The world of 3D printing is constantly evolving, pushing the boundaries of what’s possible. New materials are emerging all the time, each with unique properties that broaden the applications of this transformative technology. One such material making waves is nickel aluminum powder, a metallic blend with the potential to revolutionize how we design and manufacture complex parts.
But before we delve deeper, let’s rewind a bit. Imagine a world where you could create incredibly strong, lightweight components that can withstand extreme temperatures and corrosive environments. Sounds like science fiction, right? Well, nickel aluminum powder might just be the missing piece in this futuristic puzzle.
A Material Marriage Made in 3D Printing Heaven
Nickel aluminum powder isn’t your average metallic blend. It’s a carefully crafted combination of two powerhouse elements:
- Nickel: Renowned for its exceptional strength and high-temperature resistance, nickel is a mainstay in aerospace and energy applications. Think jet engine components and turbine blades that endure immense heat and pressure.
- Aluminum: Lightweight and lauded for its excellent corrosion resistance, aluminum is a popular choice for applications where weight reduction and durability are paramount. Think aircrafts, automotive parts, and even marine equipment.
Now, picture combining these two elements at a microscopic level. That’s the magic of nickel aluminum powder. By marrying these complementary properties, we get a material that boasts the following:
- High-Strength: Nickel aluminum parts can be incredibly strong, rivaling some traditional alloys. This makes them ideal for demanding applications where structural integrity is critical.
- Lightweight: Aluminum’s influence shines through here. Compared to pure nickel components, nickel aluminum parts can be significantly lighter, a crucial factor in sectors like aerospace, where every gram counts.
- Corrosion Resistance: Aluminum’s natural resistance to corrosion is a welcome addition. This translates to parts that can withstand harsh environments without succumbing to rust or degradation.
- High-Temperature Performance: Nickel’s heat tolerance is a key advantage. Parts made from nickel aluminum powder can potentially operate at elevated temperatures, making them suitable for applications like heat exchangers and combustion chambers.
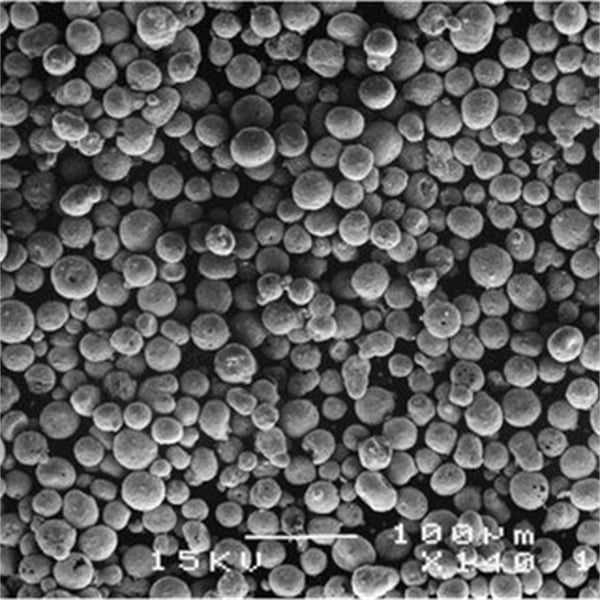
application of Nickel Aluminum Powder
The potential applications of nickel aluminum powder are vast and exciting. Let’s explore some key areas where this innovative material is poised to make a significant impact:
Nickel Aluminum Powder Can Be Used to Manufacture High-Temperature Alloy Parts
Imagine creating intricate components for jet engines or gas turbines that can handle the scorching inferno within. Nickel aluminum powder’s ability to withstand high temperatures makes it a potential game-changer. Compared to traditional methods like casting, 3D printing with nickel aluminum powder offers greater design freedom and potentially reduces production time and waste.
Think about it this way: traditionally manufactured turbine blades often involve complex geometries that require intricate machining processes. 3D printing with nickel aluminum powder allows for the creation of these complex shapes directly from a digital file, streamlining the process and potentially reducing manufacturing costs.
Nickel Aluminum Powder Can Be Used to Manufacture Corrosion-Resistant Parts
Saltwater, harsh chemicals, and extreme weather conditions can wreak havoc on traditional materials. Nickel aluminum powder, with its inherent corrosion resistance, offers a glimmer of hope. Imagine 3D printing lightweight, yet highly durable, components for ships, offshore oil rigs, and even chemical processing plants. These parts could potentially withstand the elements and aggressive environments much better than their conventional counterparts.
For instance, a traditional steel pipe used in an offshore oil rig might be susceptible to rust and degradation over time. A nickel aluminum component, on the other hand, could potentially offer superior resistance to saltwater corrosion, extending the lifespan of the equipment and reducing maintenance costs.
Nickel Aluminum Powder is a Lightweight Material That Can Be Used to Manufacture Lightweight Parts
In industries like aerospace and automotive, every ounce counts. Here’s where the lightweight nature of nickel aluminum powder truly shines. By incorporating this material into 3D printed parts, engineers can potentially achieve significant weight savings compared to components made from heavier metals.
Think of it like this: a traditional steel bracket in a car might add unnecessary weight. A 3D printed nickel aluminum bracket could potentially offer the same level of strength while being significantly lighter, translating to improved fuel efficiency and overall performance.
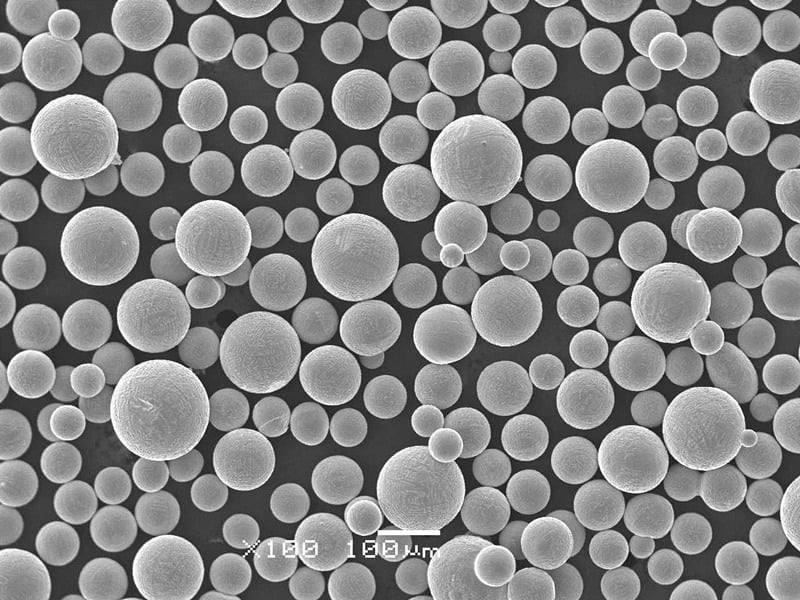
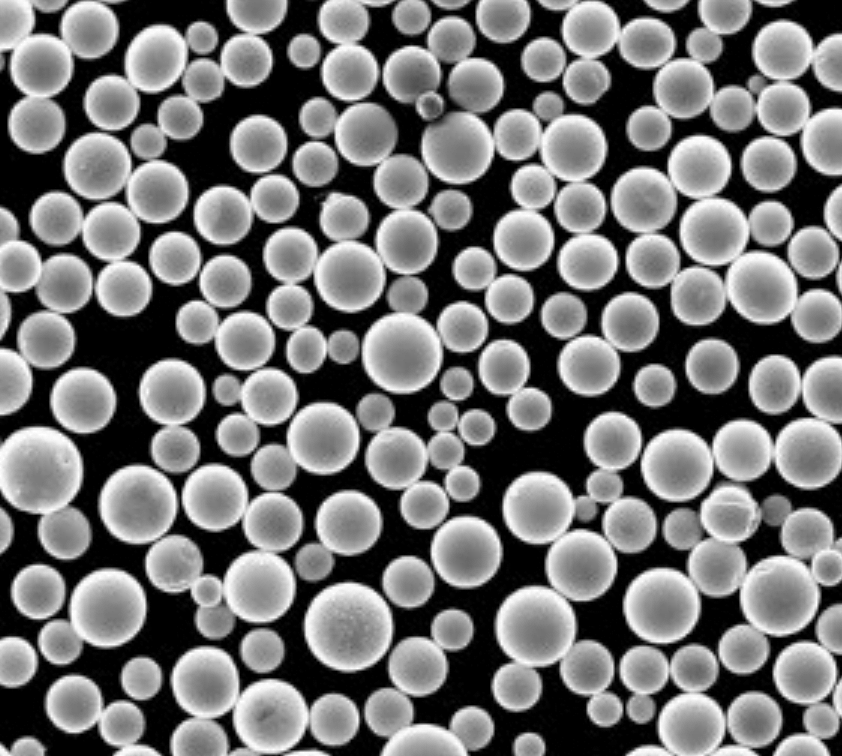
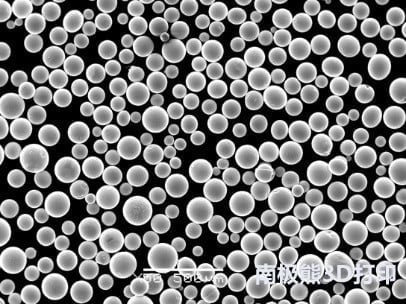
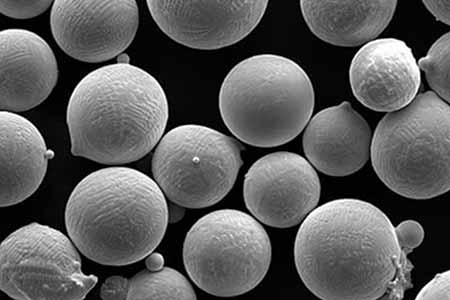
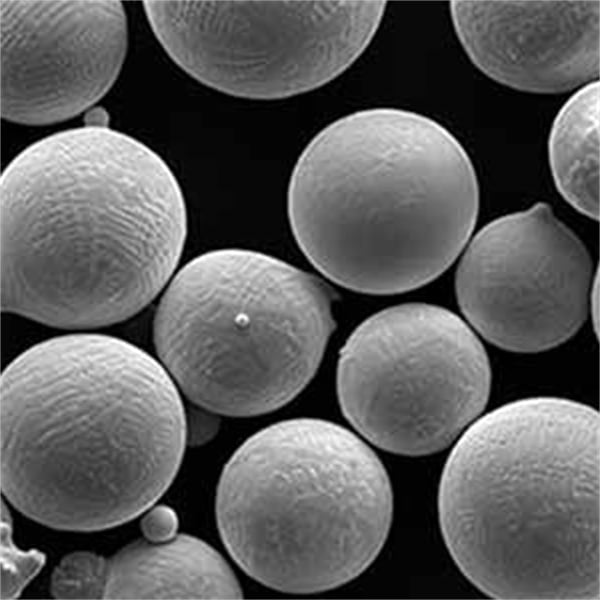
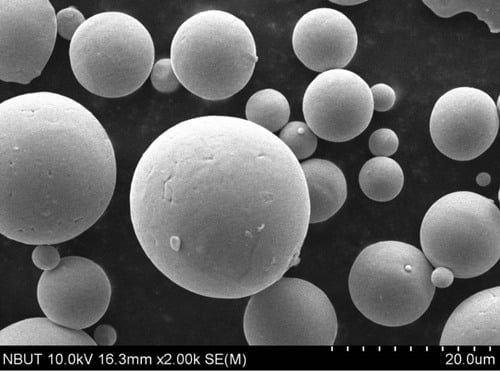
Considerations for Nickel Aluminum Powder Adoption
While nickel aluminum powder presents a compelling proposition, it’s important to acknowledge the challenges associated with its adoption. Here are some key considerations:
- Powder Handling: Nickel aluminum powder, like other metal powders, can be challenging to handle due to its fine particle size and potential health risks. Specialized equipment and safety protocols might be necessary to ensure safe and efficient use.
- Process Optimization: 3D printing with nickel aluminum powder might require adjustments to existing printing parameters compared to more common materials. Developing the printing parameters for nickel aluminum powder might involve experimentation and may require specialized printers capable of handling this unique material. This can add to the initial setup costs and learning curve.
- Material Cost: Currently, nickel aluminum powder might be more expensive compared to some conventional materials. As the technology matures and production scales up, we can expect the cost to come down. However, for now, it’s a factor to consider when evaluating the cost-effectiveness of using this material for specific applications.
The Future of Nickel Aluminum Powder in 3D Printing
The future of nickel aluminum powder in 3D printing appears bright. As research and development efforts continue, we can expect advancements in several key areas:
- Powder Production: Refined production techniques could lead to more cost-effective and readily available nickel aluminum powder, making it a more viable option for a wider range of applications.
- Printability Enhancement: Optimizing printing parameters and potentially developing new printing technologies specifically tailored for nickel aluminum powder could streamline the manufacturing process and improve part quality.
- Material Properties Tailoring: Through advancements in material science, we might see the development of nickel aluminum powder with even more desirable properties, such as enhanced strength-to-weight ratios or improved corrosion resistance for specific environments.
These advancements, coupled with the inherent benefits of nickel aluminum powder, have the potential to revolutionize various industries. Imagine a future where 3D printing with nickel aluminum powder becomes commonplace, enabling the creation of lighter, stronger, and more durable parts for everything from airplanes and automobiles to medical implants and energy infrastructure.
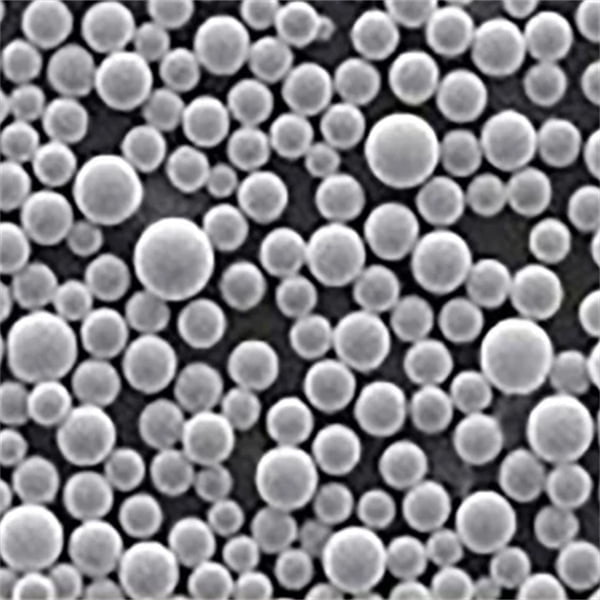
คำถามพบบ่อย
Q: What are the advantages of using nickel aluminum powder in 3D printing?
A: Nickel aluminum powder offers several advantages, including:
- High strength and lightweight: Parts can be incredibly strong while remaining lighter than components made from traditional materials.
- Excellent corrosion resistance: The material can withstand harsh environments without succumbing to rust or degradation.
- High-temperature performance: Parts can potentially operate at elevated temperatures, making them suitable for demanding applications.
- Design freedom: 3D printing allows for the creation of complex geometries that might be difficult or impossible with traditional manufacturing methods.
Q: What are the challenges associated with using nickel aluminum powder?
A: Some challenges include:
- Powder handling: The fine particle size can pose health risks and requires specialized equipment for safe use.
- Process optimization: Developing printing parameters for this material might require adjustments and specialized printers.
- Material cost: Nickel aluminum powder can currently be more expensive than some conventional materials.
Q: What are the future prospects for nickel aluminum powder in 3D printing?
A: The future looks promising. Advancements in powder production, printability enhancement, and material properties tailoring could lead to wider adoption and groundbreaking applications across various industries.
About 3DP mETAL
Product Category
ติดต่อเรา
มีคำถามอะไรไหม? ส่งข้อความมาเดี๋ยวนี้! หลังจากที่ได้รับข้อความแล้ว เราจะประมวลผลคำขอของคุณพร้อมทีมงานทั้งหมด