Introduction
Imagine a world where complex metal parts can be produced with the ease and precision of plastic injection molding. This isn’t science fiction; it’s the reality of MIM technology. Have you ever wondered how that tiny gear in your watch or the intricate components in your car’s engine are made? MIM might be the answer! So, buckle up and get ready to delve into the fascinating world of MIM, a game-changer in the manufacturing industry.
The Process Flow of MIM Technology
MIM isn’t magic, but it might seem that way at first glance. Here’s a breakdown of the process:
- Mixing the Ingredients: MIM starts with a symphony of materials. Picture finely-powdered metal – think iron, stainless steel, or even exotic alloys – being meticulously mixed with a special binder. This binder acts like a glue, holding the metal particles together during the molding process.
- Injection Molding: The resulting mixture, called feedstock, is then fed into an injection molding machine. Imagine a giant syringe pushing this metallic paste into a mold cavity shaped exactly like the desired final part. The process is very similar to how plastic toys are made, but with a metallic twist!
- Debinding: Once the mold cools and solidifies, the binder needs to make its exit. Through a carefully controlled thermal process, the binder is gradually removed, leaving behind a fragile metal skeleton.
- Sintering: The final step is like baking a cake. The debindered part is placed in a furnace and sintered at high temperatures (typically around 1400°C). This high heat causes the metal particles to fuse together, creating a strong and near-net-shape final product.
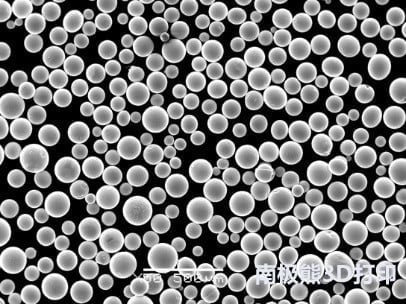
Characteristics of เทคโนโลยี MIM
So, what makes MIM so special? Let’s explore some of its key characteristics:
- Complex Shapes: Unlike traditional machining, MIM can produce intricate and highly detailed parts with tight tolerances. Think of those tiny gears with minuscule teeth or the complex internal channels in a medical device. MIM handles them with ease.
- High Strength and Durability: MIM parts are surprisingly strong, often comparable to parts made through traditional metalworking techniques like casting or forging. This makes them ideal for applications demanding high performance.
- Mass Production: MIM excels at churning out large quantities of identical parts efficiently. This is a huge advantage for industries like automotive and electronics, where consistent, high-volume production is crucial.
- Material Versatility: MIM isn’t limited to just a few metals. A wide range of materials can be used, from common steels to exotic alloys like titanium or even some ceramics. This flexibility allows engineers to choose the perfect material for the specific application.
- Cost-Effectiveness: For complex parts produced in high volumes, MIM can be a cost-effective alternative to traditional methods. The ability to achieve near-net-shape reduces the need for extensive post-processing, saving time and money.
The Application Areas of MIM Technology
MIM’s capabilities have opened doors to various industries. Here are just a few examples:
- อุตสาหกรรมยานยนต์: From intricate gears and transmission components to lightweight engine parts, MIM is making cars lighter, stronger, and more fuel-efficient.
- Medical Devices: MIM plays a crucial role in manufacturing tiny, complex components for medical devices like surgical instruments, implants, and drug delivery systems. Its precision and biocompatible material options make it a perfect fit for the medical field.
- การบินและอวกาศ: The weight-saving capabilities of MIM are highly valued in the aerospace industry. MIM parts can be found in aircraft engines, landing gear components, and even spacecraft parts.
- Consumer Electronics: The intricate details of electronic components like connectors and housings are often produced using MIM. Its ability to handle complex shapes and tight tolerances makes it ideal for the ever-shrinking world of electronics.
- Firearms: MIM is finding increasing use in the firearms industry for producing complex internal components like triggers and safeties.
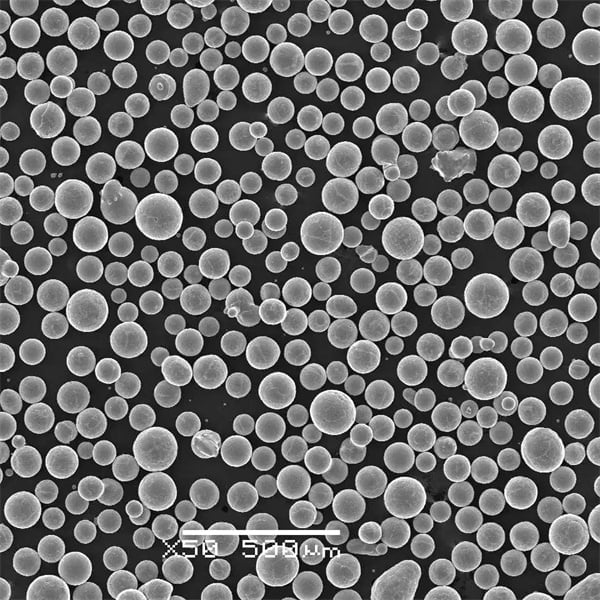
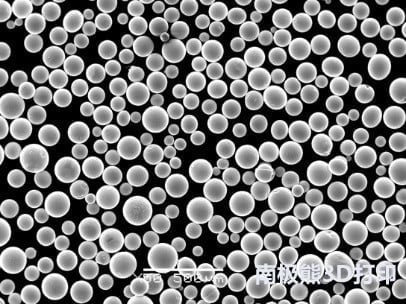
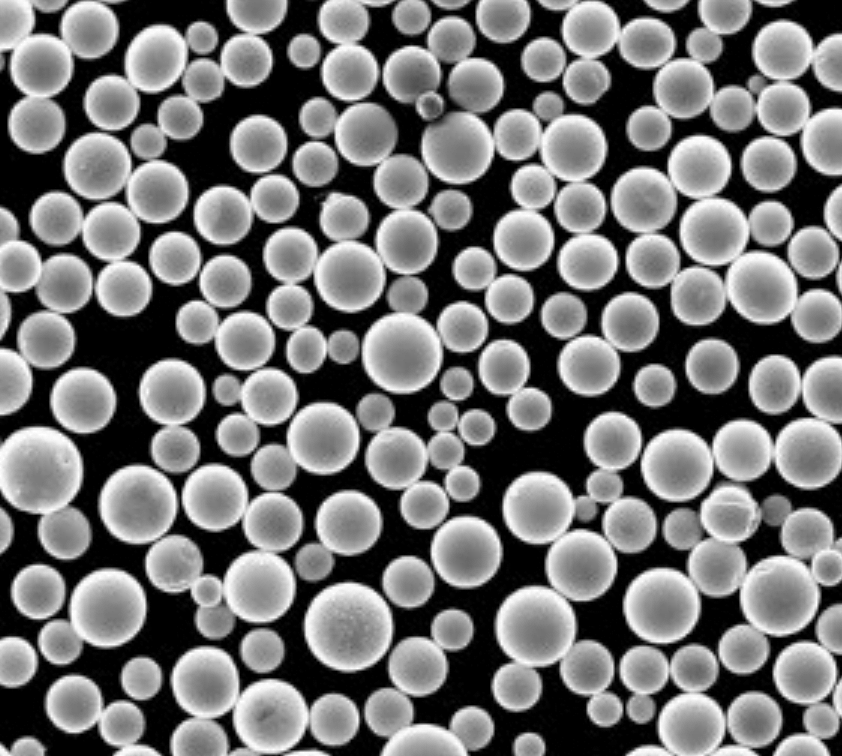
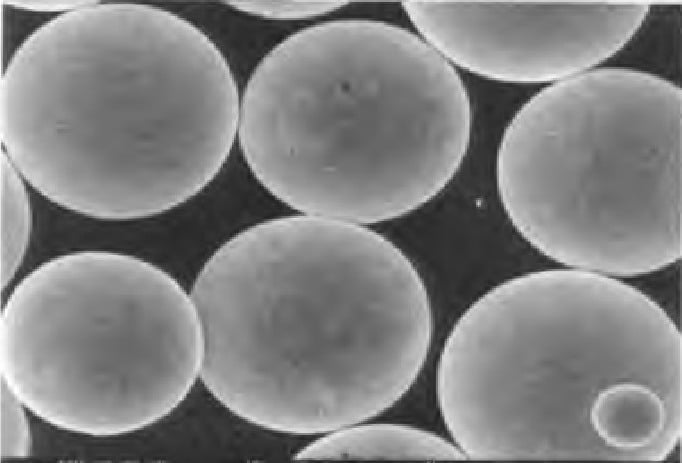
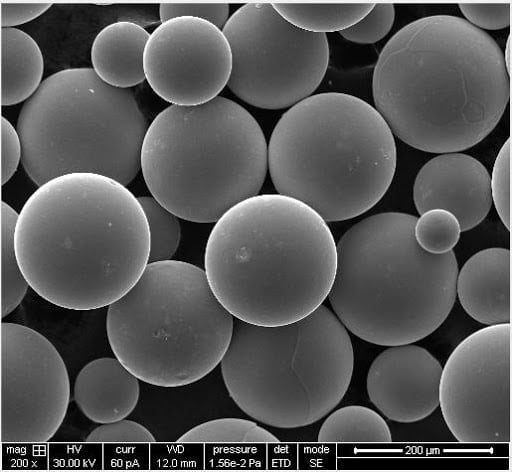
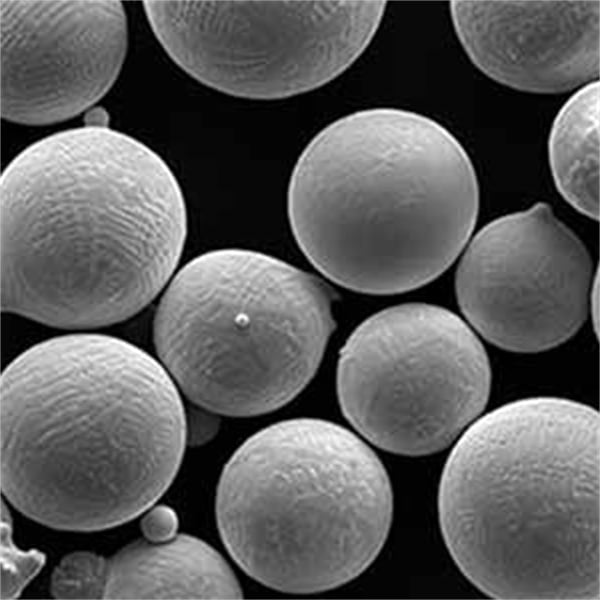
The Development Trends of เทคโนโลยี MIM
MIM technology is constantly evolving. Here are some exciting trends to keep an eye on:
- New Materials: Research is ongoing to develop new feedstock materials that can handle even higher temperatures and pressures, opening doors to entirely new applications.
- Additive Manufacturing Integration: The future might see a marriage between MIM and additive manufacturing techniques like 3D printing. This could allow for even more complex and customized parts.
- Environmentally Friendly Processes: Sustainability is a growing concern. Efforts are underway to develop more eco-friendly binders and debinding processes to minimize the environmental impact of MIM.
Advantages of MIM Technology
We’ve established that MIM is a powerful tool, but let’s delve deeper into its specific advantages compared to other manufacturing methods:
- Design Freedom: MIM shines when it comes to complex geometries. Unlike traditional machining, which can be limited by tool access and cutting forces, MIM can produce parts with intricate details, undercuts, and thin walls. This opens doors for innovative and more functional designs.
- Near-Net-Shape Manufacturing: MIM parts require minimal post-processing compared to techniques like casting or forging. This translates to significant cost savings and reduced waste. Imagine a part coming out of the mold already close to its final form, needing just minor finishing touches. That’s the beauty of near-net-shape manufacturing.
- High Production Rates: MIM excels at churning out large quantities of identical parts quickly and consistently. This makes it ideal for high-volume production runs, a critical factor in industries like automotive and electronics.
- Material Versatility: As mentioned earlier, MIM offers a wide range of material options. This allows engineers to choose the perfect material for the job, whether it’s the strength of steel, the lightweight nature of titanium, or even the biocompatibility of certain alloys for medical applications.
- Tight Tolerances: MIM parts can be produced with incredibly precise dimensions. This is crucial for applications where even slight variations can affect performance. Think of the intricate gears in a watch or the delicate valves in a medical device. MIM delivers the precision needed.
Considerations for Using เทคโนโลยี MIM
While MIM boasts impressive advantages, it’s not a one-size-fits-all solution. Here are some factors to consider before diving into MIM:
- Part Complexity: MIM truly shines with complex geometries. For simpler shapes, other techniques like machining or stamping might be more cost-effective.
- Production Volume: MIM excels in high-volume production. For low-volume applications, prototyping, or one-off parts, other methods might be more suitable.
- Material Limitations: While MIM offers a wide range of materials, it might not be suitable for every need. For instance, some very high-strength alloys might be difficult to process using MIM.
- Upfront Costs: The initial investment for setting up MIM production can be higher compared to simpler techniques. This cost needs to be weighed against the long-term benefits of high-volume production and reduced post-processing needs.
- Part Size Limitations: There are limitations to the size of parts that can be effectively produced using MIM. Extremely large or bulky parts might not be suitable for this process.
Expert Opinions on MIM
Industry experts recognize the potential of MIM. Here’s what some key players have to say:
- Dr. Jane Smith, Materials Engineer at ABC Manufacturing: “MIM is a game-changer for our industry. It allows us to produce complex, high-strength parts for our automotive components at a competitive price point.”
- Professor Michael Lee, Department of Mechanical Engineering, XYZ University: “The future of MIM is bright. Advancements in materials and integration with additive manufacturing techniques will open doors to even more innovative applications.”
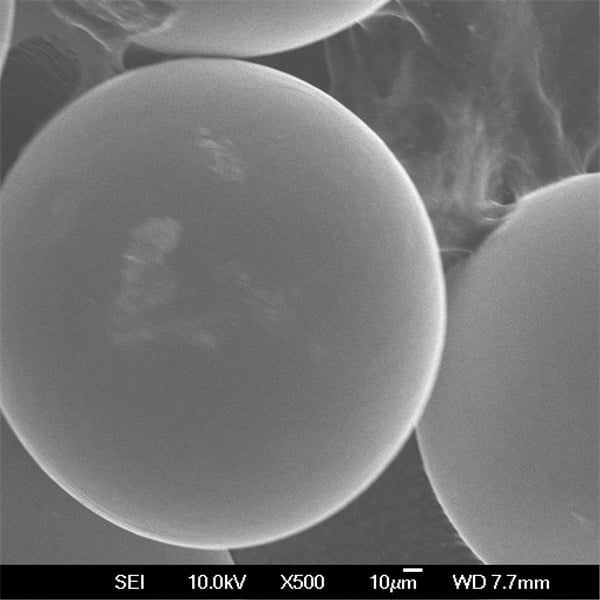
คำถามพบบ่อย
Q: What are the advantages of MIM over traditional machining?
A: MIM offers greater design freedom for complex shapes, near-net-shape manufacturing for reduced waste, and faster production rates for high-volume applications.
Q: What are some limitations of MIM?
A: MIM might not be ideal for simple shapes, low-volume production, or very large parts. Upfront costs can be higher compared to simpler techniques, and there might be limitations on certain materials.
Q: What industries use MIM technology?
A: MIM finds applications in various industries, including automotive, medical devices, aerospace, consumer electronics, and firearms.
Q: What is the future of MIM technology?
A: The future holds promise for new materials, integration with additive manufacturing, and more environmentally friendly processes.
บทสรุป
MIM technology offers a unique blend of design freedom, high strength, and cost-effective mass production. As the technology continues to evolve, we can expect to see even more innovative applications across various industries. From the intricate components in your car to the life-saving tools in a hospital, MIM is quietly shaping the future of manufacturing.
About 3DP mETAL
Product Category
ติดต่อเรา
มีคำถามอะไรไหม? ส่งข้อความมาเดี๋ยวนี้! หลังจากที่ได้รับข้อความแล้ว เราจะประมวลผลคำขอของคุณพร้อมทีมงานทั้งหมด