Imagine building intricate components capable of withstanding scorching temperatures and punishing environments. This isn’t science fiction; it’s the world of nickel alloy powders, a revolutionary material transforming modern manufacturing.
Nickel alloy powders are finely-ground metal particles specifically designed for Additive Manufacturing (AM), also known as 3D printing. These tiny powerhouses unlock a universe of possibilities, enabling the creation of complex, high-performance parts for a diverse range of industries.
Delving deeper, let’s explore the fascinating world of nickel alloy powders, unraveling their composition, properties, applications, and the exciting potential they hold for the future.
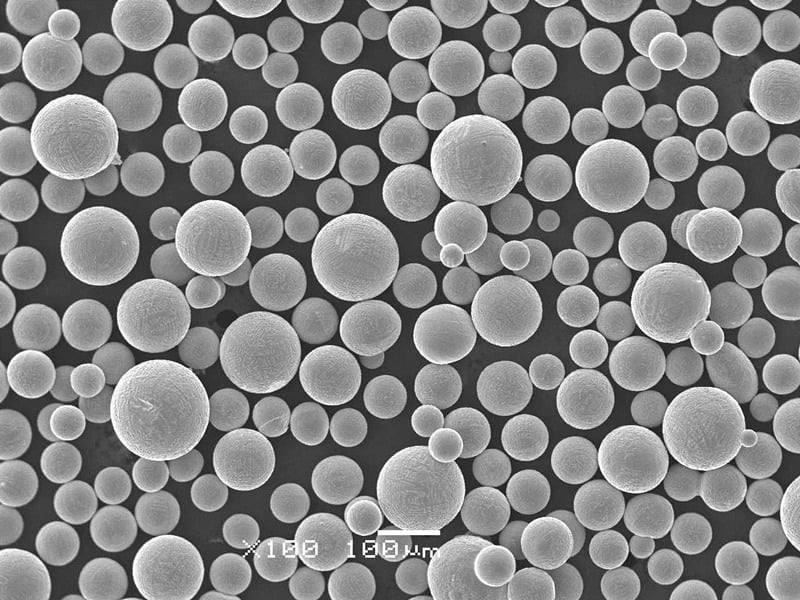
the Compositional Nuances of Nickel Alloy Powders
Nickel alloy powders are not just pure nickel. They’re a blend of nickel and other strategic elements, each playing a crucial role in defining the final properties of the material. Here’s a glimpse into some of the key alloying elements:
- Chromium (Cr): Enhances oxidation resistance, making the material stand tall against high temperatures and corrosive environments.
- Iron (Fe): Contributes to strength and overall mechanical properties.
- Molybdenum (Mo): Boosts high-temperature strength and creep resistance, allowing components to function flawlessly under prolonged stress.
- Cobalt (Co): Improves high-temperature strength and oxidation resistance, making it a valuable addition for demanding applications.
- Aluminum (Al): Enhances strength and oxidation resistance at moderate temperatures.
The specific composition of each nickel alloy powder varies depending on the desired properties. This allows manufacturers to tailor the material to meet the specific needs of an application.
Common Nickel Alloy Powders and Their Composition:
Metal Powder Model | องค์ประกอบ |
---|---|
EOS NickelAlloy IN625 | Nickel (Ni) – Chromium (Cr) – Molybdenum (Mo) – Iron (Fe) |
EOS NickelAlloy IN718 | Nickel (Ni) – Chromium (Cr) – Molybdenum (Mo) – Columbium (Cb) (Niobium (Nb)) – Iron (Fe) |
EOS NickelAlloy HAYNES® 282® | Nickel (Ni) – Chromium (Cr) – Molybdenum (Mo) – Tungsten (W) – Cobalt (Co) – Iron (Fe) |
Höganäs AM ® Nickel Alloy 625 | Nickel (Ni) – Chromium (Cr) – Molybdenum (Mo) – Iron (Fe) |
Höganäs AM ® Alloy 718 | Nickel (Ni) – Chromium (Cr) – Molybdenum (Mo) – Columbium (Cb) (Niobium (Nb)) – Iron (Fe) |
AP&C Ni Alloy 718 | Nickel (Ni) – Chromium (Cr) – Molybdenum (Mo) – Columbium (Cb) (Niobium (Nb)) – Iron (Fe) |
Oerlikon AM304L | Nickel (Ni) – Chromium (Cr) – Molybdenum (Mo) – Iron (Fe) |
Carpenter® ADDITIVE Wire 17-4PH | Nickel (Ni) – Chromium (Cr) – Copper (Cu) – Columbium (Cb) (Niobium (Nb)) – Molybdenum (Mo) |
the Properties of Make Nickel Alloy Powders
The unique blend of elements in nickel alloy powders translates into a remarkable set of properties:
- High-Temperature Strength: These powders can withstand scorching temperatures exceeding 1000°C (1832°F) without succumbing to deformation or losing their integrity. This makes them ideal for applications in aerospace, energy production, and other high-heat environments.
- Excellent Corrosion Resistance: Nickel alloy powders boast exceptional resistance to corrosion, even in harsh chemical environments. This property makes them perfect for components used in the chemical processing, oil and gas, and marine industries.
- Superior Wear Resistance: These powders excel in resisting wear and tear, making them well-suited for parts exposed to friction and abrasion. They find applications in gears, bearings, and other components subjected to high wear.
- Good Weldability: Nickel alloy powders can be readily welded using various techniques, allowing for the creation of complex structures and assemblies.
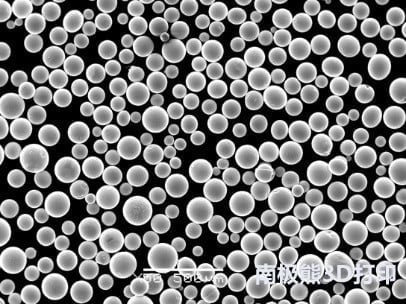
Applications of Nickel Alloy Powders
The exceptional properties of nickel alloy powders unlock a vast array of applications across different industries. Here are some prime examples:
อุตสาหกรรม | ตัวอย่างแอปพลิเคชัน |
---|---|
อวกาศ | Turbine blades, rocket engine components, landing gear components |
Energy Production | Gas turbine components, heat exchangers, combustor liners |
กระบวนการทางเคมี | Pumps, valves, piping components |
น้ำมันและก๊าซ | Downhole tools, wellhead components, valves |
นาวิกโยธิน | Propeller shafts, rudders, impellers |
ยานยนต์ | High-performance engine components, lightweight components |
แพทย์ | Prosthetic implants, surgical instruments |
Beyond these established applications, nickel alloy powders are poised to revolutionize other sectors:
- Biomedical Engineering: The ability to create intricate, biocompatible structures with nickel alloy powders opens doors for the development of customized implants and prosthetics. Imagine creating a perfectly fitting knee replacement tailored to an individual’s specific anatomy.
- Aerospace and Defense: The lightweight nature and high-performance properties of nickel alloy powders make them ideal for creating stronger, lighter aircraft components, leading to increased fuel efficiency and improved range.
- Consumer Goods: The potential for complex geometries and customization with nickel alloy powders could pave the way for the creation of high-end, personalized sporting goods or even unique jewelry pieces.
The Future of Nickel Alloy Powders
The potential of nickel alloy powders is far from exhausted. As Additive Manufacturing technology continues to evolve, we can expect to see even more innovative applications emerge. Here are some exciting possibilities on the horizon:
- Multi-Material Printing: The ability to combine nickel alloy powders with other materials within the same print could lead to the creation of components with a unique blend of properties, optimizing performance for specific applications.
- Functionally Graded Materials: Imagine a component that seamlessly transitions from one material to another within its structure. This could be achieved with nickel alloy powders, enabling the creation of parts with tailored properties in different zones.
- Lattice Structures: These lightweight, yet strong structures can be readily printed using nickel alloy powders, offering exciting possibilities for applications in aerospace and other weight-critical industries.
The future of nickel alloy powders is brimming with potential. As research and development efforts continue, we can expect to see these remarkable materials play an even more significant role in shaping the future of manufacturing.
the Specifications of Nickel Alloy Powders
When choosing a nickel alloy powder for a specific application, several factors need to be considered. Here’s a breakdown of key specifications:
Particle Size and Distribution: The size and distribution of the powder particles significantly impact the printability, surface finish, and mechanical properties of the final component. Generally, finer powders produce smoother surfaces but may be more challenging to print.
การไหล: The powder’s ability to flow freely is crucial for even deposition during the printing process. Powders with good flowability ensure consistent material distribution and minimize printing defects.
Sphericity: The shape of the powder particles also plays a role. Spherical particles typically flow better and pack more densely, leading to improved mechanical properties.
Chemical Composition: As discussed earlier, the specific composition of the nickel alloy powder dictates its final properties. Selecting the right composition is vital for ensuring the component meets the application’s requirements.
Standards and Certifications: Certain industries may have specific standards or certifications for materials used in critical applications. Choosing a powder that complies with these standards is essential.
Here’s a table summarizing some of the key specifications for commonly available nickel alloy powders:
สเปก | คำอธิบาย |
---|---|
Particle Size (µm) | Distribution of powder particle diameters |
Flowability (g/s) | Rate at which the powder flows |
Sphericity | Shape of the powder particles (closer to a sphere is better) |
Chemical Composition (wt%) | Percentage of each element in the alloy |
Standards/Certifications | Compliance with industry standards (e.g., ASTM International) |
Pricing Considerations:
Nickel alloy powders can vary in price depending on the specific composition, particle size, and manufacturer. Generally, more complex alloys and finer powders tend to be more expensive. It’s crucial to factor in the cost of the powder alongside other manufacturing costs when evaluating the overall economic feasibility of using nickel alloy powders for a particular application.
Here’s a table providing a general pricing range for some common nickel alloy powders (prices may vary depending on supplier and order quantity):
Metal Powder Model | Estimated Price Range (USD/kg) |
---|---|
EOS NickelAlloy IN625 | $200 – $300 |
EOS NickelAlloy IN718 | $250 – $350 |
Höganäs AM ® Nickel Alloy 625 | $150 – $250 |
Höganäs AM ® Alloy 718 | $200 – $300 |
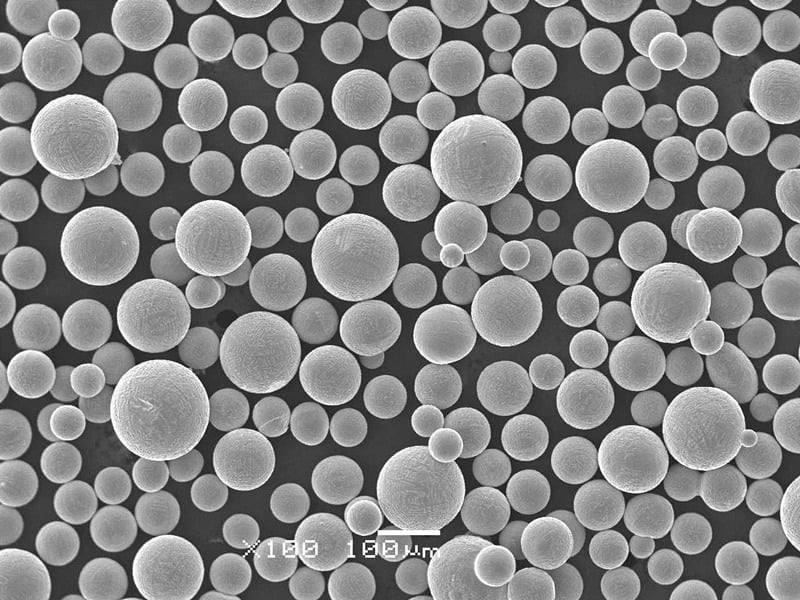
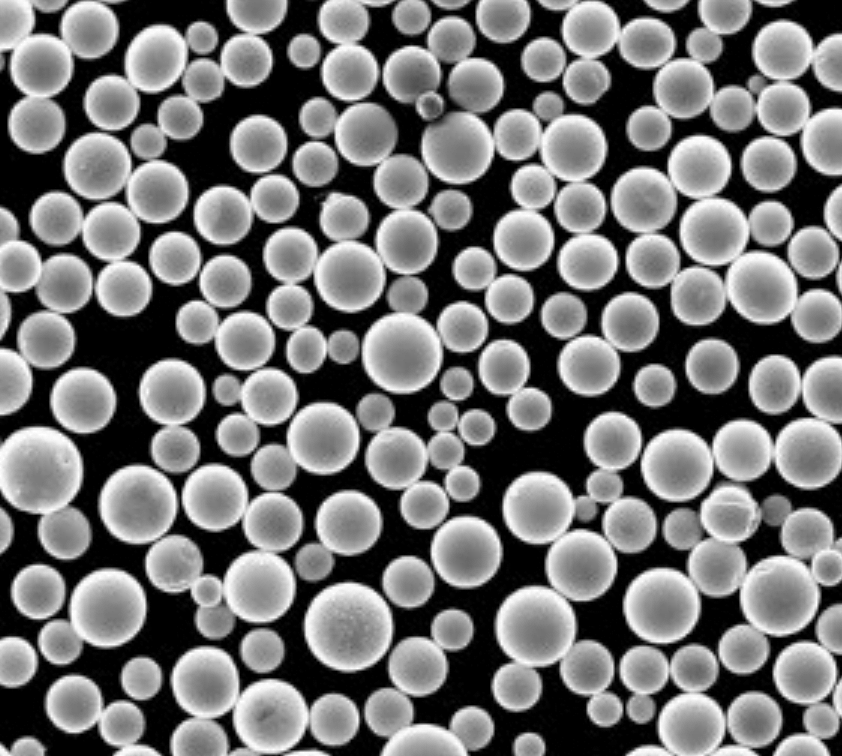
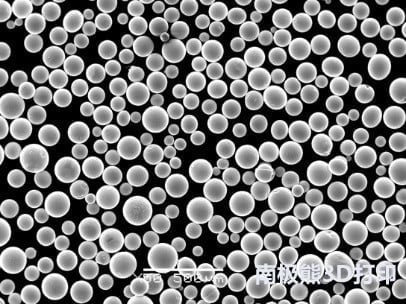
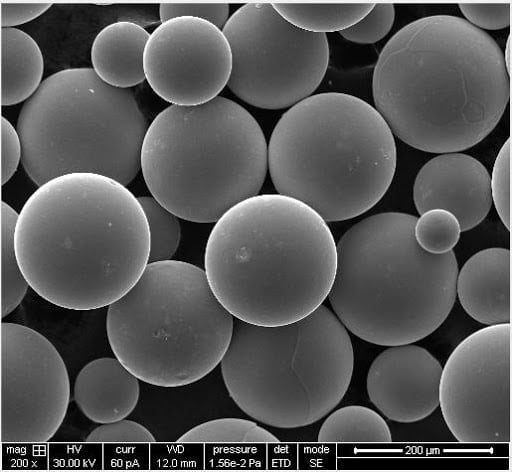
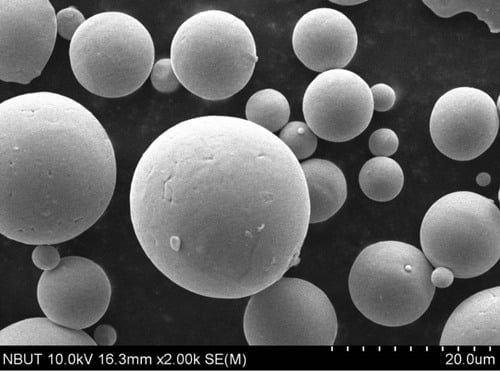
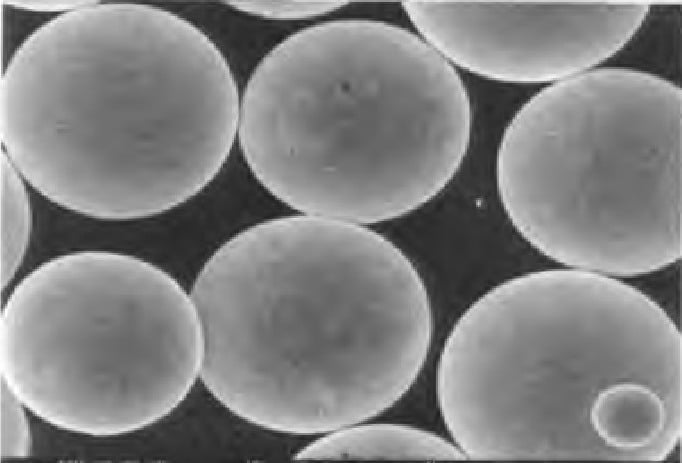
the Pros and Cons of Nickel Alloy Powders
Nickel alloy powders offer a compelling set of advantages, but it’s important to acknowledge their limitations as well. Here’s a comprehensive analysis of their pros and cons:
Advantages of Nickel Alloy Powders:
- Exceptional Material Properties: As highlighted earlier, nickel alloy powders boast impressive high-temperature strength, corrosion resistance, wear resistance, and weldability, making them ideal for demanding applications.
- Design Freedom: Additive Manufacturing allows for the creation of complex geometries that would be impossible or highly challenging with traditional manufacturing techniques. This design freedom opens doors for innovative part designs and functionalities.
- Lightweighting: Nickel alloy powders can be used to create lightweight components without compromising on strength. This is particularly beneficial in applications like aerospace, where weight reduction translates to improved fuel efficiency and performance.
- Reduced Waste: Compared to traditional manufacturing methods that generate significant scrap material, Additive Manufacturing with nickel alloy powders minimizes waste. This translates to cost savings and environmental benefits.
- Mass Customization: The ability to create complex geometries with 3D printing allows for the production of customized parts tailored to specific needs. This is valuable in industries like medical and aerospace.
Disadvantages of Nickel Alloy Powders:
- Cost: Nickel alloy powders themselves can be expensive, and the Additive Manufacturing process can also be more costly compared to traditional techniques for high-volume production.
- Surface Finish: While improving, the surface finish of components printed with nickel alloy powders may not be as smooth as those produced with traditional methods like machining. This may require additional post-processing steps.
- Limited Material Selection: While the range of available nickel alloy powders is expanding, it’s still not as vast as the selection of materials available for traditional manufacturing techniques.
- Process Complexity: Additive Manufacturing with nickel alloy powders requires specialized equipment and expertise. This can present a challenge for companies not familiar with this technology.
- Safety Considerations: Nickel alloy powders can pose health risks if inhaled. Proper handling procedures and safety equipment are essential when working with these materials.
Making an Informed Decision:
The decision to use nickel alloy powders depends on the specific application and its requirements. By carefully considering the advantages and disadvantages outlined above, manufacturers can make informed choices that optimize performance, cost, and overall feasibility.
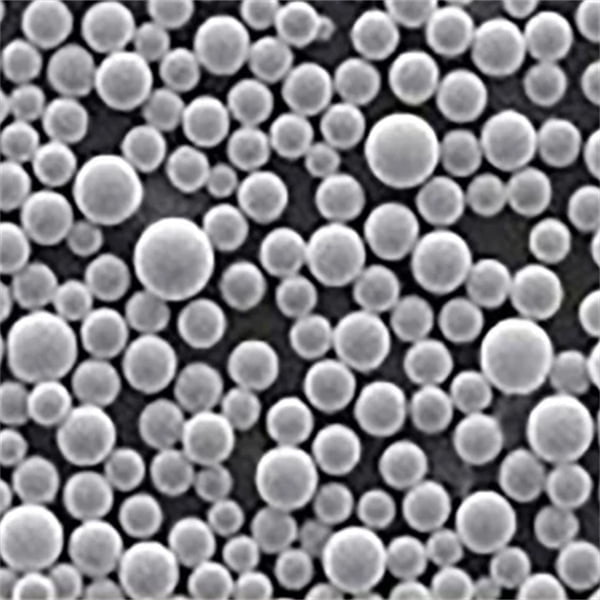
คำถามพบบ่อย
Q: What are the different types of nickel alloy powders available?
A: There are various nickel alloy powders available, each with a unique composition optimized for specific properties. Some common types include IN625, IN718, Haynes® 282®, and Alloy 718.
Q: How are nickel alloy powders manufactured?
A: Nickel alloy powders can be produced using various techniques, including gas atomization, water atomization, and plasma atomization. These processes involve melting the nickel alloy and then breaking it down into fine particles.
Q: What are the typical applications for nickel alloy powders?
A: Nickel alloy powders find use in various industries, including aerospace, energy production, chemical processing, oil and gas, marine, automotive, and medical. They are particularly suited for applications requiring high-temperature strength, corrosion resistance, and wear resistance.
Q: What are the advantages of using nickel alloy powders compared to traditional manufacturing techniques?
A: Nickel alloy powders offer several advantages, including design freedom, lightweighting, reduced waste, and mass customization possibilities.
Q: What are the limitations of using nickel alloy powders?
A: Some limitations include higher cost compared to traditional methods for high-volume production, potential surface roughness requiring post-processing, limited material selection compared to traditional techniques, and the complexity of the Additive Manufacturing process.
Q: What safety precautions should be taken when handling nickel alloy powders?
A: Nickel alloy powders can pose health risks if inhaled. It’s crucial to wear proper personal protective equipment (PPE) such as respirators and gloves when handling these materials. Additionally, proper ventilation is essential to prevent airborne dust.
About 3DP mETAL
Product Category
ติดต่อเรา
มีคำถามอะไรไหม? ส่งข้อความมาเดี๋ยวนี้! หลังจากที่ได้รับข้อความแล้ว เราจะประมวลผลคำขอของคุณพร้อมทีมงานทั้งหมด