing technologies. They enable the creation of complex, near-net-shape components with intricate geometries, previously impossible with traditional manufacturing techniques. From aerospace components to medical implants, 3D printing with metal powders is pushing the boundaries of design and innovation.
- Metal Injection Molding (MIM): This process combines the flexibility of injection molding with the strength and properties of metals. Metal powders are mixed with a binder to create a feedstock that can be injection molded into complex shapes. The binder is then removed through a debinding process, followed by sintering to achieve the final metallic component. MIM is ideal for producing high-volume, intricate metal parts for various applications, including automotive components, electronics, and medical devices.
- Thermal Spraying: Metal powders are used in thermal spraying processes to create wear-resistant coatings, improve corrosion resistance, and restore worn-out surfaces. The powder is fed into a high-temperature source like a plasma torch, melted, and then sprayed onto the target substrate. Different metal powders offer a wide range of properties for various thermal spraying applications.
- Brazing and Welding: Metal powders can be used as filler materials in brazing and welding processes. They offer several advantages, such as improved flowability, reduced spatter, and the ability to create precise welds.
Beyond Traditional Applications: The potential of metal powders from bar stock extends beyond established applications. They are finding their way into new and exciting areas, such as:
- Biomedical Implants: The biocompatible nature of certain metal powders, like cobalt-chrome and titanium, makes them ideal for creating customized implants with improved functionality and osseointegration (bone bonding) for patients.
- Electronics: Metal powders are being explored for creating intricate electronic components with high conductivity and thermal management properties.
- Aerospace and Defense: The high strength-to-weight ratio and heat resistance of certain metal powders make them perfect for lightweighting aircraft components and creating high-performance parts for demanding aerospace applications.
Choosing the Right Powder: A Look at Specifications and Considerations
With such a diverse range of metal powders available, selecting the right one for your application is crucial. Here are some key factors to consider:
- Material Properties: Clearly define the desired properties for your final product, such as strength, ductility, corrosion resistance, and thermal conductivity. Choose a metal powder that aligns with these requirements.
- Particle Size and Distribution: Consider the impact of particle size and distribution on your chosen manufacturing process. For instance, finer powders might be preferred for additive manufacturing with high-resolution requirements.
- Powder Flowability: Ensure the powder exhibits good flowability for efficient processing in techniques like metal injection molding.
Specifications, Suppliers, and Costs: A Practical Guide
Selecting the right metal powder for your project goes beyond just properties and applications. Here’s a breakdown of some key practical considerations:
Metal Powder Specifications:
Beyond the general properties discussed earlier, metal powders come with specific technical specifications that define their characteristics and suitability for various processes. Here are some common specifications to consider:
- Chemical Composition: This details the exact elemental makeup of the powder, including the primary metal and any alloying elements present. This information is crucial for ensuring the final product meets the desired material properties.
- Particle Size Distribution: This specification defines the range and distribution of particle sizes within the powder. It is often expressed as a range (e.g., 15-45 microns) or through a standard particle size distribution curve.
- การไหล: Measured by various methods like the Hall flowmeter test, flowability indicates how easily the powder flows under its own weight. It’s a critical factor for efficient processing in techniques like MIM.
- ความหนาแน่นปรากฏ This refers to the bulk density of the powder, considering the space occupied by the particles and the voids between them. It impacts the amount of powder needed to achieve a specific final product density.
- Sinterability: This specification defines the powder’s ability to bond together during the sintering process. It is often expressed as the minimum sintering temperature required to achieve a certain level of density in the final product.
Suppliers and Pricing:
A wide range of companies supply metal powders directly from bar stock. Here are some factors to consider when choosing a supplier:
- Material Availability: Ensure the supplier offers the specific metal powder composition and grade you require.
- Powder Specifications: Verify that the supplier’s powder specifications align with your application needs.
- Quality Control: Choose a reputable supplier with a strong commitment to quality control procedures to ensure consistent powder characteristics.
- Minimum Order Quantities: Be aware of the minimum order quantities required by the supplier. This can be crucial for smaller projects.
- การกำหนดราคา: Metal powder pricing can vary depending on the material, particle size, and order quantity. Obtain quotes from multiple suppliers to compare pricing and find the best value for your project.
A Cost Consideration:
Metal powders from bar stock generally cost more per unit weight compared to bulk bar stock material. However, this is often offset by the advantages they offer, such as:
- Reduced Material Waste: Since metal powders can be used in near-net-shape manufacturing techniques, there’s minimal material waste compared to traditional machining processes.
- Complex Geometries: Metal powders enable the creation of complex geometries that might be difficult or impossible to achieve with traditional manufacturing techniques.
- Lightweighting: Certain metal powders offer high strength-to-weight ratios, allowing for the creation of lightweight components for applications like aerospace.
The Bottom Line: While the upfront cost of metal powders might be higher, the overall project cost can be lower due to reduced waste, design flexibility, and potential performance benefits.
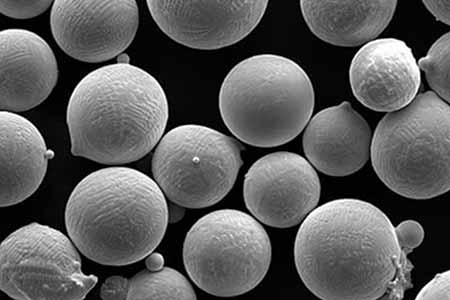
Advantages and Limitations
Metal powders from bar stock offer a compelling array of advantages for manufacturers, but they also come with certain limitations. Here’s a balanced perspective to help you make an informed decision:
Advantages:
- Design Flexibility: Metal powders enable the creation of complex geometries with intricate features, pushing the boundaries of design and functionality.
- Near-Net-Shape Manufacturing: These powders minimize material waste compared to traditional machining processes.
- Lightweighting: Certain metal powders offer high strength-to-weight ratios, ideal for creating lightweight components in aerospace and other weight-sensitive applications.
- Material Tailoring: By selecting the specific bar stock composition and atomization technique, manufacturers can fine-tune the powder characteristics for specific applications.
- Mass Customization: Additive manufacturing with metal powders allows for the creation of customized parts without significant cost increases.
Limitations:
- Cost: Metal powders can be more expensive per unit weight compared to bulk bar stock material.
- Surface Finish: While advancements are being made, the surface finish of components created with metal powders might not be as smooth as those machined from solid bar stock.
- Process Complexity: Additive manufacturing and other techniques using metal powders can be more complex to set up and manage compared to traditional machining processes.
คำถามที่พบบ่อย
Here, we delve into some frequently asked questions about metal powders from bar stock, providing you with a comprehensive understanding of this transformative technology:
FAQ Table
Question | Answer |
---|---|
What are the different types of atomization techniques used for metal powders? | As mentioned earlier, the two primary atomization techniques are gas atomization and water atomization. Gas atomization offers superior control over particle size and morphology, making it ideal for demanding applications like additive manufacturing. Water atomization is a more cost-effective option but results in less spherical particles. |
Can I use recycled bar stock to create metal powders? | Yes! In fact, using recycled bar stock for atomization is an environmentally friendly approach. However, the specific material composition and any contaminants in the recycled material need to be carefully considered to ensure the final powder meets the desired specifications. |
How are metal powders stored and handled? | Metal powders can be susceptible to moisture and oxidation. They are typically stored in sealed containers under controlled atmospheric conditions. Proper handling techniques are crucial to prevent contamination and maintain powder flowability. |
What are the safety considerations when working with metal powders? | Fine metal powders can be flammable and pose inhalation risks. Proper personal protective equipment (PPE) like respirators and safety glasses should be worn when handling powders. Additionally, proper ventilation and dust collection systems are essential in work environments. |
What are the future trends in metal powder technology? | The future of metal powders is bright! We can expect advancements in: * Development of new and improved atomization techniques for even finer control over powder characteristics. * Expansion of the range of available metal powders, including exotic alloys and composites. * Integration of automation and artificial intelligence (AI) for optimized powder production and processing. * Reduced costs associated with metal powders, making them even more accessible for a wider range of applications. |
About 3DP mETAL
Product Category
ติดต่อเรา
มีคำถามอะไรไหม? ส่งข้อความมาเดี๋ยวนี้! หลังจากที่ได้รับข้อความแล้ว เราจะประมวลผลคำขอของคุณพร้อมทีมงานทั้งหมด