Wear resistance powders are a crucial component in many industrial applications, particularly in areas where machinery and components are subjected to extreme wear and tear. These powders enhance the durability and lifespan of materials by creating surfaces that can withstand abrasion, corrosion, and other forms of degradation. Let’s dive deep into the world of wear resistance powders, exploring their types, compositions, properties, applications, and more.
Overview of Wear Resistance Powder
Wear resistance powders are specially formulated to improve the hardness and durability of various surfaces. They are used in coatings, surface treatments, and manufacturing processes to extend the life of components. These powders are typically made from hard materials like carbides, ceramics, and certain metals, providing excellent protection against wear and tear.
Types of Wear Resistance Powder
Here, we list specific metal powder models with detailed descriptions:
- Tungsten Carbide (WC) Powder: Known for its extreme hardness and high melting point, making it ideal for high-stress applications.
- Chromium Carbide (Cr3C2) Powder: Offers excellent oxidation resistance and is commonly used in high-temperature environments.
- Nickel-based Alloy Powder: Provides a good balance of toughness and corrosion resistance, suitable for harsh chemical environments.
- Cobalt-based Alloy Powder: Known for its superior wear and heat resistance, often used in aerospace and medical applications.
- Iron-based Alloy Powder: Economical and versatile, used in a wide range of industrial applications.
- Ceramic Powder: Includes materials like alumina and zirconia, known for their exceptional hardness and thermal stability.
- Stellite Powder: A cobalt-chromium alloy powder that offers excellent wear resistance at high temperatures.
- Silicon Carbide (SiC) Powder: Extremely hard and thermally conductive, used in abrasive machining processes.
- Boron Carbide (B4C) Powder: One of the hardest materials available, ideal for ballistic armor and abrasive applications.
- Molybdenum-based Alloy Powder: Offers good high-temperature strength and wear resistance.
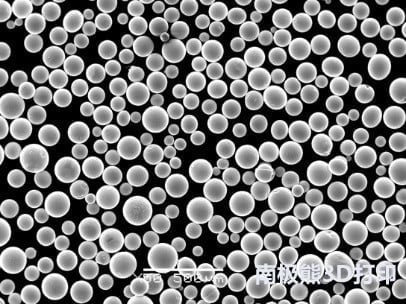
Composition and Characteristics of Wear Resistance Powder
Understanding the composition and properties of these powders is essential for selecting the right material for your application.
Type | องค์ประกอบ | ลักษณะเฉพาะ |
---|---|---|
Tungsten Carbide (WC) | WC | Extreme hardness, high melting point |
Chromium Carbide (Cr3C2) | Cr, C | Oxidation resistance, high-temperature stability |
Nickel-based Alloy | Ni, Cr, Fe, B, Si | Toughness, corrosion resistance |
Cobalt-based Alloy | Co, Cr, W, Ni | Wear resistance, heat resistance |
Iron-based Alloy | Fe, Cr, C, Ni, Mo | Versatility, cost-effective |
Ceramic | Al2O3, ZrO2 | Exceptional hardness, thermal stability |
Stellite | Co, Cr, W, Mo, Ni | High wear resistance, temperature resilience |
Silicon Carbide (SiC) | Si, C | Hardness, thermal conductivity |
Boron Carbide (B4C) | B, C | Extreme hardness, lightweight |
Molybdenum-based Alloy | Mo, Cr, Ni, Si | High-temperature strength, wear resistance |
Applications of Wear Resistance Powder
Wear resistance powders are utilized across various industries. Here’s a look at some common applications:
อุตสาหกรรม | แอปพลิเคชัน |
---|---|
อวกาศ | Turbine blades, engine components |
ยานยนต์ | Engine parts, transmission components |
การทำเหมือง | Drilling equipment, conveyor systems |
น้ำมันและก๊าซ | Pumps, valves, drilling tools |
การผลิต | Cutting tools, molds, dies |
แพทย์ | Orthopedic implants, surgical instruments |
การป้องกัน | Ballistic armor, weapon components |
พลังงาน | Power generation turbines, nuclear reactors |
Specifications, Sizes, Grades, Standards
Wear resistance powders come in various specifications to meet specific needs:
Type | Sizes | Grades | มาตรฐาน |
---|---|---|---|
Tungsten Carbide (WC) | 1-5 microns | Commercial, premium | ISO 9001, ASTM B777 |
Chromium Carbide (Cr3C2) | 5-20 microns | Standard, high purity | มาตรฐาน ASTM B276 |
Nickel-based Alloy | 10-45 ไมครอน | 625, 718 | AMS 5666, ISO 9001 |
Cobalt-based Alloy | 15-53 microns | Stellite 6, Stellite 21 | AMS 5796, ASTM F75 |
Iron-based Alloy | 20-63 microns | FeCr, FeNi | ISO 9001, ASTM B243 |
Ceramic | 1-10 ไมครอน | Alumina, Zirconia | ISO 6474, ASTM F2094 |
Stellite | 15-45 ไมครอน | Stellite 6, 12 | AMS 5894, ASTM F75 |
Silicon Carbide (SiC) | 1-50 microns | Black, green | ISO 9001, ANSI B74.12 |
Boron Carbide (B4C) | 1-10 ไมครอน | Technical, high purity | ISO 9001, ASTM B4C |
Molybdenum-based Alloy | 10-45 ไมครอน | Moly 30, Moly 40 | ISO 9001, ASTM B386 |
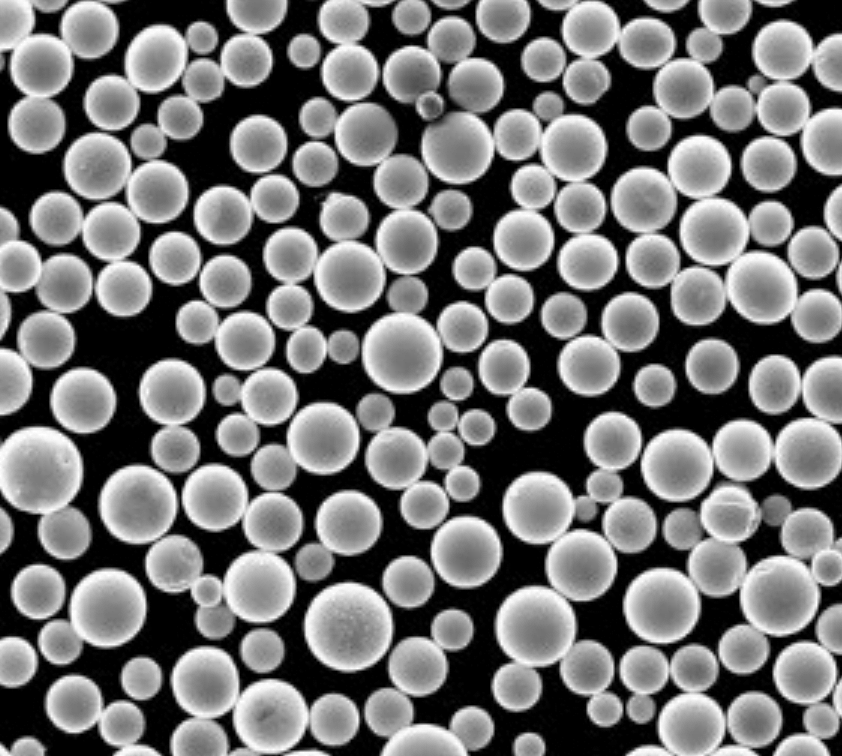
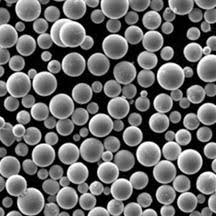
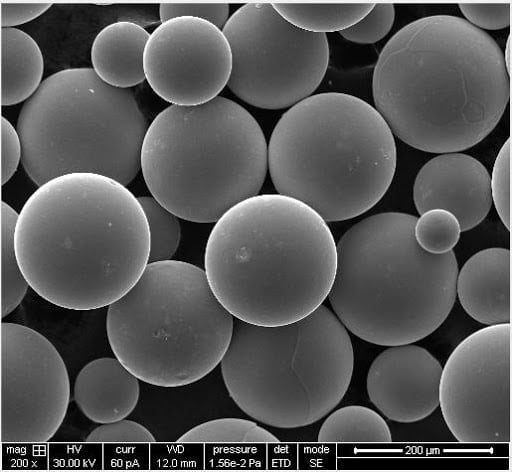
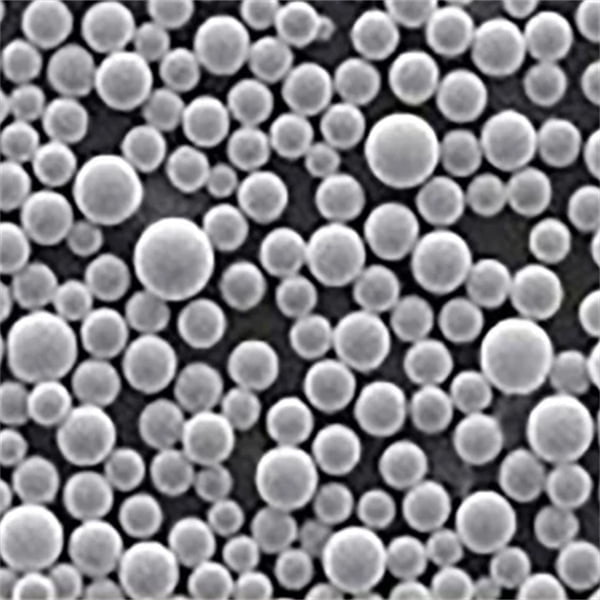
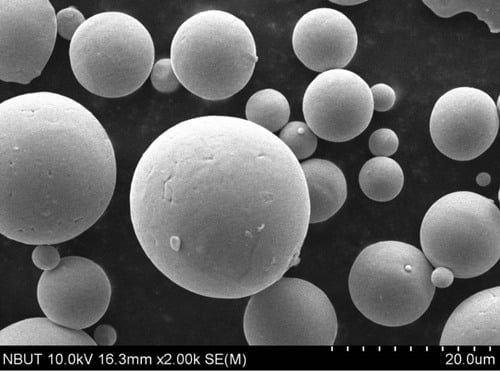
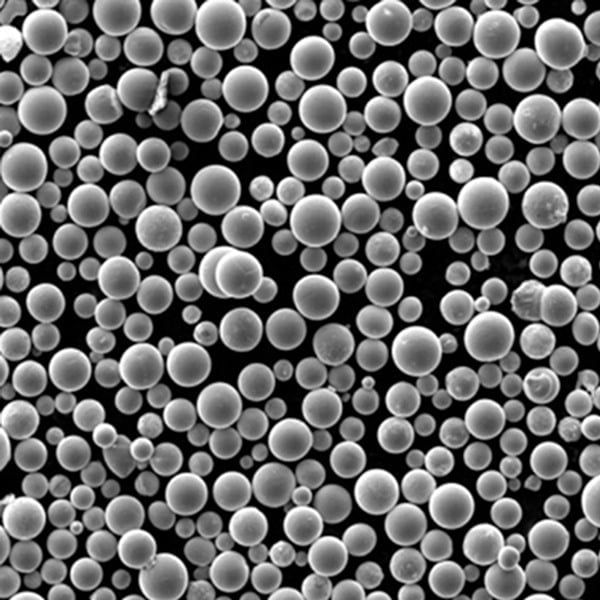
Suppliers and Pricing Details
Selecting a reliable supplier is crucial. Here are some notable suppliers and their pricing details:
ซัพพลายเออร์ | Type | Price Range (per kg) | Contact Information |
---|---|---|---|
Kennametal | Tungsten Carbide | $100 – $200 | www.kennametal.com |
Oerlikon Metco | Nickel-based Alloy | $80 – $150 | www.oerlikon.com/metco |
Carpenter Technology | Cobalt-based Alloy | $90 – $160 | www.cartech.com |
Praxair Surface Tech | Chromium Carbide | $75 – $140 | www.praxairsurfacetechnologies.com |
Saint-Gobain | Ceramic | $50 – $120 | www.saint-gobain.com |
H.C. Starck | Molybdenum-based Alloy | $70 – $130 | www.hcstarck.com |
Washington Mills | Silicon Carbide | $40 – $100 | www.washingtonmills.com |
แชนด์วิค | Stellite | $95 – $170 | www.home.sandvik |
ESPI Metals | Boron Carbide | $300 – $500 | www.espimetals.com |
Höganäs | Iron-based Alloy | $20 – $60 | www.hoganas.com |
Comparing Wear Resistance Powders
Choosing the right wear resistance powder can be challenging. Here’s a comparison to help you make an informed decision:
Type | ข้อได้เปรียบ | ข้อเสีย |
---|---|---|
Tungsten Carbide (WC) | Superior hardness, wear resistance | Expensive, brittle |
Chromium Carbide (Cr3C2) | High oxidation resistance, good in high temperatures | Lower toughness compared to other alloys |
Nickel-based Alloy | Good toughness, corrosion resistance | Moderate hardness |
Cobalt-based Alloy | Excellent wear and heat resistance | High cost |
Iron-based Alloy | Cost-effective, versatile | Lower wear resistance than carbides |
Ceramic | Exceptional hardness, thermal stability | Brittle, expensive |
Stellite | High wear resistance, temperature resilience | High cost, difficult to machine |
Silicon Carbide (SiC) | Hardness, thermal conductivity | Brittle, less corrosion resistance |
Boron Carbide (B4C) | Extreme hardness, lightweight | Very expensive, brittle |
Molybdenum-based Alloy | High-temperature strength, wear resistance | Moderate cost, less availability |
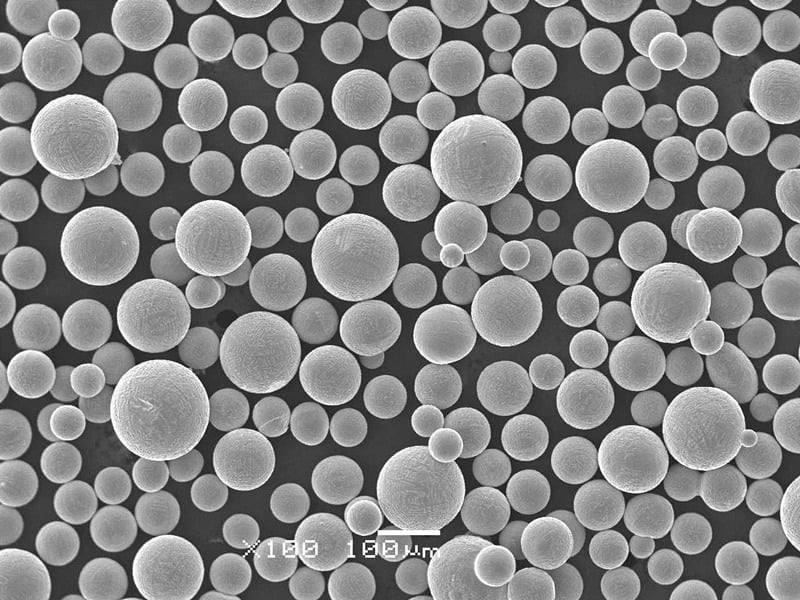
คำถามพบบ่อย
Question | Answer |
---|---|
What is wear resistance powder? | Wear resistance powder is a material used to enhance the durability of surfaces subjected to wear and tear, typically made from hard materials like carbides and ceramics. |
Where are wear resistance powders used? | They are used in industries such as aerospace, automotive, mining, oil and gas, manufacturing, medical, defense, and energy for various components and tools. |
What are the benefits of using wear resistance powder? | These powders significantly extend the life of components by providing superior wear, corrosion, and oxidation resistance, reducing maintenance costs and downtime. |
How do I choose the right wear resistance powder? | Consider factors like the environment (temperature, corrosion), the type of wear (abrasive, adhesive), and cost. Consulting with suppliers and experts can also help. |
Are wear resistance powders expensive? | The cost varies depending on the type of powder and its properties. For example, tungsten carbide and boron carbide powders are generally more expensive than iron-based powders. |
Can wear resistance powders be used in coatings? | Yes, they are commonly used in coatings to provide a hard, wear-resistant surface. Techniques like thermal spraying or cladding are often used to apply these powders. |
What is the difference between carbide and ceramic powders? | Carbide powders, such as tungsten carbide, are typically harder and more wear-resistant, while ceramic powders offer superior thermal stability and corrosion resistance. |
Is it difficult to apply wear resistance powders? | Applying these powders can be complex and often requires specialized equipment and techniques, such as thermal spraying, laser cladding, or sintering. |
How are wear resistance powders manufactured? | These powders are usually produced through processes like atomization, mechanical alloying, or chemical vapor deposition, ensuring precise control over composition and properties. |
Can I use wear resistance powders in DIY projects? | While it’s possible, using these powders typically requires advanced equipment and safety precautions, making them more suitable for industrial applications rather than DIY projects. |
บทสรุป
Wear resistance powders are indispensable in many industries, providing crucial protection against wear and tear for a wide range of components and tools. By understanding the types, compositions, properties, and applications of these powders, you can make informed decisions to enhance the durability and efficiency of your machinery and equipment. Whether you’re in aerospace, automotive, manufacturing, or another field, there’s a wear resistance powder tailored to meet your specific needs.
About 3DP mETAL
Product Category
ติดต่อเรา
มีคำถามอะไรไหม? ส่งข้อความมาเดี๋ยวนี้! หลังจากที่ได้รับข้อความแล้ว เราจะประมวลผลคำขอของคุณพร้อมทีมงานทั้งหมด