Imagine a material so small, thousands of times thinner than a human hair, yet powerful enough to revolutionize industries. That’s the realm of ultra-fine cobalt powder, a microscopic marvel with a massive impact on our world. In this comprehensive guide, we’ll delve into the fascinating world of ultra-fine cobalt powder, exploring its properties, applications, advantages, limitations, and various models available.
Properties and Composition of Ultra-Fine Cobalt Powder
Ultra-fine cobalt powder, as the name suggests, is a finely divided form of the metallic element cobalt (Co). Its defining characteristic lies in its particle size, typically ranging from 1 to 100 microns, venturing into the nanoscale territory in some cases. This minute size grants it unique properties that set it apart from its bulkier counterpart.
Key Properties of Ultra-Fine Cobalt Powder:
- High Surface Area: Due to the minuscule particle size, ultra-fine cobalt powder boasts a significantly increased surface area compared to its bulk form. Imagine a tennis ball versus a pile of sand – the greater the surface area, the more room for interaction. This amplified surface area plays a crucial role in many of the powder’s applications, as we’ll explore later.
- Enhanced Reactivity: The increased surface area also translates to heightened reactivity. Just like a bonfire uses kindling to ignite more readily than a giant log, the smaller particles of ultra-fine cobalt powder interact more effectively with surrounding elements, making it a valuable catalyst in various chemical reactions.
- Improved Strength and Hardness: Don’t be fooled by its size – ultra-fine cobalt powder packs a punch when it comes to strength and hardness. This property makes it a prime candidate for applications requiring robustness and resistance to wear and tear.
- Superior Sintering Characteristics: Sintering is a process where metal powders are compacted and heated, forming a solid structure. Ultra-fine cobalt powder excels in this area due to its small particle size and high surface area, enabling efficient bonding during the sintering process.
Compositional Variations:
While pure cobalt (Co) is the primary component, ultra-fine cobalt powder can sometimes be alloyed with other elements to achieve specific properties. For instance, adding nickel (Ni) can enhance its magnetic properties, making it suitable for permanent magnet applications.
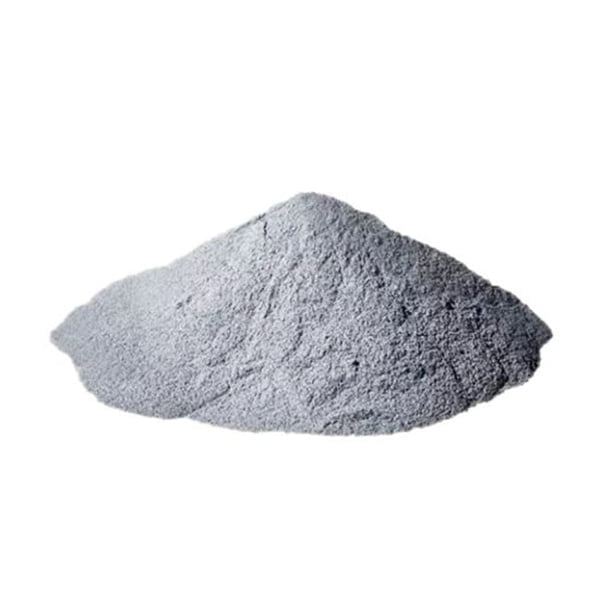
Different Models of Ultra-Fine Cobalt Powder
The world of ultra-fine cobalt powder isn’t a one-size-fits-all scenario. Various models cater to specific needs, with differences in purity, particle size distribution, and surface area. Here’s a glimpse into ten prominent models:
เช่นเดียวกับเครื่องแปลภาษาและเครื่องปรับปรุง | คำอธิบาย |
---|---|
Spherical Cobalt Powder (0.9 µm) | This model boasts a near-perfect spherical shape, ideal for applications requiring smooth flow and packing characteristics. The 0.9 µm particle size offers a good balance between high surface area and efficient packing. |
Elongated Cobalt Powder (1.5 µm) | In contrast to the spherical model, elongated cobalt powder features a more rod-like shape. This anisotropy (directional dependence) in shape proves beneficial for applications where directional strength or conductivity is desired. |
Carbonyl Cobalt Powder (Submicron) | Produced via the carbonyl process, this model offers exceptional purity (over 99.8%) and a very narrow particle size distribution. This translates to consistent performance and predictable behavior in demanding applications. |
Reduced Cobalt Powder (Submicron) | This model undergoes a reduction process to remove surface oxides, resulting in a highly active and reactive powder. Its clean surface makes it ideal for applications like catalysis where minimal surface contamination is crucial. |
Cobalt Nanopowder (30 nm) | Venturing into the nanoscale realm, this model features an incredibly small particle size of 30 nanometers. This ultra-fine size maximizes surface area, making it perfect for applications requiring exceptional reactivity or catalytic efficiency. |
Cobalt-Nickel Mixed Powder (Various Ratios) | As mentioned earlier, cobalt can be alloyed with other elements. This model incorporates nickel (Ni) in varying ratios to achieve specific magnetic properties. The precise ratio of Co to Ni dictates the final magnetic characteristics, making it tailorable for diverse magnetic applications. |
Cobalt-Iron Oxide Composite Powder (Various Ratios) | This model blends cobalt with iron oxide (FeO) to create a composite powder. The specific Co/FeO ratio influences properties like electrical conductivity, magnetism, and catalytic activity. This versatility makes it suitable for various applications in electronics and catalysis. |
Cobalt Aluminate Spinel Powder (Submicron) | Here, cobalt combines with aluminum (Al) and oxygen (O) to form a submicron-sized cobalt al |
Applications of Ultra-Fine Cobalt Powder
The unique properties of ultra-fine cobalt powder open doors to a vast array of applications across different industries. Here are some of the most prominent examples:
- Lithium-Ion Batteries: These ubiquitous power sources rely on cobalt as a key component of their cathodes. The high surface area and enhanced reactivity of ultra-fine cobalt powder contribute to efficient lithium intercalation and de-intercalation during battery charge and discharge cycles, ultimately leading to improved battery performance.
- Cemented Carbides: Imagine cutting tools that can slice through metal like butter. That’s the power of cemented carbides, where ultra-fine cobalt powder acts as a binding agent, holding the incredibly hard carbide grains together. Its superior strength and sintering characteristics ensure a robust and long-lasting cutting edge.
- Magnetic Materials: From permanent magnets in loudspeakers to magnetic recording media, ultra-fine cobalt powder plays a vital role. Depending on the specific composition (pure cobalt or cobalt-nickel alloys), the powder can be tailored to achieve desired magnetic properties, such as high coercivity (resistance to demagnetization) or tunable magnetic anisotropy.
- Catalytic Applications: The high surface area and reactivity of ultra-fine cobalt powder make it a valuable catalyst in various chemical reactions. For instance, it can be used in the hydrogenation of organic compounds, a process crucial for the production of many chemicals and fuels. The ability to control particle size and surface chemistry further expands its potential in developing efficient and selective catalysts.
- Electroplating: This process involves depositing a thin layer of metal onto a conductive surface. Ultra-fine cobalt powder finds application in electroplating baths, contributing to a smooth, adherent, and corrosion-resistant metallic coating. Its high purity often translates to better plating quality.
- Diamond and CBN (Cubic Boron Nitride) Superabrasives: These ultra-hard materials revolutionized cutting tools. Ultra-fine cobalt powder plays a supporting role here, acting as a matrix that binds the superabrasive diamond or CBN grits together. The right balance between the cobalt matrix and the superabrasive grits determines the tool’s performance and lifespan.
- เคลือบพ่นความร้อน: This technique involves spraying molten or semi-molten material onto a surface to create a protective layer. Ultra-fine cobalt powder can be used in thermal spray coatings for applications requiring wear resistance, corrosion resistance, or high-temperature performance. Its good flowability and packing characteristics make it suitable for this spraying process.
- Energy Storage: Beyond lithium-ion batteries, ultra-fine cobalt powder holds promise for next-generation energy storage solutions. Research is ongoing in areas like solid-state batteries and hydrogen storage materials, where the unique properties of this powder can contribute to advancements in energy storage efficiency and capacity.
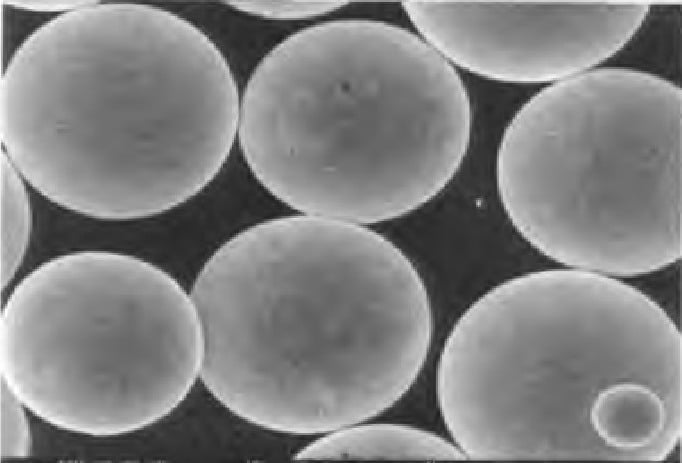
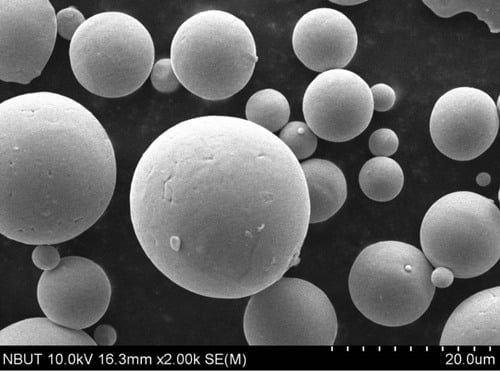
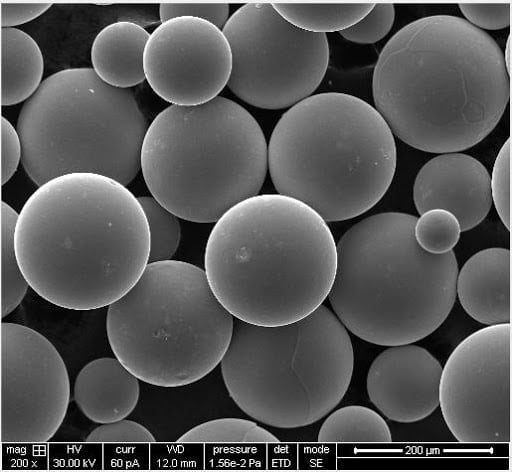
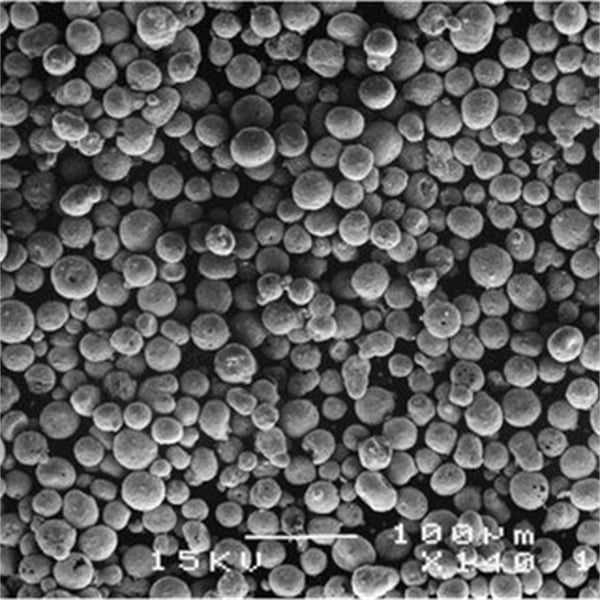
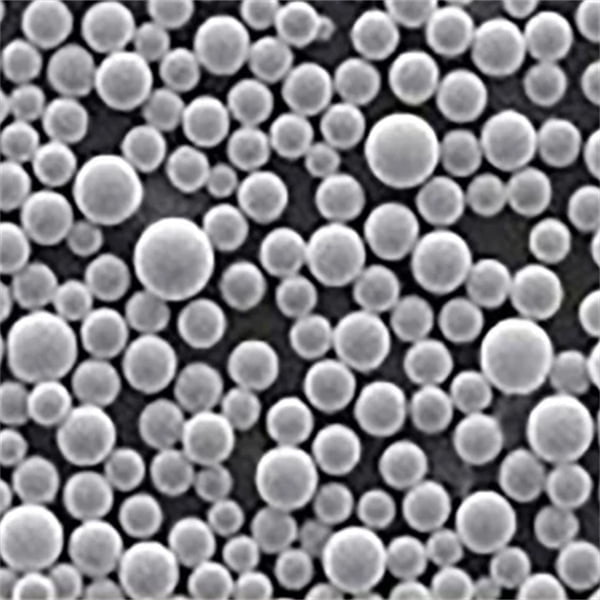
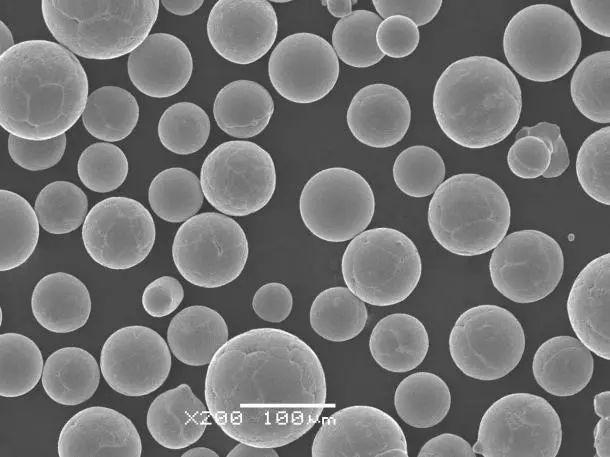
Why Use Ultra-Fine Cobalt Powder?
The decision to utilize ultra-fine cobalt powder hinges on its numerous advantages:
- Enhanced Performance: The high surface area and improved reactivity translate to superior performance in various applications, such as increased efficiency in catalysis and strengthened magnetic properties.
- Improved Material Properties: From better strength and hardness in cemented carbides to smoother and more adherent electroplating, ultra-fine cobalt powder elevates the properties of the final material.
- Tailorable Properties: The ability to control particle size, morphology (shape), and composition allows for customization of the powder’s properties to precisely match specific application requirements.
- Efficient Processing: The fine particle size and good flowability characteristics of ultra-fine cobalt powder contribute to efficient processing techniques like sintering and thermal spraying.
Considering the Limitations: Understanding the Drawbacks
While advantageous, ultra-fine cobalt powder also comes with certain limitations:
- Safety Concerns: As with many fine powders, cobalt powder can pose inhalation hazards. Proper handling procedures and safety equipment are crucial when working with this material.
- Cost Factor: The production process of ultra-fine cobalt powder can be more intricate compared to bulkier forms, potentially leading to higher costs.
- Oxidation Potential: Ultra-fine cobalt powder is susceptible to oxidation, especially at elevated temperatures. Storage and handling practices need to minimize exposure to oxygen to maintain its desired properties.
Choosing the Right Model: A Comparison of Ultra-Fine Cobalt Powders
Selecting the most suitable ultra-fine cobalt powder model requires careful consideration of several factors:
- Application Requirements: The intended use dictates the most crucial properties. For instance, high surface area might be paramount for catalysis, while magnetic properties become more critical for permanent magnets.
- Particle Size and Distribution: The desired particle size and its distribution influence factors like reactivity, packing density, and sintering behavior.
- Surface Chemistry: The presence of surface oxides or other contaminants can affect the powder’s performance. Depending on the application, a high-purity model with minimal surface contamination might be preferred.
- Cost Considerations: While cost shouldn’t be the sole deciding factor, it’s essential to weigh the performance benefits against the price point of different models.
Here’s a table summarizing some key differences between commonly used ultra-fine cobalt powder models:
ทรัพย์สิน | Spherical Cobalt Powder (0.9 µm) | Elongated Cobalt Powder (1.5 µm) | Carbonyl Cobalt Powder (Submicron) | Reduced Cobalt Powder (Submicron) | Cobalt Nanopowder (30 nm) |
---|---|---|---|---|---|
Shape | ทรงกลม | Elongated | ไม่ปกติ | ไม่ปกติ | Quasi-spherical |
ความบริสุทธิ์ | สูง | สูง | สูงมาก | สูง | ปานกลาง |
พื้นที่ผิว | สูง | ปานกลาง | สูงมาก | สูงมาก | Extremely High |
Reactivity | ปานกลาง | ปานกลาง | สูง | สูงมาก | Extremely High |
ความสามารถในการเผาผนึก | ดี | ดี | ยอดเยี่ยม | ยอดเยี่ยม | ปานกลาง |
แอปพลิเคชัน | Battery cathodes, Electroplating | Cemented carbides | Catalysts, Diamond superabrasives | Catalysts | Energy storage research |
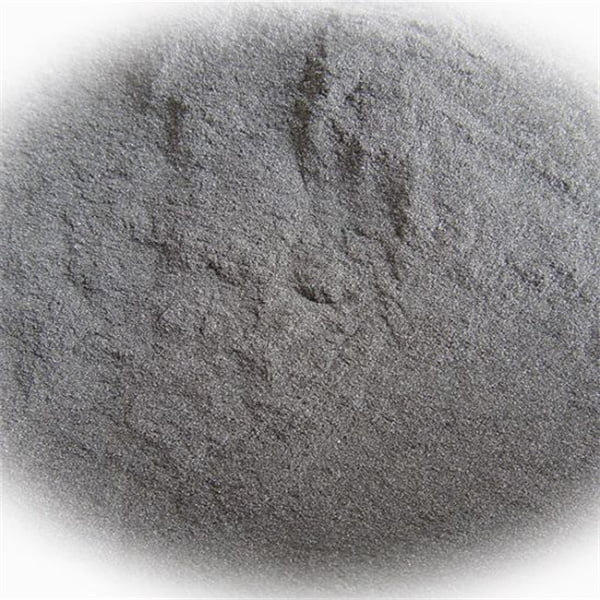
คำถามพบบ่อย
Q: Is ultra-fine cobalt powder the same as cobalt micro powder?
A: No, while both are finely divided forms of cobalt, there’s a difference in scale. Ultra-fine cobalt powder typically falls in the 1-100 micron range, while micro powders can range from 100 microns to 1 millimeter.
Q: How is ultra-fine cobalt powder produced?
A: Several methods can be used, including carbonyl process, reduction of cobalt compounds, and mechanical grinding/milling techniques. The chosen method influences the final powder’s properties like particle size, morphology, and purity.
Q: Can ultra-fine cobalt powder be recycled?
A: Yes, depending on the application and the level of contamination. Recycling processes for cobalt powder are under development, aiming to recover this valuable material and promote sustainability.
Q: What are the environmental considerations of using ultra-fine cobalt powder?
A: Cobalt mining and processing can have environmental impacts. However, advancements in recycling and responsible sourcing practices can help mitigate these concerns. Additionally, the use of ultra-fine cobalt powder can sometimes lead to reduced material usage compared to bulk forms, potentially lowering the environmental footprint.
About 3DP mETAL
Product Category
ติดต่อเรา
มีคำถามอะไรไหม? ส่งข้อความมาเดี๋ยวนี้! หลังจากที่ได้รับข้อความแล้ว เราจะประมวลผลคำขอของคุณพร้อมทีมงานทั้งหมด