Imagine a material that combines the strength of steel, the heat resistance of a dragon’s breath, and the electrical conductivity that would make Benjamin Franklin proud. That’s the realm of spherical tungsten powder, a tiny technological titan with a universe of applications.
This article delves deep into the world of spherical tungsten powder, exploring its properties, advantages, limitations, and the specific models that make this material a game-changer across various industries.
Spherical Tungsten Powder
Spherical tungsten powder is a type of metal powder specifically engineered with – you guessed it – a perfectly spherical shape. This seemingly minor detail unlocks a treasure trove of benefits. But before we unpack those, let’s understand what tungsten itself brings to the table.
Tungsten, also known as wolfram, is a naturally occurring element renowned for its impressive properties:
- High Melting Point: Boasting one of the highest melting points among all metals (3422°C or 6192°F), tungsten can withstand extreme temperatures that would melt most other materials.
- Superior Strength: Tungsten is incredibly hard and dense, making it ideal for applications requiring exceptional durability.
- Electrical Conductivity: Electrons flow freely through tungsten, making it a valuable material for electrical components.
Now, imagine these incredible properties packed into tiny, perfectly round particles. That’s the magic of spherical tungsten powder. The spherical shape offers several advantages over irregular-shaped powders:
- Improved Flowability: Spherical particles flow freely, making them easier to handle, transport, and process in various applications.
- Packing Efficiency: The spherical shape allows for tighter packing, resulting in higher density in the final product.
- Uniformity: Consistent spherical particles lead to more uniform properties in the final product, enhancing overall quality and performance.
These characteristics make spherical tungsten powder a highly sought-after material across various industries, from aerospace and electronics to medical equipment and energy production.
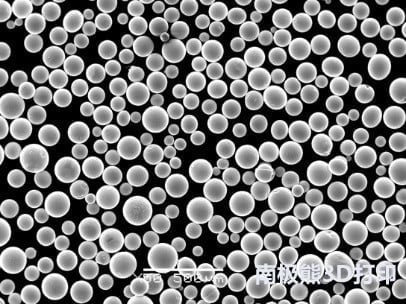
Properties of Spherical Tungsten Powder
Let’s delve deeper into the specific properties of spherical tungsten powder:
ทรัพย์สิน | คำอธิบาย |
---|---|
ความหนาแน่น | Extremely high, typically exceeding 17 g/cm³ |
จุดหลอมเหลว | Inherits the high melting point of tungsten, around 3422°C (6192°F) |
การนำไฟฟ้า | Excellent electrical conductor, comparable to pure copper |
การนำความร้อน | Very high thermal conductivity, efficiently transferring heat |
ความแข็ง | Exceptionally hard and wear-resistant |
ความบริสุทธิ์ | Available in various purity grades, with higher purity offering enhanced performance |
การกระจายขนาดของอนุภาค | Can be tailored for specific applications, ranging from micrometers to hundreds of micrometers |
These properties combine to create a versatile material capable of withstanding harsh environments, conducting electricity efficiently, and maintaining structural integrity under high temperatures and pressure.
Applications of Spherical Tungsten Powder
The unique properties of spherical tungsten powder translate into a wide range of applications. Here are some key examples:
แอปพลิเคชัน | คำอธิบาย |
---|---|
การพิมพ์สามมิติ | Used to create high-performance metal parts with superior strength and heat resistance for aerospace, automotive, and medical applications |
ขึ้นรูปโลหะด้วยการฉีด (MIM) | Enables the production of complex, near-net-shape metal components with intricate details, often used in electronics and machinery |
การพ่นเคลือบความร้อน | Applied to create wear-resistant coatings on various surfaces, extending their lifespan and improving performance in demanding environments |
Electrical Contacts and Electrodes | Leverages excellent electrical conductivity for use in switches, relays, and other electrical components |
Heat Sinks | High thermal conductivity makes it ideal for dissipating heat efficiently in electronic devices and power generation equipment |
Armor and Ballistic Applications | Due to its exceptional density and strength, spherical tungsten powder can be used in armor plating and ballistic projectiles |
X-ray Shielding | Tungsten’s ability to block X-rays makes it valuable for medical imaging equipment and radiation protection applications |
This list just scratches the surface of the possibilities. As technology advances, researchers are constantly exploring new applications for spherical tungsten powder, pushing the boundaries of what’s possible.
Models of Spherical Tungsten Powder
With such a diverse range of applications, it’s no surprise that spherical tungsten powder comes in various models, each tailored to specific needs. Here’s a look at ten prominent models:
- CPH (Cathode Powder High Performance): This model prioritizes high purity (>99.95% W) for applications demanding exceptional electrical conductivity, such as electrodes and electronic components.
- CTP (Cathode Powder Standard): A cost-effective option with a purity level of around 99.5% W, ideal for applications where electrical conductivity is important but absolute top-tier performance isn’t essential, such as in some thermal spraying processes.
- HP (High Performance): This model strikes a balance between purity (typically >99.7% W) and affordability, making it a versatile choice for various applications like MIM and 3D printing where good electrical conductivity and structural integrity are required.
- HT (High Temperature): Prioritizes high thermal conductivity for applications where heat dissipation is crucial. This model might contain additives like alumina (Al2O3) to enhance heat transfer properties, potentially affecting electrical conductivity slightly.
- LT (Low Temperature): Optimized for applications requiring low-temperature sintering processes, often used in electronics manufacturing. This model might have slightly lower density compared to other models.
- FGM (Fine Grade Material): This model boasts a very fine particle size distribution, ideal for creating intricate features in MIM or 3D printing applications. However, the finer particles can be more challenging to handle and flow.
- CGM (Coarse Grade Material): The opposite of FGM, CGM features a coarser particle size distribution. This makes it easier to handle and flow but might limit the level of detail achievable in certain applications.
- RE (Rare Earth): This model incorporates rare earth elements like yttrium (Y) or ytterbium (Yb) to improve the high-temperature performance and sintering characteristics of the powder. This can be beneficial for applications like heat sinks or components operating in very hot environments.
- Alloyed Powders: Spherical tungsten powder can be alloyed with other metals like nickel (Ni) or copper (Cu) to achieve specific properties. Nickel-tungsten alloys offer improved strength and wear resistance, while copper-tungsten alloys enhance electrical conductivity while maintaining good thermal properties.
- Recycled Powders: As sustainability becomes a growing concern, recycled spherical tungsten powder is gaining traction. This option utilizes reprocessed powder from various sources, offering an eco-friendly alternative for applications where top-tier purity might not be a strict requirement.
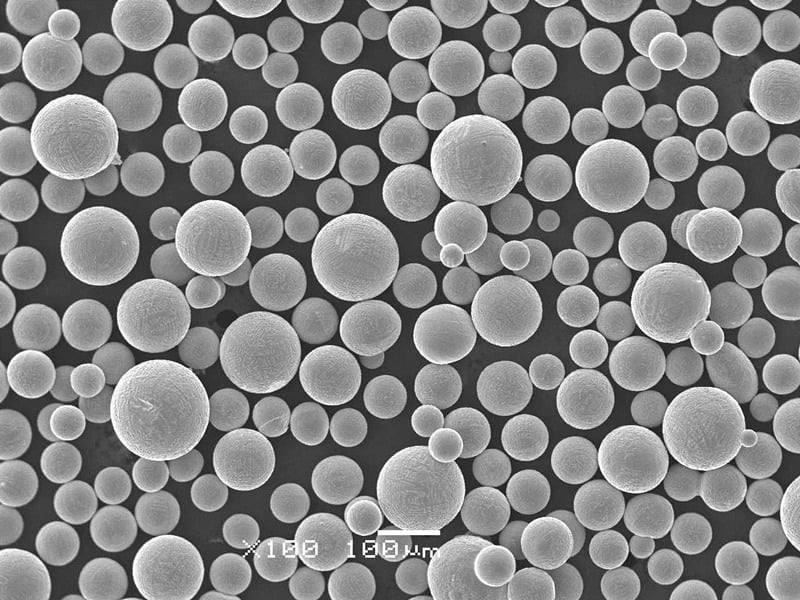
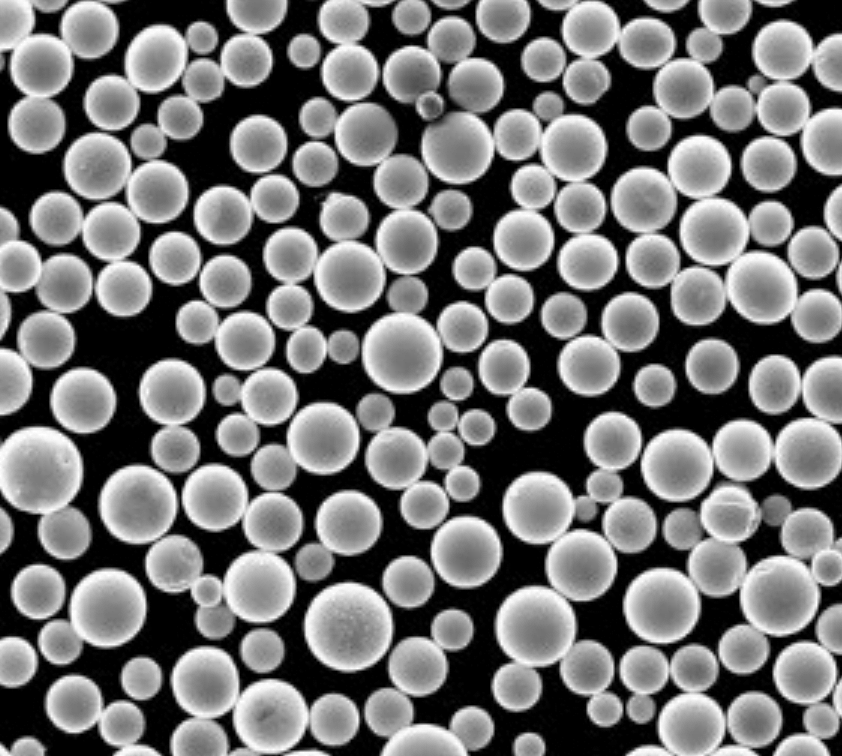
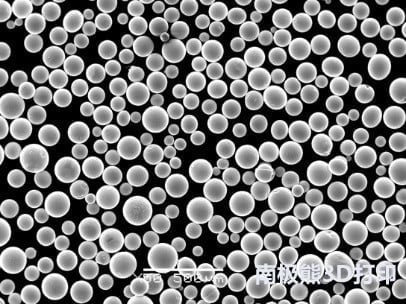
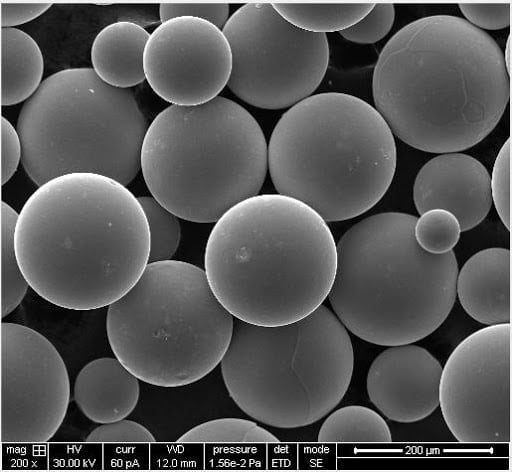
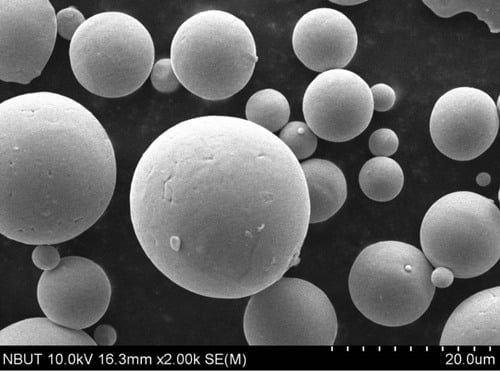
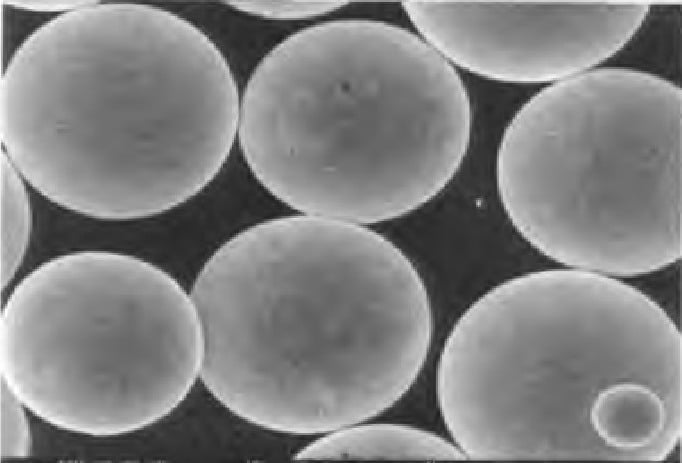
Choosing the Right Model:
Selecting the most suitable model depends on the specific application’s needs. Consider factors like:
- ความบริสุทธิ์: Higher purity offers better electrical conductivity but might come at a higher cost.
- ขนาดของอนุภาค: Finer particles create intricate details but can be trickier to handle. Coarser particles flow more easily but limit detail.
- Additives: Additives can enhance specific properties like thermal conductivity but might affect others like electrical conductivity.
- Application Requirements: Matching the powder’s properties to the application’s demands (e.g., high temperature resistance, high electrical conductivity) is crucial.
Consulting with a reputable supplier and discussing your specific needs is vital for selecting the optimal model of spherical tungsten powder for your project.
Advantages and Limitations of Spherical Tungsten Powder
Advantages:
- Superior Flowability: Spherical particles flow freely, making them easier to handle, transport, and process in various applications.
- Packing Efficiency: The spherical shape allows for tighter packing, resulting in higher density in the final product, leading to improved strength and performance.
- Uniformity: Consistent spherical particles lead to more uniform properties in the final product, enhancing overall quality and performance.
- Excellent Properties: Inherits the impressive properties of tungsten, including high melting point, superior strength, and good electrical and thermal conductivity.
- Versatile Applications: Used across diverse industries due to its unique combination of properties.
Limitations:
- Cost: Spherical tungsten powder can be more expensive than irregularly shaped powders due to the additional processing involved in achieving the spherical shape.
- Handling: Fine particle size models might require specialized handling techniques to avoid dust inhalation or settling issues.
- Oxidation: Tungsten can oxidize at high temperatures, potentially affecting its properties. Careful handling and storage in controlled environments might be necessary for some applications.
Despite these limitations, the advantages of spherical tungsten powder often outweigh the drawbacks. By carefully considering the application’s needs and selecting the appropriate model, manufacturers can leverage the unique properties of this remarkable material to create high-performance products.
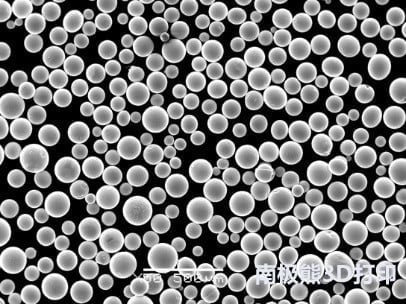
คำถามพบบ่อย
Q: What is the difference between spherical tungsten powder and regular tungsten powder?
A: Regular tungsten powder can have various shapes and sizes, leading to inconsistencies in flowability, packing density, and final product properties. Spherical tungsten powder offers a uniform spherical shape, resulting in better flow, higher packingdensity, and more consistent properties in the final product.
Q: What are the size ranges of spherical tungsten powder?
A: Spherical tungsten powder can vary in size from a few micrometers (µm) to hundreds of micrometers (µm). The specific size distribution depends on the chosen model and its intended application. Finer powders offer greater detail but can be trickier to handle, while coarser powders flow more easily but limit detail achievable in the final product.
Q: How is spherical tungsten powder produced?
A: There are several methods for producing spherical tungsten powder, including:
- Atomization: Molten tungsten is broken down into fine droplets using a high-pressure stream of gas or water. The droplets then solidify into spherical particles as they cool down.
- Chemical Vapor Deposition (CVD): Tungsten atoms are deposited onto a seed particle in a controlled atmosphere, gradually building up a spherical shape.
- Hydrothermal Synthesis: Aqueous solutions containing tungsten precursors are subjected to high temperatures and pressures, leading to the formation of spherical tungsten powder particles.
The chosen production method can influence the purity, size distribution, and other properties of the final powder.
Q: What are some safety considerations when handling spherical tungsten powder?
A: Fine tungsten powder can be a respiratory irritant. When handling the powder, it’s crucial to wear proper personal protective equipment (PPE) like masks, gloves, and eye protection to minimize inhalation and skin contact. Additionally, tungsten powder is flammable in a finely divided state, so proper handling and storage procedures are essential to avoid fire hazards.
Q: Where can I buy spherical tungsten powder?
A: Several reputable suppliers offer spherical tungsten powder globally. When choosing a supplier, consider factors like product quality, available models, pricing, and customer service. It’s recommended to research and compare different suppliers to find one that best meets your specific needs and budget.
About 3DP mETAL
Product Category
ติดต่อเรา
มีคำถามอะไรไหม? ส่งข้อความมาเดี๋ยวนี้! หลังจากที่ได้รับข้อความแล้ว เราจะประมวลผลคำขอของคุณพร้อมทีมงานทั้งหมด